Introduction: HOW TO MAKE a LATHE TOOL FROM SCRAP METAL
The chuck key that came with my 1936 South Bend Lathe was pretty worn out by the time I took ownership a few years ago. I've always been a fan of upcycling tools, and tools made from scrap. So, I figured that making a new lathe tool from scrap metal would be a perfect beginner metal lathe project. This is also falls into the category of milling machine projects for beginners. It must be because I'm definitely a noob!
*** Be sure to check out the YouTube video HERE!
Supplies
Metal Stock:
- I often buy new metal cut to custom sizes from Online Metals: http://onlinemetalspartners.go2cloud.org/SF4x
- Scrap and up-cycled metal is always an option.
- Set Screws: https://amzn.to/2SNvR99
Tools:
- Machifit 5C Collet Block Set: https://ban.ggood.vip/TQp0
- 5C Type Spring Collets: https://ban.ggood.vip/TQp2
- Lathe Cutters: https://amzn.to/2GWIegg
- Mill Cutters: https://amzn.to/2FoCDiv
- Emery Cloth: https://amzn.to/33QxyZy
- Threading Taps: https://amzn.to/2SO0wD7
Camera and Video Gear:
• Main Camera - http://amzn.to/2iGbWqP
• Main Lens - http://amzn.to/2zbMboA
• Camera Frame - http://amzn.to/2mRPzmX
• Secondary Camera - http://amzn.to/2Bav3B7
• Tripod - http://amzn.to/2hLnRTu
• Lighting Setup - http://amzn.to/2hJioMT
• Magic Arm A - http://amzn.to/2hKvSIq
• Magic Arm B - http://amzn.to/2Bd3NC3
• Video Monitor - http://amzn.to/2zWoJ1T
• Mic - http://amzn.to/2iEucAY
Step 1: The Old Chuck Key Was Worn Out.
Honestly, I could have still used the old chuck key for quite a while, but this was a great opportunity to design and make a useful shop tool, and learn some more machinist skills along the way.
The original key was very sloppy, so I really couldn't get the proper dimensions from it. I measured the square hole in the chuck and used those numbers for the CAD model.
Step 2: Diggin' Through the Scrap
Over the years I've collected quite a bit of scrap metal, plastic, and wood. Some of it is from cut-offs, while other pieces are from old machinery like computer printers (roller shafts). I've also purchased "ProtoBoxes" from Online Metals. Those are basically just random "drops" they have leftover from customer's custom-cut orders.
The skinny piece of steel that I'm using for the crossbar in this project is actually an old wheel axle from a broken garden hose reel. (I just knew that was going to come in handy someday.)
Step 3: Building the CAD Model
Sure, this could have been figured out on a scrap of paper, but I really enjoy 3D modeling. I like getting a visual for things like this. I think it helps me balance out proportions and finesse the design.
Another benefit of having a CAD model is that I can workout very clean dimensional drawings from it.
Step 4: Dimensional Drawings
I use Rhino3D as my primary CAD application, but the drafting tools are not very intuitive. Lately I've been using Fusion360's Drawing module. I simply export in STEP (.stp) format and it imports to F360 very easily.
This procedure also gives me practice with creating dimensional drawings, in case I ever give them to other people. Making parts from my own drawings is very good lesson!
Step 5: Time to Start Cutting Metal!
To be sure I had the best lathe chuck grip on the steel, I went over it with a wire wheel to remove the excess rust. Once it was locked in place, I drilled a center taper hole so that I could use the tailstock for extra support while turning.
I measured off the total length of the working area and put a slight witness mark into the surface with the parting tool.
Step 6: Three Diameters and Some Bevels
Starting at the smallest end, I cut the three diameters. The two transitions received 0.500" bevels at 45 degrees.
After shining up the finished surfaces with some emery cloth, I used the parting tool to separate it from the rest of the raw stock.
Step 7: Checking Dimensions
As I was turning the part I did check the diameters with a micrometer, but I still went through and double checked everything to the drawings. Once satisfied, I put it back into the lathe chuck and trimmed of the little 0.250" long stub that I had used for the tailstock center.
Step 8: Flipping It Around
I switched ends in order to cut the large taper on the big end. I also smoothed all the edges with emery cloth because that is the area where it will contact the palm of my hand during use.
Step 9: More Drilling
I made a small pilot hole with a center drill. That provided a really good start for the 7/32" tap drill. I also used a countersink cutter to add a chamfer. This makes it look nice, and also helps the thread tap get started.
Step 10: Tapping the Threads
I used the tailstock center to help keep the tap aligned while getting it started in the hole. While everything was still set up in the lathe, I checked to be sure that the 1/4-20 set screw threaded in far enough to interfere with the future crossbar.
Step 11: NEW Tools!
This was going to be the very first time that I would be using my new collet blocks. In this case the four sided block would provide indexing to cut the four sides of the key end. My set of collet blocks fit 5C collets. I chose 5C because of their wide range of work holding capabilities. These also have internal threads for adding a stop device inside, for repeatability.
Step 12: It's Milling Time!
I purposely sized the middle diameter of this new tools shank to be 1/2" so that it would fit into the 0.500" collet. I did use a spanner wrench to tighten the locking ring. (not shown)
Step 13: Test Cuts
After locating the block in the mill vise and finding the edges, I made a couple light test cuts just to see how this would work. I wanted to "sneak up" on the final dimension, as to not cut too much off.
Step 14: Final Cuts
My strategy worked! I hit the final sized within 0.0004"! I know this is very simple machine work, but it's very satisfying for a beginner like me.
Step 15: Drilling for the Crossbar
I swapped ends of the part in the collet. This allowed me to drill and chamfer the through-hole for the 5/16" crossbar.
Step 16: Cleaning Up That Old Axle
Upon close inspection, I noticed that the first two inches of the old hose cart axle was badly worn. I cut off that part and proceeded to clean up the surface with emery cloth.
Step 17: Gettin' Fancy!
I'm sure that the crossbar would work just fine with flat ends, but any time I have a chance to use my "Ball-Turner" lathe accessory, I do!
C'mon, it does look extra nice... Right?
Step 18: Installing the Crossbar
I milled a small flat spot in the middle of the rod to give the set screw a wider place to land. It worked out very well and looks great too!
Step 19: Test Fit
This new chuck key has a wonderfully smooth feel and fits so much better than the old one!
Now I'm a little afraid to use it. Well... it might get scratched. LOL!
Step 20: Some Beauty Shots!
I am so pleased with how nice this project turned out.
I learned a lot and got a new tool!
Step 21: Check Out the YouTube Video!
YouTube video is NOW AVAILABLE! There are many more details in the full video. Please go check it out.
Many of my plans, drawings, and 3D models are available for FREE download on my website here: https://www.worksbysolo.com
I hope you enjoyed this Instructable! Do you like my work? You can also find me on other social platforms!
• My Website: https://www.worksbysolo.com
• Patreon: https://www.worksbysolo.com
• YouTube: https://www.youtube.com/worksbysolo
• Instagram: https://www.instagram.com/worksbysolo
• Twitter: https://twitter.com/WorksBySolo
We are a participant in the Amazon Services LLC Associates Program, an affiliate advertising program designed to provide a means for us to earn fees by linking to Amazon.com and affiliated sites.
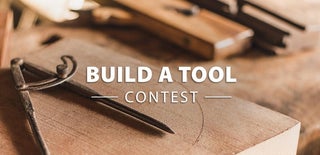
Runner Up in the
Build a Tool Contest