Introduction: Nesting Chair With Full Size Templates
One of the goals for this project was to use my CNC machine to make this project more accessible to those who do not have a CNC machine. I used my CNC to create full size MDF templates that you can purchase.
For this project I actually made a prototype out of 3/4” birch plywood. 3/4” plywood is plenty strong enough for this project so if you do go the plywood route just know that you can fit 3 complete chairs on a single 4'x8' sheet of plywood. If you go the solid wood route you can get the entire chair out of a single 8-1/2” x 16' board, which that's the size of this 4/4 ash that I'm cutting in this video. Actually, I only used 13 or so feet of it. For a simple common dimension reference, you can get one entire chair out of two 8' 1x10 boards.
Supplies
MDF Template: https://jayscustomcreations.com/product/nesting-chair-full-size-template/
CNC Files to cut your own template: https://jayscustomcreations.com/product/nesting-chair-cnc-files/
3/4" material. Either solid wood or plywood. 3 chairs per sheet of plywood.
1/2" diameter or smaller flush trim router bit: https://amzn.to/2N4TNUt
1/4" radius roundover router bit: https://amzn.to/34DrYbu
Step 1: Breaking Down the Rough Stock
After a rough layout my next step is breaking down this long board into more easily manageable sections at the miter saw station.
Then the boards can be jointed on one wide face. And then planed to final thickness. For these chairs there is no exact thickness you need to get the boards to. I'd say anything between 1/2” and 3/4” is fine. As a matter of fact I think the side pieces were a little thicker than 3/4” just because at that point they were flat and the only benefit of further reducing thickness is to reduce weight.
With the grain on both wide faces exposed I can determine what direction to joint the edges. This is only necessary on the smaller pieces that the slats will be ripped from.
Step 2: The Templates...
I used my CNC machine for 100% of the chair prototype that I made. But I realize not everyone has a CNC machine to use so I wanted to make this project accessible to those who do not. The whole point of making these templates was to make this chair incredibly easy to build for someone who doesn't have a CNC machine. The templates eliminate figuring out the radius for the overall shape, eliminate laying out and locating all of the slats, and provides perfect spacing between all of the slats. To use this template you need a flush trim bit with a 1/2” or less cutting diameter. You also need a 1/4” radius round over bit for the slats.
Step 3: Rough Cut the Side Pieces
Next It was time to rough out the side pieces at the bandsaw getting within a quarter inch or so of the traced template.
Step 4: Template Routing
The templates are attached to the wood with a few pieces of Nitto tape (double sided tape).
And then the routing can begin. I'm using a 1/2" diameter flush trim bit for this process. The bearing on top of the bit rides against the template and the router bit below cuts the wood to the exact size of the template.
With one set done the templates are popped off and applied to the second set and the process is repeated.
Step 5: Making the Slats
Next the slats can be ripped out of the remainder of the stock at the table saw. I ended up having about 40” of extra material after getting the 15 slats that I needed. So I really only needed 13' of that 16' board I started with.
Each slat is 19-1/2" long by 2" wide by 3/4" thick.
Each slat will get a round over on all four long edges that will match up perfectly with the template. With a fence installed at the router table this is a quick and easy process that can be knocked out in just a couple minutes.
Before leaving the router table I used the same roundover bit on all the edges of the seat and back supports, starting and stopping as the bearing hit the slat supports and, of course, not routing the areas where the slats will be.
Step 6: Cut the Slats to Length
The last step before assembly is to cut the slats to their final length. You have a little wiggle room here as the width is really up to you. I cut these at 19-1/2” long, which means the chair will be 19-1/2” wide.
Step 7: Back Assembly
Assembly is incredibly easy due to using the template. I started with the back support clamping the lowest slat in place making sure to have a 1/4” overhang on both sides. Then the second to last slat can be installed by drilling pilot holes to prevent splitting and securing with two screws per side. With the first slat still clamped and this second to last slat secured the assembly becomes rigid. The top slat only has one alignment side so it should not be used to establish rigidity and instead should be installed last.
Then the rest of the slats are added and a straight edge is used to quickly align them with a 1/4” overhang. Rinse and repeat with pilot holes and screws.
Step 8: Seat Assembly
With the assembled back upside down on the table the seat section is assembled in it's nested state. The seat supports slide into the back and are clamped to the back sides with a couple spacers. In my case I used four 1/16” drill bits which will result in 1/8” of wiggle room when nesting the chair. If you don't have four 1/16” drill bits than four evenly sized nails will do the job just fine. Four pencils would even work. Just make sure the seat sides are clamped parallel to the back sides at an even distance from the ends. Make sure the clamps are not so tight that they bow the side pieces.
Then the seat slats are installed the exact same way. Make sure there is the same 1/4” overhang on each side of the back sides, drill pilot holes, and secure with screws.
Finally the last slat is added to both the seat and back assemblies. The outermost screw needs to be installed at an angle to prevent splitting the end of the side pieces.
The very last slat installed is the captured slat in the seat assembly and the whole point of it is to add a little rigidity to the ground side of the seat assembly. The slot is sized for a maximum thickness of 3/4” but the slat should still be installed even if you're using 1/2” thick stock.
One mistake I made here was leaving it long while attaching it. This is the only slat that should be cut so it is flush with the sides. I trimmed mine after installing.
Step 9: Take a Seat :)
That's it! This is one of the quickest and easiest builds I've done in a long, long time. The seat nests inside the back of the back for storage and transport and slides in the front of the back to be used as a seat.
And if you're wondering how much weight it will hold, my friend and I stood on it at the same time and it held all 400 pounds of us without worry.
Step 10: Adding a Protective Finish
The last step is to give it some really good outdoor protection and for that I sprayed a few coats of Halcyon from Total Boat. It's a durable outdoor rated finish that dries really quick and cleans up with water. It also gives a very slight amber tone, so unlike water based polyurethane this really highlights the wood grain, like oil based finishes do. It looks much better than any of the water based finishes I've used in the past which easy to apply but they give the wood a milky, muddy, dull look in comparison.
Step 11: Enjoy!
This chair is done :) Use it and enjoy.
If you're interested in a set of full size MDF templates I have them available for purchase worldwide on my website store. You can also purchase the CNC files to make your own templates like I did.
MDF Template: https://jayscustomcreations.com/product/nesting-c...
CNC Files to cut your own template: https://jayscustomcreations.com/product/nesting-c...
3/4" material. Either solid wood or plywood. 3 chairs per sheet of plywood.
1/2" diameter or smaller flush trim router bit: https://amzn.to/2N4TNUt
1/4" radius roundover router bit: https://amzn.to/34DrYbu
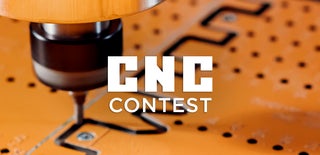
Participated in the
CNC Contest