Introduction: Silicon Mold to Cast a Pencil Box
The idea was to cast own designs with concrete multiple times with a more durable mold and the same quality of each cast.
For this was the Design made with CAD, for myself I prefer Fusion360, so I will do this example with Fusion, but you can use any CAD program you like.
After this I checked the design and noticed a small mistake (made the bottom of the Box too thin). All in all I made good learning progress and in total I start to like makeing things with concrete.
This was my first ever concrete project and it was not easy to do the right decisions, because I had no experience. Starting with a book and lots of online tutorials I got a feeling for good and bad technics and methods.
With this method you can do concrete objects with cuts that are not possible with just the 3D printed molding form, because silicone is available in different hardness levels and due to its flexibility you can form it during demolding your cast. It is a method for casting concrete objects with one side molds.
Supplies
- two component silicone e.g. Wagnersil
- casting concrete e.g.
- some cups e.g. cleaned yoghurt cups
- some tools for mixing
- water
- scale (simple kitchen scale or post scale)
- 3D printer or someone who can print your object
Step 1: Preparation
Step 2: Designing You Object
You can design whatever you want. My box has a closed bottom and some nice round edges inside. When making a silicone mold, you will notice, that silicone is not that cheap.
After some brainstorming I decided to design my mold the way you see in the pictures. Most common is to build a square box around your object, but this needs a lot of silicone. This way needs a little more printing time, but filament is a lot cheaper. I have a frame, which is around the Box and there is a distance between 7-10mm around the hole object. In the middle is a little cone to fill the big volume inside the box and reduce volume for silicone.
The structure around the object is very important, because there should be no holes instead the top to fill silicone in.
The lid is flexible to make. I print one and did two with a laser cutter, one made out of wood and one of plexiglass.
If you want to build this, I will put files online :)
Step 3: Mixing and Cast Silicone
I am using two component silicone with a working time of 5 minutes. This means I have 5 minutes to mix components together and fill in my mould. After this time the silicone is getting a skin and more and more stiff.
My silicone is Wagnersil 22NF
Why I don't use silicone tube from a hardware store? Because its not recommended and useful for molds. Also there is the possibility that there are acids in (e.g. acetic acid).
Depending on your type of silicone you have to mix the different components together. Take care to wear gloves.
Depending on your size of the molding, try to calculate how much silicone you will need. Silicone is a little heavier than water, but you can weight your mold, fill your mold with water and weight again, the difference is the weight of the water in your mold. For example: your mold weight is 160g. With water in it weights 300g, so you know that there is 140g of water inside. On my silicone is the weight/volume marked, so I could calculate the volume of the mold and than calculate the weight of my silicone.
My silicone has 1:1 mixing, that means I need 100g of component A and 100g of component B. When mixing everything together, I will use the 2 cup method to take care everything is mixed up well.
For the 2 cup method, you need 2 cups and fill in your components in cup 1 and mix it up. Than fill everything from cup 1 into cup 2 and mix up again. This eliminates unmixed silicone at the bottom or the edge of the cup.
You have to look at the time, don't be too slow. When your silicone is not filling your mold, you have to mix up again.
my silicone is finished after half an hour to an hour. After this time I can demould my silicone mold and start with concrete casting :)
Step 4: Mixing and Cast Concrete
When you will cast your concrete, there will be many many different kinds of concrete. Some with big stones, some with small and some really fine concrete mixtures.
Concrete from the hardware store is not so nice, but you can use it anyway. Maybe fine details will not be filled.
For my concrete I need for 1000g concrete 160ml of water. The concrete has a working time of 30 min, so everything is more relaxed as mixing the silicone.
To figure out, how much concrete you will need, you have to try. I figured out, that I need round about 230g of concrete for casting. This means the water I need is 160ml decided by 1000g multiplied by 230g. This gives me 36,8ml of water. For this you can use a scale because 1ml of water is 1g on the scale. But take care, that you tare the weight of your cup.
Take one of your tools and mix the concrete carefully. There should be no bigger things in and no water above the concrete.
Choose one point of your mold and start casting. Fill the form slowly not to enclose large air bubbles. My first cast had a lot of it. When the mold is filled you can vibrate the silicone mold to reduce the air bubbles inside the concrete. You can do this for round about 2-5 minutes, depending on how much air bubbles you want to see. On the surface you will recognize upcoming air.
After 24 hours my cast is ready for demolding. It is easy to take your cast out. But be careful. Lose the silicone on the outside walls all around and than in the inner walls all around. The silicone mold is ready for next cast.
When the cast is fresh demolded, it is a lot darker and is getting more light during the next days.
You can use some concrete finish to seal the surface.
Step 5: Finished Pencil Box
The finished pencil box has already the surface structure of 3D prints, because there was no sanding and no primer before making the mold, but I like this structure. It looks like it is printed with concrete. The silicone duplicates every fine line of the print.
The inner edge is at an angle to push the lid in and open the box easy.
If you want, you can apply some rubber on the bottom, so the box may not slide away on smooth surfaces.
Any questions? Anything I forgot? :)
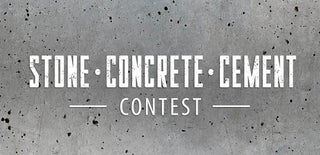
Participated in the
Stone Concrete and Cement Contest