Introduction: Cheap Metal 3D Printed Jewellery
I unfortunately need to start this Instructable by stating that I had intended to write this a while ago when I actually completed the project, and that since then my previous iPhone failed. I didn't think much of it until I went looking for the photos of making the the cuff links to create this Inscrutable, realising that i hadn't managed to upload them to my storage yet. The timing of all this meant I was not going to get a new set of metallic cuff links in time to redo the steps to enter the Metal Contest here, but figured I could still give it my all at making an informative and illustrative Instructable.
Either way, a little while ago one of my mates got accepted as an officer in the navy. As a parting and congratulatory gift, I wanted to buy him a set of shark cuff links. Upon searching the web for hours I was quite disappointed to find there were no good options available, even from site link Ali express and Indiamart.
Determined to get him shark cuff links I put my day job of using Solidworks and a few of my manufacturing connections to 3D print my own. Through this Instructable, I wanted to show just how easy and well valued it is to design, print, and paint your own metallic cuff links or similar jewellery to make a stunning present for friends, family, and loved ones.
Supplies
This is the list of items I used to create the final version of the cuff links;
- A CAD software package - my pick was Solidworks, but things like Fusion 360 is perfect for this
- Sand Paper - 120, 240, and 400 (and possibly 600) grits in roll form work well for this
- Metal Paints - Paint and primer suitable for painting metals with. This should be in aerosole form for the best surface finish.
- An Old Toothbrush - For cleaning your model after sanding
- Mineral Spirits - For removing dirt and grime from your model
- Tack Cloth - For removing dust during painting
- A little knowledge on your local manufacture capabilities
I also used these tools and materials, but they are entirely optional depending on what you have available and how much you want to spend;
- (Optional) Dremel - this really makes things a lot quicker but is completely optional.
- (Optional) A fine file - If you have a fine file lying around this can also help speed up the finishing in hard to reach places.
- (Optional) A 3D printer - Either your own, friends, or some of the methods I discuss later on.
- (Optional) Clear Coat Paint - If you would like to protect your paint job or surface finish from rubbing off, a top coat is always a good idea.
Step 1: Step 1: Design Your Piece
To start I needed a model of a cuff link. Whilst I know how to use CAD, my life like characters could use some improvement, so I headed over to Thingiverse and found a fantastic shark model that I could use. If you don't know what Thingiverse is, its a amazing collection of 3D models from users in generic CAD formats such as .STL which is the most popular file format for 3D printing. For my cuff links I downloaded the available .STL.
Next I had to import the model into Solidworks and design the stem of the link. This took some trial and error of a few different commands but ended up with the final model as shown. A good cuff link or piece of jewellery that is to eventually be 3D printed needs to use as little material as possible while still maintaining strength and printability. By optimising how much material, ie volume, you use, you will reduce the cost significantly. For myself, this was an iterative step between tuning the model and test printing the model as you will see in the next step. The final model I ended up with was 851 cubic millimeters which is pretty small, but sizeable for a cuff link.
Since I know Solidworks is not available to everyone but Fusion 360 is for hobbyists and students I exported my model in .STL and .STEP format so that the file can be imported by anyone wanting to use it. Saving the file as a .STL also allows it to be imported by Cura for 3D splicing my tested 3D prints.
Step 2: Step 2: Prototyping Your Model
This step is optional, but highly recommended - testing your design with a regular 3D printer. Since some of the methods of 3D printing metal are similar to regular FDM printers this step will also let you see where your print might fail as well. Features such as total mass and other fine features can be corrected before the final version.
To do this step its great if you already have your own printer, as you can play with the model to see how easy it is to print and if it will fit what your using it for. However, if you don't, this step is slightly harder but still achievable! I used to use 3DHubs as my go to community based 3D printing service before I bought my CR-10, but they have now changed business model to self supply with what I think is a high minimum order price.
Whilst you can still use them, and I highly recommend their services, Treatstock seems to be the next best thing in community based 3D printing. My little model can be made for as little as AU$3.37 plus shipping right around the corner from me!
Of course if you don't want to pay anything, and you don't have your own printer, you can always ask a friend with one, local school or community, maker space, or even a university. My university had free 3D printing services for Science and Engineering majors if you asked nicely, so its always worth asking the question. In all I had to go through 5 iterations of the model before I found the correct geometry that would fit my shirts.
Step 3: Step 3: 3D Printing From Metal
After you have your model finalised, its time for the fun part! Getting your model printed out of metal is much easier than you think. Contrary to popular thought its not reserved for Formula 1, NASA or any advanced engineering, its just as accessible as regular FDM for all of us makers and hobbyists.
Here in Australia our manufacturing market is starting to slow down, so its getting harder to find the right people for jobs. However I managed to find a local professional SLS nylon and metal printing service through a quick google search and a couple of phone calls to the right people. This is all it takes to find great people and companies that are able to help you make anything. In all I managed to print my cuff links out of stainless steel from my supplier for AU$40 each! That's almost equivalent to regular cuff links from a general clothing store.
Of course if you don't want to, or cannot find anyone local, you can always use the online market. Coming back to Treatstock, there is a manufacturer in china who also prints in marine grade stainless 316. Again for my model, I was able to get mine printed for AU$37.50 plus shipping, amazing!
The last option I want to propose is another one of my favourite online global services; Shapeways. These guys have also shifted their business model over the years, but have always produced a high quality product. They also have a massive range of materials to print from over other services such as silver and aluminium for about the same price. I was able to see my model in stainless steel for only AU$23.94, gold plated brass for AU$46.05, and and silver for AU$62.23!
From this step onward I will have to apologies for my lack of photos of preparing and painting the metallic version. But determined to write a worthwhile Instructable, I printed out another shark, sprayed it shiny like metal, and took some better photos on my shiny new pixel 3 XL. This worked well in the end, as I was able to really demonstrate the benefit of sanding away the rough surface of small models. In the uploaded image you can see how I have tired to replicate what metallic print may look like, illustrating most importantly that the surface finish will not be smooth.
Step 4: Step 4: Polishing Up Your Print
So if you have gone ahead and found a service you like and ordered a print from somewhere, and painstakingly waited for it to arrive, its now time to polish it up so you can paint it the way you would like. When my print arrived, the surface was like sand since the material was of that consistency. Because of this I wanted to try make it as smooth a possible so that it was more aesthetically pleasing and felt better to the touch.
To start I took a fine file to the larger surfaces and tried to get into the smaller cracks with it. This took the bulk of the surface off to a much flatter consistency. To help speed up the process and work down harder areas, I used my Dremel with a grinding bit on a medium speed. I also used my Dremel with a wire brush to really smooth out the corners of the print. If you have a Dremel it will speed this part up but a similar result can be achieved with the sand paper, just with a little more elbow grease.
Next I took varying degrees of sand paper starting at 120 working my way up to to 240 then 400 across all of the surfaces. This is a time consuming process, but the more effort you put in here the better the result is at the end. Remember if you got your print out of stainless or another hard metal, it will take some effort to get the the smooth surface finish that you want. For illustration purposes I sanded one PLA shark down to smooth and one shark unsanded after washing some of the silver paint off. Here you can really see the effect that layers or small imperfections have at this scale.
The surface finish you want for painting your metallic ones though is exposed fresh metal as primer and paint will stick to fresh metal far better than oxidises surfaces. Match this with your desired level of sanding effort and you should have a surface ready for painting!
Step 5: Step 5: Painting Your Print
After some work now you should have a brand new metal 3D printed part that has been sanded ready for painting. Now you have probably heard that painting is all in the prep work, and I can say from my years of holding rattle cans at various projects, the better ones were always where I was more patient and took my time. To paint your model for a long and prosperous life several key steps need to be taken to apply a beautiful and smooth coat. These are; washing, priming, painting, and... more sanding.
Preparation:
To start, always prep the area that you are going to paint in. This area needs to be as dust free as possible, and cover all surfaces you do not want to get paint on. Do not paint within a few meters of anything you don't want paint on, this includes car, houses, valuables, phones.... trust me on this one. The area should also be well ventilated, and you always, always need to wear a mask. Matching projects and lungs is not a good look.
Next, we will want to prep our part. All of the sanding dust and grime will still be on it so we will need to clean it with soap and water, and if you have it some; mineral spirits. Do so by taking your print to a sink, and with a toothbrush scrub the print thoroughly with soapy water. This will remove most of the dirt and grime. For a great clean use mineral spirits as well in this process to get the rest off.
Dry the part thoroughly with a towel and leave it for approximately 5 mins or so to let any remaining water/spirit evaporate. Since these prints are metal as well you can hit it with a hair dryer, heat gun, or even pop into the oven to speed this up.
Priming:
Once dry and cooled, priming can be done to get the surface ready for the top coats. It may be tempting to skip the priming coat, but it is essential for metals as paint does not stick like painting porous wood or plasterboard. Primer is essentially glue in a can, giving something for the top coat to literally stick to as you apply the coat. In the case of aluminium and plastics, this also etches itself into the top layers of the material as well. For my smaller projects I prefer to coat with cans as the surface finish is smooth and even.
To coat it, use very light short burst spanning across the part instead of one very heavy coat. This allows for an even drip free finish, and it drys quicker. Between coats use something like an ice cream container to cover your part. This keeps the dust off of the part until you are ready to coat again. The primer coat applied to the my example prints can be seen in the first image here. The image really does demonstrate how important taking your time with sanding is, showing the left unsanded model and right fully sanded model.
Sanding between Coats:
Once the first coat is touch dry, the most important part, is sanding between coats. Now whilst sanding between coats does sound counter intuitive, it is in not intended to remove paint, only tiny dust particles that stick to the paint while drying. Knocking these particles off with some sand paper makes the part have an incredibly smooth finish. The sand paper I usually use is about 400 to 600 in coarseness, this range is soft enough not to remove paint, but enough to remove the dust. Of course if you sand down too much, its super easy to just add another coat on top. After sanding, remove the created dust using either a tack cloth or moist lint free towel. In total I do 2 to 3 light coats of primer to make sure the whole surface is covered. wait for the last coat to become touch dry before moving on to the top coat.
Top Coating:
Next, we can start applying the top coats. I usually apply about 3 to 4 light top coats to make sure every surface is covered by a thick enough layer to allow for a few light dings and bumps. Applying the top coat is the exact same as the primer coat, spraying light coats across the part, allowing for each coat to touch dry, sanding, and coating again. In the second example photo you can see the unsanded model on the left and the sanded one on the right. Its hard to tell since I chose black as the colour, but the surface finish looks similar to the primer coat where the layers are visible. You can also see some dust built up on the top of the unsanded model as I also did not sand this one between coats even after covering for illustration.
After applying your top coats set the part down to dry for the next 24 hrs. It is worth mentioning that even though the part may be touch dry it usually takes a week to reach the full hardness of the paint I find, so avoid using the part until then.
Step 6: (Optional) Apply a Clear Coat
If you would like, you can apply a top clear coat to offer better protection of your part. Top coats also add a shiny lustre leaving your part looking like a true professional job. Applying a top coat is the exact same as applying the primer and top coats, but is very important that the last coat is covered when drying. I chose not to coat my final product for the simple reason that I could not find a matte finish clear coat I liked. But don't let this put you off as the benefits of top coating are well worth it.
Step 7: Step 7: Gift to Your Friends!
If you managed to successfully follow all the steps in this Instructable you should have an amazing shiny new set of cuff links or jewellery to gift to your chosen recipient! Now all that's left is to wrap it up, or even make your own box like this one. Thanks for following this all the way through. If you managed to make your own, let me know how it turned out. Id love to see what everyone comes up with!
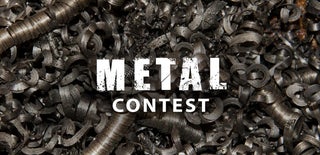
Participated in the
Metal Contest