Introduction: Tritium Arc Reactor Pendant Incl VIDEO
Ahoi
Today I show you, how to make a 20 years permanent glow tritium Iron Man Arc Reactor pendant!
Step 1: List of Materials and Tools
The number of cores and also the placing is up to you, I will explain the making process of a
"double triangle core" here...so 6 tritium cores in a triangular arrangement. Mine has a carbon fibre
cover, thats optional as well. And here is what you need:
Tools we need:
- Lathe
- in case you dont own a lathe, a drill press will do as well, or a belt sander
- rotary tool
- screw driver
- metal scissors
- sand paper 400, 600, 800, 1000 plus polishing paste
- metal file (fine)
- divider
- 3 and 5 mm drill bits for metal
- hacksaw
Material:
- 5cm / 2 inch aluminum ring, 3mm wall
- perforated alu sheet 2x2 inches or 5x5 cm
- 2 mm thick (1.5mm minimum) alu sheet
- M5 screw plus nuts
- three 25mm tritium cores and three 10mm tritium cores (color up to you)
- brass U-section 4x2mm (or similar)
- 2 mm copper wire or tubing
- super glue
- 2K Epoxy resin
Step 2: Shaping the Alu Ring:
If you got a lathe, its an easy task. Face cut until its clean, length is not important yet, better too long,
than too short! We turn it down to its final length, when the core is about to go in there.
To make the base-plate fit in there, lathe away 2mm of the inner wall. If you don't own a lathe,
you can still just keep the ring as it is, and glue in the base plate.
Step 3: The Base-plate:
Measure the inside of the space you cut on the lathe, then use the divider to transfer the diameter
onto the 2mm alu sheet.
Use a hacksaw to cut it out, then lathe of file it until it fits in the ring.
Step 4: Putting in a Hole:
The baseplate needs a 5 mm hole right in its center (does not really matter IF its off by 1-2 mm).
I like to pre-drill with 3mm, then finish it with the 5mm drill.
Step 5: Perforated Sheet Metal Inlay
To make it look a bit nicer and more detailed, I inserted a perforated sheet metal circle.
Same drill, you transfer the inner diameter of the ring (the unmachined part), to the metal sheet,
and cut it out. A strong pair of metal scissors will do here. Then file and sand OR lathe, until
it fits in snuggly.
Step 6: The Outer-core Plate:
Now, you need a trigangle, that fits your ring perfectly. Maybe 1-2mm space between its tips and the
inner ring wall. I used a piece of cardboard for the "prototype", and just trial-and-errored it.
Grab your 2mm alu sheet, and transfer the triangle, then cut it out using the metal scissors.
File and sand clean. Add a 5mm center-hole and you are done with this part.
Step 7: Tritium Core Holders:
I used brass U-section bits for that. 4mm wide, 2mm high...lenght around 15mm.
They are about to disappear under the cores anyway.
To make it easier for the glue to grab them, I roughed them up on some sand paper, then glued
them in place. A little chunk of aluminum made sure, they sit right at the edge of the triangle.
A tictac box will do that trick as well...anyting wide enough, with a 90° angle.
Step 8: Inner Tritium Core Holder:
Pretty much the same, but smaller. You need to cut a small triangle, that fits right in the big one!
Plus some 8mm long U-sections (because shorter, right?), also sitting right at the edge aaaand so on.
Sand, glue, bam, done...
Step 9: Optional: Copper Rails
This step is not really needed, I just felt a compelling urge to fill up the space next to the cores,
so I slapped in some bent pipes...2mm wire (alot easier than my tubing!!) or 2mm tubing will look great.
Bend them over a 12mm rod and glue them in place!
Step 10: Glueing in the Cores:
Before you glue it all in, you can now turn or sand down the alu-ring to its final size. In my case, there is only a 1mm layer of resin aka former space on top of the inner cores.
On the pic, you see me glueing in the cores. I started with glueing in the base plate.
I used a short 5mm (5 wide and long) center pin, to make sure everything is centered, that is not really needed though, IF you take your time when finally glueing stuff in there.
If you use super glue, time is a factor, you could also use 5 min epoxy, then you got 4-5 min to set and shift.
Step 11: To Round It Up, Tiny Tritium Cores:
Optional step as well: Tiny 6x2mm tritium cores for the edges. TIDIOUS work, if you mess that up and they
start floating in the resin, you are screwed.
Make sure you epoxy them in there. No superglue!
Looks alot better that way in my opinion. I even added 3 more around the center,
as you can see on the final pic. Hey, its your arc, do that you like!
You also may have noticed the small screw sticking out to the left. Its an M2.5 screw.
Needed to attach something to accept the necklace later.
One of the sides has to be the UP-side, 2mm hole into that, centered, thread-cut,
and in goes the screw. I glued it in place with some superglue...to make sure it can't escape.
Step 12: Building a Wall:
Before we can pour in the resin, we need a wall. I simply used masking tape for that, in combination
with hot-glue to seal off the edges. Works well.
SPOILER: When the resin has cured, and you have to remove this crap again, put it in the freezer
for half an hour, then it comes off all by itself ;)
Step 13: The Resin:
Finally, time for the resin:
I like to have mine on a temperatur of 30°C, that way you dont really need to use vacuum to suck out
all the air in it. The bubbles will just rise and pop.
A dry blower or DISTANT blow-torch will do that trick as well.
The reason, why the wall is so high, is: The higher you pour the resin, the higher the bubbles rise.
A bit of shaking and whacking it onto the table (carefully) will make sure they cant hold to whatever hideout
they are stuck in!
After 24 hours (in my case), you can get back to work on the resin....its fully cured then.
Step 14: Removing the Excess:
If you own a lathe, you are a lucky man, if not, you have to sand it aaaaaaall down (I pity you).
In that case, I would start with 80 grid sandpaper and canceling all appointments for the day.
OR you cut off the biggest part with a hacksaw, up to you : )
Step 15: First Sanding:
First step of the grand finale is here! We start wet-sanding (so get a drop of water or 2) the surface!
I do it in my lathe, you can also do it flat on the table! No problemo. Lathe is just a bit quicker.
Start with 400, then switch to 600, 800, 1000...
Finally finish it off with some car-polish and a clean rag...polish until you get a glass-like finish!
Step 16: The Hanger:
In case you wanna wear it around your neck, you need a hole for the necklace.
I quickly turned a piece of roundbar for that. 10mm diameter, 14mm long. Does not have to be THAT fancy,
its totally up to you. Mine has a 4mm hole to accept any sort of necklace, metal or leather, round of square.
Gets screwed onto the M2.5 screw (after cutting off its head...brutal, I know). I screw it on, THEN mark the
position of the hole, then drill it. To make sure its a perfect 90° angle to the pendant itself!
Step 17: Instructional Video
I hope the tutorial was easy enough....the video helps with more insight and detail!
Shows pretty much everything I have done, to get the result you see up there.
Have fun tinkering!
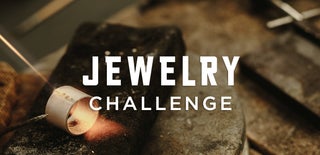
Participated in the
Jewelry Challenge