Introduction: Magic Wand That Turns Into Pen
I think like a lot of people once you get exposed to Harry Potter can't wait to get a wand. Last year our family went to Universal Studios Orlando and visited Ollivander's Wand shop and both my kids got to pick a wand. It was a great day, and they were super excited waving the wand around casting spells and pretending to battle one another. However, I noticed that once we returned home the wands went up on a shelf and they hardly touched them. I was hopeful they would play with them a bit more but alas they sat on the shelf gathering dust.
One day while making a pen on my lathe I thought it might be a neat idea to combine the pen and the wand. Naturally I searched online for "wand pen" and found a few results but the majority were plastic, and most were made so that the pen tip just stuck out of the tip of the wand or the bottom of the handle. It was obvious they were wands, this sort of ruins the illusion of the wand. There were some that were nicer plastic versions, but they were not full-sized wands. The bottom line is they all kind of looked cheap and fake. So, I decided to try and make a pen wand/wand pen, out of wood, that concealed the pen in the handle section of the wand and still looked like a wand. The following Instructable describes my process.
Supplies
1 x 1 x 17-1/2 inch piece of Hardwood - Walnut etc.,
Wood Lathe
Pen Jaws
Lathe Tools
Center Finding Jig
Ice Pick or Awl
Table Saw
Pencil
Slimline Pen Kit
Pen Clamp
Thick Leather Scrap Piece 2" x 3"
mm Drill Bit
5/16 Drill Bit
5/16 Brass Tube
Sandpaper (80, 150, 220, 400, 600, 1000, 2000 grits)
Danish Oil
Paper Towels
5-minute Epoxy
Portable Bandsaw Table
Hacksaw
Step 1:
I don't live near a Hardwood dealer so whenever I need a small amount of hardwood, I purchase it from Ebay. I found a seller that offers 20pcs of 1x1x24 inch mixed hardwood for about $31 shipped. That works out to about $1.55 per piece which I think is a good deal. These are off cuts so they are not perfect but considering that they will be turned they have more than enough material for me to use.
The first thing I do is use my center finding jig and an ice pick to mark the center of both ends of the wood. This particular center finding jig I 3d printed from a file I found on Thingiverse. If you do not have a center finding jig you can just use a ruler to mark the diagonal lines.
Step 2:
To save some time I use my table saw tilted to 45 degrees to cut off the 4 corners of my stock. This leaves me with a hexagonal shape that I find easier to turn. It doesn't have to be perfect as long as you knock down the corners.
Step 3:
Next, I chuck the wood stock in between a pair of pen jaws and a live center. I line up the live center point with my center mark on end of the wood. I try to make sure that my stock is even or is as horizontal as possible. After tightening the tail stock, I will turn on the lathe to see if the wood is balanced. If it is wobbling around, I will readjust it in the chuck and recheck. Once I am pleased with the way the wood is spinning, I will make sure everything is snug.
Step 4:
The first thing I do is knock off the sides and round everything over, using my square tipped carbide cutter. The goal here is to get the rough shape of the wand, thick at the handle and then tapered towards the tip.
Since this is a long piece, the wand can have some wobble in the center because it is unsupported. This usually becomes evident by the sound the cutter makes. To stabilize the wood, I use a folded-up cotton towel to loosely hold the piece with my non-tool hand while my tool hand makes the cut. This can be a bit tricky and takes some getting used too; you don't want a long piece of towel that can get caught and wrap around the wood as it turns. The piece of towel I use is about 5 inches long and folded into thirds. Its folded over because it gets quite hot with the friction which, you will feel if you are gripping the wood too tightly. You aren't squeezing the wood with the towel; you are just sort of gently holding it to keep it steady as you run the lathe tool across the wood. I only use the folded-up towel in the center section. The two ends of the wood have enough support from the chuck jaws and the live center that you don't need the to use the towel on either end.
Step 5:
This is the fun part where you can use your imagination. I make a mark with a pencil at about 4 inches from the bottom, this will be the handle section. The handle has to be long enough to accept the pen kit, for the Slimline kit I am using 4 inches will work. Then I make a few marks to indicate where I will be cutting into the wood to get the various contours I am after. I usually don't have a plan for this I just kind of make a few cuts here and there and see what look right. The key here is to make sure you don't remove too much material; the pen kit will be going in to a 5/16-inch hole so the smallest I make the handle is about 5/8 - 3/4 of inch round. This gives you a little wiggle room when drilling the hole. If the walls of the hole are too thing they will break.
As you can see from the pics, I use various carbide cutters to make the different shapes. I also make sure to make a transition from the handle to the shaft section. This is no right or wrong here just make what feels or looks good to you.
Step 6:
After I finish shaping the wand, I sand it on the lathe. I start with 150 grit then 400, 600, 1000, and finally 2000 grit sandpaper. I would usually use 220 and 320 grit after the 150 grit but I didn't have any so I jumped to 400 grit. If you have a shop vacuum use it while you sand this will create a lot of dust and make sure to wear a respirator when sanding.
Step 7:
Once I was happy with the sanding, I apply 3-4 coats of clear Danish oil to the wand. I use a paper towel to buff the wood while it spins on the lathe. You can use a brush to get into any tight areas. I let the dry before proceeding.
Step 8:
Now it's time to separate the shaft of the wand from the supporting wood. I use my diamond shaped carbide tip to carefully cut into the support wood while tapering the tip. The tip will be rough after it separates so I go through my sandpaper grits and smooth it over until it matches the rest of the wand. I apply a few coats of Danish oil to the tip as well.
Step 9:
Next, I use a small hacksaw to cut the wand in two. I make the cut in between the handle and the shaft portion. I used a small hacksaw, but any thin kerf saw will work just try to make the cut is as perpendicular to the wand as possible. To help with this I hold the saw in place and turn the chuck by hand slowly cutting through the wand.
Step 10:
After cutting the wand into two I make sure to sand smooth the cut ends using some sandpaper and flat surface. Here I sand to about 600 grit. The goal here to make sure the sanded edge is perpendicular and squared to the wand body. You don't want to sand in an angle because this is where the wand pieces will join up, if one piece is sanded at an angle you will create a gap at the joint which kind of ruins the effect.
Step 11:
I use a Slimline pen kit for this project which requires a 7mm hole for the pen tube. In order to get a straight hole, I put the handle section back into the pen jaw and attach a drill chuck to the tail stock with a 7mm drill bit. I turn on the lathe and drill a 3-1/4-inch-deep hole. This part can be done without pen jaws but it makes it so much easier and accurate with the pen jaws.
To make this work I have to drill a 5/16 inch wide hole as well. So I swap out the 7mm to a 5/16 drill bit and drill into the handle about 1 inch.
Step 12:
In order to drill the hole in the shaft section you have to insert the shaft into the pen jaws, but you don't want to ruin your finish. To protect the wood, wrap the wand shaft in some thick scrap leather and secure it in the pen jaws. You don't want to over tighten the pen jaws; you just want to make sure you grip it. Also, to make sure the wand shaft is centered make sure to only wrap the leather around one time so that the circumference doesn't change and end up offsetting your wand shaft. You can get a pretty good idea if the wand shaft is centered by sliding the drill bit up to the wood. The tip should meet the wood in the center. If it isn't centered, then readjust the wand shaft in the pen jaws until it is centered to the drill bit. With the same 5/16-inch drill bit drill a 1-1/2-inch-deep hole into the wand shaft. That's pretty much all that is needed to be done on the wand sections. They can be set aside until assembly time.
Step 13:
As I stated earlier, I used a Slimline pen kit for this project. I like it because it has a thin pen tube which makes for a better wand handle proportion. The second pic shows the pieces that come in the kit. The last pic is of the pieces you will not be using.
Step 14:
In order for this to work you have to modify the pen kit. Essentially you have to make it shorter. So, the first thing I did was cut off 7/8" off the end of the pen refill. To do this I removed the black plastic cap which just pulls right off. Then I tried to use a pair of wire cutters to cut it but that didn't work so I used my portable bandsaw table to cut the piece off. you can probably do this with a hacksaw as well. The last pic shows the difference in length between the original and the modified pen refill.
Step 15:
Since we modified the pen refill, we have to also cut one of the pen tubes. I mockup what the assembly will look like and mark the piece where it will be cut. I will need a piece that is about 1-1/4 inch long, again I use my portable bandsaw to make the cut. Here again you could use a hacksaw to make the cut.
Step 16:
I use my homemade pen clamp to attach the pen tube we just cut to the pen tip.
Step 17:
I wanted a brass pen but I didn't have a brass pen kit so I chucked my pen sub assembly in to my drill and sanded off the chrome finish. I stated with 400 grit sandpaper then 600, 1000, and lastly 2000 git. I used the 400 grit to sand off the chrome and copper finish before switching to the higher grits.
Step 18:
Next, I installed the transmission of the pen kit into my subassembly. This may require some adjustments, so I recommend installing the transmission then screw in the pen refill and check the fit. You want to make sure that the pen actually works, and the pen refill protrudes from the tip. If it doesn't then you can push the transmission further into the pen tube until you get a good fit. The total length of my pen from tip to the top of the pen refill ended up being 3-11/16-inches long.
*The 'transmission' of the pen kit is the twist mechanism that makes the pen refill extend or retract by twisting it. The pen refill is screwed into the top of it and if you twist the silver section clockwise it will extend the tip and vice versa to retract the tip.
Step 19:
The pen tube that is attached to the tip needs to be bulked up. To accomplish this, I cut a piece of 5/16" brass tubing to fill out the pen tube which gives it a better feel in the hand. It also adds strength to the pen tube.
Step 20:
First I use some 80 grit sandpaper to rough up the brass tube. Then I mix up some 5-minute epoxy and spread it on the pen tube. Then I slip the 5/16 inch tube over the pen tube and wipe off any excess epoxy. Set it aside to let the epoxy cure.
Step 21:
Since this part of the pen will be exposed, I use some sandpaper and my drill to polish the tube. I start with 400 grit and work my way up to 2000 grit. I mask off the transmission section with blue tape to help prevent scratches. When I chuck the transmission section into my drill I do not make it super tight just tight enough to grip you want to avoid bending or crimping the transmission.
Step 22:
I use my portable bandsaw table to cut off the excess wood from the handle.
Step 23:
I use my drill chuck and a piece of scrap 5/16-inch tube to clean up the end of the wand handle. I just use sandpaper for this, working my way up the grits from 150 to 2000. I finish the piece with Danish oil.
Step 24:
The second brass tube needs to be glued in the handle. This tube will be the part that grips the transmission allowing the pen to function. I first rough up the tube with 80 grit sandpaper and wipe it clean. Then I mix up some 5-minute epoxy and coat the outside of the tube. Next, I insert the brass tube into the wand handle. I use a piece of scrap rod to push the tube all the way into the hole. Make sure it seats in the bottom of the hole. I clean up the area around the hole with a paper towel. I set aside to let the epoxy cure.
If you get some epoxy in the brass tube you can use a 17/64-inch drill bit, by hand, to ream it out. The same applies to the 5/16-inch hole at the top of the handle; if you notice that there is epoxy residue you can use a 5/16-inch drill bit to scrape it out.
Step 25:
Once the epoxy is cured you can assemble the pieces. The pen assembly goes into the handle and then the wand shaft slides over the pen tip like a pen cap would.
Step 26:
This project was trickier than I expected. Both my kids and my wife really liked the final result. My son even said I should send this to the Harry Potter Company because people will be willing to spend a lot of money on these. I thought that was really nice of him to say. I really liked the end result and see myself making more of these in the future to give away to all the Harry Potter fans in know. Thanks for taking the time to read this, I hope you find this Instructable helpful and maybe it even inspires you to make your very own pen wand...wand pen...pen wand? I don't know which should go first the "pen" or the "wand"?
Step 27:
(EDIT: I added this step after I publish the Instructable. I just wanted to show some different variations.)
I made a few more versions of pen wands where the pen kit is installed in the wand shaft section. They are pretty much made in the same fashion as the one in this Instructable but the deeper hole is drilled in the shaft section instead of the handle section. I also experimented with adding wider tubes to the pen bodies, but this results in a fatter wand which I personally don't like especially if this is going to be a gift for a child. Ultimately, I think I prefer installing the pen into the handle section which I feel makes it more usable which is sort of the point to this project.
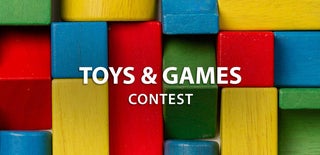
Runner Up in the
Toys and Games Contest