Introduction: Live Edge and Plywood Coffee Table
First, the design. When designing tables, I like to start with the legs. Other than the use of interesting or unexpected materials, tabletops all share the same design restriction, they must be a relatively flat surface. Whilst sketching some design ideas for the legs, I used a framing square to draw some quick and dirty straight lines and immediately became distracted by the irony of a framing square being a triangle and not a square.
I started playing with the framing square absentmindedly while sketching some more ideas. Soon after, I began considering its shape for the legs. After settling on two right-angled isosceles triangle legs, I figured out the overall dimensions of the table and its legs (consult the FREE PLANS for a full breakdown of the dimensions). I decided to use cabinet grade plywood as the material for the legs and a live edge walnut slab for the top. If you’re in need of a gravity defying coffee table, print off the FREE plans and gather the necessary tools and materials!
This is a project that can be knocked out in a weekend!
Supplies
Tools:
- Framing Square
- Circular Saw: All the cuts can be made with a Circular Saw but access to a Table Saw and a Dual Bevel Compound Mitre Saw will help to speed things up!
- Drill and Driver
- Brad Nailer + 1” Brads + Air Compressor
- Clamps (corner clamps are a big help if you have 'em!)
- Hot Glue Gun + Hot Glue Sticks
- Chisel + Mallet
- Random Orbit Sander
- Hammer
Materials and Consumables:
- 1/2 a sheet of cabinet grade plywood
- Live edge slab for the top (or other material)
- Wood glue
- Paint (optional) + Brushes
- Wood Filler + Putty Knife
- Sanding Block
- Painter's Tape
- Finish (Oil, Polyurethane, Lacquer, Shellac, Wax, etc.) + Rag or Brush
Step 1: Measure More Than Twice, Cut More Than Once
The right-angled isosceles triangle table legs utilise a little less than half of a single 3/4” sheet of cabinet grade plywood (minimal voids and multiple layers ). I purchased my plywood in 2’ x 4’ pieces, but it is often more cost effective to purchase a full 4’ x 8’ sheet. The building centre, lumber yard, or specialty wood supplier might even breakdown a full sheet into more manageable sized pieces either for free or for a nominal fee.
Using the provided cut list, cut the pieces to rough length first, then set your table saw to the exact width and cut all the pieces to width at the same time to insure congruity. Next, tilt your mitre saw to 45° and begin making beveled cuts on pieces A, B, D, E, and F. By doing so, some pieces will be cut to their final length while others, such as pieces A, B, C, and D, will require additional 90° cuts. It’s important that your mitre saw is well set up for this step, making sure the fence of the saw is square to the blade. This will make gluing up the legs much easier!
*No matter how precise you are; however, you might find that micro adjustments must be made to the pieces once you begin to assemble the legs.
Step 2: Leg Assembly
Assembling the legs requires a bit of forethought and order of operation planning. First, let’s start by making a straightforward 90° butt joint. After applying some wood glue, use corner clamps to hold the square ends of pieces A and C together and tack them together with brad nails. I also pre-drilled some holes and added some screws to pull the pieces tightly together while offering extra strength.
Next, glue piece D to C, making sure that the 90° inside joint is tight. Use some small clamps to hold the pieces together while driving in some brads from the exterior. This will help keep everything tight and allow you to move onto the next piece.
Now, the tricky bit. Join piece E to pieces A, C and D. This might take some finagling and clamp wrangling to get the pieces to sit right, so I suggest doing a dry run before applying any wood glue. Once piece E is slathered in glue and in place shoot some brads into the 45° joints to hold it in place while the glue dries.
The remaining pieces will seem to fall into place once piece E is secured to the assembly, making a completed right angle triangle. Start by gluing in and brad nailing piece B to piece A. Then, slather piece F in glue and slide it into the remaining vacant spot. Proceed by adding brad nails to keep everything locked together while the glue dries.
That’s one leg assembled! If you’re not completely satisfied with how your first leg assembly turned out don’t fret, you get to have another go at it when building the second leg assembly!
Pro Tip: *Use a wet rag to wipe away any glue squeeze out on the outside of the joints and a straw to collect any glue squeeze out on the inside of the joints.
Step 3: Prepping and Painting the Legs
Since we put a bunch of holes in the leg assemblies with our brad nailer, let’s use some wood filler to fill them up along with any other voids (either in the plywood edges or between your joints ). You can also fill areas that had some tear out or other imperfections.
Once dry, sand the filler flush to the plywood surface. A second pass might be required for deeper holes or imperfections. Once the leg assemblies have been prepped with wood filler and sanded smooth, use a tack cloth to remove any dust before painting.
For some added visual interest, I decided to keep the edges of the plywood exposed, to achieve this, I protected the edges with painter’s tape. The type of paint you choose is up to you. I decided to go with a chalk paint as it doesn’t require a coat of primer, has a nice matte finish, and is thick enough to fill in any small imperfections.
I decided to elevate the leg assemblies by hot gluing small pieces of plywood scraps to piece A on both leg assemblies. That way they can easily be picked up while the paint is wet and moved to a dust free environment to dry.
Pro Tip: Start by painting the insides of the triangles so that you can flip them around and easily get into all the nooks and crannies with your paint brush.
Step 4: Preparing the Top
While the paint is drying, start preparing the top. The live edge walnut slab I used only needed a few sanding passes to prepare it for finish, but still had some bark on it that needed to be removed. Start by removing what you can with your hands, then use a chisel to pry off the rest of the bark. For stubborn pieces you might find that you need the help of a mallet to dislodge the bark. You can simply discard the bark, but I keep the large pieces for a friend who uses it for her resin jewelry.
Sand up to a fine grit (around 320 or higher ) if you plan on using a simple oil finish.
Last step is to cut one of the ends of the top at a 45° angle, this will become the "front" edge of the table.
Step 5: Attaching the Legs to the Top
Start by knocking off the painting riser blocks, that were only hot glued on, with a hammer (an alternative is to flip a can of compressed air upside down and spray the joints to freeze the glue and snap off the riser blocks).
Next, pre-drill some pilot holes into the inside of the leg assemblies and down into the top of your choice. Then, use long enough wood screws to attach the leg assemblies to the top using an impact driver. This pulls the pieces tightly together.
Step 6: Finish to Finish!
Last step is to flip the table over and apply some finish! I chose a mineral oil which brought out the beautiful grain and colour of the walnut. I also coated the exposed edges of the plywood to both seal them and make them pop. If you’ve been following along congrats on building this unique coffee table! I’d love to know if you make one!
Cheers!
Mr. Ham.
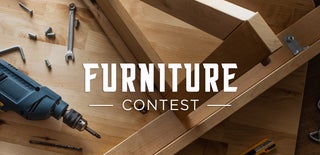
Participated in the
Furniture Contest