Introduction: Dave - the Remote Control Duck
Take a simple toy RC Boat, and a 'decoy' duck - and with only a few basic tools, you too, can make Dave, the highly manoeuvrable RC Duck, in a weekend!
I've been exploring making atypical RC toys for my son. I've worked in the design industry for some years including some deep-dive exploration of play, and I'm not a huge fan of the default aggressive tones around some RC toys, which promises either destruction (monster trust always need to *crush* something), and/or employ pseudo military urgency (*Delta Force* or *Laser* whatever) to be attention grabbing. It just all seems to be taking itself way too seriously!
As an 80's kid, I was raised on Hanna Barbera cartoons in the UK, and aside from the budget animation style, there was certainly a lot of whimsy, and 'just because' weirdness. Later this evolved into enjoying Eddie Izzard's surreal stand-ups, and Gary Larson's cartoons, and the weirdness certainly went up to 11 - as well as a love for trying to unnecessarily anthropomorphize animals.
So, pre-amble over - this is a great weekend project, which does not require any electronics skills, or a fancy workshop, and I hope sows the seed of possibility that when you or your kid if bored of the aesthetic or function of a RC toy, that you can simply dismantle it, and remix it into something new.
The irony is that commercial toys need to work well. Yet when you make something DIY (Kitbashing or Frankensteining as it is sometimes called by model makers), the imperfections can mean you end up having more fun - partly because of the process of learning, but also because most of the failure go wrong in hilarious ways! When I demoed the (now award-winning) Bo Peep Skunk Mobile with a friend who was an RC enthusiast, he really enjoyed the erratic driving experience and needed to compensate for the very real possibility the skunk would topple over on some of the BMX track's more perilous slopes - there was a lot more suspense and technique in contrast to his professional Tamya car, which naturally coped fine in all conditions. We discussed that there was something joyfully regressive about a more unconventional RC experience.... not to mention the curiosity and giggles of onlookers. Oh yeah, we did let our kids have a go too!!
Hope you enjoy making Dave the Duck!
Please do be kind to wildlife. You'll see in the video, I selected locations where there were paddle-boats and a lot of human activity already. Check with the necessary people/website before you set sail.
Supplies
Essentials Gear:
RC Boat: https://amzn.to/3eajAa9 (was £17.50)
Decoy Duck: https://amzn.to/3uaHQyh (was 7.49)
Sugru x2 5g packs https://amzn.to/3eRWCUy (~£2 each)
[You can use Bathroom Mastic / Silicone, or Hot Melt if you prefer, but may not last as long]
Safety Gloves: https://amzn.to/2RpscBc (highly recommended if new to working with scalpels).
Recommended Tools:
Scalpel, Cutting Mat, Sandpaper,
GlueGun https://amzn.to/3uaIwDP
Micro Blowtorch (or lighter) https://amzn.to/3nEMCSl
Zona Saw https://amzn.to/3vC56G6
Nice to Have:
Elastic, String, Zip-ties, Saw Blade,
Optional: Micro Camera: https://amzn.to/2QKhvIY
Step 1: Right Sizing
Assuming you can buy the boat and the duck I suggested via Amazon - great! However, if you can't, here's how I considered the 'fit' of these two components...
The duck should be 'life sized', and frankly there is no reason for suppliers to really deviate much on this, so most decoy ducks are about 37cm/~1.2ft long. This means the base is about 24cm long on the 'base' - so note that you need to think about the 'body', not the beak-to-tail size.
The boat I got is 23 cm long, and 7.5cm wide. This is a very fortunate fit, as you can see!
Step 2: Dave & Davina
Just in case you worry Dave may get lonely, or perhaps you prefer the less showy, understated muted browns of Davina, I realised after some searching that you can get female ducks also - In hindsight this 2-4-1 offer is a good one and almost the same price as getting only one: https://amzn.to/3ow3lI8.
Also, without wishing to lower the tone, I also was initially slightly concerned Davina might get too much 'attention' from some of the Male ducks, and get, err, sunk...but having sailed Dave, I'm pleased to say that although no ducks seemed particularly perturbed, they were also not overtly amorous either.
Step 3: Remove Ballast
Most Decoy Ducks are designed to stay upright, and so they have a sand-filled section in the base.
I used a Razor Saw to remove this, but after cutting it, it was actually so thin, you could use a scalpel with a few repeated cuts. However, for the workshop geeks out there - the Zona Saw is a must: https://amzn.to/3vC56G6
This allows you to cut 'flush' the the base of the duck with no effort.
Step 4: Disassemble the Boat
You will need a 'Philips' or '+' screwdriver - with a long neck to reach the screws.
Once opened, my only advice would be to treat the terminals with care, as this boat contains a Lithium Polymer Battery, and these are actually deceptively dangerous if you short them out with a metal connection (less 'instant' with water - but still take care!). So although we are not technically modifying any of the boat's electronics, we are still modifying it from its original purpose, so please have an adult present if you are a kid reading / making this.
Step 5: Checking Fit // Cutting Out Base
With the bottom half of the boat, place this against the duck base.
Ensure that the edges fall within the curve of the duck (ie not on the radius).
Mark with a pen/pencil/scribe, the outline - DO NOT CUT THIS!
Then draw by freehand a 5-6mm (1/4") inner line (DOTTED). This 'excess' is to act a a 'lip' to fit the two halves of the boat together - like a 'sandwich'. You can use a scalpel, but arguably a rotary tool would also work well. Whatever you feel most comfortable with - take care of yourself, and cut slowly, as the plastic has variable thickness, so can be tricky to cut.
(You might have noticed a 'rectangle' cut out already - this was me just playing around with ideas, so just ignore it).
Step 6: Test-Fitting
Insert the top of the boat as show to check that this fits nicely, and also that the screw-bosses can be reached easily - you will note, I have trimmed a little extra around these areas to make sure there is plenty of room.
Step 7: Bum Modification
Your Duck may need a bit of 'Nip 'n' Tuck', to ensure that the propellors rotate freely. (If you really want to avoid doing this, you can simply push the boat hull/base further towards the back of the duck, but this has it's own complications as you'll need more filler/Sugru/sealant to bridge the gap.
Anyway, this is a good trick to know how to modify plastic in a 'speed prototyping' fashion.
Note - the 'rudder' is actually a 'trim tab', and is for adjusting the direction of the travel, if the duck boat has a bias to one side.
Step 8: Reshaping the Duck's Rear End
I tested this process on a scrap of the plastic first, to check that the heat-gun / blowtorch will work well enough. Frankly, you can use a lighter, candle fame, or even a hairdryer to soften the plastic, but the focussed heat of a mini blowtorch is worth it if you have one.
The trick is to start about 10cm away, and move closer until it starts to soften. Be sure to ALWAYS keep the torch moving rapidly, and not holding in one place longer than 1/4 second. It really can roast it in no time.
Once you have it starting to soften nicely, I used the end of my scalpel to depress the section. I was aware that the metal would cool the hot plastic quickly, and if this is too fast, try using a lollypop stick instead to give you more work time.
HOLES - check for them. You'll see one where the plastic came apart slightly. Use Hot Melt to seal it up.
Step 9: Optional Pro Tips 1: Non-Invasive Assembly
So, you don't need to do this step, if you skip to Step 12, and slice off the top to allow easier access - and you can screw the two parts together much easier...
But the reason for including this, is that it's a good trick I picked up, from my days in the workshop in engineering companies. Being able to 'assemble blind' is strangely a handy work-around.
To do this, align the screw bosses, when upside-down, and then using a magnetic screwdriver, insert the screws from below. This has the benefit of not having to fully open a thing (in this case cut into the Duck) if you don't need to. In the end I had to create more access, so this step was redundant, but I try to do as little modification to things when prototyping until I'm certain I want to 'make the cut'. Hope this was useful.
Step 10: Optional Pro Tips 2: Kit-Bash Prototype Testing
So, as mentioned, I'd managed to assemble the two halves of the boat, to 'clamp' to the Duck shell. I knew it'd be imperfect, but would check it 'swam' properly. I was not so worried about the flooding (I knew from the innards that it'd cope, and the instructions actually alluded to the fact some water will leak into the boat, even if used as intended).
I included this, again, as I think it nicely illustrates a professional prototyping method: 'KitBashing', or as I recently heard 'Frankenstein Modelling'. These are really the 'dirty secret' of a lot of really amazing prototypers and model makers out there...they don't always 3D model, then 3D print a perfect thing - or even source original components. If they possibly can, they take apart something that is pretty close to the desired end-result or function, and gut it for parts [kit], and put it together with glue, tape, blutack in a hasty fashion [bash].
If you take this example, I've been able to make a working RC Duck in less than 2 hours. Now, I respect I've had some years experience, but the point is, even if you took 4 hours, it's way faster than trying to make it from scratch - and considerably cheaper.
I think this is an under-discussed technique, and as one recent question from a young designer pointed out - there are not many books or guides on this, as it's a bit of a 'freestyle' thing. https://en.wikipedia.org/wiki/Kitbashin
That said, now that you have this term to google, you may find some great examples - and if so, please do share in comments here, or message me on Twitter @Jude_Pullen - thanks!
Step 11: Optional Pro Tips 3: Lucky First Time?
So - I got it 'right first time', huzzah! Lucky...
But the fact is, this is not how you should work if possible, when prototyping. I didn't expect the ride height, angle, and alignment would all just work perfectly first time. So I didn't glue anything as mentioned in this 'Optional' series of 3 steps.
Has the position been out and the Duck failed to sail, I'd have been glad that Id' not welded it in place permanently! So, I still recommend this mindset, and doing the same. The time you save 'hoping' it'll work first time, is easily wasted on the occasions (9/10) that it does not!
Anyway - back to the build. Now you know how to do it...
Step 12: Pop the Bonnet
Like all racy machines, you need to 'pop the bonnet' once in a while, and Dave in no different. The trick here was to try and make the cut as well hidden as possible: To do this, I didn't cut a straight line, but rather tried to work along the existing contours and lines of the 'feathers', and shape of the model duck. (Do also look at the last picture, and see how in later steps I created a elastic loop, so keep the 'tail feather' as shown). With this method, it not only gives it a 'resting position' and stops it flapping about as much, as it 'keys' it in place, but also it hides the cut better.
To do this, use a fine scalpel and using your pinky to support you, carefully cut along the sides as shown. Try to let the scalpel cut, on the 'pressing in', not 'pushing along' motion, as you're less likely to slip and cut your hand. It also sounds easy, but I try to position my other hand (and rest of my body) in such a way that I *assume* if I slipped, it'd go into air, and not my hand, leg or gut. Sounds like I'm being over-cautious, but having worked in a butchers as a kid, and ran a workshop, I can tell you the butchers were safer than the designers, as they were trained to cut away whenever possible (or get chain mail if not). Start good habits early, and you'll spare yourself some nasty cuts.
The other thing to be aware of when cutting something like this, is that unlike cutting a nice homogeneous sheet of plastic, this duck is cheaply made, and has variable thickness, and quality of plastic - so you might be pressing hard on a 1.5mm thick part, and then it goes thin to a 0.8mm thick part - and this is when the same pressure with the knife becomes dangerous - as you will slip and slice out of the plastic - and into whatever is nearby, if not careful. So really, please take this method to heart, scalpers will go through tendons in your finger in one swipe. If in doubt, wear a glove like this / as someone else who is more experienced: https://amzn.to/3tTP60S (NOTE - they are slice resistant (parallel to glove surface) - not stab resistant (perpendicular to the glove)!).
Step 13: Optional: Flush Fitting
The two halves of the boat fit together with a little 'lip' around the edge. This is is not needed when the two parts are 'sandwiching' together the inner plastic of the duck, so it makes sense to file them down - as this also gives you more room for the screws to go together, and make a stronger assembly. It'll work fine without it, I noticed, but a good skill to know.
If you have not looked closely at a file, you'll notice one of the thin sides is abrasive, and the other is not. It's best to keep the smooth side facing the inside of the boat, as this way you will not accidentally file-off any of the screw bosses, or catch any wires from the electronics, etc.
The file used is a Bastard File: https://amzn.to/33R01hi
Step 14: Internal Mounting: Boat Top to Duck Inner
As you will see in the next step, I used Sugru to create a waterproof seal between the boat and the duck body. However, even though glue gun is not going to work - long term - for sealing the boat and duck together, it's good enough for the purposes of assembly.
The way I found this out was by first testing glue gun on an off-cut of the plastics, and found they stuck reasonably well, but they did pull apart with some force. But for the purposes of creating a bit of rigidity in the assembly, hot melt works fine, and is significantly cheaper than using Sugru.
A key thing to bear in mind is to let the hot melt get really hot, then to apply quickly and assemble quickly also! (Take care not to burn yourself, and wear latex gloves if you like). Then to press down firmly as shown in Pic 5. This will have the benefit of making the duck's plastic (which is usually a bit warped) more flat, and better to bond with the lower half (hull) of the boat.
Tip: For better adhesion - 'key' by roughing-up with some sandpaper, as shown. Be sure to wipe the dust away.
Step 15: Sugru - Wonderstuff for Makers.
So full disclosure; I worked for Sugru, as Head of R&D, so I do love the stuff, but I can say that this project will probably work with silicone mastic / sealant. If you have some kicking around, and are very skilled/accurate, I'd say - have at it, as it's cheaper. You'll need 2x 5g packs.
But, if you don't have a half-open tube on the go, and/or want to make a more accurate job of things, then Sugru really does have the benefit of being more 'mouldable' than liquid caulk/silicone, and is not as sticky, and can be smoothed out nicely.
I really don't think this is a shameless plug, as it really will make it easier for you, but you have both options (or at a push, you can use Glue Gun and just accept it will leak and need repair).
The choice, as they say, is yours!
Step 16: Prepare to Unite!
An often forgotten tip - is to apply Sugru to the duck-side, by pressing/smearing it in. This not only removes any dirt, but it also works it into the surface (keyed by the sandpaper earlier), and helps adhesion.
Once you have the two halves ready to assemble, press them lightly together, taking note of the alignment of the screw bosses on all sides.
Step 17: Tighten Up Time
This is a very satisfying part of the build - as the Sugru gradually splurges out, when you screw the two halves of the boar together!
The Pro Tip here is to not screw one corner all the way in, but rather tighten each one up a little at a time, spiralling out. This is an engineering thing, and you'll see mechanics do things in this way on engines mounts. So perhaps a little overkill for a Duck Boat, but at least you'll know you did it right.
Step 18: Keep It Smooth
The great news is that Sugru is 'Family Safe', so you don't need to use gloves at all, from a Health & Safety perspective. However, I must admit that if you have gloves, you can get a nicer (imho) finish.
Also, as much as Sugru recommends using soapy water to get an even smoother finish, between you and me, spit works even better. Gross perhaps, but it just works better imho. Your call ;o)
I suggest leaving in a warm room for 24 hours to allow the Sugru to fully cure. Though mine was firm/cured overnight, this may vary from place to place. The rule of thumb is Sugru cures at around 3-4mm thickness, every 24hrs.
Step 19: Replace Hatch
The RC Boat I purchased had a removable hatch, add it back in now.
You'll note the region I cut was large enough to make it easy to access, so keep this in mind if reading ahead of making it!
Step 20: Bonnet Hinge
I think there are many ways to do this, in hindsight: One could pop rivet and add a metal hinge. You could add a flange, and magnetise the two halves together....but honestly, this seems the right level of finish for the job.
Drill 2 or 4 holes near the neck, and also in the corresponding place for the 'bonnet' flap. Using either zip-ties, or some elastic, or string, you can create a hinge as shown.
Likewise, drill holes near the tail as shown, and create a loop with elastic, or a rubber band, or cable tie, such that it can be secured as shown.
Step 21: Hello Dave!
Dave is now ready to ride the waves!
Step 22: Optional: Rescue Loop
If you need your duck to be lifted out from a place which is hard to access, or perhaps it stalls in the middle of a pond, it'll help to have a Rescue Loop.
I first worked out the mid-point by balancing Dave on a screwdriver as shown. Then drilling holes either side, and threading a zip-tie through.
Step 23: Optional: Rescue Hook
Following on from the loop - here is the corresponding stick, made simply from a hook, screwed into a bamboo gardening cane. I added some insulation tape to avoid splinters.
Step 24: Ready, Set...
Dave looking ready for action...easily lowered down from a bridge over a pond near us.
Step 25: Dave of the Waves!
Please do sail/use your Duck responsibly. I later took Dave to a small lake/pond which had organised Boating / Water Sports. This is arguably the best place, as the water-foul are already used to weird man-made things, and such floating by, so I find it unlikely we have traumatised any wildlife as a consequence, but as with any toy, drive with care and respect for wildlife.
Do it for Dave, and David Attenborough.
Thanks,
Jude
PS - Please see more at www.judepullen.com
PPS - Please share with anyone who may also like this!
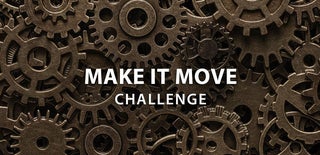
Runner Up in the
Make it Move Challenge