Introduction: How to Make Resin Beach Art
In this Instructable, I show you how to make beach art with resin and reclaimed wood. This project can be used as wall art or as a small table.
There are several things which are difficult to fully explain with words and images, so be sure to check out the video tutorial above.
Supplies
Material Used
Tools Used
Digital Protractor Angle Gauge
Step 1: Choose Wood
For this resin ocean wave art project, I decided to use 2 pieces of reclaimed cypress wood to make ocean waves.
I say the wood is ‘reclaimed’ because I found it in a burn pile at my wood dealer's warehouse. Basically, the type of wood and size doesn't matter. Just make sure the wood is in decent shape and the same size (if using 2 pieces).
Step 2: Sand & Cut Wood
I rough sand from 40 grit up to 120 grit to simply remove loose debris and reveal the wood grain. My sanding sequence started at 40 grit with my sander in rotex (coarse) mode in order to knock down the resaw marks from a bandsaw. Then, I used 60 grit, 80 grit, 100 grit, and 120 grit in rotex mode.
I used my combination square and marking knife to mark a line roughly 36″. Why did I trim it to 36″? The 2 pieces of cypress wood were level (flat surface) up to 36″ before it became thinner and sloped down. I didn't want to deal with an uneven surface.
The marking knife created a tiny groove, which made it easy to start the cross-cut with my Japanese pull saw. As a quick tip, it helps to get the cut started with a ‘pushing’ motion when using a Japanese pull saw.
Step 3: Make Epoxy Mold
First, I used a piece of 1/2" plywood as the base. Next, I covered the board with packing tape and coated the packing tape with furniture wax.
The sides and ends should be as long, wide, and tall as the table. I also covered the sides with packing tape and secured them with brad nails to the rear of the table.
For this project, I only used 2 ends because the wood on each side served as the sides. I used a silicone caulk (any type will work) to seal all edges, seams, and corners.
As a quick tip, clamp the wood to the resin mould before sealing with silicone caulk. If I clamp the work piece down after sealing, I risk breaking the caulk which causes leaking.
Finally, I checked to make sure the surface was level.
Step 4: First Epoxy Pour
For the first resin pour, I mixed 48 ounces of epoxy resin in a mixing container. My daughter likes watching epoxy resin pours. She especially likes when I mix pigments and dyes in the epoxy resin. Next, I mixed the material until it was clear. Most epoxy resin gets cloudy during the mixing process. The material becomes clear when fully mixed.
Step 5: Add & Mix Translucent Blue Dye
Once fully mixed, I added the translucent blue dye. As a quick tip, translucent resin dye darkens with each epoxy pour. So, do not mix too much dye on the first few epoxy resin pours.
I always add a very small amount of translucent dye to resin, mix, and inspect. Keep in mind, I can add more if the color needs to be darkened.
Step 6: Pour Resin
I poured the resin into the mold and allowed it to settle for a few minutes while I checked for leaks.
Step 7: Add Alcohol Ink
I add alcohol ink within 3 to 5 minutes after the resin pour. It is important the resin to be fluid in order for the alcohol ink to disperse correctly. I used the bottle to pour white alcohol ink across the length of one side near the wood.
Also, the point here is to make it appear as though waves are crashing on the shore. In order to get the lace effect or water effect, I only needed to move the alcohol ink a few times. There is no right or wrong way to go about creating resin ocean wave art. I encourage you to do what feels right to you. After all, art is about self expression.
Step 8: Second Epoxy Pour
For the second resin pour, I repeated the exact steps for the first resin pour - 48 ounces, transparent blue dye, etc.. Again, I allowed the resin to cure for 24 hours. As a quick tip, the color darkens quickly when using transparent dye with multiple layers of resin. In other words, the color compounds with each layer. I made this mistake once and there is not a way to fix it. So, be sure the color doesn’t get too dark by the time you reach the final epoxy resin pour.
Step 9: Second Alcohol Ink
I poured the alcohol ink in the tinted resin as I did in the previous step. This bottle does not have a spout, so the alcohol ink dripped down the side of the bottle. Consequently, I poured more than I intended.
I used my heat gun to move the resin until I achieved an ocean wave pattern. Remember, less is more when creating resin ocean waves. You will feel an overwhelming urge to keep fiddling with the waves. Just don't b/c it won't end well.
Step 10: Third Resin Pour
For the third resin pour, I repeated the same process as the previous 2 layers. In order to create more of a 3D ocean wave effect, I used my heat gun to roll some of the blue resin over the alcohol ink. I did not want the surface to be too white considering I had one more epoxy resin layer after this one.
I almost forgot to mention the resin inlay in the previous step. This piece of cypress wood had many imperfections, so I decided to pour resin into a crevice in the wood and add alcohol ink. This not only secures the imperfection, but also adds to the look of the piece.
Step 11: Final Resin Pour
Yep, you guessed it! I repeated the same process as the previous 3 resin pours for this resin pour. I poured the final resin layer and allowed it to settle for a few minutes.
Step 12: Final Alcohol Ink Layer
I added alcohol ink and started working it in the resin with the hot air. There is no right or wrong way to do this - simply work the alcohol ink until it looks and feels right to you.
As you can see, the ocean waves appears as though half of it is under the surface of the water. This is the 3D effect. I find it really helps to roll the blue resin over part of the white alcohol ink to create depth at the very end.
After I rolled the blue resin over, I left it alone. Furthermore, it is a bit more difficult to accomplish this effect with a deep resin pour especially if you don't have much resin experience.
Step 13: Remove From Mold
After the resin beach art cured for 48 hours, I removed the epoxy mold without issue. This part of resin beach art projects causes me to feel anxious. If leaks exist, it means a lot of messy work to clean it up on the underside.
Step 14: Trim to Size
I used my Festool TS75 track saw and track to trim the ends and sides.
Step 15: Sand Resin
I realize some folks may get nervous when sanding epoxy resin. Most believe the scratches caused by sanding won’t come out. Ultimately, the process is not difficult as long as the proper sequence and technique is used.
My resin sanding technique consists of the following sanding grits. Also, the ‘C’ stands for coarse mode and the ‘F’ stands for fine mode in my dual action sander: 40C, 60C, 80C, 100C, 120C, 120F 150F, 180F, 220F, 320F.
Step 16: Polish Resin
I use festool MPA5010 orange polish with the orange waffle sponge to polish wood and resin. Again, you don’t need this setup to polish resin. Simply polish the resin the same way as a vehicle – with a car buffer and polish.
First, I spread the material on the surface and rub it in with the sponge to prevent splattering. I use the lowest speed setting and gently go over the surface as if I were sanding.
Then, I use the sheepskin bonnet to buff the polish out.
Step 17: Final Thoughts
I hope this instructable provided you with value. Please feel free to leave a comment if you have any questions - I'm happy to help.
Be sure to checkout my YouTube channel and my website for more DIY tutorials.
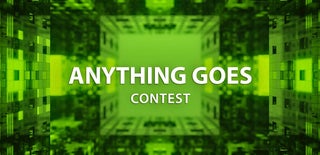
Participated in the
Anything Goes Contest