Introduction: Indecisive Drawbridge: a K'nex Ball Machine Element
This is an improved version of an element from a ball machine I made recently. The ball travels down a ramp, and its impact at the end lowers the drawbridge. The ball then crosses the drawbridge, realizes it doesn't lead anywhere, heads back, and drops onto whatever path or element is underneath it. The element also includes a "safety path" for when two balls go down at a time. It captures the second ball and sends it out the side of the element.
The element itself is much smaller than the support frame shown, the frame was just to allow a reliable entrance track for it. I tried to make it modular enough that it could be adjusted to fit other designs.
For some reason, I'm having trouble getting videos to embed, so here is a video of the element as a link instead.
Supplies
The supplies listed here are for the entire instructable, including the frame, exit paths, and entrances. Counting the parts is, of course, optional anyway.
Connectors:
- Gray one-slot: 9
- Gray two-slot: 7
- Orange: 24 (element) + 4 (Entrance ramp V2)
- Red:12 (element) + 2 (Entrance ramp V2)
- Green: 9
- Yellow: 23 (element) + 4 (Entrance ramp V2)
- Blue: 19 (element) + 4 (Entrance ramp V2)
- Purple: 30
Rods:
- Green: 31 (element) + 6 (Entrance ramp V2)
- White: 29 (element) + 10 (Entrance ramp V2)
- Blue: 26
- Yellow: 13
- Red: 35
- Gray: 27 (element) + (Entrance ramp V2)
Other:
- Clip tire hubs (with tires): 2
- Medium tire (without hub): 1
- Silver spacers: 4Blue spacers: 2
- Ball clips: 2
- Tan clips: 2
- Y-clips: 7 (element) + 4 (Entrance ramp V2)
Bricks (Entrance ramp V1 only):
- 2x2 brick: 2
- 2x4 brick: 5
- 2x8 brick: 2
- 2x10 brick: 4
- 2x4 plate: 3
- 2x8 plate: 4
- 2x4 slope: 3L 3R
- 2x6 slope: 1L 1R
- 3x13 slope: 1L 1R
- sloped hood: 1
- 1x4 K'nex to brick adapter
Step 1: Supports
The machine from which this came was built on a gray rod scale instead of a red rod scale, but the element itself is at a diagonal to the rest of the machine, thus putting it back on red rods. The frame shown here is based on the original machine to mimic the conditions under which the element operated. For using this in a red scale machine, the most important things to make sure of are that the counterweight has room to swing up, that the bridge has room to move out until it is level, and that the ball has enough momentum to trigger the bridge.
- The frame begins with the hexagonal base shown. If you choose to make the same exit track shown in these instructions, the gray single-slot connectors in the center will be used to attach it. Otherwise, ignore them. Since the bridge just drops the balls, other exit track designs will work (and are encouraged).
- This small spindle starts the support for the top of the entrance.
- The spindle connects to the back of the base, where the two all-purple 3D connectors are.
- This piece goes on top of the spindle.
- Here it is attached to the top of the gray rod.
- Now to begin turning the spindle into a proper frame. This wall will support one side of it.
- Here is the attached wall.
- This wall will attach to the other side.
- Both walls are now attached.
- This wall will go on the front of the machine, near the bridge.
- It attaches to the first wall you added.
- The last wall attaches to the remaining space on the front. The yellow connector is for attaching a pair of free-falls that join the secondary path back to the main path. If you like the free-falls but want the paths to be separate, move the connector to the other side. If you don't want the free-falls at all, just ignore it.
- This is a close-up of how the yellow connector attaches.
- Here is the wall attached to its spot in the frame.
- This is a front view of the frame so far. The bridge will go in the gap between the front walls.
- This brace keeps the gray rod from rotating. It will stabilize the safety track later.
- This is part of the exit for the safety path. One of the slots on the blue 3D connector is broken, but that was unintentional. You will not have to modify any parts for this element. I just used it because it didn't affect the end result.
- These will form a corner to clip on to the side of the frame.
- Here is the completed corner.
- Here it is attached to the frame. It goes beside the wall with the brace that locks the gray rod from rotating.
- This will go on top of the frame. The ball drops through the hole in the center to enter the element.
- These parts hang below the hole to support the entrance track.
- Here is the support attached to the upside-down hole.
- Here is another view.
- With the entrance hole on top, the frame is now complete.
Step 2: The Drawbridge
It's really just a single zig-zag element on a hinge and counterweight, but that wouldn't sound nearly as fun.
- This part forms the far end of the bridge. The rod is yellow, and the spacers will allow the ball to pass through.
- Two gray rods with Y-clips will act as the lower return path.
- The Y-clips attach to the two inner orange connectors.
- A yellow rod with two orange connectors will spread the lower path so the ball can fall through. Friction is sufficient to keep them separated on this end, no spacers necessary.
- This is the assembled structure so far.
- The upper path consists of two gray rods, three orange connectors, and two blue rods as shown. The tan clips are to give the ball an extra nudge forward after the bridge descends.
- The upper rail is assembled as shown. The distance from the end of the rods to the orange connectors can be adjusted later, but it must be the same for both rods, and the orange parts should be pressed together.
- The upper piece connects to the orange connectors on the lower path.
- This is the final assembled bridge.
- Now to set the bridge itself aside and start the counterweight. It starts with two yellow connectors, three blue rods, and a medium tire (not the hub).
- The tire goes between the yellow connectors, and the blue rods attach in the slot above the rod that connects the connectors.
- A pair of medium clip-on hubs with tires go on the ends of the central blue rod.
- Here is the counterweight. Now to make the hinge that connects it to the bridge.
- The hinge is the two orange connectors on the red rod, but the green connectors, yellow rod, and gray clip will be needed to ensure it all works properly.
- The yellow rod attaches as shown so that the gray connector points down.
- The counterweight attaches to the hinge as shown.
- Here is the assembled counterweight and hinge. Note that the axle holding the weights is above the blue rods.
- The part shown is part of the mounting system. The purple (silver) 3D connector near the front should be at the end of the rods, and the other one can be adjusted later. Don't forget the Y-clips.
The rods attach to the green connector as shown. The mechanism is now right-side up.
- These parts will guide balls that get stuck under the bridge onto the safety path.
- The primary guide assembles as shown.
- The purple connector with the blue rod acts as a secondary guide to ensure balls land on the bridge. Both guides will attach to the red rod. A red connector should work; I was just using all of those for something else.
- This is how the guides fit to the hinge. The gray connector on the primary guide should be above the gap between the orange connectors.
- Here is another view of the attached guides.
- The bridge should now attach to the orange connectors.
- The full drawbridge is now assembled.
- The last two pictures are two views of the where the bridge connects to the frame. When the entrance ramp is connected, adjust the three orange connectors and two tan clips on the upper deck until the rods are about even with the end of the ramp. It doesn't have to be exact though, so if friction becomes an issue, you can adjust them to reduce the friction without changing the effect too significantly.
Step 3: The Failsafe Track
This track is for balls that fall under the drawbridge. This is not likely to happen unless the machine vibrates significantly or two balls come down the track together. Since the track can lead to alternative paths, this may be done on purpose.
- The track starts with the pieces shown.
- To hold it at an angle, the blue rod connects to the ball end of one piece and to the gray-connector end of the other piece.
- These two parts form a drop-off to get the ball out of the way.
- The Y-clips on the drop-off track connect to the balls on the first track.
- Here they are connected. The orange piece is for the next step.
- The two orange pieces attach to the gray rod from the drawbridge, and the drop-off connects to the gray rod on the frame.
- Another view of the connection. The orange connectors and purple (silver) connectors should be positioned close together, but spread out enough that the counterweight can rise as high as possible.
- Here are some more guides to keep the balls on track.
- The claw-shaped guide goes on the outside of the curve.
- The yellow (gray) rod and the hook attach to the inside of the curve. The gray connector either holds balls still until the bridge rises or allows them to pass immediately depending on whether it is flipped up or down. (In the picture, it is flipped up and will hold balls still until the bridge pushes them out onto the track.) The blue connector smooths the curve to help them go around it.
Step 4: Entrance Track V1: K'LEGOs
This is the ramp I used in my ball machine. Originally, this started as an attempt at finding a use for the K'nex-LEGOs (K'LEGOs?) in a project. It isn't as strong as I would like, but it could be made stronger using other LEGO parts for reinforcement. Alternatively, you can make entrance track V2 from classic K'nex parts only. For that, skip this step and follow the next one. As another alternative, any ramp or element that generates sufficient speed to operate the bridge can be used as an entrance, and this can be ignored entirely. The most important thing here is making sure the ball has enough momentum to trigger the bridge.
- The ramp starts with two 2x8 stud plates, two 2x4 bricks, and a 1x4 half-K'nex axle.
- The plates stack on top of each other, and they and the axle attach to the bricks as shown.
- Two more bricks attach to the top of the structure to hold it together.
- An engine-hood-nose-thing (the white thing in the picture) attaches to the top to act as a ramp while a 2x8 brick attaches underneath as shown.
- Two mirrored 3x13 sloped and tapered bricks form the first part of the track. A 2x10 brick attaches under the pointed end of each as shown in the picture.
- Here is what the ramp looks like so far.
- The next parts include the following: one 2x8 brick, two 2x10 bricks, two 2x2 bricks, two mirrored 2x7 sloped and tapered bricks, and six mirrored 2x4 sloped and tapered bricks. The layout shows how they will attach when assembled.
- The main ramp is now assembled.
- Flipping the ramp upside-down allows you to reinforce the structure from underneath.
- The plate/brick thing goes between the large slopes next to the brick that holds them to the support. (A brick would work, but I used those up.)
- Three 2x4 plates and two 2x8 plates will hold the rest of it together.
- One 2x4 plate holds the plate/brick thing from earlier to the other brick. The remaining plates reinforce the other weak points as shown.
- Four classic-K'nex-to-K'LEGO adapter pins will help support the ramp.
- The pins go into the holes closest to the reinforcement plates at the end of ramp.
- The ramp is now completed.
- To attach it to the frame,the axle goes in the connectors under the starting hole on the frame.
- The bottom of the ramp attaches to gray connectors that slide onto the gray rods on the bridge.
Step 5: Entrance Ramp V2: Classic Parts
For anyone who doesn't have K'nex bricks or prefers not to use them, this is an alternate entrance ramp. It is just a standard three-rail path with some adjustments to fit in the same space. It is sturdier than version 1, so you may wish to use it for that reason as well. Anyone who uses the brick ramp or who would prefer to design their own ramp may skip this step.
- The ramp is one gray rod and one white rod long. Note the blue connectors on the white side of the side rails and on the gray side of the center rail. These are important.
- This is the ramp assembled.
- These parts will hold up the top of the ramp.
- The white rod snaps into the center of the yellow connector.
- The Y-clip will attach to the blue connector on the center rail.
- Here it is connected. The yellow connector goes under the ramp.
- These four parts will hold up the bottom of the ramp.
- They attach underneath the track as shown.
- The track is now ready to be attached.
- The yellow connector at the top attaches between the two holders using the green rods.
- The bottom connects to four gray connectors which slide onto the rails from the drawbridge.
Step 6: Exit Track (Semi-optional)
This is one example of an exit track to collect balls from the bridge. Since the main element drops balls straight down, almost anything can be used to catch them. Similarly, almost anything can be used to catch balls coming off the safety path. This particular design uses free-falls, a two rail track, and a three rail path to catch the balls.
- This version of the safety track drops through a pair of free-fall holes. Those start with the pieces shown in the picture.
- The two parts connect as shown. They will fold over each other later.
- The lower hole will attach to the yellow connector on the frame.
- Here is the lower hole attached to the yellow connector.
- The upper hole attaches to the connectors near the safety ramp.
- This ramp leads to the main exit track.
- Here is how it connects to the frame under the free-falls.
- Here is another view of the connection. Adjust the height until the ball you are using can roll under the free-fall easily. If you use both types, adjust it for the larger, single-piece balls.
- The main exit ramp starts with a three rail path. The center is one gray rod, but the sides are two yellow rods each.
- These connectors will join the yellow rods. Note that one uses a Y-clip and the other does not.
- Here is the assembled path.
- The blue rods connect to gray connectors in the bottom of the frame.
- The orange connectors clip to the vertical sides of the frame.
- Here is another view of the center connection. The exit track is now finished.
Step 7: Exit Track Modification - Path Separators (optional)
Since the machine works with both types of K'nex balls, it can be used to separate them based on their size. Also, the safety track can be redirected to other paths as well. This gives it potential as an element, a two way separator, or a three way separator depending on how you choose to modify it.
- The size selector mod is basically a barricade positioned so that balls fall to one side or the other based on how far they travel across the bridge. This barricade is designed to attach to the exit track shown in the remaining pictures.
- Since the balls drop from some height, you will want to guard the sides of the track to ensure they don't bounce off.
- Here is the barricade replacing the original high end of the primary exit track.
- Smaller balls don't roll all the way back, so they bounce off the face of the barricade and roll forward.
- Larger balls roll over the barricade before they drop, so they continue backwards.
- Here is the safety track exit mirrored so that the balls roll away from the primary exit. Finding an alternate route for the failsafe is particularly useful if you use this as a size separator and if the other exit tracks lead to elements that only work on one size. Since the safety path accepts both types of balls, having it lead away from such elements will prevent malfunctions in them.
Step 8: Finished!
I hope you enjoy this element!
Since it was a bit of an experiment, any improvements and modifications to the design are welcome.
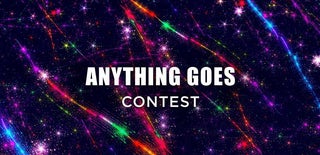
Participated in the
Anything Goes Contest