Introduction: 3D Printed Hidden Blade Prop - Fusion 360 Design
This is a project that I undertook for a Halloween costume prop. It worked several times, but did eventually fail just before leaving for a costume party.
DISCLAIMER: This is not an original design by me (I'm of the opinion that very few of us actually create truly original designs). I did some reverse engineering on several hidden blade props I found online, mainly the one done by Colin Furze (YouTube). Side Note: I highly recommend checking out Mr. Furze' YouTube channel as it is highly entertaining and has a lot of inspiring ideas as well as interesting construction techniques.
[Play Video]
The design was done entirely in Fusion 360. The device was printed using a Stratasys Dimension 3D printer. The blade was cut from a piece of acrylic and had a slot milled (for a battery and LED) using an X-Carve CNC routing table.
I will provide a general overview into the process of how I designed this project using Fusion 360. For some processes, I will demonstrate with a screen cast how to accomplish the desired task. The purpose of this particular Instructable is not to be an in-depth guide into using CAD software or 3D printers. The purpose is mainly to showcase how Autodesk Fusion 360 could be used to create a virtual mechanism with several components which could be 3D printed and assembled into a functional real world mechanism.
Step 1: Design Process
The first step after starting a new design file was to create separate components for each of the pieces needed for the hidden blade prop. This populates the design tree with several expandable folders.
Step 2: Sketching and Modeling
After the initial design tree was constructed each component was sketched up and modelled. This process involves creating a 2D sketch and then "Extruding" it to create a 3D object with a matching profile. The 3D object can then be modified by stretching the faces or making sketches on the faces and extruding either positively or negatively. A hole would be made by sketching a circle on the face of an object and negatively extruding into the object. A shaft would be made by sketching a circle on the face of an object and positively extruding away from it.
NOTE: There is a .GIF in the first image frame but it doesn't seem to be working in the "Full Preview" window. I apologize and will attempt to include an alternative form of instruction ASAP.
Step 3: Assembly
Once components have been modeled, they can be re-positioned using the "Move" and "Align" tools. They can be connected to each other using static or moving "Joints". It is important to consider the order in which joints are created and what the dependencies are between each of the joints and objects. It is possible to create a joint constraint that is impossible to complete. If two objects have a static joint that prevents them from moving relative to each-other, it is not possible to later on create a joint that requires one of the objects to move while the other remains stationary.
NOTE: I am having the same issue with the .GIF file for this step as well.
Step 4: Motion Testing
It is possible to create physical interactions between components in an assembly. This means if one component is moved, it will move the other components that are connected to it, creating a simulation of the mechanisms' movement.
Step 5: 3D Printing
Once all of the components were completed and modified as required to allow the desired movements and fits, they can be saved in a file format that can be sent to a 3D printer. Each component was "Exported" as an .STL file and sent to 3D printer using another software package.
Step 6: Assembled Product
After all of the components were 3D printed everything was assembled into the final product you see in the picture.
I am currently trying to prepare a YouTube video for the instructional videos since some of the .GIF files I've uploaded do not seem to work.
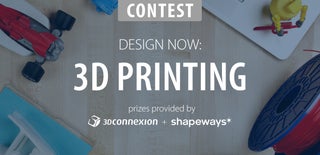
Participated in the
Design Now: 3D Design Contest 2016