Introduction: Jewelry From Scrap and E-Waste
I'm searching for a new style of jewelry to make. My old standby, Steampunk, is now so popular that I can buy pre-made parts that are better and cheaper than anything I can make from scavenged parts. I spend too much time tinkering with electronics, 3d printing, welding and other hobbies to get really good at traditional jewelry techniques. But I like to make jewelry a few times every year. So what to do?
Recently, I've started trying to combine scraps from all my other interests into a single style whenever i feel the need to make my occasional pieces of jewelry. So far, my work looks awkward, not like anything else I see being done, and it doesn't fit into any market at any craft fair. I don't even know what to call it. And I'm okay with that.
When I started doing Steampunk I felt the same way. Who but us weirdos would wear old gears as jewelry? Top hats, spats and gaiters, and even goggles - you people are strange. Well now everyone is doing it, so I, as a creative contrarian, need to find a new challenge.
So I thought I would share just in case anyone else is doing similar experiments. You are not alone.
Step 1: Collecting the Bits and Baubles
Finding interesting shapes and forms to use in jewelry making is easy and fun - especially if you already take stuff apart for other purposes. I take apart almost everything before I send it to the trash and recycling center. Teardowns are always popular events at my local Maker Group. Everyone loves to crack the case on a mystery device and take it apart.
If you've never done it before, just haul out that old VCR from the basement, grab some tools and invite some friends and family over - then start taking it apart. Save anything that looks cool to you. It's really that simple.
I've written Instructables on how to salvage the electronics components and how to reuse existing cases for new projects. But I never thought about using those salvaged parts in jewelry until I started the Glowing Evening Pendant project. I didn't use many scavenged parts in that project, but while I was completing it I kept thinking of all the amazing small parts I had thrown away. Since then, I've been saving the tiny mechanical parts right along with the electronics and motors.
Watch the attached video to see how I approach harvesting interesting parts for a wide variety of project types.
There are lots of great Instructables for salvaging electronics and motors, making CNC machines and a great recent tutorial on making toys from salvaged components.
Good Sources of Parts
- Cameras - lots of small parts and boards in old disposable cameras ($1-5 at thrift stores)
- Printers - A lot a high quality mechanical parts
- Cassette and CD players - Gears and brackets galore
- Motors - take the case off any motor and you will probably find a wonderful part or two
Tools Needed
You'll need a basic set of screw drivers, some pliers and a pair of wire snips. For the tiny parts you may need some jewelers screwdrivers (like in an eyeglass repair kit) Newer items often use specialty screws like star-drive or triangle drives. Since I do a lot of repair work I already have a selection of high quality tools. But you might not need pro quality tools. Luckily, cheap versions of all of these tools can be found for a few dollars per set at the local hardware store. If you're not comfortable using you flatheads as a spudger, you might pick up a set of them.
You'll need some cans and trays to collect the parts in. I find it useful to begin separating and organizing the parts as I go along. If I wait until I have a huge pile it seems tedious to just do the sorting at the end. You, however, might like to do all the teardown at once and then have a sorting party at the end - whatever works for you.
I also like to have some paper towels or rags along with some degreaser on the teardown bench. I try to clean off the worst of the grease and grime as I go. That way the clean parts don't get contaminated.
If you are doing this at the kitchen table you may want a throw cloth to protect your table top. Eye protection is always a good idea. An illuminated magnifying glass can be handy. Some rubber gloves can be useful. I've never had to resort to using one (wink) but a hammer could be useful at times.
Organizing
Salvaging is so much fun that you might wind up with a big box of scrap parts before you realize it. Now the challenge is finding the part you want in that big jumble of stuff. As painful as it sounds, you might need to think about organizing your parts collection.
How exactly you organize it is up to you. I struggle with it constantly. Do I put all the metal parts together? Do I group all the round parts together? Do I organize by size? Or do I organize by intended project type? I don't think there is any one right answer. And there is almost certainly no single way that works for everyone. Organize your collection the way you think about the parts.
Plus, I seldom know exactly which piece I want to use. My projects come together organically. I might have an idea of the final form, but every decision forces me into a new direction. Often, the parts I pull out initially never get used. But I have a vaguely useful sorting system, so I can generally find a part of the right size and material with only a few minutes digging.
Tackle boxes and those wall mounted parts drawers are great for this stuff. But for the majority of your sorting tasks, I do suggest that you use scrap recycled containers. I have bought specialty organizing containers, but I now prefer yogurt and hummus containers, ice cube trays and recycled cardboard boxes. I find these much easier to reconfigure when I re-categorize the parts. Individual bins are easy to bring to the table. And they are cheap, always a plus for crafters and makers.
Step 2: Selecting a Style
For me, a mixture of Art Deco, Craftsman Style and Steampunk all work well for upcycling electro-mechanical e-Waste into jewelry. Cyberpunk and Future-Rave also work, especially for Cosplay, but my local market doesn't support these styles yet, so I stick to the styles with historical references. I also think there's a hidden Egyptian style waiting to be discovered, but I've never done a successful piece in that style.
Art Deco uses strong shapes and bold colors. A motor armature with red wire fits right in. The flutes on a heat sink look natural in this style. The repetitive blocks on a memory stick and the intricate traces on a PCB also fit naturally.
The Craftsman style also accepts the exposed e-waste well. It's somewhat blocky, but with subtle details. I use Craftsman more for home décor items like lamps and decorative boxes, but some of my jewelry has a Craftsman feel.
And then there's Steampunk. Ahh, the forgiving, all inclusive, make it up as you go along Steampunk style. The market has embraced Steampunk wholeheartedly and lucky for us, has primed the minds of jewelry wearers to be accepting of the odd and quirky. People always call my work Steampunk, even when I wasn't trying for that look. If I add a gear or two, maybe a clock face or hands, and finish it off with a wing or a ribbon, well this seems to create the most popular pieces I do. Even if I intended to reference another style, I'm perfectly willing to let it be called Steampunk if it helps other people enjoy my work.
50/50 or Less for Sales Success
This isn't a guarantee, but I've noticed that my market needs at least 50% traditional jewelry materials before they will buy. I've done pieces made from 100% upcycled parts that I thought were quite attractive - and not one of them has ever sold. But when the upcycled items are mixed with identifiable craft-store jewelry items, the same look and feel sells.
In fact, it seems like just a piece or two of e-waste (more like an accent than a focal point) works best for my market. Just enough to catch the eye and set it apart from other Steampunk vendors seems to work best for me.
Masculine and Feminine
(Note: I'm talking about traditional small town, middle aged markets here, not Burning Man or the Bay Area) It can be hard to make e-Waste attractive to a traditional female market. The scavenged parts can be harsh and somewhat brutal in form. The colors don't match any palette that's been seen on the runway or the racks for several decades. But the electro-mech parts aren't as masculine as a rusted bolt, grinning skull or motorcycle sprocket. It doesn't really meet the needs of either market. Again, the answer is to use the salvaged components as accents, not as the entire object. A hint of the electro-mechanical is enough to distinguish my work from other folks'.
Simple versus Complex
I have a bad habit of making every piece into a magnum opus. If I don't use at least 20 parts I feel like I'm cheating. Although these pieces catch people's eye and draw them into the booth, I only wind up selling a few of these elaborate pieces. My best sellers are very often the simplest ones.
Step 3: Clean and Protect the E-Waste
You will often have to clean and protect the e-Waste before you use it in jewelry.
Use goo-be-gone or another degreaser to clean off any oil or grease from mechanical parts. Wipe off as much as you can, then degrease the part, wipe again and repeat until it feels clean. Then use hot soapy water and wipe it down again.
Smooth any sharp edges or corners. PCBs often have sharp corners that you will need to round out. Motor parts might have surprisingly sharp little wires sticking out of them. Real gears can be uncomfortably sharp. A quick hit with some sandpaper or a file is usually enough to take care of these sharp items and prevent them from poking the wearer.
If there are too many sharp points, like in a through-hole PCB with 100s of components sticking out like a vegetable grater- well you may need to find another way to mount that piece. Even the small surface-mount PCBs can become irritating when worn next to the skin. Putting a frame, backer-board or standoffs around it keeps the rough surface away from your skin. But the best solution is to put it behind glass or a thick coat of resin. This completely isolates any sharp areas and keeps you safer.
Step 4: Gluing and Adhering
This isn't "normal" jewelry materials, but many of the traditional assembly techniques still apply. If you've made jewelry before, you probably already know the basic glues and fixings. Cleaning the parts, and scuffing and smoothing the surfaces is just like any other material.
Also check out the Instructables Class on glues for much more detailed info.
E6000 - it rules !!!
Good old E-6000 is still one of the best adhesives for jewelry making. It's very sticky, gives you an extended working time, and it remains flexible after drying. It is my go-to solution for adhering materials, especially if I'm unsure of what else to use.
I especially like it for joining parts with large gaps on the contact surface. The thick gooey glue fills the gaps and helps form a solid bridge between the parts to assure a good bond.
I've used the quick dry formulas, and the "clear" jewelry specific formulations. They work well, but I don't see much advantage over cyanoacrylates or resins, so I still prefer the basic E-6000.
The disadvantages of E-6000 are the smell, the long cure time and the high viscosity.
- Work in a well ventilated room when using E-6000.
- It can take an hour or more before the glue dries enough to hold a heavy part securely in place. There's nothing worse than putting a piece together, then coming back hours later to find that the parts have slipped into new locations and dried there. You may need to prop up, tape-down or clamp the pieces together while the glue dries. Nothing fancy, just a piece of tape or a clothes pin will work fine.
- The glue is super thick, and it can be difficult to accurately apply small amounts. Use a toothpick to apply small dabs of glue to tiny areas. You can cut the corner out of a plastic sandwich baggy and use it like a piping bag for cake frosting. The smaller you make the hole the finer the stream of glue you will get. You can also get long plastic tips, or use the smaller tubes of glue which already come with a finer tip.
Cyanoacrylates (Super/Crazy Glue)
I use these glues mostly for hard or glassy surfaces with of a lot of contact surface. I prefer the gel type because it seems to give me better control. These glues dry very quickly, so you will need to place the parts accurately. Unlike E-6000, you won't get 15 minutes to play around with the final location, it's more like 5-15 seconds before the glue sets.
Resins and Fillers
You can use resins and fillers, ModgePodge, or even nail-polish to adhere parts. I usually reserve these for "embedding" items, but it also secures them in place. I seldom use these as the primary glue, but I often apply them over a previously glued part for an extra level of adhesion.
Putting a thin coat of resin or nail polish on the surface not only protects the piece, it also helps fill tiny gaps and forms a smooth fillet at sharp corners. This helps avoid the piece getting snagged on something and getting pulled off.
Solder
If the parts are metal, you can actually solder them together. Just be sure the adjacent parts can take the heat from the soldering iron. Use the lead free solder. It's often called silver solder or jewelry solder.
Silicone Caulk
Although I've used it on other items, my main use of silicone is to adhere silicone items, like those squishy buttons from remote controls, to another object. The only thing that sticks to silicone is more silicone.
Findings and Mechanical Bindings
Glues and resins are fine. But using the tangs and wings on findings can give you an extra level of security. Go ahead and glue the parts together, then bend the tangs or claws of the finding around the part. If this technique is good enough for gemstones, it's good enough for scavenged electronics and gears.
Step 5: Putting It All Together
Have fun taking apart things and save any part that looks interesting.
When you're ready to begin designing the jewelry you can:
- start with a basic idea and find the appropriate parts to complete it,or...
- find a few parts that seem to go together, or
- start with a single amazing part and just start adding
That's pretty vague, I know. But my jewelry bench is often covered with multiple projects that use a combination of these techniques. Sometimes there's one part that is just so cool that I have to use it. Sometimes I dream up an idea and search for the parts to make it happen. And sometimes, different parts will accidentally wind up next to each other on the bench and that combination sparks an idea.
Working with found material adds a weird set of constraints. You can't just make something the size and color you want. You are forced to find an already existing object that works with three other pre-existing objects. It might sound like this would make it easier, but finding compatible parts from three generations of equipment from three separate manufacturers - well it's more of a treasure hunt than the traditional roles of say a painter or sculptor
I tend to work on jewelry the same way I draw super-hero characters:
Block in the basic body shapes first. A black rectangle (heat sinks) with a red circle (armature) at one end. This gives me an idea of the style I want. From there I can decide that it needs some blue and gold to balance the composition. I go back to the parts bin and find something that fulfills these needs.
For me, abandoning the original purpose of a part is difficult. I still have a need to make the parts look functional. Its silly, but true. I have to work hard to see a salvaged part as merely a compositional element. I know the jewelry won't perform any mechanical operation, but my handyman's mind has a hard time letting go of that idea.
I will often leave the project on the bench and let my preconceptions of the parts dissolve over time while my subconscious mind begins to find historical art references for those parts. Browsing randomly through art books helps with this process. And the more variations I try the easier it is for me to see the parts as just forms and shapes.
After a few rounds of this, I should have a basic assembly that I can work with. At this point, I will probably need to start adding the store-bought jewelry parts. I use the craft-store items to both tie the composition together and hide the rough edges and awkward boundaries between the disparate salvaged parts.
Eventually, I should have a nearly finished piece. However, I will very often need to add just a touch of bling and a spot of color to finish it off. A faux jewel, maybe a dab of paint or even nail polish can tie together an awkward color palette and brighten up a piece that has remained too mechanical looking.
And voile, the piece is done and always, always beautiful.
Just kidding, this technique might sound easy. But the constraints of using found parts almost always causes my work to be "a little out there" for most crafts fairs. I get juried in to most shows, but this technique and look are not for everyone.
But if you are looking for a new style to try, and some odd new challenges, this process can be very rewarding.
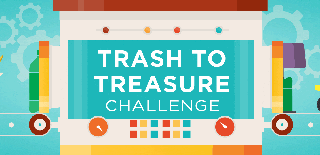
Participated in the
Trash to Treasure