Introduction: DIY Epoxy Beach Glow Table
In this Instructable, I show you how I made a beach-inspired epoxy glow table. Learn how to embed objects in resin and how to make epoxy glow in the dark without lights.
Even if you don't need this type of table, the techniques covered in this build can be directly translated toward other epoxy wood projects.
There are several things which are difficult to fully explain with words and images, so be sure to check out the video tutorial above.
Supplies
Step 1: Choose and Mill Wood
I have a locally owned Cypress sawmill not too far from where I live. During one of my visits to pickup cypress wood for a different project, he gave me a raw piece of new growth cypress. I liked the light color, grain pattern, and the fact it was in the trash pile. I like bringing trash wood back to life.
It is vital to use wood with straight sides, square ends, and a flat surface. Ultimately, it reduces frustration and makes the project so much easier. If you don't have the tools to mill wood, find a local sawmill to mill it for you. Also, you can pay the wood dealer you purchase it from to mill it for you.
First, I used my Japanese hand saw to cut off the end of the Cypress. The live edge cypress did not have a straight side to rest against my miter saw fence. Therefore, it was unsafe to cut with anything but a hand saw.
Next, I used my festool track saw to rip the wood down the middle with 2 passes rather than all at once. Again, the wood did not have a straight side so the table saw was not an option. Additionally, I find myself using my table saw less and less now that I have this Festool track saw.
Then, I ran the live edge cypress through my surface planer to get each side flat. Luckily, the cypress had one flat face even though it still needed to be sanded. So, I was able to get the other face flat by referencing the face which was already flat.
Finally, I used my miter saw to cut one end of the wood at 48". I flipped the wood over and cut the other side at 45". Remember, one side of the wood has a live edge which cannot be placed against the fence of the miter saw. So, I had to rotate the the wood and flip it to ensure the flat side stayed against the fence.
Step 2: Clean Live Edge
I used my Festool RO125 sander to clean up the live edge side of the cypress. Any random orbit sander will work just fine.
Next, I used my wood carving tools to remove the loose debris for 2 shallow wood cavities. I vacuumed the cavities to make certain they were clean.
Step 3: Prepare Resin Mold
I used a thin piece (1/8") of dry erase board large enough to fit the live edge river glow table. I presume this is melamine, but not entirely sure.
First, I wiped furniture wax on the surface to ensure the resin would not adhere to it. Also, I've heard vaseline works just as well as furniture wax.
I placed the wood on the melamine with the live edge facing inwards. Using my combination square, I made sure each piece of wood was pushed in 3" from the melamine. This step saved me an additional step later in the project of squaring the sides of the table. Since each side was cut with my track saw, I knew they were perfectly. So, no need to get them straight again.
Then, I used a scrap piece of wood with F-clamps to secure the wood to the melamine. I used silicone caulk to seal the inside of the live edge river to prevent resin from seeping through. Also, hot glue works just as well as silicone.
After I finished securing and sealing the river table sides, it was time to complete the mold by adding the two ends.
First, I cut 2 pieces of wood the larger than the width of the river. I covered them with packing tape and wax. The exact length doesn't matter as long as it is wider than the river.
Next, I used my brad nailer with 18 gauge 1.5" brad nails to secure them. I used brad nails because they are quick and the holes are easy to cover up when nailed into end grain. Hot glue is a good alternative to brad nails.
Then, I sealed each end with silicone to prevent the resin from leaking.
Step 4: Mix Epoxy and Glow Powder
The first epoxy resin pour consisted of 48 ounces of resin and 4 ounces of glow powder.
After the epoxy resin was properly mixed, I tested the glow powder to verify the color with a black light.
Next, I added 4 ounces of green glow powder (phosphorescent pigment powder) to 48 ounces of resin. Art n Glow recommends using a 4:1 ratio of resin to glow powder; however, I feel this is a bit overkill for my river table projects. So, I use a 12:1 ratio of resin to glow powder and this works fine.
Once the glow powder and resin were mixed thoroughly, I poured the resin in the river table. As I poured the resin, I moved back and forth to each end of the table. I used my torch to remove bubbles.
Step 5: Add Sand
After the first layer of epoxy resin cured for 24 hours, I added pool sand. I sprinkled enough pool sand to lightly cover the top.
Step 6: 2nd Epoxy Pour
I mixed 48 ounces of resin and mixed per the instructions. Once the resin was completely mixed, I added 1 drop of transparent blue dye.
Next, I poured the resin slowly in the live edge river glow table. As you can see, the resin pushed the sand to the side. I used my ruler to spread the sand evenly on the bottom of the live edge river table. The ruler helped me create a natural pattern with the sand similar to the ocean floor. I made certain the sand was thin enough for the glow powder to shine through.
Step 7: Add Sand Dollars
I used my paint stick to push the sand dollars to the bottom in a random pattern. Luckily, the sand helped create somewhat of a suction.
As I pushed the sand dollars down, a small amount of sand came through the holes in the sand dollars. This created a very natural look that was completely unintentional - I love when that happens. :)
Step 8: More Epoxy Pours
After the resin was completely cured (24 hours) from the second pour, I lightly hand sanded the epoxy resin river with 220 grit sandpaper and proceeded with the next pour.
I mixed 48 ounces of resin with 1 drop of transparent blue dye. I poured the resin from one side of the table and allowed it to flow evenly to the other side. I used my heat gun to move the resin around and my torch to remove the bubbles.
I repeated this until I filled the river with epoxy.
Keep in mind, I could have used deep pour epoxy and combined many epoxy pours into 1 pour. However, pouring epoxy in layers allows me to control the underwater effect of the epoxy better.
Step 9: Repair Wood Defect
I filled the wood cavities in the live edge river glow table.
I mixed 12 ounces of epoxy resin. Next, I added one ounce of pearl white pigment powder and one ounce of white glow powder to the resin. After I mixed the pigment powder and glow powder, I carefully filled the wood cavities with a popsicle stick while preventing the resin from dripping into the resin river glow table.
Step 10: Remove Resin Mold
I allowed the live edge resin river glow table to cure for 48 hours before I removed the silicone mold.
Step 11: Roundover Edges
I rounded over the edges with a 1/4" roundover bit and
Step 12: Sand Table
I sanded the bottom of the table from 80 grit to 220 grit to remove the caulk and other high spots. I sanded the top of the table to 320 grit. I have a specific technique for sanding resin. Be sure to check that out if you need sanding tips.
Step 13: Install LED Lights
I installed black UV LED lights on the underside of the table. This was not necessary, but I like to do this in order to charge the glow powder if the table is placed where natural light is not available.
Step 14: Apply Finish
I recently refinished this table with Odie's Oil and it was much better than the finish I originally used. I encourage you to visit my article explaining the best finishes for epoxy river tables if you need further information.
Step 15: Glow in the Dark Table
I glanced at the epoxy ocean table and realized it was glowing brightly after taking the final pictures in the natural sunlight.
Obviously, natural light charges glow powder the best. The glow is more consistent and uniform.
Step 16: Conclusion
I hope this instructable provided you with value. Please feel free to leave a comment if you have any questions - I'm happy to help.
Be sure to checkout my YouTube channel and my website for more DIY tutorials.
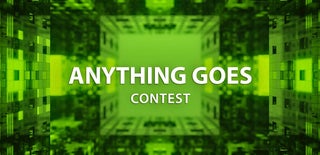
Participated in the
Anything Goes Contest