Introduction: Lapidary Butterfly
This project started during a holiday in Idar-Oberstein. This is a place in Germany known for its gemstones. There are also many small factories and atteliers which work with gemstones.
During a visit to one of these factories, where equipment for pharmacies is produced, there was a posibility to search for gemstones. In fact there was a pile of waste, with all kind of gemstones.
The idea was to create a mozaic, as a souvenir. With as result this large butterfly mozaic (44 x 30 inches, 110 x 75 cm).
Different tools are needed for the processing of gemstones. Successively, a saw, a bench grinder and a polishing machine. These machines are designed for processing gemstones, unfortunately they have an associated price tag. That's why I've started to look for alternatives.
In this instructable I describe how to make a mosaic with gemstones. Mainly with the use of power tools, complemented with some home made tools.
Step 1: Trash to Treasure
As mentioned the gemstones for this mosaic were found during a holiday in Idar-Oberstein. These lay on a big pile, together with large agate gems. These stones were not suitable for further processing. But what is waste for this factory, is a beautiful and inexpensive product to create something else.
It soon became clear that several types of waste stones were thrown on this pile. And not just big chunks of agate. But also smaller parts of amethyst, quartz and various other gemstones.
We came to the idea to make a mosaic. And with this in mind, we started collecting colorfull flat pieces of gems. And at the end of the afternoon we were 50 euro poorer, but a bucket full of gems richer. And after sorting the stones, we had the following types of gemstones:
- Red Agate (6.5 - 7)
- Green Agate (6.5 - 7)
- Black Agate (6.5 - 7)
- Quarts (7)
- Rose Quarts (7)
- Aventurine (green) (7)
- Lapis Lazuli (blue, 5 - 6)
- Sodalite (blue, 5.5 - 6)
- Citrine (yellow, 7)
- Citrine (dark, 7)
- Amethyst (purple, 7)
- Amazonite (bright green, 6 - 6.5)
- Red Jasper (6,5 - 7)
- Tiger's Eye (6,5- 7)
The value behind the name is the moh's value of the material. This value is the relative hardness of the gemstone. The higher this value the more time it takes to polish the material. Diamond has the moh's value of 10.
------------------------
Warning:
In this instructable I use power tools, which aren't designed for working with gemstones. Always use appropriate safety equipment. This starts with a good dust cover, goggles and ear protection.
Especially my tool for polishing the gems requires caution. It combines electricity, polishing agent, and water to polish the gemstones. Always remove the plug from the socket before replacing the gemstones. And use a ground fault interrupter for the wiring to your equipment.
Step 2: Required Materials
In addition to the gemstones, the following materials are required:
Wood (4 x 3 feet, 122 x 90 centimeter) . I've used a remainder of 18mm plywood.
Transparent Glue (300 ml tube)
Felt (4mm, local hobbystore)
Carbon Paper (120 x 80 cm)
Geode (for the feelers).
The polishing materials (silicon carbide) has a moh's value of 9 to 9.5. Polishing alumina powder has a moh's value of 9. This is why we can use these materials to polish gemstones.
------------------------
A note on the abrasive materials used in this Instructable:
Don't throw away the water from this project into the sink. The abrasive powder can cause clogging in the pipes. Always filter the water with a very fine cloth or coffee filter. This way you can reuse the water.
Step 3: Butterfly Pattern
After collecting and sorting of the gemstones it was time to decide what to make. The first idea was to decorate a mirror. finally, we have chosen this butterfly. This image does not have too many details, but it has all the characteristics of a butterfly.
Convert this image to a Acrobat/PDF-file. And print out the design as a large poster (3x3 or 4x4 pages).
Draw the outside of the patern on a piece of plywood. Use a jigsaw to cut out the butterfly. And paint the entire butterfly with white primer. This improves the colors of the transparent stones. The outside is painted with brown paint.
Draw the inside of the butterfly using carbon paper.
Fill the pattern with gemstones to determine the desired color pattern. This gives an idea of the required number of stones for every color.
Step 4: Rock Tumbler
For the tumbling of the stones I've bought a Lortone tumbler drum. Not the whole tumbler, but only the necessary drum (about 45 euro). I use an old cordless drill for rotating the drum. Along with a 5 volt power supply from an old external hard drive. Due to the low load, and lower voltage, the motor is not running too hot.
A metal rod (8 mm) in the drill bit serves as a drive shaft. Two additional wheels ensure that the drum is able to rotate. The cordless drill is placed on a shelf, using a clamp. With a second clamp on the power switch.
In addition to the drum, I have used different types of polishing powder and plastic pellets in this step:
- Silicon Carbide abrasive powder K-80
- Silicon Carbide abrasive powder K-220
- Silicon Carbide abrasive powder K-400
- Silicon Carbide abrasive powder K-800
- Alumina Powder
- Polypropylene Plastic Pellets
Fill the drum about half full with gemstones. Add 2 tablespoons of abrasive powder. Cover the stones with water. And close the drum properly. Let the drum rotate for a few hours (4-8 hours).
It is not the intention to get perfectly circular stones. The stones need to be clean. And the real color has to be visible, with some polishing effect.
After this first round, clean the gemstones in a bucket of water (not in the sink). And repeat this process, each time with a finer abrasive powder (K220, K400 and K800). The final step is uses a combination of aluminum oxide and poly props. This step provides the final gloss.
Don't forget to clean the drum between each step. You don't want any coarser abrasive powder inside the drum before proceeding to the next step. So it is better to start with all the rough work. Start tumbling with the coarse powder. This saves time to clean the drum. And it also saves a lot of water, which you can't throw directly into the drain.
Step 5: Slab and Trim Saw
There are two types of saw when working with gems:
- Slab saws are used to make cross section cuts through gemstones.
- Trim saws are used for trimming thin slabs.
We mainly collected small flat gemstones. Most stones we found were already cut with a professional saw. So I did not have to saw many gemstones. But for the few stones I had to saw, I used a standard tile saw. This is equipped with a diamond blade with water cooling. It is much less expensive than a special saw for gemstones.
A tile saw is not the most optimal method for gemstones. It is possible if you move the gemstones very slowly. The downside is that these gemstones, which are processed with a tile saw, require more post processing. Because the slice is less beautiful.
To remove small pieces of (thin) gemstone you can better use a bench grinder.
Step 6: Vibrating Lap
A vibrating lap is used for polishing flat gemstones. Because of the high price of a flat pan, I started by making my own version.
The first version was an old aluminum teflon baking pan mounted on an electrical sander. This gave a vibrating pan. Unfortunately, it didn't polish the stones very well. Also a sander isn't build to move the weight of a pan. I was afraid that it would wear out quickly.
Another method for polishing gemstones is surface grinding on a piece of glass. Just take a piece of glass, polishing agent and some water. Now move the gemstone in a circular way. As a result, the stone will be polished. In order to do this by hand is a lengthy process.
At one point, I started using a sander to move the rocks. This accelerated the process, but it's not really something to do for a long time.
Finally I made a wooden box (second picture). slightly larger than the sander (1/4 inch). In this I place a piece of felt (4 mm thick) with the same size as the box. I placed flat pieces of gemstones (with the same thickness and moh's value) on top of this layer of felt. Next I added water and and a few teaspoons of polish. The last layer is a second piece (wet) felt with the size of the sander.
The sander can move freely within the box. And turning on the machine will polish the stones. This worked surprisingly well. Make sure the felt doesn't dry out. The whole must remain wet. And check the proces each hour.
Working with a vibrating lap uses the same steps as working with a rock tumbler. Use increasingly finer polishing material after each step. You must really clean the box after each step, to prevent polution of the next step. And do not forget to replace the felt.
The combination of electricity (movement), and water (polishing) requires some discipline. Remove the plug out of the socket before checking on the gemstones. And Place all this in a large plastic container.
Please note, this process does take a lot of time.
Step 7: Bench Grinder
Together with the power sander, this machine has been used for most of the time. This grindstone was bought at a local hardware store. These machine are not designed to be used with water. But there is no problem for using this machine with little water. Just make sure that the main (electrical) parts don't get wet.
I started this project with the included grinding stones. This worked for roughly sizing the stones. But I noticed that the grindstone quickly wears out when used with gemstones.
After rough editing of the gemstones, it showed that the gemstones are harder than the grinding wheel. And it became increasingly difficult to get a straight cut. This is why I switched to a diamond grinding stone (about 40 euros, search for "150 mm diamond grinding wheel Ukraine" on Ebay).
The diamond grindstone was almost as expensive as the bench grinder itself. But it works much better than the supplied grindstones. And it shows no visible wear, even after processing all stones for this butterfly.
After sizing the stones, they were polished for a last time. I replaced all felt, and used alumina as a polishing agent.
Step 8: Butterfly Mosaic
After polishing all gemstones, it is time to place them on the wooden frame. First take some pictures, for the exact places of each stone. Clean all stones with detergent and water and let them dry.
I've used the following number of gemstones:
- Red Agate (29)
- Green Agate (37)
- Black Agate (6)
- Amazonite (37)
- Amethyst (48)
- Aventurine (34)
- Citrine (12)
- Dark Citrine (44)
- Lapis Lazuli (42)
- Quarts (8)
- Red Jaspis (10)
- Rhodonite (2)
- Rose Quarts (34)
- Sodalite (25)
- Tiger's Eye (6)
A total of 374 gemstones.
Step 9: Attach the Gemstones
After cleaning and placing the stones is time to glue them.
The wooden surface is painted white, but not sanded. This gives more grip for the glue. Use transparent adhesive and make sure the stones are evenly spaced.
There is some difference in height between the gemstones. Because the different stone slabs are not equal in thickness. This can be solved by adding additional glue. But it is not the intention to obtain a completely flat surface. I have enhanced this effect, and glued the rose quarts with the rough side on the front.
Step 10: Mosaic Grout
When working with grout I used much more water than indicated on the package. Due to the irregular structure of certain gemstones, I didn't want to cover the entire butterfly with grout. It would take a lot of efford to remove all excessive grout afterwards.
I've placed the cement directly between the stones, using a syringe. This can only be done if the grout is almost liquid. Always remove the excess grout with water and a clean cloth.
We also made an example using black grout. In this first sample the grout seeped underneath the transparant gemstones. This can be solved by using more glue underneath these stones. Finally we've choosen white grout. It made the colors more lively.
Step 11: Lapidary Butterfly
Crafting this butterfly with gemstones isn't hard to do. But working with Gemstones takes some dicipline. And mainly, it takes a lot of time.
But I'm very pleased with the final result. And It's definitly a great souvenir of our vacation spent in Idar-Oberstein.
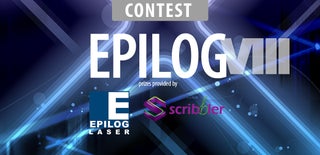
Runner Up in the
Epilog Contest 8
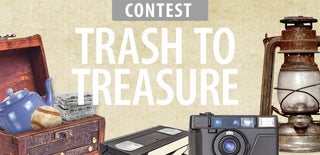
Participated in the
Trash to Treasure Contest 2017