Introduction: Edison Desk Lamp
Vintage style Edison bulbs, named after their creator Thomas Edison, are a great way of creating soft lightning in your home and are instantly recognisable thanks to their iconic shape and thin filaments. I have now made several of these lamps to give as gifts have also been using them in my own home for a couple of years.
In this Instructables I will give an overview of the process to make these lamps with a look at some 3D Design, CNC machining, and electrical assembly. While this Instructables will give general steps to build these lamps it does assume a reasonable amount of prior knowledge in the use of the tools described (especially the CNC router!) and electrical wiring of a plug / light fitting.
This Instructables involves working with power tools and mains electricity and so safe working practise is essential. As always this Instructables is a documentation of what I have done and as so is provided without any assurance it is correct or free from errors. You follow this documentation at your own risk.
Supplies
The bill of materials (BOM) for this project is relativly short and simple. I picked up most of the parts from amazon and the glass dome from my local IKEA. The dome came with a base which we will alter to fit the bulb saving a lot of work. I have included links here to the parts I have used (or similar) but suggest you do your own research as you may be able to find them cheaper / easier in your country. You will need:
- Edison Bulb - Amazon
- Vintage Style E26 Fitting - Amazon
- Braided 3 Core Cable - Amazon
- 3 Pin Plug - Amazon
- Dimmer Plug - Amazon
- Glass Dome - IKEA
- Inline switch - Amazon (Optional - I chose to use smart switches with my lamps so omitted the inline switch)
- 8 mm Earthing Ferrule - Ebay
- Rubber feet - Ebay
The total cost of parts for one lamp cost me around £25 but if buying multiples it works out a bit cheaper.
The equipment required will depend heavily on how you want to machine the base of the lamp but you will certainly require:
- Lathe / CNC Mill / 40 mm Hole Saw (I chose to use a CNC as I had one to hand and it's the quickest option)
- Screwdriver Set
- Epoxy or Hot Glue
- Stapler (A wall stapler is ideal as you will be stapling into wood)
- Crimp Tool for Ferrules
Step 1: 3D Design
Once we have all of the parts we need to begin by making a CAD model of the lamp base from which we can generate a technical drawing (to work from on the lathe) or start creating cutting paths for a CNC mill. I used SOLIDWORKS to create my solid model but the process will be mostly the same in any parametric CAD package (such as Fusion 360) so you should be able to follow along no matter which program you choose.
I started by creating a basic model of the wooden base that comes with the lamp which is easily achievable with a revolve feature driven by some basic measurements with a ruler or digital callipers. A 40 mm hole is then put through the base to hold the lamp fitting. An extrusion is used to reduce the height of the top surface by 10 mm. This moves the fitting down inside the dome placing it such that the bulb sits concentrically with the top of the dome and doesn't touch. Finally a channel is routed into the bottom side for the cable.
You may want to go ahead and model up the rest of the lamp - including the bulb, fitting and dome so that you can test the fit and design before you go ahead and start cutting material! I always like to have a complete CAD model before making a cut so that materials aren’t wasted. It also gives me the opportunity to create some glossy renders to check that it will look aesthetically how I want and to get some opinions.
Step 2: Generating Cutting Tool Paths
How you machine the base of the lamp depends on what tools are available to you. I chose to use a CNC but a lathe would also work. Alternatively you can reduce the height of the base using a planer and drill the hole using a hole saw. In this step I will talk through the tool paths used to cut the base using a CNC router.
I imported the model into Fusion 360 to create the tool-paths. An initial setup was used with the part facing upwards. 3D adaptive clearing was used to reduce the height of the base and to cut the central hole. The adaptive clearing tool path is excellent for rapid material removal and works by maintaining a constant chip load on the tool maintaining material removal rate and reduces tool chatter to give a good surface finish. A circular machining path was used to to finish the top surface leaving a concentric pattern. A second setup was created to mill the channel into the part using a 2D pocket. Some light sanding removed any tooling marks.
You could optionally seal the base at this stage with an oil, wax or varnish to help protect the wood from damp or light scratching.
Step 3: Machining the Base
Two programs (one for each setup) were generated using the Fusion 360 post processor for the machine I used.
I put two bolts into the base board of the machine to use as a datum point for the base. By pushing the circular base into these two bolts I am able to quickly locate the base in the machine allowing you to run several bases back to back with minimal setup time. The two screws also provide a datum for the second setup so the second setup is aligned with the first.
The base was fixed to the base of the machine using 3D printed step clamps onto the edge of the part that isn’t being machined. The printed step clamps are great when working with softer materials as they are a bit more forgiving to crashes than steel clamps. In this case I ended up milling through the top of the clamps to get the tool to cover the entire top surface. For the second setup the base is secured in place using a single step clamp through the central hole.
With the part located and fixed to the machine we need to create a G54 offset to set the starting point for the cutting program. The Z height can be found using a piece of paper as a feeler gauge. XY location was done by eye to a centre point drawn on the base.
All thats left to do now is to press cycle start. (and put on our safety glasses!)
Step 4: Electrical Assembly
NOTE: Working with mains electricity is dangerous. Take care and never work with objects plugged into the mains. Always check for shorts with a multimeter before pugging in and if possible have a PAT test completed. This Instructable is a documentation of what I have done and does not make any suggestion that this is safe or correct. You follow this documentation at your own risk.
Take your three stranded mains cable and separate the end 5 cm into individual strand. Remove the fabric wrapping from the unwound section and use some electrical tape to prevent any further unwrapping if you want. Strip the insulation form the ends of your three wires and crimp the 8mm ferrule onto the end of your earth cable (Green and yellow).
Disassemble the light fitting by unscrewing the central ceramic part. Pass the cable through the threaded tube and crimp the brown and blue wires into their terminals on the ceramic piece. The brown cable is the live cable and should be connected to the terminal that connects to the central contact. You can check which terminal is connected to which contact using a multimeter.
With both terminals screwed down tight onto the cable check for any shorts with a multimeter. Loop the 8mm ferrule over the threaded tube and fix down with the nut to provide a ground connection. Slide the the brass housing on and screw into place.
Pass the cable through the hole in the wooden base. The cable will not fit through once you have attached the plug onto the end! (trust me!) Also make sure it is the correct way around!
How you wire your plug will depend on your countries plug! Have a look for an Instructable for your countries plug.
Step 5: Final Assembly
Assembly of the lamp is very simple and only requires one glued joint between the base and the lamp fitting. This joint can be made with either hot glue or epoxy but epoxy is the better option here as it will give a much stronger joint.
I strongly suggest wearing a set of nitrile gloves whenever working with epoxy and you should follow the safety instructions on the packet of your epoxy.
Start by mixing your two part epoxy on a disposable surface and leave to rest as per the instructions for your specific epoxy. You want to bond the base to the fitting with a continuous line. I found it helpful to rest the fitting upside-down and place the base centrally on top. When gluing the base work quickly and cleanly and avoid dripping the epoxy where you don’t want it. Leave the epoxy for 24 hours to fully set before moving on.
With the epoxy set, put the cable into the channel on the base of the lamp and secure with a couple of staples. Avoid stapling the cable - check with a multimeter if you are unsure.
Cut a 110 mm diameter circle from the sticky backed felt and stick down to the base. This should cover all of the base so that the staples, central bore with glue joint and cable channel is covered. Alternatively you can use 3 stick on feet to give you a level surface.
Fit your bulb of choice and place the glass dome on top. I chose to use a traditional style Edison bulb but for LED variants are also available for a more energy efficient option. Plug the lamp into the dimmer switch. I find that about 25% on my dimmer switch is about right.
Before powering on the lamp I highly recommend testing for any shorts again. Use your multimeter to check that the outer casing is connected to the ground, that your live and neutral pins are not shorted and are connected to the correct pin. Double check that your plug wiring is correct.
Step 6: Finish
Thanks for following along with this Instructable! I hope you found it informative and it has inspired you to make something. I think the Edison bulbs are a great way of creating a simple and understated lamp and using the bases from Ikea makes this project a lot quicker!
I chose to use my lamps with a smart socket that allows me to turn them on and off through automations and voice assistants. If you wish to use your lamps with a smart switch as part of a home automation remember to put the smart switch into the socket before the dimmer switch or you will get unpredictable results.
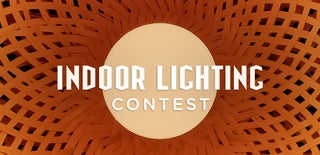
Participated in the
Indoor Lighting Contest