Introduction: DIY Extreme Airsoft Gun
Make your own Airsoft gun with just a few off the shelf parts.
Over the last few years I have been playing around with launchers made from PVC and sprinkler valves. I first came across the idea from Make Magazine where they used a sprinkler valve to launch paper rockets. As soon as I could I made one of these and had a blast with it. I wondered though if it could be made more portable? After a little experimenting I worked out a way to add a hand-pump and from this came the Handheld Compressed Air Launcher.
I recently decided to revisit this idea and made a more powerful one which needed an external pump. From this, the Compressed Air Acorn Gun was born. Still I wasn't happy. I didn't want to wait around for Autumn before I could go shoot things!
I decided that I needed something that was more portable and able to shoot readily available bullets. A quick search on Instructables and I found NightHawkInLight’s great Ible’ for making a portable airsoft gun. Only problem was, I couldn't find the brake tubing anywhere that he used. Also, although the triggering system is genius, I wanted a more traditional way to release my bullet.
So now I come to my latest incarnation. This would have to be the best one that I have built to date. I was totally blown away by how powerful this beast is! Just 5 pumps of the hand-pump and you’re ready to go. The air is released quickly by the electric sprinkler valve, and that little airsoft bullet is released at some seriously dangerous speeds.
So to all those out there who want to build their own – I happily present the following instructions.
DISCLAIMER – This has the potential to be a really dangerous project! I'm assuming you’re all responsible, intelligent people who know how to put things together. Make sure you use the right materials, glues etc as you are dealing with some serious pressure.
Step 1: Things to Gather
Parts:
PVC Piping (pressure piping):
1. 1 x 25mm “T” section
2. 1 x 25mm pipe (aprox 500mm long)
3. 1 x 25mm Cap
4. 1 x 25mm coupling
5. 1 x 25mm coupling with 20mm female thread on one end
Copper fittings
Copper or brass tubing and wire can usually be found at your local hobby shop. If not, then you will be able to order it on eBay
1. 5/16 (8mm) Hose Barb x 3/4" inch Female Thread - Aliexpress. This ended up being the wrong sized barb. I did however hack a way to use it and it worked fine. I would suggest taking the 7mm copper tubing down to your local hardware store and working out which hose barb fits best.
2. 1 x 7mm (OD) piece of tubing. Aprox 300mm length
3. 1 x 8mm piece of tubing. You'll need about 100mm
4. 1 x 9mm piece of tubing. About 100mm should do it.
5. 1 x piece of copper wire. Just 2 mm thick should do it.
Other Parts
1. Push button (Momentary) - eBay
2. 9v battery
3. Small spring (needs to fit snuggly over the 7mm copper tubing. - eBay
4. 2 x self tapping screws (if you are using the same switch as me)
5. 9v battery terminal
6. Sprinkler valve - eBay
7. Small hand pump
8. Pressure pipe glue
9. Heat-shrink
10. 500mm length of thin electrical wire (aprox)
11. Holographic sight - eBay
Tools
1. Small blow torch
2. Solder
3. Flux
4. Drill
5. Various files
6. Hammer
7. Circular saw
Step 2: "T" Section
First thing to do is to modify the “T” section in order to fit a piece of 25mm pipe through it. This makes the air chamber for your gun.
Steps:
1. Grab a round file and start to file the insides. You will need to remove a fair bit of the plastic to enable the piece of pipe to fit through. If you have a dremmel you can use this as well (mine fell apart recently so I have to go manual)
2. Once you have made the hole large enough, push through the 25mm pipe. You’ll have to probably use a rubber mallet to cox it through.
3. Once the pipe is through both ends, you need to trim up each end so only about 30 to 40 mm is sticking out of each end. I just used a circular saw to do this.
Step 3: Adding the Coupings
Steps:
1. Glue into place the 2 X 25mm couplings onto the ends of the 25mm pipe, The front coupling should sit flush with the T section. Trim the 25mm pipe if necessary. The other coupling (the one that the pump will go into) should sit about 10mm away from the T section. This will allow a little more pressure in the air chamber.
2. Next you need to glue into place the threaded coupling to the front section of the gun.
3. Add some more 25mm pipe to the bottom of the T section. This will be your handle. I make the handle a little longer than necessary as it balances out the finished gun. DON'T glue tis into place, you are only adding this at the moment for painting. Lastly, push on the 25mm end to the bottom of the handle.
Step 4: Adding the Pump and Painting
Steps:
1. Glue the 25mm coupling to the other end of the T section.
2. Next add some glue to the end of the pump and push into the other end of the coupling. If you find that the pump is too big for the coupling, you’ll have to open up the hole with a dremmel.
3. You have now completed the chamber section of the gun.
Painting
1. Hang-up the gun outside and paint whatever colour you want.
2. Give a few coats to ensure that the paint won't rub off.
Step 5: Adding the Sprinkler Valve.
Steps:
1. The valve that I used has a 3/4 inch end. As we only have metric sized pipes and couplings, the closest is 20mm. It will mean that you will need to add some plumbers tape to the end of the valve. It will also be a little tight but should screw on ok.
2. You need to modify the valve slightly. First remove the plastic filter inside the valve. This till just slow down the air leaving the chamber and we don't want that.
3. Next un-screw the 4 screws holding the solenoid on to the cowling. turn it 90 degrees so the wires are facing away from the front of the valve.
2. Put the valve into a vice and screw into the female coupling as below.
Step 6: Adding the Electronics
Next you need to wire-up the sprinkler valve to the battery and push switch. Initially I was going to add a safety switch and had drilled all of the holes but found that it wouldn't fit because of the battery. I left the schematic just in case anyone wants to add one.
Steps:
1. The switch I went with was from a kids bike horn. You can get these from eBay of you went to use the same switch. Otherwise just use any momentary switch. Drill the appropriate holes and attach the switch.
2. Drill another hole on the side of the T section to allow thew wires from the valve to go through.
3. Next is to solder the battery terminal, valve and switch together. This is pretty simple but if you need a reference check out the attached schematic.
4. Attach the battery and test.
Step 7: The Loading Chamber - Part 1
For my initial prototype, I used a ram rod to push the bbbullet down the barrel if it was a little tight. I wanted to avoid having to have to do this so I can up with a way to load the barrel. You don’t have to do this if you want to keep it simple. Take a look at the last step to see what I did with the prototype.
Steps:
1. First things first – you need to make a hole in the 7mm tubing. The hole needs to be big enough for a BB to fit into. To do this I used a small bit on the drill and started off drilling a small hole. I then changed to a larger one to complete it.
2. You’ll have to file out the hole and ensure that there are no burrs etc. Keep testing the hole with a BB bullet and once it can be pushed in easily and move down the barrel you’re done.
3. Next thing to do is to cut all of the other pieces of copper etc that you will need. The 2 collars and larger piece of tubing is cut from 8mm tube. The piece of copper wire needs to be bent as shown to make a “trigger”
Step 8: The Loading Chamber - Part 2
Steps:
1. Next thing to do is to solder on a collar. To decide where to add one, you’ll need to put all of the pieces onto the 7mm tube and work out how everything will fit. I wanted the latch to the barrel to open towards me so I made sure that the trigger faced away from the gun. Mark where the first collar needs to go and with a small blow torch and flux, solder into place.
2. Replace the spring, latch and other collar and then solder on the collar to the barrel. You may have to put the latch into a vice and hold it back so it doesn’t also get soldered.
3. Wipe away any flux and clean the spring. Test and make sure that the latch pulls back correctly.
4. Done
Step 9: Adding the Barrel
One of the trickiest steps for me was working out how to attach the barrel to the sprinkler valve. It took me some time to come up with the finished version due to the different sizes between the barrel and end of the valve. In my initial prototype, I did manage to get the barrel on by using a copper reducer, a bolt and a lot of solder. The main problem with this idea though was it was pretty much impossible to get the barrel straight. I had to re-solder a few times until I was happy with the end result.
The version below is quite simple but will ensure that the barrel is straight and that the solder points are strong.
Note - The 3/4 inch female with the 8mm barb I purchased wasn't the correct size. Although the barb was 8mm, that was the OD size, not the ID. It meant that I had to do a little more re-work than expected but it still works great.
Steps:
1. As the OD of the barb is pretty much the same as the barrel (7mm) you'll have to add some 9mm tube first. The 9mm is a tight fit but a few hits on the end with a hammer and it will go on ok.
2. Next you will need to cut the 9mm tube and leave about 50mm. File smooth the end of the tube.
3. Grab some 8mm tube and cut a piece so it fits into the 9mm tube and has a little sticking out the top. Add some flux and solder the 8mm to the 9mm tube.
4. Now you will be able to slip the 7mm tube that the barrel is made out of into the 8mm tube you have just soldered. Before you solder it though, climp the end of the 7mm tube slightly so the bb bullet doesn't role back into the valve.
5. Screw into the sprinkler valve and test.
Step 10: Optional - Make a Tripod and Adding a Sight
Tripod
You don't need to have a tripod for your bb gun so I’m not going to go into much detail on this. All I used was a tripod, some bits and pieces from the ratchet set (u-joint, extension pole etc) and a spare 25mm PVC cap.
Check out the video at the start of the ‘ible to see it in action.
Holographic Sight
You can pick these up on eBay for about $25.00. Definitely something you should think about adding. I secured mine with hot glue and cable ties. You want to make sure that it is secured fast as the slightest movement will put the sight out.
Step 11: Optional - Make a Case!
Recently I came across a great old wooden case and thought it would make a fantastic case for my gun. This isn’t necessary at all, but is a good way to store and carry about all those bits you need in order to shoot a few rounds off.
Steps:
1. Find or make yourself a wooden case large enough to carry everything in.
2. Decide what you need to add, and then work out where to store everything. Here is a list of things I added to mine
a. Gun barrel
b. Gun body
c. BB bullets
d. Safety glasses
e. Targets
f. Tripod
g. Speakers (so I can listen to some tunes and shoot sh*&)
3. Once you have decided how everything is going to fit, you’ll then need to work out a way to make sure that everything is stable and doesn’t move about. The best way I found was with some dense foam.
4. Mark out on the foam the sections to cut out. Use a exacto knife and cut out the foam.
Step 12: Complete!
Congratulations – you have now built your very own, high powered BB gun. Although there are quite a few steps, most are pretty easy and the end result works a treat.
What have I learnt from making this gun…
- Well firstly, plastic bb bullets hurt when they hit you – I’m mean really hurt!
- Next that the bullets are pretty useless over large distances. Not that they lose speed, but trying to hit a target with a little wind becomes nigh on impossible.
- Lastly that bb guns are a whole lot of fun.
What would I do differently next time? Usually I have a whole list of things that I would do differently. This time though there really isn’t much I would change. That’s because I made a prototype initially and gleaned a whole bunch of ideas from the initial build. If I had to point out a few flaws, then this is what I could have changed.
- The barb that the barrel went into. Ok so I purchased the wrong sized one initially but it still worked after a couple of modifications. The ideal one would have had the barrel fit snuggly into the barb.
- Pump. The pump that I used is fine but it has a plastic handle section which will probably break at some stage. The good thing is if it does, the actually body section is cheap and easy to make. The bad thing is it might break at some stage.
- The extra holes I accidently drilled. I was going to add a safety switch and LED indicator to this gun but after I wired everything up and had most parts in place, I realised that there was nowhere to comfortably add the safety switch! Usually I would locate this in the handle but the 9V battery took up the space where I wanted to add the switch.
Step 13: Optional - Pump Handle Mod
I have only recently done this mod to the pump handle as it started to become bent. The handle shafts are only plastic so it doesn't take much for them to become bent. The mod is pretty simple but works a treat.
Steps:
1. You will first need to remove the pump handle from the pump. It's not very hard to do, depending on the type of pump you have. just pull really hard on the handle and move side to side. The pump I used has 2 pieces of plastic which hold the pump handle in place. These popped off with a little pressure
2. Cut the shaft about half way down.
3. Find a piece of metal tubing (I used some copper tubing I had) that the shaft fits nice and tightly into.
4. Cut the copper to the same length of the shaft.
5. Add some epoxy glue to the handle and push the 2 halves into the shaft. Leave to dry for 24 hours.
6. You may have to enlarge the hole that the shaft goes into as you have now increased the size. I used a dremel to remove some of the material.
7. Put the handle back into the pump and push the little plastic bits back into place.
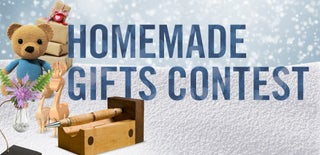
Participated in the
Homemade Gifts Contest