Introduction: Easy Childrens Easel
With Christmas literally just around the corner it's time for me to get into the shop and build the kids something. I like to try and build them something every year if I can and this year I've decided to make them an easel for painting and drawing.
I built this project using timber that I had left over from a much larger project I completed earlier in the year but as it's a fairly light weight frame if you need to buy the timber it's only going to require 3 small planks. The hardware required for this project should be easy to get hold of from any home improvement store and all the construction could easily be completed with hand tools if needed.
This project along with loads of others is available at Wobblycogs Workshop.
Tools and Equipment
- Hand plane or thicknesser
- Circular saw or table saw
- Mitre saw or mitre box
- Screwdriver
- Rasp (optional)
- Sandpaper or random orbital sander
Materials
- Two boards 1500x130x20
- Two boards 600x130x20
- One board 750x130x20
- 1m Chain
- 2 Door hinges
- Finish, wax or oil works well
Step 1: Design
I started off by making a ten to one scale drawing. This was so that I could gauge the size of the finished item and get an idea of what sort of angle would work best. I initially thought 10 degrees from the vertical but a quick look online told me 20 degrees is more normal for easels.
I normally get carried away at the design stage and break out SketchUp or even SolidWorks but I decided this time I should just wing it a bit and enjoy the creative process. I'm glad I did and I think I’ll try and do it more in future.
Step 2: Ripping the Stock to Size
Here you can see the two boards that I’ll make the legs of the easel from. The boards are about 130mm wide so if I rip them in two I’ll have legs of about 60mm which is what I want.
As I don’t have a table saw or even a decent track saw and my planner thicknesser is out of commission I'm in a fair bit of work. I start by setting up my home made track saw and ripping the board to width. This process is slightly complicated by the fact my track is only about 1200mm long but the boards are 1500mm. Off camera I've marked the centre line of both boards.
Once I've cut to the full length of my track I move the track forward to finish the cut. Aligning the second cut accurately with the first is time consuming and care has to be taken to make sure the blade doesn't bind on start up.
Next I ripped the cross pieces to size. This is the same process as for the leg boards only it’s much quicker because I can cut them in a single pass.
Step 3: Preparing the Stock
If my planner thicknesser was working this next step would take all of five minutes but as stands I probably spent the better part of two hours bringing all the pieces down to a uniform thickness with the hand plane.
I started off with the plane set to take quite thin cuts but quickly advanced the blade to take cuts that were perhaps getting on for half a millimetre in thickness. I found this wood, Meranti, responded well to heavy cuts but very poorly to light cuts.
My bench isn't very flat so if I want to hand thickness some wood I first lay down a piece of oak flooring I've had kicking around the shop for years. I've checked this board against my straight edge and it’s good enough for this work and fairly stiff.
I then clamp a stop block on to the end of the board and butt the pieces I'm working on against the stop. A clamp on the far end of the pieces holds everything in place and I'm ready to get a sweat on with the plane.
Meranti naturally has a bit of interlocked grain and doesn't always plane terribly well so to get a better surface finish I hit it with the belt sander for a few seconds. I used a very old 80 grit belt here.
I then repeated the whole process for the leg pieces. The legs are harder to get perfectly flat and true due to the length so I marked the sides I’d prepared with a cross. The end result was pretty good but I did have a slight dip in the middle, certainly nothing that would be noticeable though. When I come to assemble the easel I’ll turn the cross sides out so that the mortices are against a machined edge.
Step 4: Rough Cutting the Frame
With all the stock prepared I started to cut the pieces to length. As I didn't have a plan I just cut the pieces to a round number wasting as little material as I could. For the legs this meant 1400mm and for the cross pieces this was 600mm.
I thought that it would probably be a good idea at this stage to lay the pieces out and get a feel for how big the finished item will be. It was a tight fit on the bench which is a good sign that it’s a bit on the large side. The height looked good it was the width that seemed to be out. That’s easy to fix later though.
Step 5: Adjustment Holes
The next job is to add the adjustment holes for the legs. I want holes every ten centimetres and it’s important that they are exactly the same in every leg piece. The easiest way to ensure they are all the same is to drill them all at the same time.
To make the pieces easier to handle I used masking tape to gang them up as one piece. I find masking tape to be invaluable when doing woodwork. It’s surprisingly strong and leaves no residue when removed.
Measure the width of the leg and then mark a centre line. Measure down sixty millimetres from one end and then mark every one hundred millimetres for adjustment holes.
At the drill press I drilled 10mm holes every 100mm at the marks. Off camera I have supported the far end of the stack so that it sits flat on the drill press table. Unfortunately the plunge on the drill press isn't quite enough to go all the way through the stack of timber. The bottom piece in the stack will only get drilled about half way through. This is actually not a bad thing as it means I don’t have to worry about breakout at this stage.
Using a knife I cut the pieces free and then laid them out on the bench. I then used a countersink to remove any sharp corners from the holes which will prevent chip out when the bolts for the support tray are pushed through.
Step 6: Adjusting the Size
As I wasn't sure about the width of the easel I decided to do another layout and check it against the whiteboard I’ll be using on it. As you can see it would work in landscape but the easel is far too wide to support the whiteboard in portrait.
The solution was as simple as cutting 120mm off the cross pieces.
Step 7: Construction
With the easel now the right size I laid out for the final construction. I’ll be using dominoes to join the pieces together in this build. I quite enjoy cutting traditional joints by hand but when you need to get a project finished there is really no substitute for the domino.
The top cross piece is mounted flush with the top of the legs the lower one is 800mm down. I checked the squareness of the piece while it was in the clamps and found it to be a couple of millimetres out. For a piece of this size before glue up that’s excellent and corresponds to an error of about 0.2 degrees.
I started by cutting domino mortises in the cross pieces and than in the legs. I'm using 8 by 40 dominoes here which should be amply strong. My timber is a little under 20mm thick but I have the depth fence set to 20mm anyway. As long as you are careful about always working from the same face it’s not a problem that the domino is a little off centre.
With a glue up this small I’d normally do it all in one go but I had a few other things to do so I first glued the dominoes into the cross pieces and let them set. As long as the piece you are working on is fairly square this can actually make the final glue up simpler as there’s less play while you are putting it together.
The next day I glued the cross pieces into the legs and again checked the piece for square. The error now was less than 1mm corner to corner which is good enough for me. When the piece was dry I took it out the clamps and sanded all faces. The timber has some planner marks where there much have been a chip in the blade so I sanded with first with 80 and then 180 grit paper.
Step 8: Fitting Hardware
The two sides of the easel are now essentially complete so it’s time to add the hinges and the mechanism that will decide the angle it’ll stand at. For the hinges I've used a couple of door hinges I had in the cupboard. They are perhaps a little large for this project but on the plus side there’s no danger they will ever fail. Unfortunately I didn't have any stainless screws to match the hinges so I had to use brass. Next time I'm near the shops I’ll get some appropriate screws and swap them out.
If the piece is going to fold up nicely it’s important that the two sides are perfectly aligned when the hinges are fitted and that the hinges are aligned to the top edge. This is quite easy to achieve by clamping the legs to a straight edged piece of timber and just aligning the corners of the hinge with the top rail.
Many of the child’s easels that I looked at had a tray to hold the sides open. This is a great idea as it gives them somewhere to store paints and pencils. Time was not on my side though and I probably didn’t have enough timber to make a tray so I instead opted for a chain. I quite like this idea though as it makes it very easy to change the angle of the easel. As with all of the other pieces for this project I’d had the chain in cupboard for ages.
Step 9: Fixing the Feet
I realized at this point that the easel would be standing on carpet most of the time and the sharp corners on the bottom of the legs may damage it. The solution is to round over the corners, the obvious way to do this is with router but it’s currently buried under a ton of other tools which I'm too lazy to move. Fortunately the rasp is hanging up on the wall so that’s easy to get to.
I marked down 5mm on the face and base, rasped a little bit and then sanded the curve smooth. It’s not the perfection that the router would give but no one will ever notice.
Step 10: Finishing the Easel
I've still got the tray to build but I wanted to get the main part of the easel out of the way so I decided to apply the finish now. I had a rummage around in the finishing cupboard to see what I had. I’d normally use something like Osmo Polyx on this but I've only got a little left and it’s nearly dried out anyway. I found an old can of beeswax that I've not used in years, to my surprise it looked fine when I opened it – or at least no worse than it did last time I used it. Beeswax doesn't provide a terribly durable finish but it’s easy to reapply and smells quite nice.
Step 11: Making the Support Tray
To make the tray I first laid a piece of stock under one side of the frame and centred it up by measuring each side. Using a transfer punch I transferred the holes through onto the tray piece. I could probably have measured the separation but this method is more accurate. Mark lines from the edge to the punch marks and then measure up about 15mm from the edge for the fixing holes. Drill 8mm holes at the marked locations and then countersink the holes.
I want the bolts to be captive in the tray piece and there’s a number of ways you can achieve this. One method is to counterbore the bolt hole for the bolt head and then fill it with epoxy. Another method is to drill a counterbore somewhat smaller than the head of the bolt and then pull the head in with a nut. The method I'm going to use here is quite uncommon but incredibly quick and easy – I'm going to cut threads in the wood.
As I'm tapping into wood there’s no need for the care that you usually take when tapping metal. Just stick the tap in a drill and power tap in one pass. With very hard wood a little care should be taken but with something soft like this you can go as fast as you like.
Since the fibres are crushed as well as cut the end result is a surprisingly usable thread. In a soft wood like this you can’t expect it to last if you are screwing bolts in and out every five minutes but it’s good enough for a dozen goes which is about eleven more than I need.
Sand the two tray pieces and then glue the edge of the top piece to the face of the piece with bolt holes. I came up with a number of different designs for the tray but this simple two part tray was the overall best it seemed. I considered using dominoes on the joint but it really isn't necessary when gluing long grain to long grain.
The square outer edge of the tray looked a bit sharp and is likely to be leant against quite a bit so I gave it a strong round over. I first planed it at 45 degrees and then rounded it over by hand with sand paper. I then gave the tray two good coatings of beeswax with buffing between before insert the mounting bolts for the final time.
Step 12: Final Test
All that’s left now is to test out how everything fits together and relish the warm feeling of having built something for the kids. It was a bit of a rush to get this project ready for Christmas but I'm glad I did it.
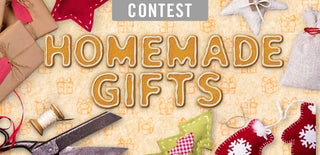
Participated in the
Homemade Gifts Contest 2015