Introduction: How To: Restore an Axe- Two Tone Handle/Leather Sheath
In this inscrutable I will be going over the steps to take an old rusty axe head, some rough sawn ash, scrap teak, and veg tan leather and turn it into a beautiful tool that will last a lifetime!
The video below details the entire process:
For. detailed write up of the entire process continue onward into this instructable!
Step 1: Materials and Layout
I got this old axe. head from a garage sale a few years ago. It was made by true temper in Nebraska USA in 1994 ( its stamped with the year) From my experience American made axe heads hold an edge better than less expensive chinese imports. If you can't find on locally, eBay is a great source for vintage axe heads.
The handle design I am using is one I developed by combining a few handle shapes that I liked the most. My suggestion is to visit a store that sells axes or axe handles, and see what shape you like. Snap a photo of it and sketch it out on some large paper, if you find you like the shape a lot, make yourself a plywood or cardboard template so you can make more.
I begin this project by tracing my favorite axe handle shape onto my rough sawn Ash lumber.
Ahs is VERY strong material, and I really like it for use as an axe handle.
Step 2: Rough Cutting the Handle
Once your haps is traced, you'll want to cut out the handle. I use a bandsaw with a thick blade to handle this desert material, but you could use a quality jigsaw just the same.
The material I am starting with is 2 1/4" thick, and my handle will be about 1" which when its finished, so once I cut out the blank I am able to rip it in half on the table saw, and save one blank for a future axe handle.
Step 3: Layout the Inlay
The interesting accent on this axe is the two tone handle. I don't lay this out with any particular geometry, I just draw a shape that I think will compliment the shape of the handle. I made a quick template of the shape so it would be exactly the same on each side.
Step 4: Router Out the Handle to Receive the Inlay
Im using a trim router with a straight cut bit to remove 99% of the material for the inlay. Once thats done I use a simple plywood guide, and a pattern bit to make the lines perfectly straight, and get both sides symmetrical. Its important that these inlays be equal so when you look down the back or front of the handle they are nice and even.
Step 5: Refine the Inlay
Depending on how well you router the handle you may be able to skip this step. The bottom cut on my routed sections was not so great, so I flattened them out using my 2x72 belt sander and an 80 grit belt.
Step 6: Selecting the Inlay Handle Scale Material
Once I had the handle ready to receive the scales I went over to my scrap wood area and found a nice piece of teak. The teak contrasts the light colored ash very nicely and is a super resilient wood that will last forever.
Step 7: Cutting the Handle Scales
I translate the angle of the routed section in the handle using a straight edge, then go over to my miter saw to cut a nice clean cut at that exact angle. Once thats done I match the handle to the teak material and trace it out. Once I've got the shape traced I rough cut it on the bandsaw, then resew it using the bands fence. I leave all this material a little oversized because its all going to be sanded to match once its glued up. I used a belt sander to flatten the backs of the scales so they mate well with the handle.
Step 8: Glueing the Scales to the Handle.
At this point its epoxy time. I have made similar axes in the past using wood glue, but the gap filling properties of epoxy coupled with its strength really makes it the better choice. This epoxy is West System G5, it sets up in about 20 minutes and is very strong. I apply it liberally and clamp everything up making sure to seal all the gaps. While the epoxy dries ill begin my work on the axe head.
Step 9: Cleaning Up the Axe Head
This axe head is in pretty good shape for being 23 years old. Its got surface rust and pitting, but its not that bad. I start with a 36 grit flap wheel and just get everything down to even bare metal. Once thats done I switch to a palm sander, and then a wire wheel to get the finish even. I move over to my bench grinder to further the process of getting a uniform finish. Finally a quickly buff the head with black compound on a stiff wheel to get an even sheen.
Step 10: Deburring the Inside of the Head.
Most vintage ave heads have burrs in side the head from years of use, so using a file or in my case, a Dremel you can remove those burrs so the handle will fit into the head with less interference.
Step 11: Rebuilding the Edge.
The edge on my axe head had a few gouges in it so I grinned it back to shape, then using a few grits of sanding paper I reground it to a geometry that I like. There are MANY ways to rebuild an axe edge, and I encourage you to look on youtube at videos describing axe geometry to learn more about it. I finish my edge with a leather strop and its ready to cut.
Now that this parts over, back to the handle!
Step 12: Shaping the Handle
Sanding, sanding, and more sanding.
There are many ways to shape an axe handle, I prefer to use my belt sander. I use a stiff wheel to bring the high spots down to a uniform thickness, then switch to the slack belt. Using the slack belt allows me to lean into the sander getting a nice naturally rounded shape across the length of the handle. DONT RUSH THIS PROCESS. Your hands are your guide to this, feel the handle as you work, make this axe handle ergonomic to YOUR hands (or if your making it for someone else, ask them to stick around and give you their input on the shape) Little dips and swells can make a big difference in the comfort of an axe handle. Its all about preference, and enjoying the use of tool you are making. Have fun with this part!
Step 13: Shaping the Top of the Handle to Receive the Axe Head.
I will admit, here is where it an all go bad. I have ruined a few axe handles trying to fit the head, so TAKE YOUR TIME.
You will now trace the inside shape of your axe head into the top of the handle. MAKE SURE ITS CENTERED AND NOT TWISTED.
Once you get it drawn out, darken the line so you can really see it. Now I move over to the flat platten on the belt sander and work my way toward that shape slowly and evenly. At this point you want to be constantly checking the fit, and once it goes about half way on STOP. You will then need to make relief cut down the center of the top of the axe head, so you have room to drive a wedge later on.
If you made it past this part GREAT JOB!!
Step 14: Putting the Head On!!
Moment of truth!
I knock the head of this axe on by hitting the actual axe head with a good sized hammer. There are other ways to do this, but this is how I choose to. The axe head is already banged up so I don't mind giving it a few more dings and dents.
Do this part slowly, if its not going to fit and you try and force it you may break the handle, so take your time, hit it evenly, and be patient.
Once the head is on, put a wedge in the slit you cut with the bandsaw. I chose to make the wedge out to matching teak.
Step 15: Glueing the Head, Filling Some Gaps.
If you do a superb job shaping the top of your handle to perfectly match the hole in the axe head you may be able to skip this step, but I aways have a few gaps and glue my axe heads.
I mix up some West System epoxy, and add black dye to give it a clean look. Using painters tape a build up the walls of the axe head to make a well that the epoxy can sit in so it fills all the hole in the wood around the inside of the head. I let this dry overnight and come back to it the next day to grind away the remaining epoxy.
Step 16: Cleaning Up the Epoxy
Once the epoxy is full cured I jump over to the Balt grinder to take away whatever is oozed out of the top.
Step 17: Finish Sanding the Handle
At this point the handle is ready to be finish sanded. I use an orbital sander with grits from 120 up to 220, then hand sand it with 320 to make it nice and smooth.
Step 18: Applying Finish
This might be the best part of the whole process!!
I use clear mineral oil to finish the wood handle. I will apply a few coats throughout the day and let each coat soak in. There may be no better feeling than applying oil to unfinished wood! At this point you can see the fruits of your labor!
I continue onward to make a leather sheath, if your stopping here congratulations! You've made a beautiful axe with a handle that will almost definitely outlive you (if you take care of it)
Continue onward for the leather sheath!
Step 19: Laying Out a Leather Sheath.
Im using veg tanned leather to make this sheath. Its an offset that already has a half circle in it so I use that she to dictate the shape of the sheath. I designed this on the fly, and let the axe head tell me how to cover it. I like to use small spring clamps to get an idea of how I want to stitch the sheath, and I used a pencil to mark directly onto the leather as I go.
Step 20: Punching, Stitching, and Riveting.
Once I get the shape cut and I know how I want to lay out the seam I apply glue along the edge and begin to punch the holes. I use a few different size prong punches to lay the track for the stitches. Once the track is done I stitch it using tan waxed thread. I get almost all my leather supplies on Amazon, or Tandy leather. Once the sticking is done you'll want to install rivets at the beginning and end of your stitch track to really lock it in.
Step 21: Adding a Strap and a Snap.
You'll want to be able to lock this sheath onto the axe head. To do that I cut a small strap, and rivet it to one side of the sheath. The other side of the strap gets a snap so its easy to remove the sheath, but also very secure. I make this strap very tight because the leather will stretch over time. I burnish the edges of the strap using a scotch brite wheel on the buffer.
Step 22: Adding a Belt Loop.
This was sort of an afterthought, but it worked out well. Using glue, and 4 rivets, I added a belt loop to the back side of the sheath. Normally I would stitch this on, but since I didn't think to do it until after the sheath was stitched I had no choice but to rivet it.
Step 23: Embossing a Logo Into the Sheath.
I plan to do a full inserucable on this process but here is a quick abbreviation of how to add a custom logo to a leather project.
I rendered my logo in sketchup, and 3d printed a mirror image of it using my makerbot. I then glued it to a piece of plywood. Using my vise I clamp the stamp against the leather with a wood backing and it presses the logo into the leather permanently. Im still experimenting with this process but so far its worked really well!
Step 24: Finishing the Leather Edges
I learned this tip in a knife making book a few years ago. I used a worn sanding belt to finish the edged of my sheaths. It burnishes the edges really nicely and makes it all very even. I round the edges slightly and get any frayed sections down.
Step 25: Finishing the Leather.
Using neatsfoot oil I finish the leather to give it a natural look that will help it repel water and keep it from cracking.
At this point your done! (But check the last step for some glamour shots and some notes)
Step 26: Admire Your Finished Piece!
You did it!
This project has a lot of steps, but I completed it in 2 half days in the shop. My favorite aspect to this is the legacy of the axe head being carried on with a new handle. I believe that vintage tools should be cared for and carried forward as part of history, and I love restoring them.
I hope you enjoyed this instructable. I will be entering it in the "before and after" contest and if you like it I would appreciate your vote. Please ask me any questions in the comments, and if your a youtuber, please subscribe to my channel for more video and how tos like this!
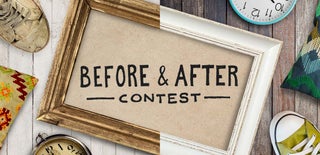
Second Prize in the
Before and After Contest 2017
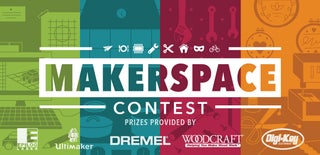
Participated in the
Makerspace Contest 2017