Introduction: 1000 Piece Cutting Board
So the idea of making this 1000 piece cutting board came to me as a way to celebrate and to say thank you to my 1000 subscribers on YouTube. I had to think long and hard on a way to make this work in a normal size cutting board. I ultimately ended up using the Sketchup program to come up with the design. In order to make all the pieces fit I figured on making 100 rows of pieces 1/8 of an inch thick. And each row would consist of (5) two inch wide pieces of walnut, (4) two inch and (1) one inch pieces of maple. And they all basically started off around two inches tall. I only planed down the bottom knowing that everything would be planed down again anyway after all the pieces were glued together.
Be sure to check out my other videos and hit that subscribe button my channel!
Supplies
Wood. I used Walnut and Hard Maple.
I also used 1/2" plywood and 3/4" plywood to make the jig.
Titebond III Ultimate Wood Glue, 16-Ounces
8 oz ounce Bottle, Roller Applicator
Table Saw
Diabo by Freud D1060X 10" x 60 Tooth Fine Finish Saw Blade
Table Saw Sled - How to build a table saw sled video
Electronic Digital Vernier Calipers
Tape Measure
DEWALT Random Orbit Sander, 5-Inch
Hand Plane
Scotch Heavy Duty Shipping Packaging Tape
Carpenters Square - Optional. Any tool with a right angle will work.
Howard Products BBB012 Cutting Board Oil
WALRUS OIL - Wood Wax, 3 oz Can, FDA Food-Safe, Cutting Board Wax and Board Cream
Clamps
The links above are Amazon links which means if you purchase anything through those links I may earn a small commission at no extra charge to you.
Step 1: Design the Board
I first spent some time using the SketchUp program coming up with a design I thought would work. At first I thought of doing some sort of random design with all the pieces but ultimately settled on this patterned design. I thought it would be the easiest to build by making all the cutting of the pieces uniform and therefore able to batch them out quickly on the table saw.
Step 2: Build a Jig.
I knew I was going to need something to keep everything in line as I built the board so I made this simple jig. It consisted of a base of 1/2" plywood and two walls of 3/4" thick plywood that I made two layers thick each. Using a carpenters square I ensured the the two walls were at a perfect 90 degree angle and glued and clamped them to the base. Once dried I covered the base and walls with packing tape to ensure no glue would stick while gluing up the board.
The overall dimensions of this jig I made to be just larger then the board to allow for plenty of room.
Step 3: Prepare the Wood for Assembly - Part 1
Although not really shown I started by cutting off large sections of wood from longer boards of walnut and maple. The lengths of these sections were determined by knowing that I needed to get up to five 2" pieces per thin strip of wood plus the kerf of the blade plus just a bit extra.
At that point I took a hand plane ( not shown ) to the bottom of each chunk of wood to give them a flat surface. I didn't worry about the top as that would just be planed down later using my power planer.
From there I moved over to my table saw. I used a thin strip jig that I made in this video. It works great for batching out large quantities of thins strips of wood. In this case I cut 100 strips each of walnut and maple. Plus a few extra.
Step 4: Prepare the Wood for Assembly - Part 2
I started by taking one of the thin strips of maple and making some test cuts on my table saw sled. Once I dialed in the cut to as close to one inch as I could I proceeded to cut 100 pieces of 1" maple.
Then I repeated the process for two inch pieces. Cutting just over 400 pieces of maple and just over 500 pieces of walnut.
I'm glad I cut some extra as it turned out some broke during the glue up. Mainly the walnut as it's not as hard as the maple.
Using a box I stacked up all the pieces to be used later. But then of
course I had the bright idea of dumping them all out to make a thumbnail picture for YouTube. It was real fun stacking them all back up nice and neat again;)
Step 5: Time for Assembly!
Now the fun part! I started by laying out the pieces walnut and maple in an alternating pattern up against the back fence with no glue. Basically starting off with one 1" piece of maple and then alternating pieces of 2" walnut and maple from there. Then applying the next row off pieces with glue using this handy glue roller applicator I set the next row off pieces up against the first row.
I figured I could get around 6 rows done before I felt it was time to put the clamps on. So at that point I quickly grabbed a scrap piece of wood that already had a flat face on it and applied a layer of scotch tape. Yes, scotch tape works. I had run out of packing tape and couldn't or didn't want to run to the store during the time of the virus. Anyway after the tape was applied I set that piece of wood against the pattern and applied several clamps and waited several hours till dry.
Step 6: Repeat. Repeat. Repeat.
It was at this time where I just got into a rhythm of gluing up sections of 60 pieces or 6 rows, clamping, and waiting at least a few hours. Then repeating. I got to the point where I could fit in 3 glue ups per day or 180 pieces.
It was also great timing that my main job had to shut down due to a virus scare for one week. So I had plenty of time to get lots of glue ups done!
The last two pictures you see of a smaller section which is the last 50 pieces being glued up will be explained in the next step. Mainly the reason why I had to do it this way.
Step 7: Planing and One Last Glue Up.
So one of a few mistakes that I made was making each strip just over .125 or 1/8" of an inch. Not sure why but I settled on about .128" to .130". If I had stuck with .125" or less the final width of the board "should" have fit through my power planer which has a maximum width of cut of 12.5 inches. The little bit of extra wood of course added up for extra width on the whole board. Oh well... So my solution was to send the almost completed board which was just over 12" wide through the power planer. Well, after first knocking down some high spots with my hand plane.
And for the last glue up I applied glue to the last 50 piece section and glued and clamped it to the main section. I had already previously taken my hand plane to the small section to get it very close in height as the main section. Once the last section and the main section were glued and dry I used my hand plane again to get the two sections even with each other.
Step 8: Trim the Edges.
Now that the top and bottom faces have been planed down to a nice smooth surface I went back over to the table saw and trimmed the sides. I didn't trim the long edges as this board isn't perfect. The long edges do have a slight bow to them. So if I did try to cut them straight I would end up cutting through some of the pieces and lose the 1000 piece count. So it is what it is:)
Step 9: Fill in the Gaps.
So since things don't always come out perfect especially with dealing with 1000 pieces I had some gaps to deal with. I proceeded to mix up some filler using the Titebond glue and sawdust from sanding on the same type of wood used in the board. Once a portion was mixed well I simply started pressing some into all the gaps and set aside to dry.
Step 10: Sand the Board.
Once all the filler was dry I used my orbital sander with 80 grit and removed all the excess filler on all surfaces till nice and smooth. I then put a small chamfer on the corners using the sander as well. I used very light pressure and took my time with this method. If done wrong here you could certainly go to far with your chamfer.
I then switched to 120 grit paper and repeated sanding the whole board. Once that step was done I sprayed a light mist of water over the whole board. This does what's called "raising the grain". Anytime moisture contacts wood after sanding it will raise the fibers of the wood that has been sanded ( or laid down ). So after the water dries and you feel the board again it will fill rough. It was then that I took the sander with 120 grit paper back to the board to remove those raised fibers. Now it's nice and smooth and it will stay that way.
Step 11: Add Logo.
I heated up my branding iron that I got from Budget Branding Irons and proceeded to burn in my logo on the under side of the board. This step is of course purely optional.
Step 12: Oil and Wax the Board.
Now that the board is finally all smooth from sanding and logo applied it's time to condition the board before use. I use Howard's Cutting Board oil which is a food safe mineral oil. I applied a generous amount of oil and let that soak in. I usually just let it soak overnight.
The following day I wiped off the excess and proceed to apply some wax. I use Walrus Food Safe Wax.
I love this stuff! Easy to use, just wax on, let dry for a bit and wipe off. Done!
Step 13: Enjoy the Board!
With proper care and maintenance a handmade board like this should last for many many years. Every so often when the board feels dry simple add some more oil and then some wax. For cleaning simply use warm water and mild soap. NEVER put one of these in the dishwasher! It will ruin the board beyond repair.
So get out there and make your own board. I would love to see what you come up with!
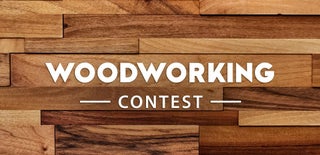
Second Prize in the
Woodworking Contest