Introduction: 3D Modeled Gummy Candy Molds
Manufacturing processes aren't the most glamorous and exciting topics for most high school students, but this lesson attempts to intrigue students by having them create their own injection molding system that can produce individually designed gummy candies.
I use this lesson in my introductory high school engineering/manufacturing class (grades 9-12) after we have learned how to use CAD software to make 3D models. I introduce manufacturing methods (specifically highlighting injection modeling) within this project and have students apply their newfound CAD skills to help them better understand that process.
This project begins by having students design and model an original candy shape. Next, they they turn those models into 3D printed molds that they can use to create personal injection molding machines. Finally, they can inject those molds to create their own personalized gummy candies.
Supplies
General supplies:
- Paper
- Computer with 3D modeling software*
To create the mold:
- 3D printer and filament (for food grade projects like this, a stainless steel hot tip on your extruder and PLA made from natural fibers is best)
- Masking tape
- Cooking spray
- Drill and drill bit (drill bit size should match the outer diameter of the tubing used)**
- Plastic tubing (~6" long per mold)**
- Syringe**
**There is no strict size requirement here, but you want to make sure all three of these components (syringe, tubing, and drill bit) work together. I recommend a syringe that has at least a 20mL volume, but larger is fine. The goal is to have tubing that will attach snugly at one end to the syringe and at the other into a hole in your mold.)
To make the edible gummy candy:
- Small bowl / jar (for mixing)
- Spoon (for mixing)
- Microwave (or any other head source for boiling water)
- 1 box of flavored jello
- 1 Tbsp unflavored jello
- 1/3 cup water
- 1/2 tsp citric acid (optional; add if you want the gummy candy to be sour)
Step 1: Sketch the Candy Design
Before beginning the modeling phase, students should create a rough technical sketch of their proposed candy designs. I don't have a set drawing style I require students to submit, but have included some styles that can be helpful in the image above.
This sketch serves two purposes:
- It gives students a chance to think through their designs and add general dimensions, etc. prior to modeling.
- It gives you (the teacher) a way to ensure their design is appropriate both in difficulty level and content prior to them beginning the modeling phase of the project.
It is helpful to set some guidelines and/or project constraints for size that students need to take into consideration for their designs. For my project, I limit student mold sizes to 2" x 2" by 0.5" deep (for each side of the mold).
Note: With these sizes, I can generally print each 2-piece mold in about an hour, which makes the 3D printing time manageable for an entire class.
Project extension: This is a great opportunity to introduce or reinforce technical drawing techniques (such as orthographic projections and isometric drawings, annotations, etc.), depending on how much time you have for this project. I have included sketches in each of these styles that reflect the level of sketch I can expect to see in my student's projects.
Step 2: Design/Model Your Candy
Once students have solidified their design, it is time to model the project. I strongly recommend having students become familiar with 3D modeling before beginning this project. Any software you currently teach (that allows you to output a .stl file) should work for this project - so if your students have learned anything from Tinkercad to Solidworks to Catia, this project should work great for you.
Task #1: Create a plane that will serve as the surface where the two molds will come together. Determine where this plane will be in your design (sketch) so you can model it accurately.
Task #2: Build two part bodies: one should be a model of the front half of the shape (see the gray shape in the above images) and the other should be a model of the back half of the shape (see orange shape in above images). The two part bodies should combine to make the total shape (with no overlap) when visible together.
Side note: My engineering students are located in Ohio, near Honda R&D and several Honda auto plants and suppliers. Many local jobs related to this industry use the 3D modeling program Catia, and though this project could be completed with any 3D modeling program, my students complete this project after working through a series of tutorials I created in Catia. Tutorials for Catia are hard to come by, so I have included those tutorials below for reference in case you have the opportunity to use this program. Even if you are not planning to make the gummy mold project, the tutorials given below should be useful to familiarize yourself with this program.
CATIA TUTORIALS
- Tutorial #1: Introduction to Catia and How to Create a Basic 3D Part
- Tutorial #2: Catia Navigation and Basic Sketching Tools
- Tutorial #3: Catia 3D Modeling and Rendering
- Tutorial #4: Catia Advanced Solid Modeling I: Creating Part Bodies, Planes, Splines and Shafts
- Tutorial #5: Catia Advanced Solid Modeling II: Surface Sketching, Rib/Slot and Multi-Section Solids
- Tutorial #6: Catia Advanced Solid Modeling III: Solid Body Manipulation (Mirror, Fillet, Chamfer, Shell)
- Tutorial #7: Catia Advanced Sketching: Unit Setting, Dimensioning, and Sketch Manipulation
- Tutorial #8: Conclusion to Catia Basic Part Modeling: Efficiency Tips and Simple Analysis Tools
Step 3: Design the Mold for Your Candy
Once your candy shapes are complete, the last step before preparing them to be printed is to "remove" that shape from a box, or mold (as shown above).
Begin by creating a new part body for the box that will become the mold of the front of the candy as shown in the yellow images above. The box sketch should be created on the plane you originally set as the middle of your candy and be slightly larger than the candy footprint (I generally start with 2" x 2" but size up slightly if needed based on the size of the candy model) . Extrude that box sketch slightly past the thickest portion of the candy (approximately 0.5", slightly more if needed).
Then, remove* the candy shape part body from the box part body to create the open mold shape.
Repeat this for the other side of the candy. When done, you should have two mold shapes that show opposing sides of the candy. I have attached the 3D model (created in Catia) of the example elephant candy and the related molds for reference.
*If using Catia, this remove feature can be found in the Boolean Operations toolbar.
Step 4: 3D Print the Molds
Once your mold designs are complete, save each side as an .stl file to 3D print.
Just as the 3D modeling software you use for this project is open to anything your students are familiar with, any 3D printer and related software should work just fine.
My molds were printed on an older Flashforge Creator Pro and turned out nicely. You can print these with very little infill (I used only 10%) since they will only need to stand up to the force of being clamped closed.
I have attached the .stl files for the example elephant candy molds for reference.
Depending on your class size, it may take you a couple of days to get all the molds printed so you can begin making the actual injection mold systems. This is a perfect time to get in depth with content and explain different manufacturing processes.
If you do not already have a starting point to begin a discussion of the injection molding process with your students, HERE is a great animation from Tronicarts to talk through with them. I have discussed our molding machine system in terms of the labels used in this video for consistency.
Note: You could also use this lesson to highlight casting and/or additive manufacturing depending on where you choose to work this into your curriculum, but I have chosen to talk about this project in terms of injection molding.
Step 5: Prepare the Molds
Now comes the fun part: turning your 3D printed designs into an injection molding system.
The first step to prepare your mold is to determine where you will have your gate, which is the location that the liquid material will enter your mold. I always recommend students select an area on the back of their part that has the least detail possible (see the elephant's back in the images above).
Drill through the mold completely and remove any debris, etc. from the mold.
Next, wash your molds next to ensure the candy you produce is clean.
Before closing up the molds, spray them lightly with cooking spray (canola oil, etc.) to help avoid having your candy stuck in your mold when cool.
Line up the molds (ensuring the molds will come together to make the correct internal shape) and tape them tightly closed with masking tape. This simulates the high pressures that are applied to the injection molding machines during the actual manufacturing process.
Finally, ensure your syringe and tubing fit together and into your mold to prepare for the actual candy injection.
Step 6: Melt and Inject the Gummy Solution
There are several recipes I have used for this project in the past, but the best results have come from the following recipe. This will make enough "solution" for several candies, depending on the volumes of each mold.
- 1 - 3 ounce box flavored gelatin
- 1 Tbsp unflavored gelatin
- 1/2 cup boiling water
To prepare the candy solution: Combine the gelatin and mix with the boiling water until the mixture is fully dissolved and not grainy. (Optional: If you want sour candies, add 1/2 tsp of citric acid to your mixture as well.)
Note: If you are looking for an alternative to the recipe above, check out the recipes below:
To inject the solution:
- Submerge the tip of the syringe in the gelatin solution and pull the plunger until the desired amount has been drawn in. (It's always better to overfill the syringe than under-fill it so you do not run out during injection.)
- Carefully attach the tubing to the syringe and mold.
- Inject the solution into the mold slowly and gently until you see excess solution running out the side or top of your mold. (This ensure the mold is completely full.)
- Remove the tubing and cool the mold in the refrigerator for about a half hour (though up to a day is fine if you want to space this out over two days).
Step 7: Remove the Shaped Candy From the Mold
After the mold has cooled, it is time to remove the part.
Unwrap the tape holding the molds together and slowly pull the mold halves apart. Gently pull up one edge of the gummy and carefully peel it out of the mold. You may need to use a small toothpick or other tool to remove the candy depending on the intricacy of the shape.
And that's it! Your injection molded gummy candy is complete!
For some students, it's hard to eat a project they worked so hard on, so I always let them take the molds home in case they want to make some more candies and/or impress their parents with their gourmet candy production at home.
Step 8: Project Variations
Single Molds
For a simpler version of this project, you can simplify the molding process from injection molding to simply using a single mold to set your shape. The steps for this project are similar except that only one mold is needed and the solution can simply be poured into the mold (as opposed to using the syringe on the taped mold system). This project works great if you have a class who is less savvy with modeling or if you need to squeeze the project into a tight time-frame.
Volume calculations
To amp up this project technically, have students calculate the volume of their gummy candy (using CAD software) and then have them inject only that calculated amount of solution to see if it fills the mold completely. This nicely leads to a discussion about inefficiencies in manufacturing processes (such as the solution left over in the tubing, etc.).
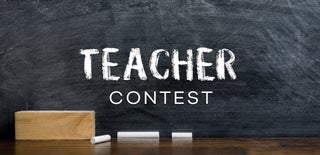
Participated in the
Teacher Contest