Introduction: DIY 3D Printed Windshield Washer Nozzle - (And How the Design Process Works)
Do you have a car that has all the parts for the windshield washer, except for the nozzle? Is the car old/weird enough that Tesla Model 3's will reach stated production numbers before you find a replacement? Do you have access to a 3D printer?
Why not just make your own!
That's the state I found myself in, recently. I have an old Comuta Car (Cheese-wedge shaped electric car from the 80's) that has every component of the foot-operated windshield washer except (you guessed it) the nozzle. So I decided to design one myself, and create an instructable documenting the process.
(Side note: I know the Model 3 has reached production goals now- Good for Tesla! So far I've seen 5 in the wild...)
Step 1: Measure and Research
The first thing to do is to get to know the requirements. For my ComutaCar, all I needed was a few measurements. If you care about how it matches the car, maybe see if you can find a close-up that happens to show the nozzles. I couldn't, so I went with a simple design in a color that matched the rest of the car.
Here's what I measured:
- The diameter of the hole on the hood where the nozzle goes
- The thickness of the hood
- The ID (Inner diameter) of the tube that goes to the nozzle
- The OD (Outer diameter) of the tube
Here's some things I should have measured:
- The angle the spray should be at to miss the wiper blade and hit the window in the desired spot
(My car has the single wiper blade in front of the nozzle- I was lucky and the spray happened to pass right through the middle of the blade- But this may be something you'll want to watch for)
Write all the measurements down, and if there's anything else that seems like it'd be good to measure, do that too!
Step 2: Design
Now the time has come to design the nozzle.
I like to use Fusion 360, but you can use your preferred modeling software.
Here are some things to consider (besides the measurements previously) when designing:
- Printability: Does it have too many overhangs, or no flat area that can be placed on the print bed? Some of this can be taken care of with supports, but not always.
- Aesthetics: This is where you make the rules. How should it look? Because I'm not super skilled in Fusion 360, I went with something pretty simple looking.
- Spray pattern and hole: This is kinda tricky. My design just spits out a stream, which should work, but probably isn't as nice as the original nozzle. In general, you want as small a hole as is possible to print. If you want a really nice spray pattern, do some research, or just play around until you get something that works.
- Printer tolerances: Your printer can only properly print holes down to a certain size. Print smaller, and you run the risk of clogged holes. My original design had a tiny nozzle hole, and a tiny tube for the fluid- Both got plugged. I figured out I could make them both much bigger, and they worked fine.
Some of these, especially printability and tolerances, are applicable to many design processes, in 3D printing and other manufacturing processes, not just making your own windshield washer nozzles.
You'll likely create several iterations of the design. Don't worry! This is a normal learning and designing process, and it's exactly how all engineering works.
Step 3: Print
Now that you've got your design, it's time to print it, then test fit it to make sure it's how you want.
Here are a few considerations while printing:
- Infill: I printed with 100% infill. This probably isn't necessary, but I felt better about the strength of the final part, and 100% infill also lowers the chances of the part getting filled with water.
- Orientation: This is important. My part has a nice flat piece on top, and everything else prints fine in that orientation, so I oriented that part to be on the build plate. This is an important thing to consider when designing, as well.
- Bed adhesion: Will your part stick to the printer bed well enough? I tried with and without a brim/skirt on my printer, and with the heated bed and PLA it seems to work either way. If you don't have a heated bed, you may want to use a skirt/brim.
As for material, I used the ever standard and trusty PLA. The rest of the car's body is vacuum-formed ABS, but PLA will work fine. You may want to choose a plastic that won't degrade with exposure to the elements, if long-lasting durability is important to you in your replacement nozzle.
Step 4: Clean Print (Or How to Deal With Tolerances and Threads)
In some cases (such as threads), there is no good way to compensate for tolerances in the design.
Luckily, there are methods to counteract this. My design, which includes a 1/4-20 thread, didn't print with the threads sharp or small enough to thread a nut onto, because printers aren't usually that precise. However, it created a base that was pretty close- Close enough to use a thread cutter to clean them up.
Hopefully your washer nozzle isn't more complicated than this, but if you'd like the print to be a little cleaner, there are several methods to making it pretty. I don't care, except for the threads, so I left mine rough. You can sand yours, or paint it/sand it, or whatever you desire, until it's finished how you like it.
Step 5: Test Fit and Spray
Now that it's printed, it's time to test it and make revisions before the final product.
My original design had holes that were too small (and got clogged), and it was (in general) smaller than I expected. Thankfully Fusion 360 has a feature that allows you to edit specific things without redoing the whole design, so I widened the holes, thickened the part that the tube slipped onto, and widened the top nozzle part quite a bit.
Make sure it fits wherever you plan to put it, matches up with whatever you plan to attach it to, and looks how you wanted it to.
If you can test the spray without fully attaching it, go ahead. I was lucky, and mine just happened to pass through the middle of the wiper blade sitting in front of it. If yours doesn't spray satisfactorily, it's back to the design process for you! Don't worry, this is a normal part of engineering anything.
Step 6: Attach
This is probably going to be the least applicable part for most people. Nozzles are attached in many different ways, and I can only show you how mine is attached.
Mine attaches by sitting in a hole in the hood. The wider nozzle keeps it from falling through the hole, then a bolt is threaded onto the lower part to keep it in place. A rubber o-ring that sits in the channel on the underside of the head seals it from water, and keeps it snug to the hood and unable to move.
Step 7: Finished!
Hopefully at this point, you've made yourself a replacement nozzle, and learned some about design and manufacturing in the process. I'll bet you didn't think there could be so much involved in making a simple little washer nozzle...
Leave ideas, tips/tricks, or nostalgia for the cheese wedge electric car below!
Finally, if anyone out there actually has a ComutaCar or CitiCar, and it needs a nozzle, I'll attach the file here. It's licensed under a CC BY 4.0 license, which means it's free to use, modify, and distribute, so long as you give me credit for the original work. (You'll also need a 15MM OD/14MM ID/ 2MM Dia O-ring, and a 1/4-20 nut).
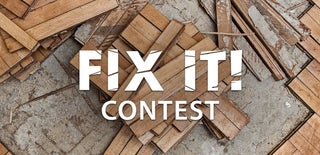
Participated in the
Fix It! Contest