Introduction: Cast Pewter Robot Badge
So, I had just published a pewter-casting Instructable, when I suddenly realised I was missing a trick: detailing.
I had to spend a few hours driving, and cogitated as I drove, working out a way to do it: engraving.
Welcome to another step in me learning how easy it can be to cast pewter...
Step 1: Materials, Tools and Brain Damage
Materials:
- Pewter
- 3mm MDF
- Butterfly badge-pin
Tools:
- A hot air gun
- Tongs or pliers (more than one pair)
- Clamps
- Something to cut MDF (I used my laser cutter, because I can, but ordinary hand tools are absolutely fine)
- Ladle.
- A heat-proof surface over which to work. I used an old baking tray.
The "ladle" needs to be steel, but beyond that there are many options - you could use an actual soup ladle, use a serving spoon or cut a clean food can into shape. I found a set of measuring spoons - the smallest turned out to be perfect for the ingot of pewter I bought, and had a flat bottom (so balancing was a lot easier).
There are lots of suppliers of pewter online, but I always recommend supporting a local physical craft store if you can. Use lead-free pewter - the presence of lead doesn't really affect the use of the finished item if you're making a something nice to look at, but you don't really want it on your skin, and (worse) you don't want to breathe in hot lead fumes. Lead is a cumulative neurotoxin - each exposure damages your brain a little more.
If you are working indoors, please make sure that you have plenty of ventilation - open windows and doors, have fans maintaining an air-flow away from you (and especially away from any children or pregnant or nursing mothers).
Step 2: Design Notes
I took the image of Robot from this old forum topic - I imported the image into Inkscape, and the drew over the picture to make a slightly simpler vector image.
Drawn in thick lines, I then turned each thick line into a pair of thin lines (Path -> stroke to path), and created the mould files from that (attached in several formats)
If you use my ECP file, notice that the actual drawing of Robot is doubled up: the lines are engraved, and then vector-cut.
Making the mould needs three layers of MDF.
The central layer is the outline of the Robot, with a small notch at the top to let you pour in the molten pewter. The front layer is just a rectangle of MDF with a hole to pass through the pin of the badge-back, and the back layer includes the engraved detailing.
The pin for the badge was a bit too wide for the mould, so I just clipped off the sides with tin-snips.
Step 3: Clamp
Just what it says - get the parts lined up, and clamped as firmly as you can.
I didn't push the spike of the badge-back all the way through the hole in the mould - the plan is for pewter to flow all around the pin & hold it firmly in the metal.
You want the parts clamped as firmly as possible, held vertically over a surface you don't mind spilling molten pewter over.
Step 4: Melting Your Pewter
The joy of using pewter is that you do not need a furnace, just a ladle.
If you have a small metal ladle, then you're good to go. You could also use a large spoon (with a pouring lip bent into the side of the bowl), or cut down an empty can to make a ladle.
One advantage of using the measuring cup I used (or an old can) is that it has a flat-enough bottom to stand without spilling. I put my pewter ingot in the ladle, and blasted it with the heat gun until it was melted. Standing the ladle on the part-open vice meant I could heat it from above and below.
Don't forget that metal conducts heat, and the handle will get hot - use the pliers to pick it up and pour.
Step 5: Pour Your Pewter
With the mould propped firmly in a vertical position, gently and carefully pour molten pewter into the funnel-shaped cut-out of the mould.
The design I was making needed only a small fraction of the pewter in the ladle - the mould filled quickly and over-flowed.
Step 6:
After the pewter has had time to solidify (officially just 2-3 minutes, but I give it five), release the clamps of the mould.
The pewter seemed to glue the layers of MDF together - I had to slip a knife blade between the layers to prise them apart.
Resist the temptation to immediately pick the badge up with your bare hands - despite being solid, it might still be hot. It will only take a couple of minutes to cool enough to handle, though.
Unlike the smooth rocket badge, the textured surface of the mould seemed to "grab" the pewter - parts of the MDF got pulled off the textured layer, and I had to break the central layer to extract the badge.
Step 7: Finishing
Once the pendant is set, you may have excess material, known as a sprue.
These need trimmed off - a mall pair of tin-snips easily removed the bulk of the sprue, and then a pair of toenail clippers removed most of the rest. Final trimming was done with a Stanley knife and a fine file.
MDF is really just thick paper, so the last scraps of adhered material came off after soaking in hot water and scrubbing with a stiff-bristled brush.
Dry it off, and you're ready to wear it - just remember, it's a bit heavy for a thin shirt, but ideal for a jumper or suit or coat lapel.
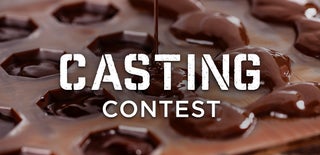
Participated in the
Casting Contest