Introduction: Soulmates Lamp
In summer 2016, my son and I made a pair of these lamps, and when we showed them to the uncles, aunts & grandparents they all wanted one. So for Christmas I decided to build a bunch of them.
Everything about this lamp is very simple, except for cutting the 'body' shapes. As an owner of a home-built CNC (Openbuilds OX), I cut them on my CNC.
Now, you may think 'Oh, with a CNC it's all easy' but in fact production on a CNC poses its own problems, and requires you to think well ahead during the design. So in this instructable, I will explain a few of those learnings. For all the ones without CNC, it's maybe a first step to getting started with that. Or you may always turn to traditional tools such as bandsaw and/or jigsaw.
Step 1: Tools & Materials
Each lamp body is made of 2 half parts. An E14 lamp socket is ~27.5 mm diameter. Using 18 mm plywood yields a 36 mm thick lamp, and thus the socket fits inside. Using 15 mm plywood is possible, but you then carefully check your dimensions because you have less margin. E25 lamps are more common, but the socket is thicker and does not fit into 2 * 18 mm.
Regular plywood will result into a darker color. Pictures are made from lamps made with Finnish Spruce, yielding a nice light colored body.
For the end result, the kind of lamp you choose is quite important. Luckily you can choose from a wide range of LED lamps today. At first I used some 2W LED filament lamps, but afterwards I replaced them with a 1W LED lamp from Calex (see photo). 70 lumen is enough for this kind of lamp.
Cost Estimate :
- 18 mm plywood, 600 * 250mm: 5 euro
- power cable : 2 * 4.2 euro
- socket : 2 * 1.6 euro
- led lamp : 2 * 3..10 euro
Total cost for a pair : 25 .. 35 euro
Examples for online sources of these parts :
Step 2: CAD
As you can see from my previous instructables, I designed most of the stuff in Sketchup. But then I met David Truyens and he recommended me to try Autodesk Fusion360. Fusion360 is a really extensive CAD/CAM software, which is normally too expensive for hobbyist, but Autodesk allows you to use it legally, for non-profit purpose : "Free for students, enthusiasts, hobbyists, and startups"
Learning a new CAD software takes time, but fortunately there are quite a lot of good Youtube tutorials. If you follow Lars Christensen (twitter or youtube) you will be up and running in no time. Here is a link to the very starting point.
Now that I've digested (part of) the learning curve, I'm really happy with Fusion360 : The Sky is the Limit. Thanks Autodesk, let me know if I can do something in return :-)
I included the Fusion360 CAD file, so you can look into the design to get all the dimensions.
As I was going to use a 45 mm diameter lamp, I decided to draw the bodies in proportion to that. They end up being 190 mm high and ~100 mm wide. Furthermore I was going to use a 6mm mill to cut the parts out, so I made sure that the gap between legs, arms and other parts is always at least 6mm. I took 8mm
After drawing the outlines of everything, it is easy to extrude into an 18 mm 3D object.
Then you need a few extra steps for the socket pockets and cable groove.. Try it as an exercise and let me know if you're stuck.
Attachments
Step 3: CAM
So in the CAD (Computer Aided Design) part, we designed a 3D object. Now the CAM part (Computer Aided Manufacturing) the design will come to life by 'manufacturing' it from raw materials, aka 'stock'.
In summary we need to:
- cut 2 halves of the body out of a piece of plywood
- cut out some pocket where the socket will go
- cut out a groove for the power cable
- cut out a base, the 'feet' of our lamp. For this part I used 6mm plywood, as this is more in proportion to the body.
In Fusion360, you can simulate the CAM operations, so you can already get an idea what it is going to do. even if you have no CNC, with the file included you can simulate and see for yourself how it will be made.
The first problem is that when cutting the shape out of the stock material, at the end it will be no longer fixed to anything. With a milling cutter turning (up to) 30000 rpm next to it, that is a recipe for disaster. You need to make sure that the part remains fixed. One possible way to do it is to leave some so-called 'tabs' : these are small 'bridges' between the part and the stock material which are skipped in the milling, and they need to be cut manually after the milling job. I decided to have 3 tabs : one at the head and two at the feet. (See image 2 and 3)
Second thing is that my CNC does not allow to cut 18 mm plywood just like that, it is not powerful enough. It is a best practice to cut a maximum depth of half the diameter of the tool. (milling cutter is 6 mm, so recommended maximum step down is 3 mm). I choose a so-called 'step-down' of 2 mm, so the CAM operations will iterate several times around the piece, stepping down 2 mm each turn. (See image 2 and 3)
As a result of the above, you may have a cut which is a little bit jagged. This can be solved by leaving (eg) 0.5mm of stock in the first rough cut, and then do a finishing pass to remove that remaining 0.5mm. As this time the tool only needs to cut 0.5 mm (io of the full 6mm), it is possible to do full depth (18 mm) in 1 pass. (See image 4)
Note that when cutting 18 mm wood, it is not always exactly 18 mm, so you would better cut (eg) 18.5 mm deep, to be sure you completely cut through the stock. But as a result you will be milling in the material under your stock, so you need what they call a waste-board underneath it.
For the base plate, I decided not to work with tabs, but to cut a hole first (position under one foot), which can then be used to fix the material to your CNC with a bolt. Then a second operation will cut the contour. Don't forget to also fix the stock : a flying piece of stock is as dangerous as a flying workpiece! (see image 8 and 9)
Milling the pocket for the socket is a different kind of CAM operation, it is actually a 3D milling, io the more traditional 2.5D milling. I decided to use 2 operations : a first rough cutting (taking away the majority of the material), followed by a 'parallel' which finishes the surface to something more smooth. It would also be possible to rotate the workpiece, aligning the cylinder pocket's axis with the cutter axis, but that's something for future enhancements. (Image 5, 6 and 7)
One last detail : as plywood consists of layers of wood glued together, it's not so easy to get a nice clear cut. In fact the milling bit 'pulls' the chips up, and as such you risk to delaminate the wood. From previous experiments with milling plywood, I've found that a so-call up & down milling bit works best.
Step 4: Assembly and Finish
After cutting the 3 wooden parts, assembly is easy :
- assemble power cable to socket : test carefully that all electrical connections are tight and working, as after gluing you cannot disassemble this anymore.
- I used some TEC7 to glue the socket into the wood
- Use wood-glue to glue both halves together, carefully align, press and let it dry for 2 hours
- Glue the body onto its base plate (foot)
- Finish with sandpaper if needed
- Finish with wood-oil
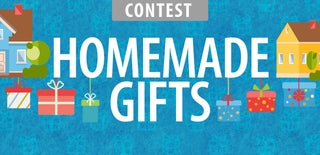
Second Prize in the
Homemade Gifts Contest 2016
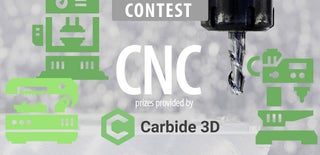
Participated in the
CNC Contest 2016
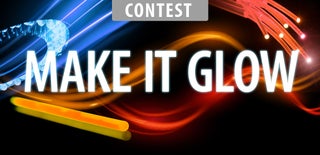
Participated in the
Make it Glow Contest 2016