Introduction: Save Heat & $'s - Reusable Duct Seals
Half* the world is entering Winter and probably half of that is in a cold climate where heating is required.
Here in Australia it also gets hot in the Summer so Evaporative Air-conditioning is common.
This leads to a problem when your winter heating ends up escaping into the air-conditioning ducts. While modern evaporative coolers have winter shutters to stop the air leaving the roof-top unit, the hot air still enters the ducting, and while it has some insulation, all that heat eventually radiates into your roof space.
With increasing energy costs it pays to save as much of your heated air as you can. This also has the benefit of reducing the carbon footprint. I'm going to enter this in the Green Design Competition, so if you find it instructive, please give me your vote.
Last winter, I tried closing the movable vanes in the vents, but it was obvious that they were still leaking my dollars into the roof. So this year I want to have a real fix. Properly sealed ducts (ducts not ducks, that would be cruel).
I searched Instructables and found iectyx3c's Winter HVAC Hack which used corrugated plastic, draft-sealing strips and Velcro, which gave me some inspiration. I have a 3D printer so I though I could design a clip instead of the Velcro, I had a design tested, but with a central clip it had trouble keeping the edges sealed flat.
So back to the drawing-board... (and no you don't need a 3D printer for this)
[Note: this is for cooling vents (or unused heating vents) and as framistan says below, don't block vents with fans/heat bulbs as they will overheat and cause fires. Also don't block exhaust vents unless you know what you're doing; they probably have a reason for being]
----------------------
* You northerners have a few more months to prepare.
Step 1: Light Bulb!
Then light-bulb moment*, just insert the board under the removable vents.
Bang - sealed!
So this will not work for fixed outlets, like iectyx3c's, but I believe these removable/adjustable vents are commonly used nowadays.
So if that is what you have, read-on...
Terminology: I'm not sure of the correct technical terms, but here I use Outlet to mean the whole thing over the hole in the ceiling, which, in my case, has 4 Vents, which can be removed/adjusted. The vents have vanes to deflect the air.
So, on to what you need...
----------------
* I had another one too; brain hurts. Want a possibly simpler solution, read to the end.
Step 2: What You Need
According to wikipedia "also known under the tradenames of Polyflute, Coroplast, IntePro, Proplex, Correx, Twinplast, Corriflute or Corflute - refers to a wide range of extruded twinwall plastic-sheet products produced from high-impact polypropylene resin with a similar make-up to corrugated fiberboard. It is a light-weight tough material which can easily be cut with a craft knife."
Basically that hollow core plastic that political/ad signs are made from.
While you could use any sheet material to block the vent, I think that corflute (as it is called here) is ideal as it is easy to work with, and with the small air gap may give a little extra insulation.
I'm sure you could find some hanging around somewhere, but I wanted a clean look, so bought it from my local hardware store, I used the 3mm (1/8") thickness. There was also a 5mm (3/16") version, but I think it would be more work cutting it up and it was significantly more expensive.
While it will depend of your outlet/vent size, for me, a sheet of 900 x 600 mm (~3 x 2 ft) was enough for three and a bit outlets. It was also available in 1200 x 900 mm (4 x 3 ft) sheets, I think that would be harder to work with unless you have a larger work space.
2. Step ladder or sturdy chair etc. to access your outlet/vents. Remember balancing sideways on tip-toes will result in a fall. Sex with a broken pelvis is not so good, or so I'm told...
3. One, or more, of your vents
Now is the time to remind you that they come in different sizes, so if you have multiple sizes, get the one from the outlet you want to block, not the easiest to get to; like I did - and ended up with wrong sized cut-outs. Luckily I was going to block off the other vents too...
4. Implements
- A Fine Marking pen, thin lines = accurate cutting
- A box cutter - you could use other cutting implements, up to you
- A steel straight edge - to rule lines, and to run the blade along to get a straight cut. You may get away with a ruler, but in the past I found the cutter digs into the edge of wood/plastic rulers
- Scrap wood sheet or cutting board - to protect your work surface. Unless your surface is already cut up
- Cleaning cloth etc - those vents are filthy. Bonus tip: Top tray of dishwasher - without your dishes ;)
- (Optional) Thin ribbon - like for wrapping presents
- (Optional) Insect Spray/Shoe - I didn't use it, but opening the first vent liberated a large spider 8^| , I showed him how nice the weather was outside...
5. A sturdy flat work surface with elbow room
Step 3: Measure Twice, Cut Once, Repeat...
The insert needs to be slightly smaller than the vent size, so it sits inside the outlet without bowing, which will create a gap.
Either measure the width of the pop-out vent, or use it as a template to mark the width on the corflute.
The outside edge is a U shape, measure from the outside of the U.
The mark will likely not be in the center of a channel of the corflute. If it is, lucky you. If it is past the center, make a new mark in the center. If it is within the first half, mark the center of the next shorter channel, i.e. the width needs to be smaller than the vent. If you end up with an edge flush to the vertical channel it will be difficult to trim later if required.
Using your straight edge draw a line down the middle of the channel, for the length of the sheet.
Measure it again. Put the vent on the sheet again to double check it is a shade smaller. Once you cut it is too late.
So now you have marked a strip along the sheet, slightly thinner than the width of a vent. Time to cut.
You want to use a few lighter passes, use the straight edge, in manageable shorter cuts, moving the sheet and/or scrap/cutting-board underneath as you go. The first cut should be light and just cut through the top surface of the corflute. Make the first cut slow and accurate, it will guide the next cuts. Follow with a firmer cut pressing into the scrap/cutting-board, then a third lighter cut if needed. Remember to make sure your scrap is position properly or you will cut into you work surface, bad if you're using the dinning table...
You may have gone off course here and there, extend the cutter blade and carefully whittle back any grossly protruding bits.
Repeat the above for as many strips as fit on the sheet, depending on how many vents of that size you need. For the 900 x 600 mm sheet I got three usable strips, with a thin strip left over.
Step 4: Measure Twice, Cut Once Again, and Again Repeat. Clear?
Use the vent as a template again. Align it with the end of the strip, mark the other edge top & bottom.
As we want the cut-out to be slightly smaller, move the edge back ~2-3mm (1/8") and using your edge, mark a line.
Cut as before, you may need 3 or 4 light passes, probably safer than using a lot of force.
Place the cut-out over the vent to check the size.
Repeat, but check that the front edge is square and trim square if necessary.
You should now have a number of cut-outs slightly smaller than the vent.
Before you make too many, you probably want to look ahead and do a test fit...this is where I found I had used a different size vent to the one I wanted to fit first, luckily I had only done one strip.
Step 5: Fit, Trim and Repeat...
So get your safety ladder, or as in my case a chair with the yellow pages on top... :| (Don't do as I do)
Take out a vent, clean around the hole, then insert the cut-out*. Make sure any Marker lines are on the top face.
If the cut-out doesn't sit down flat you may need to trim the edge which is catching, but try rotating the cut-out first. Whittling the corflute with an extended cutter blade works well, go slow otherwise you may gouge too much out, or slice your finger off. If you do, keep it in a plastic bag on ice until the ambulance arrives.
Replace the vent on top of the cut-out. It wont sit as firmly as normally, it is really just to store the vent out of sight and weigh it down.
Repeat two times and you are left with the last vent.
So how do you fit the last one?
-------------
*If you're anal, like me, make sure you line up the channel 'grain' in the 4 vent holes. Otherwise do a chequerboard pattern of your choice or go radically random...
Step 6: Wrapping Up
This had me stumped briefly.
Initially, I stored the 4th vent on top of the other vents and just had the cut-out sitting there.
If you find it difficult to get the cut-out into position you can wrap the flat ribbon around it. This gives you a nice handle which allows you to pull the cut-out down, and you can slide the ribbon out. I used this first on a high ceiling as it was difficult to reach up at the right angle.
Alternatively if it doesn't settle when inserted manually, you may need to trim the sides a little (at a time) so it easily falls flat without catching on the sides. I used this method subsequently on easier to reach outlets.
That looked good. Until...
Step 7: The Fix. the End.
...until I opened an inward facing door, to an otherwise sealed room; popping up the last cut-out.
So, I fell back to the ribbon solution, with the vent to hold down the cut-out.
Place the cut-out on top of the vent, wrap with ribbon across both in one direction only. Around the sides without the vane adjustment mechanism makes it easier to remove the ribbon. If you get the vent facing the right way, you won't have to get up/down the ladder two times :|
Use the ribbon it to manoeuvre the pair onto position and pull down to seat both in position. Slightly lifting one side helps remove the ribbon. Lightly tap to get it to settle again. If all else fails, I didn't try this, briefly turn on the aircon.
I then retested opening the door and it all stayed in place.
Done.
The two rooms I have done so far are noticeably warmer and quicker to heat, so I'm looking forward to smaller heating bills this winter.
When spring arrives, remove the cut-outs and store in the back cupboard for reuse next year.
Want a cheaper solution?
Step 8: Cheaper, But Maybe Not As Nice Solution.
I have not full tried this, but as I was writing this Instructable I had another light bulb moment. I'll give it a try on my next vent (which I didn't do as it's in a less used room).
Wrap the vents in cling film/kitchen plastic wrap/Glad Wrap/Saran Wrap. That will be easy for fitting the first three vents. I can see some problems getting the last one on cleanly, but you never know, use a smooth ribbon and it may work.
I don't think it would look as clean (you will want to clean the vents), it may allow more heat conducting through, but you probably have it in your kitchen, and you won't need any tools etc. Unlikely to slice your finger too.
However it won't be reusable, you will be sending grams of plastic to land-fill...
Let me know if you try. Good luck.
And. I also tried cardboard, if you're not to worried with the look, or find a nice white box, it works well. Tho I do like the clean look from the corflute, and it will be a more durable.
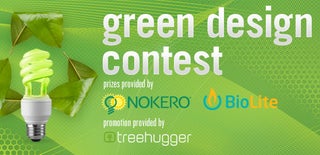
Participated in the
Green Design Contest