Introduction: Chess Salt and Pepper Mills
In this instructable, I will show you how to turn your own wooden salt and pepper mills that look like chess pieces.
After turning a few wooden bowls I was way too overconfident and decided to make these mills as my first project turning end grain. I ran into a few issues, but am really happy with the result. The first time I made the mills more than a year ago I took hardly any pictures because I didn't have any dust prove camera lenses. Now, thanks to my recent contest wins on Instructables I was able to get one (thank you guys!).
I remade the mills since I couldn't part with mine and I wanted to give them to my Dad who has been obsessed with the Queen's Gambit lately and chess all his life. So while I remade the mills I finally took enough pictures to write an instructable.
I uploaded the STL files of my design to the next step, should you not have a lathe and want to 3D print the pieces.
By the way, now I would really like to make a checkered cutting board, but I haven't found the time.
Step 1: The Design
Before I started, I made a few design choices. Chess figures are supposed to have a wide base that allows them to stay stable. A small column that doesn't obscure the pieces behind it and a clear distinguishable feature to tell them apart.
I decided to pay homage to the so-called Staunton design wood-turned by "The John Jaques Company" in 1849 and popularized by Howard Staunton (April 1810 – 22 June 1874) who was one of the best chess players of his time.
I saw that you can buy mills that look like chess pieces online, but they either had a wide base, used metal parts on the outside, or were painted.
The first choice I made was to go with a base that is smaller than the ones usually used on chess pieces. I tried using a wider one, but it didn't work well because they were hard to aim at the food. My goal for these mills was to combine design and function and a mill that is impractical doesn't serve the purpose.
The next choice I made was that I wanted to use only natural wood and no exterior metal parts, dyes, or paint. I also wanted to use a ceramic grinder mechanism, since there is no point in spending time turning them and then using a cheap mechanism.
With these parameters, I went into Fusion 360 and came up with the design you can see here.
I uploaded three pdf files you can print should you want to replicate my design (the measurements are in millimeters). All the blue lines are required by the mechanism. Otherwise, you are free to choose any form you like.
Before starting, I 3D printed the head of the king, to make sure that the mill was comfortable to use. Luckily it was, so I was ready to begin.
Step 2: Tools and Materials
Materials
- Wood: I used birch and walnut; both pieces need to be about 70 mm x 70 mm x 250 mm; try to find pieces whose grain is as straight as possible
- Mechanism: CrushGrind (e.g. from amazon.com here*, the 195 mm one is long enough); I have used the mechanism quite a few times by now and can highly recommend it.
- Wood oil that is food safe (+ a towel to apply it)
- Sanding paper: I used 320, 400, and 600 grid
- Optional: Ball bearing: 61705 2RS1 25 mm x 32 mm x 4 mm **
Tools
- Lathe
- Safety gear
- What type of tools you need depends on your preference. If you are experienced, you can probably mainly use a skew chisel. You can also use carbide tools, but traditional tools will give you a superior finish. I used:
- Roughing gouge
- Spindle gouge
- Skew chisel
- Parting tool
- Crush Grind tool (e.g. from here*); You can also glue the mechanism in place if you don't want to buy one or make your own
- For mounting the wood:
- Multi prong center
- Tailstock live center
- 4 jaw lathe chuck, with jaws to hold a 60 mm tenon; optional: jaws to fit into a 22 mm hole
- Drill bits: 22m, 26 mm, 38 mm, 42 mm + a drill chuck (there are also special tools that do most of the drilling at once, but you don't need one unless you would like to save some time.)
- Caliper, pen, ruler
- Thin saw
- Metal saw and file
- Metal tube to push the mechanism in. The outer diameter has to be about 40 mm.
- Unless you are fairly strong, you will need a vice
- If you would like to mill the indents into the headpiece of the queen as I have done then you will need an indexing setup (that can be divided by 12) for your lathe, as well as a possibility to mount a milling machine. I used a milling bit with R = 6 mm / A = 12 mm / B = 9,5 mm (check the image below for reference)
* Affiliate link. I earn from qualifying purchases. Thanks a lot for the support!
** As you can see in the title image, I used ball bearings the first time I made the mills. I was a suggestion in a German woodturning forum, but later somebody posted a picture of the gears that started to rust. Apparently, due to moisture and salt, this might happen. Luckily this hasn't happened to me, but I wanted to warn you. So the second time I made the mills, I didn't add bearings and they turn fine. It is your choice if you would like to make super smooth mills and are willing to risk them getting rusty, go with the bearings, otherwise don't.
Step 3: Let's Get Started
When you made it this far then I'll assume that you feel capable to replicate the design. My goal for this instructable is not to teach the fundamentals of woodturning, but to show you how I created the mills. If you are interested in learning woodturning then I highly suggest watching these videos before getting started.
Woodturning is dangerous and I don't want you to get hurt, so please make sure that you know how to use the tools and please take all necessary safety precautions.
So let's get started. There are many different possibilities of how you can manage to make the parts. Here I am going to show you how I did it.
I started by mounting the wood between the centers and used the roughing gouge to turn it to a diameter of 64 mm. Afterward, I used the skew chisel to add a tenon to the side of the tailstock that matches my 60 mm chuck jaws. I had to do this because my drill bits and lathe weren't long enough to drill through the whole piece at once.
Next, I drew on lines with a pencil to mark all the low and high points of my design. The bottom of the column has to face the tailstock.
I suggest creating the column of the king and the queen at the same time. This way you will have to change the different mounting tools less often.
Step 4: Creating the Profile
Next, I used the skew chisel to cut to the low points and a spindle gouge to create the profile. Use the calipers to see if you need to go any further. If you are experienced, you can probably create the whole profile with a chisel.
Don't make the wood above the neck too thin, we will need to add a 60 mm tenon to it later.
Step 5: Finishing the Profile
Just move along the profile. A parting tool works great to quickly get to the right diameter.
I didn't, but it is probably a good idea to sand your piece at this point.
Step 6: Parting Off the Column
Next, we are going to add a 60 mm tenon to the other side of your piece of wood. It is going to help us to hold the headpiece in place later on.
Afterward, we are going to add another tenon right behind the neck and part the column off. The more space you need for the tenon and parting the piece off, the more the grain is going to be disrupted. But since the rings on the head are slightly smaller than the ones on the neck, it is not going to be too noticeable.
Once you've finished creating the tenons you can part the column of your chess figure off.
Step 7: Drilling
Now we are going to use our four jaw chuck and place our column bottom first into it. Mount the drill chuck and a 26 mm drill bit into the tailstock.
Like I wrote before, my drill bit wasn't long enough to drill all the way through. So I drilled to about the halfway point. I only had a 25 mm drill bit, therefore I had to sand the opening slightly bigger.
Make sure to go slow and to constantly remove the shavings, to prevent the drill from getting caught.
Step 8: Finish Drilling
Once you have drilled to about the halfway point, you can turn the piece around and drill the hole all the way through. Afterwards, use a skew chisel to remove the tenon from the bottom.
Now you can start drilling the bigger holes that are needed for the mechanism. Start with the 42 mm drill bit and drill to a depth of 19 mm. Afterward, use the 38 mm drill bit and drill to a total depth of 53 mm.
Step 9: Cutting the Notch
As you can see in the first picture, the mechanism needs recesses for it to work properly. You can either cut the small pieces of plastic off and glue the mechanism in place or cut the notch on your lathe.
I prefer cutting them and use a special tool by Robert Sorby to archive this. The shoulder of the tool gives an accurate position of the recess required for the base section of the mill. You can of course also create your own tool.
After I was done with the holes I sanded the piece.
Step 10: Finishing the Column
In order to remount the column, you will need a jam chuck. You can either create it from another piece of wood you have lying around or use some of the extra wood, you will have from this project since 25 cm is a bit longer than what you need. Simply mount it into your chuck and turn it to a diameter of about 42 mm. Constantly test if your diameter is right by trying to fit the column of your mill onto it.
Place the column of your chess figure onto your jam chuck and finish the neck of your piece, as shown in the pictures. If you would like to add a gear, you will have to do it now.
Don't forget to sand the neck and you are done with the body.
Step 11: The Column of the King
As I have written a few steps ago, the column of the king is exactly the same as the one of the queen (except of course the type of wood you are using.). So it is a good idea to create them at the same time. It doesn't really matter, if you don't follow my measurements precisely, but you should check and see whether your two figures match.
Step 12: Starting With the Coronet
Usually, the queens feature a coronet topped with a tiny ball (a monde), but I decided not to create the tiny ball in order not to risk it breaking of during usage later on or during the assembly.
You can see all the measurements I used in the first image (in millimeters). Since we did add a tenon to our cylinder a few steps ago, you should be able to clamp it into your 4 jaw chuck.
Start by making a clean cut on the side that is held by the tailstock with your skew chisel.
Step 13: Adding the Profile to the Coronet
Next, we are going to turn the profile, the same way we have done the column (adding the low points with the skew chisel and connecting them with the spindle gouge). You can finish the top of the coronet, but as you can see, I haven't since I wanted to test the setting of my mill without ruining the piece.
Once you are happy, you can sand the parts that you have finished.
Step 14: Drilling Into the Coronet
Next, we are going to drill the hole. Use the 22 mm drill bit and drill to a depth of 36 mm. After we have finished drilling the hole, you will either have to cut a notch for the mechanism or cut the plastic tags off and glue it in place later.
I decided to cut the notch, which can also be done with the Robert Sorby tool. There is a line on the tool, that tells you at what position the notch needs to be. Simply place it straight on your tool rest inside of your hole at the correct depth and slowly move it to the outside.
Once you are done with the inside of the coronet, you can part it off. Make sure to leave enough space for the top of it.
Step 15: Setting Up the Mill
Next, we are going to cut the indents into the coronet. I am using a very cheap construction that uses this* slide table, that I can put into my tool rest base. While it may not be perfectly precise, it has worked great for everything I wanted to do with it (tell me should you be interested in seeing more pictures of it).
As you can see, I used a four-jaw chuck to hold the coronet in place. I tried using a wooden jam chuck when I first attempted making the mills but accidentally cracked the piece and didn't want to risk it again.
Before I could start, I had to make sure that everything is straight. To do so I am using a steel square with a stop. As you can see in the third image, I aligned the bit with the center of my wooden piece.
Before milling all the way through, I made a few tests and ran into problems. The wood either showed burn marks or the cut wasn't very clean. So I decided to test what would happen if I would drill straight into the piece instead of milling from one side to the other and to my surprise it worked a lot better (as you can see in the fourth picture).
* Affiliate link. I earn from qualifying purchases. Thanks a lot for the support!
Step 16: Finishing the Coronet
Once I was happy with the tests I did, I milled the 12 indents. Afterward, I very carefully finished turning the form. Make sure that your tools are sharp to prevent cracking.
Once you are happy with the form, don't forget to sand the piece.
Step 17: Tuning the Crown
You can see the measurements I used in the first image of this step (once again they are all in millimeters).
As for the coronet, use your four-jaw chuck to hold the piece in place. Once you are happy with the profile, you can drill the hole and cut the notch on the inside.
As you can see I also added the rough form of the cross. Once you are done sanding, you can part the piece off.
Step 18: Making the Cross
You can of course leave the cross as is, but I didn't want it to be round. Therefore I used my four-jaw chuck to hold it in place and a saw and a chisel to cut it to a form I liked.
Don't forget to sand it once you are done.
Step 19: Applying the Finish
If you look closely at my pictures you can see that there were some sanding lines visible. Usually, when sanding a piece of wood, you would go with the grain to hide the sanding marks. Obviously, when you are sanding end grain pieces on a lathe, you will go against the grain.
Instead of going with the grain after switching from one grid to another (which would be the correct way). I decided to just sand with the grain once at the end with a grid of 320. Don't go any finer than that in order to allow the oil to properly penetrate the wood.
Once you are done sanding, clean the pieces to remove the sanding dust with compressed air or a towel and apply the oil according to its instructions. In my case, I used three layers, waiting 20 minutes in between them and afterward giving the pieces 24 hours for the oil to harden.
I used a special oil for light-colored woods on the queen because I didn't want it to go any darker.
Step 20: Shortening the Mechanism
You can add the mechanism after the oil has hardened. In order for it to fit, you will have to shorten it slightly.
Use a ruler and mark a line at a distance of about 120 mm, as shown in the first picture. Cut slightly above it with a metal saw and use a metal file to add a bevel, as shown in the third picture.
Step 21: Assembly
Now we are finally ready to assemble the mills. I placed a towel over my four jaw chuck to prevent it from scratching up them up and cut a hole into it so that the pole from the mechanism can be pushed through it.
As you can see in the second picture, I used a metal tube to push the mechanism in place with my lathe. Quite a bit of force is needed and I am not strong enough to do it by hand.
I used a vice to press the mechanism of the crown and coronet in place.
All that is left to do is to fill the mills with either salt or pepper and push the coronet and crown onto the columns.
Step 22: Murphy's Law
Murphy's law typically states: "Anything that can go wrong will go wrong" and quite a few things went wrong when I first tried making the mills. Mainly because, it was my first time turning end grain and making a mills.
I decided to show you all the problems I faced so that we can learn from them.
The first picture shows a minor problem I had after I was completely done with the column of the queen and tried to remove it from the jam chuck. I didn't place my tailstock far enough away and hit the live center with my piece, which as you can see left an indent. Luckily it was close to the inside so that it can't be seen once the mill is assembled, but I was still a bit annoyed.
The second picture shows what happened the first time I tried to make the coronet of the queen. Instead of using jaws to hold the piece in place, I used another jam chuck. While I was pushing my piece onto it, I heard a cracking noise but didn't think much of it. After I was completely done and pushed the mechanism into it, the piece cracked. If you look closely you can also see another flaw. The woodturning oil for lighter-colored pieces will show unevenness quite strongly. So when I remade the piece, I paid a lot of attention to the sanding to get a more even finish.
The third picture shows another issue I had the first time I tried drilling the hole. Instead of using a tenon at the bottom of the body as I have shown here, I tried using a jam chuck and an auger. I drilled way too fast, the part got loose and the auger completely destroyed the opening of the hole.
I hope you are not going to run into any issues and are going to enjoy making the mills.
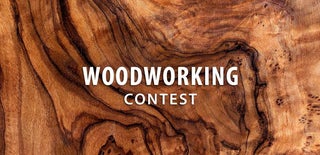
First Prize in the
Woodworking Contest