Introduction: Toy Truck Aftermarket Trailer & Hitch
My son loves all things with wheels. After watching Mater in Disney's Cars, he liked the idea of vehicles towing things. He doesn't have any toy cars that tow so, I thought I would make him something. That, along with my longing to make an instructable, brought me to this 'little' project. It's a submission in the Big and Small contest. Check it out here.
The ball hitch was made from the post of a rivet. The trailer hitch was made with a coat hanger and the head of a roofing nail. It includes a magnet so the trailer does not come undone too easily.
Step 1: Drill a Hole for the Hitch
Using my trusting calipers, I measured dead center on the the bumper. Then I marked the bumper with an automatic center punch. The divot left from the punch helps keep the drill bit from wandering. I used a 3/32nd drill bit. It came in a set by Dremel.
Step 2: Machine a Little Ball Hitch
The post of a rivet turned out to be just the right size for the ball hitch. After knocking the post out of the rivet, I chucked it in my lathe. First I made the rough shape with a square file. I refined the shape with a round file. Once I was happy with the shape, I cut it off and turned it around in the chuck. I filed the end down, measuring along the way with my calipers, until it fit in the 3/32nd hole I drilled.
Step 3: Install the Hitch
Now it's time to peen the back side of the ball hitch. First, I polished it up with a buffing wheel.
Normally, I would just place this against my vice and hammer away. The problem is, I didn't want to damage the finish on the ball. I balanced the truck over my doming block with the hitch resting in the appropriate depression. I I couldn't reach the rivet from with a regular hammer so I used a punch to access it. Start by hammering around the edge of the rivet. Then, work your way to the middle as you hammer in a circular motion. I followed up with a ball punch to help round over the edge of the mushroomed metal.
Step 4: Trailer Frame
This truck was destined to be a trailer. I cut it off right at the back of the cab. This revealed the gaps between the plastic undercarriage and the die-cast body. These gaps turned out to be exactly the right fit for the thickness of a coat hanger. I formed the frame by bending the hanger around round nose pliers. Finally, I trimmed it to length with diagonal cutting pliers.
Step 5: Forming the Receiver
My first thought was to cut out a little circle from 22 gauge sheet metal and turn it round on my lathe. This would require me to draw a circle on the sheet of metal, cut it out, hammer it flat, solder it to a nail, and then de-solder it. This got me thinking, "why don't I just cut off the part of the nail that's already a circle?"
I thought it was worth a try. So, I chucked it in, filed it perfectly round and cut it off. I used a doming block and ball punch to progressively turn it into a little half sphere.
Step 6: Solder the Receiver to the Frame.
This was a puzzle to figure out. I needed the little half sphere to sit in just the right spot. As I tried to position it, it kept falling off. I added a supporting piece, using the same wire, to help prop it in place. To prevent the support wire from soldering itself into the project, I heated it red hot and oxidized it. Oxidized metal won't fuse to solder.
I applied soldering paste to both parts. The solder and paste came from the plumbing isle at the hardware store. When I tried to solder this assembly directly on my soldering stone, the half sphere oxidized before the wire got to temperature. I filed off the oxidation and elevated the assembly with tweezers. Take 2. Heating it all from the bottom was the key. This heated up the wire first and allowed the solder to bond with the half sphere.
I used a diamond coated bit to remove the excess solder.
Step 7: Outfit the Trailer Frame
This steps adds a frame guard and magnet. I'm using an old metal forming trick to make it work. If you lay a piece of sheet metal on a piece of wood, you can place wire on top of it and hammer it down. This transfers the shape of wire to the metal.
I use this technique to bend the skirt of the frame guard down. The center of the piece bowed up so I hammered it flat again.
The piece of metal I'm using came from an old Kickstarter project, "NeoWeb". It's a piece of 22 gauge sheet metal, laser cut with rounded corners to 1"x1/2". I cut the piece in half to fit the frame. It not only makes the trailer look "finished" but it was also necessary. It created a surface for the magnet to be epoxied on. The magnet is 1/2" round by 1/16". I wanted to make sure it would not come loose.
Step 8: Finishing Up
The wire had to bent so the trailer would sit level. I did this in my vice with aluminum jaws installed. The softer jaws kept the wire from getting scratched up.
When it came time to solder the guard on, I didn't want to de-solder the receiver during the second soldering process. I used "KOOL JOOL". This is actually for jewelry work. I used it to keep the part I didn't want to melt from heating up. You can see how I coated the frame in the 3rd picture. It worked great.
I used "Water Weld" epoxy to bond the magnet to the frame. Finally I painted it with Rustoleum oil based paint. It matched the existing red perfectly.
With the guard soldered on,the whole assembly pressure fit very tightly into the frame rail.
Step 9: All Done
All the stars aligned for this project. The trailer bed matched the same color blue of the truck. The truck had just the right bumper to be drilled for a hitch. Coat hanger made a perfect fit for the body. The red paint matched great. The magnet was the same width as the frame rail. I'm happy with how it turned out.
Most importantly, my son is happy with his truck and trailer.
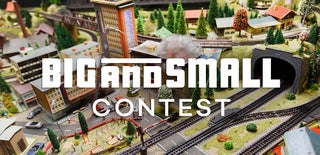
Participated in the
Big and Small Contest