Introduction: The Transistor - Sword Prop
Hello!
Welcome to my first fully-constructed instructable!
This is my entry into the Halloween Props Contest. I built the Transistor Sword, a weapon carried by Red in Transistor by Supergiant Games, the creators of Bastion. This game is one of my favorites, being a pretty small indie game with stunning hand-painted backdrops and concept art, along with good gameplay (though short), and fantastic music. Again, one of my favorite games from every aspect.
I decided to make the sword as it's a beautiful prop, and it's *pretty easy to re-create. Also, being a low-radar game, people would love the sword, but couldn't judge it against the real thing (since they don't even know it exists). I'm pretty proud of it. I recommend NOT doing it the way I did, I just did it this way since I couldn't pass up the material and opportunity.
*I assumed being a semi-cartoon weapon based with no particular scale, or consistent design would be easy. I was wrong.
A couple notes before we start: 1. I'm not finished. I'm too stupid to be done with it. 2. I tried to go through with taking DSLR photos, but it was unappealing to have to put my stuff down to take a photo, or get epoxy/ plastic dust on it. Thus, my phone(s) will have to do. (Note 7 ordeal). 3. I am by no means qualified to make this, I just needed something to do after work.
That being said, a picture is worth a thousand words, so expand the photos! I took a lot.
You can check out my other projects on www.forrest-lucas.com
Step 1: Designing From Scratch
Alright, so this thing is from a video game. Better yet, most of the reference is from concept art. That means most of the details are going to be a little inconsistent, and it has physics (or magic) that don't exist in this world, so there have to be some compromises. Since I didn't have all the money or time in the world, I had to design this thing around the tools and materials I had or could get quickly. I can't really write this like a normal instructable, so this is more of a detailed story on how I built it. Here's what I ended up with.
MATERIALS:
- 1" thick acrylic (yes, 1 inch, scrap)
- 3d printer filament, black and red
- roll of addressable LEDs (reclaimed)
- 3 Arduino-like microcontrollers
- an 18650 battery with step-up/ charging circuit
- wire & solder
- 1/8" aluminum sheet (scrap)
- 1 1/2" aluminum round (scrap)
- 1" aluminum C channel (scrap)
- 1" aluminum bar (scrap)
- 8 flat phillips screws (and nuts)
- 2 5/8" or better bolts (and nuts)
- random bits of hardware here and there (descriptive, right?)
TOOLS:
- 4'x8' 2.5D table mill
- tap and drill set
- hacksaw
- drill press
- belt sander
- lathe
- bandsaw
- lots of sandpaper and horse files
- 3d printer (with a large enough bed)
- de-burr tool
- pliers and other random hand tools
- combo-square, ruler, tape measure
- xacto knives, utility knives
- soldering iron
Step 2: The Blade
-So the entire spark of the project was this 1" thick piece of "scrap" acrylic I found. It was never going to be used, and was starting to get wrecked in the weather. I needed a halloween costume, and the thickness reminded me of the Transistor. I've seen other Transistor props before; they've always been stacked acrylic, a hollow "box" made from acrylic, or vacuum formed plastic. All great options, but it's not what I wanted.
-I hopped onto my good friend Illustrator, and drew over a couple different images, trying to get the most "visually" accurate sword. I used a combo of photoshopped concept art, fan art, and another person's design: Chrix Design. She inspired most of this project, and I give her full credit for the design I basically stole. Sorry! Check out her Transistor, it's way better than mine, and she's pretty awesome (though I've never talked to her).
-When I finally stopped touching the file, I scaled it to the largest size that fits on the almost 4'x8' sheet of weathered acrylic, and produced a vector cut file. I could have made positive circuit pieces that sat on top of the sword, but I wanted to catch the light from the milled/ smoked edge of the acrylic, simplifying some of the pieces. Ultimately, it ended up working worse than I thought, but I'm satisfied.
-After it was all cut, I carved it out (literally), and flipped it over. Using 0.25" metal dowels in the 0.25" flat end mill channel, I re-aligned the sword and cut a mirror of the other side. I ultimately cut two versions, a MDF test cut, and an Acrylic final. Taking them home on the train was hilarious.This meant that I had to mill at three different depths, the light-catching details at 0.125", 0.25" for the "floating" effect, and 1" for the profile cutout. I could only cut 0.25" around the circle, since I was doing it on the other side too, leaving only 0.5" to hold the thing together. This also meant I had to cut the details at 0.125" to prevent it competing with the float cut.
I've added the AI file so you can cut your own, or use it for whatever. Just make sure not to claim it as your own.
Attachments
Step 3: The Eye
I wanted to make the eye as intricate as possible, without casting it. I couldn't think of a good way to create multiple color layers, other than the Z height layering of my 3d printer. I have a Prusa i3 from Josef himself, so it has his multicolor firmware installed, where at a specified layer height, it will stop, move to the edge of the print plate, and eject the current color of fillament.
I designed the eye in Fusion 360, with a random curve I sketched out, guessing the curvature of it. In the game, and most renderings, the eye is a partial sphere. In one rendering I found (the beginning of this instructable), the top of the eye is so clear, you can only see the inner pupil which is concave, and multi-layered. I decided this could allow me to cheat and skip the actual outside of the eye, which I couldn't find a reliable way to get clear. I thought about pouring resin into a partial sphere, but I don't have a de-gasser on hand, and the resin I had would probably need it for a perfect cast.
To get the eye as glossy and acceptable looking as possible, I used Smooth On XTC-3D, a resin/ epoxy built specifically for covering 3d prints. Worked like a charm. It's an easy 2:1 mixture of A to B, so it was a pretty painless process to cover.
I didn't take any photos of it, but the two eyes (each side) are held together with embedded magnets, since the eye's concave part actually protrudes into the hole in the center of the sword.
You can find the .stl and F360 file over here on Thingiverse, so I only have to update in one place.
Step 4: The Frame
So this is where time started to run out. I spent so much time 3d printing, I ran out of time to design and make the frame. What I ended up with wasn't perfect, but it did the job. I used 1/8" aluminum plate, estimated in scale to the sword. It ended up being a 1'x1' aluminum square (since it was the width of the scrap and looked good) that I cut from corner to corner to make two right triangles. I used my band-saw and lubricant, since that was the fastest way, but it meant every screwup in either direction had to be sanded out.
Sanding was easy, I just aligned the two pre-cut edges (the edges that make up the 90 degree) and clamped the pieces together. I used Gaff tape to hold them while I clamped. The Blue Tape helped from scratching the aluminum.
I used some scrap aluminum channel to mount the handle to; this meant the two 1/8" panels sandwiched the 1" thick channel and sword. I wish I had access to a tig, but I ended up putting 4 flat screws into each side, anchoring the panels to the channel. Don't do this, since it was really hard to put the nuts on, with only 1" of clearance for my hand. Since I was doing all this at night, I had to use a hacksaw and coping saw in the separate building away from my house, so away from the band-saw. I should have waited, since I got super shitty results.
I have yet to paint these pieces.
Step 5: The Handle
Ah, the Handle. The largest design flaw in my entire project. I didn't really think of the weight until I cut the sword, meaning I didn't design a proper mounting system before I cut the sword. The acrylic ended up weighing over 50lbs, so now (without cutting the sword again) I couldn't design a good mount for the handle, with not only the weight, but the leverage against it.
I ended up using the C channel to mount the plates to, so I machined a collar on the lathe at home to mount the handle pipe to the channel. I used a scrap piece of aluminum stock and turned it down to fit. Since it's length was cut before I owned it, it turns out it was not enough. I couldn't mill out the entire thing, since I needed to tap the other side (to bolt into the bottom of the channel). This left me with too shallow of a collar, so the leverage popped the pipe out, even with TWO grub screws.
Version 2 featured a longer collar, and tighter tolerance around the handle. I was rushing to make this after work before I left, so I didn't take any photos. Work's lathe is much nicer. Version Two works much better, and it only uses one grub screw and no spacers.
For the actual part you grip, I designed and printed the shape from Fusion 360, but had to split it half, since my printer can only print up to 200mm. Without any prep, I covered it in the same epoxy I used for the eye, but mixed in brass powder, ending up with a ratio of 2:2:1. Mixing the brass powder with A, then adding B when ready. I didn't expect the brass fill to thicken the mixture that much. It was really hard to apply; I ended up not mixing enough and it started to cure while I was still applying, since it took longer to apply in the first place. It turned out alright, and the whole purpose of this cold-cast skin was to give it a metallic sheen. When I started to burnish it however, I was only able to reach the brass on the positive of the 3d print surface, leaving the brass in the negative between bumps untouched. I plan to redo this, but next time sand it first.
You can find the .stl and F360 file over here on Thingiverse, so I only have to update in one place.
Step 6: The Electronics
So just like every other part of this project, I didn't really plan out how the electronics were going to work.I just knew I wanted to light it from the handle, and put the battery inside the handle. I salvaged some half-dead neopixel strip from work and VHB'd it inside the C channel. This kind of LED strip requires three wires; +5v, Signal, and Ground. I was able to hook these straight into the Teensy LC I was using (with it's LED pin), but it's recommended you use a resistor and capacitor to keep everything smooth and consistent. I wasn't too worried about it, since I was only powering 22 LEDs. The Teensy LC runs 5v logic (and the LED strip can be powered anywhere from 5-7), so I planned to use one of those single 18650 battery USB chargers. It already outputs 5v, and I could just plug into the Teensy's USB port. When I measured the pipe I used as a handle, I only measured the outer diameter, and didn't even think about the ID.
Well, it turns out the cells didn't fit without a little modification. I had to take them out of their casing, and tape them together. I wanted to keep the 5v charging system so I didn't have to figure out how to charge those things, but it looked pretty janky in the mean time. Again, this was only a temporary fix for halloween.
After a test light, it looked pretty cool, but I didn't think about the column of darkness behind the eye, as it blocks most of the light coming from the bottom. To solve this, I decided to put more LEDs in the metal contacts that hang off the side of the sword (that I hadn't designed yet; the only benefit to designing one part at a time).
After designing the side contacts from the original AI mockup, I printed them in halves to get them to fit. Each print (two halves) took 34ish hours to print; I had never printed anything that long before. They both turned out fine, and I installed the electronics I designed while it printed. By making two more LED strips, I had to add two more microcontrollers, so I dug up some Adafruit trinkets I got free a while ago.
Since I again, just clicked print instead of fully thinking everything out, I couldn't find a battery I had on hand that would fit inside... except a GoPro Hero 3 battery. It puts out 3.3v, but I tried running the 5v trinket and LED strip off it anyway... It worked. I printed a custom pressure-fit battery holster for the GoPro battery and soldered up some contacts. Pin the whole thing together, and slip it into the clear 3d printed mounts... and bam. Done.
Since I was running out of time, and I hadn't perfected my cold-cast skin technique, I left them black (for now).
Step 7: Putting It All Together
I guess this is a wrap up of a sort. The steps in this instructable were written by sub-project, not in the exact order they were completed, since everything was being done in the middle of the night, at the same time. I should also say that it's not done. There's some finishing on the 3d printed parts to be done, the raw aluminum needs to be finished, and I need to work on the "asap wiring" and "whatever I could find" parts.
I also purchased an EL Panel for my costume part, but I ran out of time doing that too.
Next on the Docket:
- clean up 3d prints
- finish painting/ coating raw aluminum
- replace janky 18650 lipo and GoPro batteries
- Add a microphone so the light is sound reactive to my voice
- Cut and mount EL Panel on jacket
The 18650 can power 22 of those neopixels for at least 8 hours, and the GoPro batteries can power 17leds each for at least 4 hours. When I turn them all on, I have to time it so the glowing animation all start at the same time; each micro-controller has a slightly different boot time. It's funny that I have to count in-between switch flips.
As I mentioned earlier, this thing weighs 50 lbs, so it wasn't fun carrying around, but ultimately worth it. Definitely more of a wall hanger though. It really is too heavy to hold by the proper handle longer than a couple seconds. As I built every part, modifications were made throughout the project, like adding plugs where I needed to detach the handle, sanding and grinding things that didn't fit, lots of 3d print clean up, and more I forgot to document.
Thanks for reading; I wish I had more than a day to put this instructable together, but I guess there's no rest for the wicked. If you have any questions, feel free to ask!
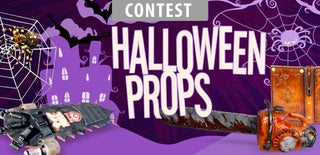
Second Prize in the
Halloween Props Contest 2016