Introduction: Infinity Cube in Fusion 360
Infinity cubes have become a popular fidget gadget. I wanted to design one on my own using Fusion 360 to 3D print in place. There are several existing designs on Thingiverse; however, they don't provide the design files for customization. I will walk you through the creation process and provide the design files and STL files for you to modify and print your own customized design!
Print-in-place designs can be tricky to perfect. The designs typically use loosely fitting joints/hinges with enough of an air gap around them that they move freely, but not enough that they come apart. It can be a tricky line to walk. Sometimes you might not have enough clearance and your design may fuse together. Other times, you may have too wide of a gap that it may come apart or it may bridge poorly and become hard to move.
There were a few different revisions for this design. At first, the cubes had a rod that traveled all the way through the hinge. These rods ended up restricting the movement too much and would wear down over time. I then proceeded to try pairs of rounded interlocking pins. Eventually, I determined that creating conical pins and sockets on the hinge and cube would provide the most freedom of movement without sacrificing the strength or durability of the assembly.
A complete walk-through tutorial on creating this design in Fusion 360: https://www.youtube.com/watch?v=UlSd0zvG-_E.
A demo of the cube in action is here: https://www.youtube.com/watch?v=gpM8QhBmqXA.
The design files are also available on Thingiverse: https://www.thingiverse.com/thing:4997903.
Supplies
- Fusion 360 (students/educators qualify for free)
- 3D Printer
- PLA filament
Step 1: Designing the Cubes
Create a sketch on the bottom plane (X-Z by default) as shown. Use the two-point rectangle tool to create a 20 mm x 20 mm square that begins with the top left corner at the origin. Create a second 20 mm x 20 mm rectangle that is 0.4 mm away with horizontal lines colinear to the original square. The sketch should now be fully dimensioned.
After finishing the sketch, extrude each of the squares upwards by 20 mm to create two separate cubes. Apply a 3 mm chamfer to all edges of each of the cubes.
Step 2: Sketching the Hinges
Create a sketch on the top face of the cube placed at the origin. By selecting the top face, Fusion 360 automatically projects the edges of the face into the sketch.
Create a rectangle for the cut area to make space for the hinge. The rectangle should be 10 mm x 7 mm placed 2 mm from the side edge of the face and 10 mm from the far edge. Make another rectangle inside the previous rectangle to use for the hinge extrusion. The rectangle's dimensions should be 9.2 mm x 6.8 mm and it should be offset inside the other rectangle by 0.4 mm. It will extend over the edge of the cube by 0.2 mm.
Delete the edge of the face that intersects with the squares (between the purple dots) by selecting and hitting the delete key. This will make the later extrusions easier.
Finish the sketch. Create three more identical sketches for the other hinge connection points. See the animation to see all four of the hinge connection points.
Step 3: Cutting/Extruding the Hinges
Select the 10 mm x 7 mm rectangle by selecting the outer "U" shape profile and the smaller internal rectangle profile. Perform an extrude cut with a depth of -7 mm.
Next, select the 9.2 mm x 6.8 mm internal rectangle profile as well as the 0.2 mm rectangle that hangs over the edge. Perform an extrusion with a depth of -6.6 mm.
Finally, select the inside horizontal edges of the hinge facing the cube to apply a 3.3 mm fillet. This will round off the hinge entirely and improve clearance and mobility.
Repeat three more times for the other half hinges. Make sure you select "New Body" (not "Join") when doing the extrusions for the hinge. We want to keep each half of the hinge separate to allow us to more easily duplicate/mirror the additional cubes and hinges.
Step 4: Creating the Pins/Sockets
Sketching Pins/Sockets
Now, it is time to make the pins and sockets to connect the hinges to the cube. View the hinges in the image. In order to make each hinge, you will need two identical sketches on different faces. The sketch should always be made on the face where you will extrude the pin from. To make the pin/socket on the right side of the hinge shown in the image, the sketch will need to be created on the face of the hinge. To make the pin/socket on the left side of the hinge shown in the image, the sketch will need to be created on the inside face of the cube. I standardized by making the pin exit the cube on the left and the pin exit the hinge on the right when looking at the front face of the half hinge.
Since the sketches will be placed in a 0.4 mm gap, it can be difficult to be sure you are selecting the correct profiles. You may have to toggle the bodies on and off to make the profiles visible. When it comes time to make an extrusion or a cut, make sure you have the bodies' visibility turned on.
Start by creating the sketch for the pin/socket on the left side of the hinge. Select the inner face of the hinge hole on the cube for your sketch. Create two center-diameter circles with the same center point. One should be 2.6 mm in diameter and one should be 3.0 mm in diameter. The center point should be a distance of 3.5 mm away from each of the edges.
Next, you will need to make the pin/socket on the right side of the hinge. To do this, create a new sketch on the face of the hinge on the opposite side. Use Project/Include to project the center point of the circles from the previous sketch into this sketch. Then, create two identical 2.6 mm and 3.0 mm center-diameter circles using the projected center point.
Repeat this same process to create the pin and socket pair for the other three half hinges.
Extruding Pins/Sockets
After completing all of the sketches, it is time to create bodies from the sketches. First, make the extrude cut. Select the outer 3.0 mm ring profile and the internal 2.6 mm circle profile. Perform a 3 mm extrude cut at a -25 degree taper angle. Make sure you have the body visible so you can successfully perform the cut! You should now have a conical socket.
Once the hole has been cut, you can do the extrusion for the pin. Select the internal 2.6 mm circle profile. Perform a 3 mm extrusion at a -30 degree taper angle. You should now have a conical pin. Your pin and socket should be nested inside each other as shown. Ctrl+select the appropriate faces to see through the bodies and double-check.
Now, repeat the cut and extrude process for the pin/socket that protrudes from the cube body. The complete hinge/cube connections are shown.
Repeat this same process to create the pins and sockets for the other three hinge halves.
Step 5: Mirroring/Duplicating Cubes
Finally, the base two cubes and their associated two half hinges are complete. It is time to mirror and duplicate as needed to create the other 6 cubes.
Start with the cube placed at the origin. Mirror the cube with both of its half hinges. Use the face of the exposed hinge as the mirror plane.
Now, move on to the second cube. Mirror the cube with both of its half hinges. Again, use the face of the exposed hinge as the mirror plane.
Create an offset plane on the inner face of the two middles cubes. Set the offset for the construction plane to be 0.2 mm. Select the pair of cubes along with their four half hinges. Mirror these bodies across the new construction offset plane.
Finally, select the pair of cubes on the end along with their four half hinges. Select Move/Copy. Use "Free Move". Check the "Create a copy" checkbox. Rotate them 180 degrees about the y-axis. Next select "Point-to-Point" on the Move/Copy options. Select a point on the face of the hinge on one of the cubes and the corresponding point on the face of the cube where you want it to go. It should snap into place. You should now have a completed infinity cube!
Step 6: (Optional) Customizing Your Design
If you want to customize your design, you can add patterns or letters to the face of the cubes. To do this, create a sketch on the face. Design the pattern within the sketch as a profile. Once you are finished with the sketch, select the profile and perform an extrude cut into the face to notch out an area.
If you want to work with text, add text within a sketch. Resizing and manipulating text can be a bit difficult in Fusion 360, so it is easiest to work with a single character per text box to correctly arrange them on the cube faces. Make sure you select a good font that will have recognizable profiles to cut into the cube face. Once it is in place, right-click on the text and select "Explode Text". This will convert the text into a series of lines and curves. Once you are done, finish the sketch. You can now select the letters as profiles and perform an extrude cut to "engrave" letters on the face.
Step 7: Printing Your Design
The .STL file was generated with a Z-up configuration. The Fusion 360 The design was optimized to be printed with a 0.2 mm layer height and a 0.4 mm nozzle width.
It was designed to be printed with a 10% infill; however, you can increase the infill as much as you want if you want the cube to have a bit more weight. 10% infill is more than sufficient to withstand regular use and the occasional drop.
On a Makerbot Replicator+ with default settings, it took about ~2.5 hours to print and required ~30 grams of PLA filament (including a raft). A raft is not necessary; however, our printer is older and has poor adhesion so they were printed with a raft.
If using Ultimaker Cura to slice your file, be sure to set "Fill Gaps Between Walls" to "Nowhere" under the Wall settings to prevent the hinges/cubes from welding together.
The interlocking pins and sockets should move freely right off the build plate but it will require some working in to loosen up the joints completely, particularly the two hinges that print vertically.
Step 8: More Projects
For more projects, visit these links:
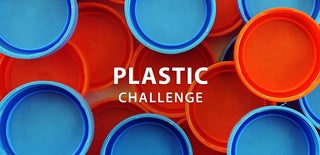
Second Prize in the
Plastic Challenge