Introduction: Storage Case From Road Signs
This is a heavy duty storage case I made from recycled aluminum road signs.
Several years ago I acquired a pile of "retired" signs from a city road department. They were removed and replaced due to damage or other reasons, and were destined for a recycling center.
You'd be surprised what you can get if you just ask! An alternate source for similar aluminum scrap is noted in the next step.
This Instructable covers how I made this neat little storage case to hold a cheap RC radio. Thanks for checking it out.
Step 1: Gather Materials
I've made a lot of stuff out of the pile of old signs I got, and these are the leftovers. There's enough to make a few more little things whenever inspiration strikes though.
There are a couple of Habitat for Humanity ReStores near where I live, and occasionally they have old aluminum doors. I recently bought a broken aluminum door for just a few bucks (parts of it in 2nd photo). It requires more work to break down into usable pieces, but the material is great and very useful for all kinds of projects.
So if you can't track down any retired (or "decommissioned") road signs, old metal doors are a great alternate source for used plate aluminum.
Along with aluminum sign scraps, I purchased two 6-foot long pieces of 1/8" thick, 3/4" aluminum angle, a bunch of pop rivets, and an old briefcase that I cannibalized just for the neat handle.
Step 2: Start Cutting
I quite enjoy working with sheet aluminum. You can cut it with a jigsaw with a metal cutting blade, or on a table saw or circular saw equipped with carbide-toothed blades.
It's soft and fairly easy to work with, but the shavings do tend to get all over the place. Fully sealed safety goggles are a must.
The dimensions for this case are roughly 10" by 11" by 6". It has two parts: the bottom is 4 inches deep, and the lid section is 2 inches deep.
Step 3: Pieces Cut
I determined all the sizes needed and cut them out. The flat pieces were all cut out using a table saw. Smaller cross cuts were done using a sled on the table saw.
The aluminum angle pieces were cut to length using a portable metal band saw mounted in a stand with a table.
Step 4: Cut Angles
The aluminum angle pieces all needed 45 degree cuts made on both faces of the piece ends. These were marked with a framing square, and then cut using a metal bandsaw.
Step 5: Assemble With Tape!
The boxes were initially assembled with double-sided clear tape.
This held things in place while I drilled holes and added rivets. It turned out to be a great technique that worked extremely well!
Step 6: Add Rivets
Holes were drilled through the angle pieces and sheet pieces in one shot, with the help of a backing block held firmly behind the drilling locations.
A bit of tap magic cutting fluid was used to help holes get drilled quickly. (See puddle on table. Just dip the drill bit before drilling each hole.)
Rivets were added using a pop riveter. The rivets I used were 3/16" wide with a grip range of 1/4".
Step 7: Add Hinges
I had some old hinges I used for this.
They were first epoxied in place with a bit of 5-minute 2-part epoxy. Once they were locked into position, I drilled the holes and added rivets. This is a great trick to simplify getting hinges and other hardware exactly where you need it.
Step 8: Old Briefcase
So this is kind of funny . . I found this old briefcase at a thrift store for 3 dollars, but it was locked shut. All I wanted it for was the neat leather handle though, so I bought it.
I cut through the locks and opened the briefcase up to find a Mr. Goodbar mini candy bar.
It was nasty.
Step 9: Add Handle
The handle was removed from the briefcase and added to my new aluminum case.
This particular handle had pairs of tabs that get bent over to lock the handle in place. I drilled holes tabs and epoxied the handle in place. When the epoxy was cured, I bent the tabs over on the inside of the case and pounded them down firmly with a hammer.
Step 10: Add Clasps
I added a pair of spring-loaded clasps using the same epoxy-then-drill-then-rivet method described for the hinges. These were take off of some old table at some point. I hold on to every bit of hardware I come across - it's great to hold on to stuff if you'll actually use it someday . . otherwise you're just a hoarder!
Step 11: Reinforce Handle Area
I added a piece of scrap under the handle to reinforce that area, and also to provide a lip to center and support the lid of the case when closed.
This was epoxied in place, with some extra epoxy globbed over the folded-down handle tabs.
Step 12: Lining
For the lining of my case, I used some 2" thick sheets of foam. I'm not sure where it came from originally; it's just more stuff I had lying around.
Since the case halves are 2" and 4" deep respectively, these foam sheets conveniently just needed to be trimmed a little so they'd fit.
The foam was cut to fit the radio using a snap-off-style utility knife, with the blade extended.
Step 13: Add Bumpers
Some clear stick-on bumper pads were added to the "bottoms" of the case - to the bottom when standing upright, and to the other bottom when the case is laid down to open.
Step 14: Done
This was a fun little project and now I've got a rock solid, quirky little case that I'll be proud of for years.
Thanks for reading!
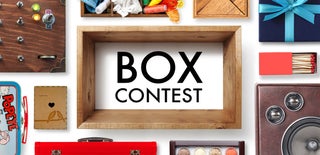
Participated in the
Box Contest 2017