Introduction: Nordic Dagger - Skyrim: Dragonborn
Keeping in theme with my previous instructable, I also made the Nordic Dagger which is available within the Dragonborn DLC for Skyrim. This was made using very similar techniques and materials as the Mehrunes' Razor build, but some things are different so hopefully this will inspire people to make similar projects of their own.
Materials used include:
PVC Sheeting - I used 3mm thick stuff, it's a rigid sheet similar to styrene sheets or acrylic that can be cut easily with a cheap exact-o or snap blade.
Craft Knife and Wood/Super Glue - Need these to cut out the templates onto the PVC, glue them together and attach everything.
Dowel - I used a 1.25 cm balsa wood dowel from a local craft shop, anything similar will work fine as it will be covered up later.
Sandpaper/Rotary tool - Sandpaper to smooth everything down and the rotary tool to add battle damage before painting the casts.
Clay - I ended up using Monsters Clay to sculpt the curved pommel and cast that separately, but I initially used Apoxie Sculpt on the handle for the hilt and tried to do the pommel as well (didn't work too well for me)
Molding Silicone - I use Pinkysil, an Australian brand very similar to Smooth-On. It's self removing so I didn't need mold release for the casting itself, just while making the mold. Mixes 1:1 by volume and cures bright pink.
Mold Release Agent - Petroleum Jelly works fine, but a spray would be easier.
Casting Resin - I use EasyCast, once again similar to Smooth-On 300. Mixes 1:1 by volume and cures white.
Paints - I used primers, flat black spray paint, and then drybrushed metallic paints.
Faux Leather Strips/Faux Fur - I used 3mm thick fake leather and some fake fur for decorating the handle.
Step 1: Templates and Gluing the Body
Very simple process for this part. Find a decent quality image of your blade, in this case I took the wiki image of the Nordic Dagger, and use an image software to make an outline vector of it to scale. I used CS6, you can use Paint or just the image itself and print it out. Cut it out and trace it onto the PVC sheet, I did 1 tracing for the full size of the blade portion and 2 more which went to the flat edge of the blade and had the middle cut out. These were glued down with wood glue so I could 'wiggle' them into place if they moved (I ruined 2 other attempts due to superglue issues).
As you can see, it has a 'step' which can be filled in with body filler to create a blade edge. You could just layer 3 identical piece on top of each other and dremel them down to shape, but that was a bit annoying with my other project so I tried something different. I also cut out the symbols for the body of the blade in PVC, I'll glue those down once everything is almost done to avoid any dust/particles messing up the gaps.
Step 2: Cleaning Up the Blade
Fairly simple part, grab an auto body filler and mix it with it's catalyst, and then smear the mixture along the edge gap. It cures fairly fast so once it starts getting tacky stop and don't add any more of that batch (it can make a mess and lead to even more sanding). Apply this stuff to each side and while it's still curing you can take a knife and carve excess material away to make sanding easier. Once that fully cures take some sanding paper and start cleaning it up, making that blade nice and smooth and finishing with a coat or two of primer to hide/show any imperfections.
Step 3: Sculpting the Hilt
This was my first time working with Apoxie Sculpt, which is a 2 part self curing modelling compound. It has part A and B, and they mix together in equal amounts to make a clay that cures hard in 2-3 hours and rock hard in 24. I mixed up a tiny bit to start with for the hilt, making sure I was wearing latex free gloves as that stuff as individual parts is bad for your skin (once mixed it seems fine, just wash with soap though). It can be blended and smoothed with water so I played around with is a bit trying to get the shape right.
Step 4: Creating the Pommel and Assembly
I don't have too many photos of the making of this one. I attempted to do the pommel as well with Apoxie Sculpt, but it kept sagging out of shape as I didn't have anything to support the curved shape. I should have cut out a rough shape out of PVC sheeting to act as a 'spine' of sorts. Instead I used Monsters Clay and sculpted the curved pommel from that onto a spare piece of wooden dowel (making sure the handle join was the right size). Covered that in silicone and poured in some EastCast to make a resin copy to carve the symbols into.
I spent a bit of time looking up some reference photos of other replicas, in game screenshots and 'HD' mod photos to design the pommel. I decided on a 'bird head' looking design which got marked with a sharpie. I had a metal clay tool which I used to carve in these lines, a knife or metal pin work work as well or even tracing it into the clay/apoxie before it cures to reduce work. Sanded the whole thing down with some finer sand paper, gave it a coat of primer and attached the blade pieces and pommel to a length of wooden dowel. I had to cut the ends on an angle so the whole thing was straight. At this point you can glue in those symbols from earlier into the blades body and can prepare for the mold making process.
Step 5: Molding and Casting
This part is pretty much the same as most of my other submissions so I won't go into too much detail. You could just take the piece at the moment and skip straight to the finishing steps to have a personal copy, I like resin copys so I do it the expensive way. Surround the props with some clay, making sure it is perpendicular with the edges of the prop and add some walls along the edge. Add in a pour spout with some extra dowel or material (I found out afterwards that having it on the end of the pommel would have worked better for me, but the handle gets covered later anyway), and using something thin add some vents for excess resin to seep out while casting (to avoid air bubbles getting trapped). Poke in some holes in the clay to create some registration keys so the 2 silicone parts fit together and you're ready.
Mix up a small batch of silicone and pour in a detail coat to reduce any bubbles in carved places or the blade symbols. Let that cure and keep adding larger amounts until it is fully covered. Flip the whole thing and carefully remove the clay, then apply some of the release agent to the silicone, as it sticks to itself and we want to avoid that. Repeat the previous steps and you have a 2 part mold.
Take the silicone parts apart, remove the master copy and get your resin ready to pour in. I mixed up a small batch and poured that into the parts of the mold that may catch bubbles if I were to just use the pour spout (the pommel carvings, the blade symbols, and some of the hilt). I did that to both sides, let them cure and then clamped them back together. I took some foamcore sheets and used them to hold the 2 pieces together, but anything flat would work. Mixed up another larger batch of resin and poured that into the pour spout, making sure to tap and move the mold around to dislodge any bubbles. Once that is filled up leave it to cure hard for a couple of hours and remove it from the mold. Now you have a hard resin copy of a Skyrim Dagger. Time to clean and paint it up.
Step 6: Cleaning, Detailing and Painting.
Take your raw resin cast and use a knife to remove any excess resin from the seams. Mine mostly had some excess resin along the blade back and along the pommel. Go over the whole thing with some higher grit sandpaper and clean up any bubbles or bad semas with some body filler, and recarve the details lines if needed on the pommel. Give it a coat of primer and then it's time to give it a battle damaged look, it's meant to be an old used blade from ancient times so lets make it look like one. Mark some lines on the blade, pommel and hilt with a sharpie and using either a cutting disc on a rotary tool or a file, cut some damage into it. Make some of the blades edge chipped, scratch the surface, make it look like it has stopped a blade or 3.
Now I took some help from Punished Props when they did their own painting of a Nordic Dagger Kit, it is a very helpful video and the techniques can be applied on most other projects:
Sand up to around 400/600 grit, another primer coat and spray on a base colour coat. I used black but a dark brown works fine too, just make sure you seal it with a clear coat or lacquer (I used matt spray) to protect the paint. Now to dry brush on some metallic paints, I used some different silvers, bronze, and copper to make it appear a little 2 toned. Take a frayed brush, dip the tip into some paint and wipe most of it off with a paper towel. Lightly brush that over the black to give it a metal-like sheen, swapping paint colours and stroke direction every so often. Eventually you get to a point where the cuts and groves are still black while the rest of the prop looks like an aged metal. Spray that again with some clear coat to protect it and now we can finish off with the handle.
Take some rough sandpaper and scratch up the handle a bit, we need it to be rough so the glue and leather/fur can adhere to the plastic. I super glued a small amount of fake fur to the end of the handle and just below the hilt, wrapping it about 3/4 around it. This is so we can glue the leather strip to the plastic itself to ensure it stays attached. Glue a tiny bit of leather to one end, and carefully wrap it around the entire handle, making it somewhat tight so it doesn't come loose (you can glue parts of the handle to the leather so the whole thing stays down). Finish up at the other end, cut the end of the strip used on an angle so it 'blends' into the end of the handle and you are done!
You could rough up the leather with some sand paper to make it look older, or do a brown paint water wash to 'dirty' up the blade, but there you go. A step by step process on how to make your own dagger.
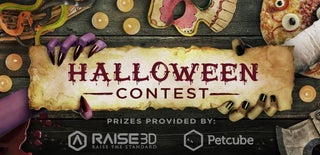
Participated in the
Halloween Contest 2017