Introduction: Flat-Pack Wooden Chairs
These chairs are my heavy-duty version of the classic 2-piece wooden beach chair (or "camp" chair).
They are comfortable to sit in and are rock solid. The best part is that they pack away tidily with the seat section nesting into the back section for storage or transport.
I made these from 1" thick solid ash wood with cotton canvas and lightly padded seats. I'm very happy with how they turned out, and I hope you'll use my plans to make some for yourself.
Full details follow. Thanks for taking a look.
Step 1: Plan
I wanted a pair of wooden portable chairs that were especially robust and heavy duty, but was not impressed with what I could find available to buy.
So I decided to make my own, up to my own standards.
I laid out some butcher paper on a table and began working out the geometry and details full-scale using rulers and an angle gauge. I'm old school like that.
My goal was come up with a plan that used simple measurements and maximized use of material. I think it was a successful effort, and I'm quite proud of how it all turned out!
The top image is a digitized version of my finalized plan and contains almost all of the details needed to complete the wooden frames for one chair. However, I have covered the entire build process in the coming steps as well.
What tools do you need?
This project requires access to common woodworking tools. There are numerous ways to achieve the same results though, and what route you take depends on what tools and skill level you may have.
I used a table saw and band saw, as well as drills, router, sanders, and common finishing supplies. For the fabric portions, I used a sewing machine along with other common sewing supplies.
Step 2: Wood
I decided to use ash for my chairs.
Other hardwoods like oak or maple would be good choices as well. I would not recommend anything soft like pine or cedar.
The board I purchased was 1" thick and 11" wide, and was chosen because it was especially flat and straight, and wide enough to allow me to squeeze one full chair from a four-foot section of the board.
I began by cutting a section from the full board that was 48 1/2" long (a little extra to compensate for kerf loss).
I trimmed a 1/4" piece off of one edge, which will be used to make the G pieces (see plan).
Generally speaking, you'll need to start by making one edge of the board perfectly straight. You can joint one edge, or even mark a straight line right along the edge and cut it free hand with a band saw or circular saw.
This will provide the initial edge to put against your table saw fence or circular saw guide.
Step 3: Break Down Board
The 4-foot board was broken down at the table saw in the following order:
- Ripped 2 pieces that were 2" wide (will become A and C pieces)
- Ripped 2 pieces that were 1 1/2" wide (will become B, D, and E pieces)
- Trimmed remaining piece to 3" width (will become F pieces)
The 3" piece was then taken to the band saw and split in half. It was marked down the middle of one edge with a sharpie, and then carefully cut freehand with a 1/2" 3 teeth-per-inch blade.
All the pieces were then taken back to the table saw, and were cut to the lengths indicated on the plan using a crosscut sled.
Step 4: Notches and Bevels
All the notches were cut using the band saw according to the measurements of the mating cross pieces, and located as indicated on the plan.
If you have a dado cross-cut system set up on your table saw, you could cut the notches that way. Or cut and chisel by hand. Or whatever method you choose.
The C cross pieces have a slight bevel cut on the edges where the seat-legs rest. These bevels were cut with the table saw.
Step 5: Notches Continued
Note that the two C cross pieces are fit into notches, rather than simply screwed in place.
I did this on purpose to add strength to the joints and solidify the chair as a whole.
However because of this, this area requires a little more precision. In storage, the seat-legs (which are 1 1/2" wide) need to slide between these two C cross pieces, so the gap needs to be at least 1 5/8". Be certain to mark and cut the notches for the C cross pieces no deeper than 3/16" each.
Step 6: Angles and Curves
The angles at the leg bottoms were marked and cut with the band saw. See plan for measurements.
A quarter (any coin will work, as this just aesthetic) was used to mark curves at all the pointy ends of the legs. The pointy bits were cut off, and the pieces were sanded up to the marked lines.
Step 7: Route and Sand
I used a router to put a 1/8" round-over on the edges of all of the pieces.
Where pieces were to be joined, however, I did not route but left the edges square. This required a dry assembly and a few pencil marks to indicate where NOT to route, but this little bit of extra work results in cleaner-looking joints later on.
The flat sections of the pieces were all lightly sanded with 150 grit sandpaper using an orbital sander.
The routed corners were lightly sanded by hand with 220 grit sandpaper.
Step 8: Assembly Materials
I used Titebond III glue since it is water proof and better suited for projects like this that will likely be out in the rain at some point.
All joints were glued but also joined with treated deck screws that were fastened into tapered countersunk pilot holes. The deck screws may have been overkill, as they'll all be completely sealed away . . but they can't hurt.
Step 9: Glue on G Pieces
The thin G pieces are shims that allow the seat to fit correctly into the back portion for storage.
Glue these in place onto the tops of the B pieces, flush with the front edge. I used some tape to hold them in place until the glue dried.
Step 10: Assemble Seat
The seat/leg section was assembled with glue and screws that were fastened into pilot holes.
The pieces come together fairly logically if you've cut them as indicated in the plan. Put the E cross piece in place before doing the seat slats.
The seat slats (F pieces) should be fastened beginning with the back slat flush with the back ends of the G shims.
I used a pair of quarters to act as spacing shims between each pair of slats.
I clamp was used to hold the B leg pieces at precisely 15 7/8" apart, and the seat slat overhang on either side was measured to be precisely 1 inch.
Be sure to wipe up any glue squeeze-out with a wet rag before it dries.
Step 11: Plug Countersunk Holes
I used a 1/2" poplar dowel to plug all of the countersunk holes. I cut a 6-inch piece which was enough for all the holes in one chair.
Glue was applied to the end of the dowel, and the dowel was tapped in place with a mallet. Using a flexible pull saw, the protruding dowel was trimmed off and the process repeated.
Step 12: Assemble Back Portion
The back portion was assembled with screws and glue in the same manner as the seat.
The plugged holes as well as any bits of visible glue were sanded smooth at this point with 150 grit paper on an orbital sander.
Step 13: Finishing
I finished the wooden frames with several coats of brush-on spar urethane. I think oil-based provides a better result, so that's what I used.
Oil-based spar urethane is pretty thick, and works best if you brush it on in the thinnest coats possible. Follow the instructions on the can and apply several coats. If you take your time (read: this may take several days) you can build up a plasticky, durable waterproof coating that is nice and smooth. It's tedious if you do it right, but the results are worth it.
Then again, if you're lazy you can just spray it with a few coats of spray lacquer and call it good!
I normally do that with non-outdoorsy furniture, but in this case I felt it was worth the extra time and effort.
Step 14: Seat Pad
I made seat pads for my chairs, which is not necessary but is a nice touch.
They are made from heavy cotton canvas with straps to hold them in place, and on the inside I used pieces of anti-fatigue floor mats as padding.
The pads are only 1/2" thick, but the dense foam provides a decent cushion without adding a lot of bulk to the completed chairs.
The cover is basically a flat envelope with an opening on the bottom where you can slip the foam pad inside.
Step 15: Seat Pad
I began by cutting out fabric pieces for the seat pad as indicated in the image above.
A half-inch of one long side of each bottom piece was ironed over a couple of times and then sewn down (see diagram note above).
Pieces of 1" strapping were cut and prepared. For each chair pad, two straps had sliders sewn on the ends and were trimmed to be 6" long, and two more pieces were cut 12" long.
All cut ends of the webbing straps were melted briefly with a lighter to keep the ends from fraying.
Step 16: Seat Pad
The bottom pieces were positioned on the top piece, and pinned in place with the hemmed inside edges facing outward.
The short side edges were stitched down now. I actually stitched over the seam a second time to reinforce it.
Measuring in from the sewn edges, I placed a mark 2 1/2" in on both ends of both long sides. The straps will be sewn in place just inside of these marks.
Step 17: Seat Pad
Place the straps as indicated and pin the long sides together. The straps with the sliders need to be placed so the sliders will be oriented as desired when the cover is turned right-side-out.
The long sides of the cover were now stitched together. The areas over the straps were stitched over 3 times to reinforce the connection.
The cover was turned right-side-out and pressed flat.
Step 18: Seat Pad
The foam for the seat pads were cut on a cutting mat with a straight edge and a utility knife (only one piece of foam was used per chair).
The dimensions for each foam piece are 17 3/4" by 8 3/4".
Step 19: Seat Pad
A foam piece was inserted into the cover and the underside of the cover was stitched shut by hand.
The completed seat pads were then strapped onto the wooden seats.
Step 20: Seat Back
The seat back is made from a single piece of cotton canvas that was hemmed and then screwed in place to the wooden frame with stainless steel screws and stainless finishing washers.
Step 21: Seat Back
The fabric for the seat back was cut and hemmed as indicated in the diagram. See photo notes for details.
With the seat back edges hemmed, six evenly-spaced marks were made along each side hem, 1/2" in from the outer edge.
Using a hobby knife, I plunge-cut a small plus-sign (+) pair of cuts through each mark. Each cut should be no more than about 1/8".
Step 22: Seat Back
The seat back was installed to the frame 2 1/2" from the top of the frame.
I began by holding the fabric in position hanging over the edge of the frame by 1", and carefully drilling a pilot hole through one of the end marks, and then installing a screw and washer.
This was followed by drilling and installing the screw on the other end, and then the middle screws, followed by the remaining locations.
One entire side of the seat back was completed before moving to the opposite side of the chair. Keep the fabric fairly tight as you go.
Step 23: Seat Back
With the seat back installed, I took the frame outside and sprayed the fabric with water. As it dried, it shrunk and pulled tight on the frame.
I did not pre-wash the fabric for these chairs, although doing so is probably a good idea to get full shrinkage taken care of ahead of time. Next time I make these, I will do that.
Step 24: All Done!
And that's it.
Now just sit back and enjoy the sunset. Or watch your kids' Little League games all summer, as I'll be doing.
If you make some chairs using this instructable, please share a photo or two in the comments.
I would love to see how they turn out!
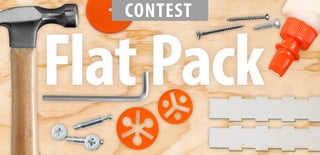
Participated in the
Flat Pack Contest