Introduction: The Easy Way to Design Gears in Fusion 360
One of the first things I ever made from a 3D printer was a gear. But it wasn't just any old gear. The beauty behind this gear was that it was a replacement part for the very printer that was making it. This still blows my mind to this day. I love printing gears and still get excited about this new world that 3D printers have opened up. The problem is that designing gears have always been a bit of a challenge for me. That is until I learned what I'm about to teach you.
In the last step I also include a video demonstrating the entire process.
Step 1: Insert From Mcmaster-Carr
There are a few different ways you can go about designing gears in Fusion 360 but the easiest method is to simply import them from the McMaster-Carr catalog. You can do this by choosing Insert - Insert McMaster-Carr Components.
Step 2: Choose Category
This will present you with the McMaster-Carr catalog where you can use the search bar to type whatever it is you are looking for or simply scroll down to choose from the list of categories. In our case we will type "gears" into the search box hit enter. Next, select gears from the images. This will bring up a variety of different types of gears.
Step 3: Filter Search
You can now filter your search by pressure angle, number of teeth, pitch, material, and so on. Go ahead and narrow down the selection by choosing the following from the left column:
Pressure Angle = 14 1/2;
Number of Teeth = 24;
Material = Nylon;
Pitch Diameter = 1"
This should narrow your choices down to only one gear with the product number of 5765K53. Click on this number and then click on Product Detail.
Step 4: Save Gear to Current Design
Scroll down until you see this drop down box. Click on the down arrow and select 3-D Step and click save.
This will bring the 3D model into your current workspace. Notice under the browser on the left hand side that it was brought in as a component.
Step 5: Modify Gear
Wait, you’re not done. This is simply where the fun begins. You can now start modifying the model to make it custom to your design. The beautiful thing with Fusion 360 is that you can simply delete geometry you don’t want by clicking on it and hitting delete. Fusion 360 will delete the part and automatically heal the body. One tip to note is that if there is a fillet or chamfer you’ll want to delete that feature first. For example if a hole has chamfer around it, you will want to delete the chamfer first and then delete the hole.
Step 6: Create Mounting Holes
You can also sketch on top of any surface and begin creating your geometry. In the example above I want my gear to have four mounting holes so I create a sketch on the top face of the gear, draw a circle and create a circular pattern to get four circles. I then can stop the sketch and extrude my holes.
Step 7: Summary
With this method you can bring in any type of gear and then modify it to your own specifications. It sure beats trying to design it from scratch and trying to figure out all the different angles. Let Fusion 360 handle all the difficult parts so you can focus on your design.
Here's a project where I used this exact method to create the gears for this fidget spinner. This design along with six other spinner designs are all covered in the Fusion 360 for 3D Printing - Design Fidget Spinners course.
To see a video tutorial of this entire process visit simply watch the video above or click here.
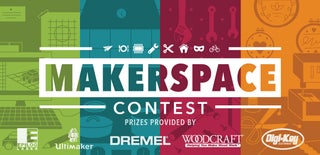
Participated in the
Makerspace Contest 2017