Introduction: 3D Printed and Mycelium Grown Beehives
Welcome to the exciting world of biological design, regenerative beekeeping, and digital craft! This post will bring you through the process of creating entirely 3D-printed and mycelium-grown beehives—or what we prefer to call beesnest enclosures—using a biohybrid design approach.
This post serves as an appendix for the article "Fostering Symbiosis in the Eusocial Realm: the State of the Mycelial Hives of HIVEOPOLIS" in the upcoming book "Drivers of Design, Vol. II" from the Distributed Design project with EU funding. The article and these instructions will be cross-linked as soon as they are published. Through these platforms, we encourage all makers and makers-to-be to use and modify this version of the HIVEOPOLIS mycelial hives in a range of ecological and social/cultural settings. Our goal is to engage designers, craftspeople, and makers in collaborative critical making and reflecting activities, as well as to produce practical design solutions to shared design challenges using available resources and collective experimental findings.
This instructable is essentially a biocomposite-making workflow. This approach, design models, and overall process were created by Asya Ilgün during her Ph.D. study as part of the EU-funded project HIVEOPOLIS. The design prototypes and experiments were realised with the support of the Artificial Life Lab of the Institute of Biology at the University of Graz as well as project partners of HIVEOPOLIS. They are presented here in the most concise and accessible manner feasible for anybody who wants to explore the numerous concepts and digital technologies included in this project. Because we apply several technological methods for manufacturing, some may find it challenging or unachievable to complete the whole task. If you have the opportunity, this would make an excellent design workshop case for your local fablabs, maker or hacker spaces, and design studios.
The items and procedures detailed in this post are widely available in local markets, woodlands, and construction supply stores. However, biodesign and biohacking are becoming essential components of maker culture; thus, once the maker has access to them, it is also advisable to make use of local biohacker spaces and wet labs for sterile working and regulated growth processes, particularly for advancing the procedure for scientific purposes in controlled conditions. We find the further exploration of this method useful for progressing research in ecological living materials and sustainable manufacturing processes.
Mycelial Beehives of HIVEOPOLIS 2023 is licensed under a Creative Commons Attribution-NonCommercial-ShareAlike 4.0 International licence. Visit http://creativecommons.org/licenses/by-nc-sa/4.0/ to view a copy of this licence.
Supplies
Design Modeling Software
3D Printing Materials
- Commercially available biodegradable filaments: GrowLay Brown by Kai Parthy (more experimental); the hive that is presented here is made with Extrudr Wood.
- FibreClay (optional)
3D Printer
- The hive prototype presented here was produced by BIGREP One V3 in FabLab at TU GRAZ. Therefore, the gCode specifics are according to BigRep.
- You can start experimenting with smaller sizes using Prusa printers, i.e., Prusai3 MK2 since you can find the specific initial and end codes for the gCode in the grasshopper script.
- Depending on the size of the components, any desktop or industrial 3D printer is suitable, with the only requirement of editing the "Initial" and "End" gcodes in the Grasshopper script.
- Of course, this requires material and parameter checking with the material you prefer and the available 3D printer.
or
- The author has experience with the WASP3D 40100 LDM printer, as she produced an early prototype with clay and mycelium composite at the Shape Lab, Institute of Architecture and Media, TU Graz. She used the Termite plug-in for gCode generation, which is an advanced 3D printing plugin for Grasshopper3D.
Mycelium Composite
- Spawn: In this prototype, we use Phoenix Oyster (Pleurotus pulmonorius), which is a summer oyster mushroom mycelium. The species is preferred due to its comparatively dense mycelium branches with faster growth and suitability for workshop contexts. This species is easily cultivable and available from many local mushroom farms, largely commercial in Europe and is mainly used in introductary settings in which mushroom materials are produced.The hive on display here was grown using the spawn product of Glückspilze, Tyrol, Austria
**Prefer mycelium spawn grown on a wood substrate instead of grain. Birds like to eat the grains in the grain spawn and since our purpose is the outdoor assembly, we prefer using wood-inoculated spawns.
- Growth Substrates: Collect fibrous substrates like straw, hemp fibers, or flax fibers, as well as small particle-based substrates like beech wood sawdust. The fibrous substrates contribute to insulation and holding moisture, while the small particle-based substrates affect the composite’s density and, therefore, its water absorption properties.
- Option 1: Acquire from raw material suppliers. Communicate with the provider about the sizes and the plant species you want to use. Find local farms or organic producers. We have three main plant species: wheat, flax, and beech. Below are the providers and the substrate types we used:
- Flax: Flax fibers are already processed for use as blown-in insulation.
- Wheat: 1-2 cm organic wheat straw**approximate ingredients related to mycelium: 30–45% cellulose, 20–25% hemicellulose, 15–20% lignin, as well as a number of minor organic compounds.
- Beech: Selected, natural beech wood from European forests, size 0.5mm - 1mm.
- We have selected these suppliers to provide the substrates for our project on account of their commitment to quality and organic assurance, equitable working and environmental conditions, and local resource emphasis.
- Option 2: Forage for your own substrates in the woods in your region and take part in natural material circularities. This will, of course, increase the chance that you get many extra microorganisms and particles. You can approach this as a waste upcycling initiative by visiting local carpentry workshops or contacting local farms, but make sure there are not so many chemical glueing agents in the sawdust. We suggest trying this out if time is not a constraint for you (which has become a constraint for us due to the fact that these hive prototypes have been developed as part of an EU project with numerous deadlines)
- Growth supplements (optional): The author used gypsum for calcium supplementation. However, it is highly encouraged to experiment with different additives to improve different aspects of the process. Here is a good source for reference (Adrien Rigobello, Ph.D. Dissertation, chapter 20.5)
- Pasteurization: Hardwood ashfor alkalizing cold water for the bath pasteurization of the substrates. This instructable is for makers, gardeners, and ; therefore, it assumes the possibility of making buonfires in gardens, visits to friends' huts to have a nice evening and collecting the ash leftovers of the evening heat provided by the natural hardwood buonfire. this is the way to go.
- Equipment:
- large buckets for soaking the substrate
- (optional_see below) Water (deionizing or purifying agent such as these, if necessary)
- (optional_see below) lime (calcium carbonate, or magnesium carbonate)
- burlap sacks
- burlap fabric
- pH Strips or calibrated pH meter
- buckets or boxes with sealed lids to grow the infilled modules in (We use IKEA Samla boxes :)
- A luggage scale or kitchen scale upto 10kg
- Long, slender poles are used to push the substrate into the hive scaffolds.
- micropore paper tape
- latex gloves
- 70% ethanol
- basic modular grow tent with metal mesh racks OR 2 + plastic boxes (minimum 70cm)
Step 1: Choosing Fungal Species, Substrates and 3D Printing Materials
The purpose of the described method is to fabricate a low-density mycelium composite for insulation purposes.
Firstly, a reduction in density correlates with an increase in water absorption capacity, attributable to the higher surface area of the substrate. Secondly, lower density also implies decreased thermal conductivity, thereby enhancing the material's insulative properties. Utilizing fibrous substrates such as straw, hemp fibers, or flax plant fibers, which are recognized for their natural insulating characteristics, is advantageous. Moreover, substrates like sawdust from hardwood plants exhibit a higher concentration of hydrophobins. Consequently, a careful consideration of the inert properties of these substrates can facilitate the crafting of a bespoke input substrate. You are invited to try out the mixtures of your own preference.
Depending on your time, location, financial resources, and design variables, there is really no one recipe that everyone should repeat and that works .Numerous resources delineate the methodologies employed in the fabrication of mycelium composites, predominantly characterised as laboratory processes. These resources provide an extensive overview of various species and types of substrates, along with their corresponding functionalities.
Choosing Mycelium Spawn
- Based on your local climate, choose a mycelial fungus species that thrives in your area. For warmer regions or areas without stable temperatures (above 20°C on average), opt for native species that can handle warm temperatures and are resilient to temperature fluctuations. The Phoenix Oyster mycelium spawn is a good example for Graz, Austria, where we grow hives mostly indoors throughout late winter and early spring. It typically colonizes straw substrates in 2-3 weeks at temperatures of 23–28°C
- You can acquire spawn from local mushroom technology or farming companies, as described above in the "Supplies" section. Alternatively, if you have expertise in mycology and microbiology or are willing to learn, you can create your own spawn using native species from nearby woodlands. You can find "how-to" descriptions of such processes online.
Step 2: ADAPT THE GRASSHOPPER3D MODEL
This is the part where we will decide on the hive form.This parametric design process in Grasshopper3D integrates various elements, including geometry, wall topology, and gCode generation, into one comprehensive script. The process is multifaceted and uses multiple data series and mathematical graphs. Here’s a breakdown of the key components:
- Inputs for Design
- Geometry and Density Definer Parameters: These initial inputs establish the basic guidelines for the design.
- Input Graph-Mappers: The numerical parameters are fed into the curve-mappers to shape the inner nest's profile curves.
- Hex-Weave Algorithm for Continuous Path Drawing: This step involves creating a continuous toolpath that weaves between the inner and outer surfaces of the selected form.
- (optional) Decision-making via the Interactive Evolutionary Algorithm (IEA): This optional but recommended plug-in for Grasshopper3D, Biomorpher, allows designers to interact with the evolutionary development process. IEAs in GH3D facilitate rapid visualization and assessment of performance criteria, numerical factors, and beehive shape. The focus is on merging machine intelligence with computational power in a complex parametric model. The model's variables or 'genomes' include predefined numerical domains and geometries, crafted through extensive trials in computational design and 3D printing.
- Preparation for Manufacturing:
- Segmenting the Design into Components: This step involves breaking down the design for easier manufacturing.
- Fabrication-Related Inputs and gCode Generation: This includes preparing the final inputs and generating gCode for manufacturing.
Important Recommendations!
- While working around the variables and adjusting parameters, it's advisable to:
- disable the "prepare for fabrication" components to streamline the process.
- work at a lower resolution in terms of layer height. For quick visualizations, avoid using final layer heights like "0.8mm." Instead, use larger values like "25mm" to facilitate easier and faster adjustments.
- IEA: We find the principle of interactive evolutionary design more appealing than objective-oriented design optimisation. This is especially relevant in design scenarios when there are several "objectives" that cannot be accurately expressed computationally and instead require the expertise of a skilled craftsman. Unfortunately, due to the time constraints of our research and the complex nature of the multispecies biohybrid design, we were unable to utilise it to the extent that we had hoped. We appreciate any comments, implementation suggestions, and ideas. Recommended reading by the authors of the plug-in
- The current parameters need more combinatorial variety. The IEA and design tools are presently limited to shaping and performance tests. For a more nuanced design approach, it's advised to use less dense input geometry. For instance, incorporating offset lines and evaluating their length can effectively influence the overall toolpath length.
Step 3: OR DOWNLOAD THE FILES OF THE CURRENT DESIGN ITERATION
- Download the polyline toolpaths of the thermoplastic wood composite hive scaffold here
- Find the gcodes of the parts printed to make the hive presented in the article and in the photos you see here.
- Find the STL. files of the soild parts for stabilising the hive parts below.
- If you prefer to use frames or top-bar components, this is a challenge for you to adapt modular frames into your design.
In the figure, where you see the wooden frames hanging towards the cavity of the hive scaffold, you see the reconstructed parts of the commonly used Zander-type hive frames. This is only because we used the foundation frame method in order to be able to adhere to the regulations of beekeeping and experimentation in the university area. This discussion goes into the section on conclusions in the article that supports this post.
CLAY HIVE FILES:
- We uploaded the CNC milling files of the wooden frame and top bar parts that we produced for the clay hive. In case you want to check it out.
- Find the gcodes of the printed parts here.
Attachments
base_H32cm_Extrudr_filamentthickness_2_85mm.gcode
body_H52cm_Extrudr_filamentthickness_2_85mm.gcode
floor_H32cm_Extrudr_filamentthickness_2_85mm.gcode
roof_H17cm_Extrudr_filamentthickness_2_85mm.gcode
hive_Stabiliser_base2floor_left side.stl
hive_Stabiliser_base2floor_right side.stl
hive_Stabiliser_floor2body_left side.stl
hive_Stabiliser_floor2body_right side.stl
Step 4: Manufacture the Parts!
Time: Approx. 60 hours
Step 5: INFILL SUBSTRATE PREPARATION
Time: 2 days
Preparing a substrate for mycelium cultivation involves several critical steps, each of which is essential to the process.
Substrates Used: Flax, Wheat straw, and Beech Wood Particles
1.Mixing Substrate Mixture
Here we describe a recipe, with some flexibility for further experimentation. We initially tested this recipe during a workshop at the FabLab Budapest (Co-creation for Cohabitation), supported by the mobility scheme of Distributed Design EU. The ingredients and the making process are suitable for making low-density, highly water-absorbent, and fast-colonizing bee nest enclosures.
The process described here diverges from typical laboratory methods, offering a more accessible technique suitable for diverse environments. 1-2-3 as an easy proportion, as we used during this co-design workshop, our main focus was the thermal insulation properties of the mycelium composites and how we could form a low-density mycelium composite using the fablab facilities provided. This involves combining two units of fibrous substrates (one with a low water-absorbing capacity and one with a high water-absorbing capacity) with one unit of small particle-based substrates, as we formulated here simply as the “1(dry)-2(wet)-3(wet) proportion.”
In this methodology, it's important to acknowledge that the mass of substrates (moist with their field capacity depending on their properties) varies significantly depending on their density. For instance, a standardized volume of wet straw possesses a considerably lower mass compared to an identical volume of wet beach dust. This disparity underscores the necessity for a volume-based proportional approach in the preparation process.
For measurement, we employ a standard cup, filling it with the substrates without compacting them by pressing. In the formulation used in this hive, 3 cups of wet straw, 2 cups of wet flax fiber, and 1 cup of dry beach dust are measured. But the mass ratio would be a different one, such as 720 g: 730 g: 320 g (in a 600-ml beaker glass). So one unit of dry particle-based substrate, two units of wet water-absorbent fiber-based substrate and three units of wet less water-absorbent fiber-based substrate. This recipe facilitates a standardised yet adaptable recipe for mycelium composite preparation that ensures thorough colonisation and fibrous reinforcement.
- Proportion: Follow a '1-2-3 proportion': two units of fibrous substrates (flax and straw) to one unit of small particle-based substrates (beech dust).
- Amount needed for one hive: approximately 60 liters in total for one beehive
- Measurement: Use a standard cup for measuring substrates
- Mixing: Combine substrates before pasteurization or sterilization.
2. Pasteurization or Sterilization
To develop to their full potential, fungi need a substrate that is both moist and nourished. On the other hand, moulds, bacteria, and other organisms thrive in these environments. So, by pasteurising or sterilizing, we decrease or completely remove these organisms from the substrate and give a hand to the mycelial fungi, since these other organisms grow quicker than mushroom mycelium. While these procedures do lessen the likelihood of contamination and associated development issues, they may not be suitable in all cases.You don’t need to sterilize less nutritious substrates like straw, sugarcane bagasse, coco coir, hardwood sawdust, and cardboard.
Wood-ash Ash pasteurization
- Process
- Fill a large bucket with tap water and increase the water’s pH to 11–14 using wood ash (3% of water weight or 30 g per 1 liter of water).
- see this video for reference
- Soaking Process:
- Soak flax and straw in separate buckets overnight in natural or neutral-pH tap water at room temperature.
** For oyster mushrooms, alkalize the water by adding some lime or soda ash if tap or well water is acidic (pH 6.5 or below).
- Avoid soaking beech dust; it will absorb moisture from wet flax and straw.
- Removing excess water:
- Squeeze the substrate gently with your hands until no more water drips.
- Alternatively, use burlap sacks: fill the sacks with your substrates, hang them in spots where suitable, such as trees in your garden, and drip-dry the substrates to a similar moisture level (hydration level is often referred to as the substrate being at field capacity)
- Pros: Environmentally friendly and effective for certain mushroom species, like the Phoenix Oyster.
- Cons: Sourcing untreated hardwood ash can be challenging and requires more ash than lime to achieve the desired pH.
(or Sterilization
Use an autoclave or pressure cooker. We will not describe here the specifics of the sterilisation procedure we use when needed; please refer to the online DIY references such as , how to sterilise mushroom substrate_source 1, how to sterilise mushroom substrate _source 2
- Pros: It kills all or most of the competing organisms, increases yields, supports a wider variety of mushrooms, and reduces spawn costs.
- Cons: can result in high energy usage, expensive equipment, requires careful monitoring, and is time-consuming.
3. Adjusting pH Levels
This enhanced process ensures that the pH level of the substrate is ideally balanced for mycelium growth. Understanding the scientific aspect of pH and its implications for the healthy growth of this organism is crucial. The addition of lime (or soda ash) should be tailored based on the initial conditions of the water and raw materials, aiming for the optimal pH range that supports healthy mushroom growth.
- pH Testing: Use pH test strips for testing.
- Procedure:Squeeze a bit of water from the testing material onto a pH test strip.
- Compare the color change with the provided pH color chart.
- ** pH meters usually produce more accurate and reproducible readings, but in this method, we prefer pH strips as they are designed for quick and easy use with an immediate response and are cheaper.
- pH Adjustment:
- Objective: If your measured pH is lower than 6.0, use lime As a pH buffer Add it incrementally by measuring at each step and raising the pH to levels between 6.5 and 8. Consider the alkalinity or acidity of your sample.
- Scientific Perspective:pH measures the acid-base balance, not the alkalinity or acidity separately. A pH of 7 is neutral; a pH above 7 indicates alkalinity.
- If you use "pH-based cold pasteurization," you might not need this process.
- Regional Considerations:In areas with alkaline water (pH above 7), substrates often grow well without additional lime.
- If using fresh, clean husks, lime might be unnecessary.
**Additional Considerations:
- If you sterilise the substrate, the "soaking process," "removing excess water," and "adjusting pH levels" are performed before the sterilisation.
- Species-Specific Needs: Some fungal species can almost only survive on substrate with NO competing microorganisms; therefore, they require sterilised substrate.
- Environmental Impact: The wood ash method is environmentally friendly but requires careful sourcing and handling of ash.
- Timing is key, particularly when coordinating the preparation of the substrate with the arrival and fresh storage of your mycelium spawn. It's crucial to act promptly after pasteurizing the substrates. Immediately inoculate them with the mycelium spawn once you've confirmed that the substrate's pH, temperature, and moisture level are within the desired range. Avoid any delays in this process! Prolonged waiting can compromise the quality and effectiveness of the cultivation.
- If possible, prepare your substrates incrementally. For example, for step 6, prepare half the batch of 30 liters, and for step 7, prepare another 30 liters. Meaning that you pasteurize the next batch of the substrate mixture before the next step.
- Otherwise, if you pasteurise in bulk and you cannot use all of it during the first spawn run, store them in sealed boxes in cold rooms or fridges with temperatures of 4C.
Step 6: GROWTH PHASE ONE: Spawn Run With the Substrate
Time: 5 days
Before integrating the spawn into your hive scaffolds, it’s advisable to acclimate the spawn to your substrate mixture for about 5 days. This step is especially crucial when working with wild mycelium and substrates.
Preparing the workspace and materials
- Clean Workspace: Ensure your work area is ventilated and clean. Prepare a work desk, clean the surface with ethanol, and cover it with plastic sheets if necessary.
- Prepare Buckets: Clean buckets with lids using soap and water, followed by wiping them down with ethanol.
- Hand Hygiene: Wash your hands thoroughly with soap and/or gloves, and clean them with hand sterilizer or ethanol.
- Amount of Substrate and Mycelium Spawn: When working in a non-sterile environment, use a 15% to 20% weight percentage of spawn to substrate. For example, if you have 1000g of substrate (which is 80% of your total mixture), your total mixture should weigh 1250g. Therefore, add 250g of mycelium spawn to the 1000g of substrate. A 30L volume of wet substrate will probably weigh around 25kg. Then you will probably need around 4 liters of mycelium spawn for this stage.
- Store the left-over spawn and substrate in the fridge or in a cool area at a maximum temperature of 4 °C.
- If possible, prepare your substrate incrementally. Meaning that you pasteurize the next batch of the substrate mixture before the next step.
Mixing the Substrate and Spawn
Break the mycelium-inoculated substrate into smaller pieces and mix it with the substrate mixture in a shallow Samla box. Again,make sure that the substrate is not too moist. Squeeze it with your hands; no water droplets should drop. Aim for a homogeneous mixture to promote faster colonization and reduce contamination risk. Fill the box up to about 15 cm of its 18 cm height without overcompressing the material.
Managing Temperature and Environment:
- Temperature Considerations: Be mindful of the temperature differential between the substrate and the surrounding air, as significant differences can lead to fermentation and mycelium degeneration. This can affect both the material’s mechanical integrity and the mycelium’s biological efficiency. Using a species like oyster mushrooms is beneficial because they can grow in ambient or cooler temperatures.
- Storing the Mixture: Seal the box tightly and store it in a dark area with stable temperatures. During the summer, consider placing the boxes in a cooler location, like a basement. In winter, store the boxes indoors in an area that is not constantly heated to maintain a temperature of around 19°C.
Observing the mycelium taking over the substrate.
You should be able to see the white hyphae of the mycelium going into and around the substrate. If it looks to moist with droplets on the inner surfaces of the box, you may open the lid slightly to ventilate and place some microporous paper tape where there is an opening.
How to Spot Unwanted Organisms in Your Substrate: Discoloration and decay are symptoms of contamination. Contaminants have the potential to deplete fungi of their necessary nutrients or even cause their demise. Mycelium grown on contaminated substrates can harbour harmful organisms; thus, it's crucial for hive growers to keep that in mind while working. If you suspect there is harmful mould, do not smell it or similar.
Step 7: HIVE GROWTH
This process ensures that the hive modules are properly filled and prepared for optimal mycelium growth. The use of burlap and careful filling techniques helps fill the hive scaffolds with the substrate without leaving any voids.
Preparing Burlap Fabrics:
- Cutting Burlap Fabrics: Cut the burlap fabrics into 50x50 cm pieces. These will be used to cover the conjunction parts of the hive modules.
- Soaking Burlap Fabrics: Boil water and soak the cut burlap fabrics in it. Allow them to cool down while submerged in the water.
Preparing the Workspace and Hive Boxes
- Workspace Preparation: Clean and prepare your workspace.
- Cleaning Boxes: Clean the boxes that will be used for growing the hive parts. For the hive presented in the model above, you will need 4 large boxes, a minimum of 50cm by 50cm, and varying heights. You can use the "acclimatising box" used in step 6 for hive growth as well.
- Spare one clean box for the new bulk mixture.
Setting up the Hive Modules
- Arranging Burlap and Hive Parts: Place the soaked burlap fabric pieces at the bottom of each box. Then, place the 3D-printed hive parts on top of the fabric, ensuring the narrower openings of the channels face upwards. Spray the hive scaffolds with water.
- Adding Substrate to Mixture: Take the remaining pasteurized substrate (about 30 liters) and add it to the acclimatized mixture in a larger, clean bucket. Incorporate an additional 2 kg of fresh mycelium spawn, aiming for a homogeneous mix.
Filling Hive Modules with Substrate:
- Filling Channels: Start filling the channels in the hive modules with the substrate mixture. Begin from the side with larger openings, as the channel's curvature will facilitate smoother filling.
- Avoiding Certain Cavities: Note that the diamond-shaped cavities in the hive diagram are mostly reserved for wooden sticks and 3D-printed stabilizers. These do not require full filling.
- Using Tools for Narrow Cavities: For narrow cavities, use tools like long sticks, clean knives, or spoons to push the substrate into these areas.
- Ensuring Substrate Distribution: Gently tap the hive part to help the substrate settle. After filling from one side, carefully turn the part upside down, holding the burlap fabric in place, to fill from the other side. The substrate doesn’t need to be packed tightly.
Finalizing and Storing the Hive Modules:
- Securing with Burlap: After filling, place another piece of burlap fabric on the newly filled side and turn the module right side up again.
- Storing the Filled Modules: Once satisfied with the filling, close the lid of the box tightly. Store the boxes in a dark area with stable temperatures. During the summer, a cooler place, like a basement, is ideal. In winter, an indoor area with a temperature of around 19°C is suitable.
Grow for 14 days. Observe regularly without necessarily opening the boxes.
Step 8: HIVE GROWTH PHASE TWO
This is the process for handling and assembling the mycelial hive body once it has reached a robust state:
Inspecting and Preparing the Hive Modules:
- Removing Burlap Fabrics: Open the boxes containing the hive modules and carefully remove the burlap fabrics from the top layers of each module.
- Installing Stabilizers: In the diamond-shaped areas of each module, insert the stabilizer pieces. These areas should be filled with the extra spawn mixture. Carefully stack or interlock the hive parts, but leave the roof section unattached to avoid it becoming locked to the main body of the hive.
Transferring to a grow tent or tall plastic boxes:
- Relocating the Hive Body: Transfer the assembled hive body to a basic grow tent. You may need to remove the middle racks of the tent to accommodate the size of the hive.
- Further Stabilization: Allow the hive to sit in the grow tent for additional stabilization. This step is important for the internal strength and integrity of the hive structure.
Observing Mycelial Growth and Hive Integration:
- Monitoring Growth: Over the next 7 days, watch for mushroom fruits to emerge. This is a sign that the mycelium is actively growing and strengthening the structure.
- Checking for Welding: After 7 days, the first three parts of the hive should have begun to weld or fuse together. It's important to note that while some bonding will occur, the strength of this welding might not be very strong. Handle these parts with care to avoid damaging the newly formed connections.
Step 9: HONEYBEES IN THE HIVE
Following the fungal biofabrication phase (instructables, step 8), honeybees move in (by humans or swarm in naturally). This instructable does not involve the protocols needed for honeybee introduction into such a hive. It is recommended to discuss the options for housing honeybees with your local beekeeping school, a beekeeper friend, or someone with experience and expertise working with honeybees. We will share in the future in another instructable how we introduced a honeybee colony in our most recent prototype. We would like to share below how design thinking can support this ecological scenario, though.
Mutualism between honeybees and mycelial architecture is an interaction and cooperation scheme. In order for the nest enclosure to provide advantages to the bees, it is not necessary for the mycelium within the nest enclosure to be actively developing and consuming the organic parts continuously, causing it to collapse. The majority of the digestible parts in the substrate should already have been converted to mycelium, leaving it in its dormant stage after it has developed in hive forms, such as nest enclosures or internal modules. This means that the mycelia have moved permanently into the substrate-filled channels of the enclosure walls. The porous areas facing the inner nest have made it easier for the mycelia to form a biological relationship with the honeybees.
During the honeybee occupation period, nest-related substances such as beeswax, propolis, pollen, and honey should be able to fulfil their functions without being negatively impacted or even potentially aided by the fungal mycelia that we introduce. While, ideally, pathogenic organisms and toxic substances are inhibited.
The first image above reflects the hive geolocations where mutualistic events can occur. "B" tags indicate regions where honeybees benefit from mycelia, whereas "M" tags indicate the opposite:
B1) The water homeostasis has a big impact on the colony's wellbeing. The upper parts of the hive's inner surfaces are one of the areas that require consideration in a hive regarding humidity control. Some beekeepers "quilt" their hives by adding an extra-thick layer of water-absorbing materials, such as wood chips held in place by a permeable canvas, on top of the comb storage modules. The porosity of the canvas and wood chips allows warm, moist air to pass through the hive's upper surface and up until it meets the cold surface of the roof material, wetting only the top part of the quilt box and preventing water droplets from falling directly on top of the bees, brood, or honey storage areas. A similar effect can be achieved by changing the porosity and thickness of the 3D-printed material that holds the fungal material in those areas, thereby providing the water that mycelia requires.
B2) Fungiinsulate the nest area.
B3) detoxify the storage where environmental hazards are packed and
B4) The fruit bodies feed the honeybees with their highly nutritional and medicinal biomaterials. CO2 levels may exceed 5000 PPM, while lower CO2 levels may, depending on the fungus species and strain, lead to fruit formation.
B5) The living mycelium plays a role in luring bees to their homes. By this point, the mycelium has developed highly potent organic volatiles, which are excellent insect attractants.
B6) Self-healing (saprophytic capacities and aerial growth of mycelium) seals the nest enclosure.
M1) The nectar and water brought by honeybees to nest can be resources for mycelial growth.
M2) The honeybees’ dynamic regulation activities may keep the mycelia of the beehive alive, healthy, and sensitive to its environment. The honeybee’s metabolic production of humidity and carbon dioxide can create a favourable incubator for mycelia, causing a gradient of density from within the beehive wall towards the outside. This spot is where we place the climate sensors.
M3) Mycelium would also respire and release CO2 towards the nest space. Because CO2 is heavier than O2, it would sink to the heights where the nest entrance is placed in the hive space, requiring the bees to use additional fanning energy to keep the CO2 levels constant.
M4) Dark spaces are already favoured by mycelia.
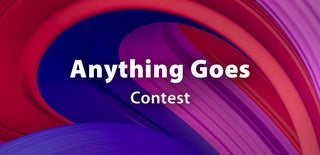
Runner Up in the
Anything Goes Contest