Introduction: Concrete Loudspeakers
Concrete is a wonderful material for speaker boxes: it's strong, stiff, dense, non-resonant, and (to me) beautiful Concrete's other ace is that it can be made into a variety of different shapes. For this project, I went with a simple rectangular sort of shape, because that's what my friend wanted :) However, using this method, you could make any kind of shape.
To make speakers, you'll need:
- Speaker drivers (woofer, tweeter, full range, whatever) - I used the Continuum kit from Meniscus Audio
- Crossover
- wires
- Binding posts
- Screws
For the boxes you'll need:
- Cement + sand + glass fibers OR premix. I used VOH from Sika and some additional fiber for the backing coat
- Acrylic bonder/fortifier - like this from Home Depot
- Some wood for front/rear baffles - 3/4 MDF from your local big box
- Gasket material - like this from Parts-Express
- Construction adhesive. I used this stuff which will glue anything to anything
- (Optional) concrete stain
- (Optional) Wood veneer
- (Optional) concrete polishing pads and a sander (or strong elbows)
For the molds:
- Melamine-covered particle board - from the local big box
- 3/4" angle aluminum - ditto
Tools:
- Router
- Screwdriver
- Saw
- Caulk
- (Optional) texture sprayer - like this one from HF
The main thing you'll want to do is ensure you have the best speaker components. If this is your first build, I _highly_ recommend getting a kit from Meniscus, Parts-Express, or Madisound.
For this project, I'll walk through the process of building the teal speakers I built for my friend, Noah. They are stained concrete, but (of course) you can keep them raw. You can see a similar project with the Linaeum tweeter that's in raw concrete.
After you've gotten your supplies. Plan the work carefully. Concrete isn't as forgiving as wood, so you'll need to know exactly what dimensions you need where.
Step 1: Build Some Boxes!
Once you have acquired your material. You need to build the boxes.
The first step is to build a mold.
Cut your melamine board to the correct size and screw it together. Then cut the aluminum angle to size and screw it in. You can see from the photo how to align it. The angle will be the edges of the box and determine the thickness of the material. Next, run a thin beat of silicone caulk around all the seams to prevent leakage.
The next step is to mix up the face coat, load it into the hopper of the texture gun and spray it in. Follow the instructions of the cement you are using. There will not be any glass fiber in the face coat. The mix is thin, it's got to spray through the texture coat. This coat is thin - only about 1/16 of an inch. It will set up quickly, so next step is to mix the backing coat. Mix it quickly! You'll want to include some glass fiber and some acrylic fortifier to increase the strength. You'll be looking for "peanut butter" texture in your backing coat.
After your backing coat is mixed, pack it into the mold, into the face coat to ensure a good bond. Work quickly, packing the same side on each mold - i.e. do the bottom for both, the left side for both, etc, this will let the cement set up before it has to hang upside down. The backing coat will set up very quickly, but you don't want your walls to be hanging upside-down while they are too liquid.
Once the GFRC has set up, you can de-mold. After de-molding, do some polishing (if desired) and fill pinholes by mixing acrylic with the cement (no sand) and rubbing it into the holes; polish again. I took mine to 400grit. Then I stained the concrete with floor stain in teal.
Finally, I cut some braces to go around the edges out of some 1.5" scrap lumber I had laying around and glued that around the perimeter of the front and rear opening. I used polyurethane construction adhesive for maximum sticktuitness.
Step 2: Woodwork (for Concrete?)
Since I'm using a wood (mdf) front and rear baffle to take my concrete box to a fully-enclosed speaker enclosure, I needed some front and rear baffles. To do this, I cut some 3/4" MDF to the size of my speaker boxes, then rounded over the edges with a router. I also used a 3d printed speaker template to match my (somewhat oddly shaped) speakers. This enables me to have the speakers sit flush to the baffle, reducing diffraction.
The next step (and maybe the hardest of the whole project) was to veneer the baffles. Veneering the corners was very tricky. I used paper backed teak veneer and stuck it to the baffles using wood glue that was allowed to dry, then heating the veneer with an iron to reactivate the glue.
After sticking the veneer on, I finished it with some danish oil and a spray of matte polyurethane. I probably should have done one or the other, btu it ended up looking pretty nice anyway.
I then added the speakers to the baffles and did some preliminary wiring.
Before the baffles were mounted, I used some spray adhesive to mount denim insulation to the interior of the box to absorb some of the rear wave.
To mount the baffle to the front, I drilled holes through the perimeter bracking and screwed screws into the front baffle. Be careful and don't overdo it! A little bead of construction adhesive acts as a seal and glues everything down. The screws are really just there to hold stuff in place while the glue sets.
Finally to mount the rear panel, I screwed in from the back, drilling and countersinking the screws. Before finally screwing it in place I added some speaker gasket to keep things airtight.
Step 3: The Home Stretch: Crossovers and Final Assembly
To finish the speakers I had to assemble the crossovers in the tight space between the perimeter bracing. This was more work than I anticipated and I ended up having to use some acrylic (because that's the only thing I had). Eventually, I got the crossover wired up and mounted, then it came time to finish wiring, add the binding posts to the rear panel and seal it up for good.
A note on crossover assembly. It's not the easiest thing, you realy have to be careful where components go to minimize interference between the inductors. Here's a handy guide
Once everything was closed up, I could listen to them, finally. They sound great!
But they weren't for me, so I had to pack them up and send them to San Jose for my friend Noah to enjoy. He's still listening to them now!
Hopefully that gives you some idea of how to build some concrete speakers if you are so inclined. Let me know if you have any questions!
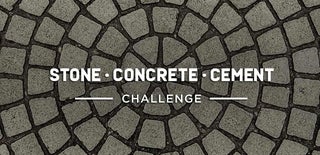
Participated in the
Stone, Concrete, Cement Challenge