Introduction: Two Person Cedar Hot Tub From an IBC Tote
I've always wanted a hot tub in our current yard, but most off-the-shelf packages are expensive to buy and costly to run, large, and usually a kind of fugly big chunk of fiberglass. I've always liked the look of a cedar tub, but if you think the fiberglass tubs are expensive, wait till you start pricing cedar tubs. Thus, the goals of this project were to design a hot tub that was:
- Relative inexpensive in materials: I was aiming for $500, and I think all told I was able to hit about $600.
- Inexpensive to run: Most hot tubs are powered by electricity and require a 220v hookup. They can also be insulated poorly and cost significant money to keep heated. I wanted something that was well insulated and fired off propane.
- Compact: I have a small yard in the city and I don't want to dedicate a ton of room to a tub. I've got a roughly 4ft x 4ft space by the back stairs that I could easily dedicate to a tub, and I really only need a 2-person soaking tub.
This project was heavily inspired by this portable hot tub build. I really like the minimal footprint and shape, as well as the propane fired heating system. But I wanted something that was slightly more permanent and had a more finished look to it. Initially, I imagined a design that was an internal wooden tub made out of a thin wood, either tongue-and-groove cedar boards, or marine grade plywood. This would be supported by an internal plywood frame, giving an interior void-space that I could insulate, then faced by cedar that would be non-structural so as to be thin and inexpensive. After some exploration on the woodworking forums I realized that my plans for a wood interior tub was likely a path to madness in chasing leaks and structural failures. Instead, I realized that I could compromise and use a plastic tub for the watertight interior, insulate it, and clad it in cedar and end up with a low maintenance watertight tub with a classy-looking wood exterior.
Enter, the IBC tote.
The IBC, or intermediate bulk container, is a palatalized unit for transport of liquids. Along with the standardized shipping pallet, and the larger shipping container, the standardization of the size and unit of volume in shipping revolutionized transport of goods and was responsible for much of global trade as we know it. The rigid IBC is a container for transport 275 or 330 gallons of liquid, is robust enough to survive global shipping, but is cheap enough to dispose of after use. Perfect for my hot tub build, cheap, strong and lightweight.
Now the only next steps are to source an IBC tank, frame it, insulate it, heat it, and then relax in 275 gallons of hot water.
Supplies
- 330 gallon IBC tank - The two common sizes of IBC tanks are 275 and 330. The footprint of the two is identical, but the 330 is taller (46 vs 53 inches, including the metal pallet base). Because the top corners are rounded, to cut to a vertical sided tub you'll need to remove a significant portion of the top of the plastic bottle. I was concerned that a 275 tank would be too short after I cut the top off so I went with the 330 for $25 more. Seeing it now, a 275 might have been an okay depth so if that's what you can get, don't stress about it. What you should stress about is what was formerly in your IBC, which I'll discuss in the first section below.
- Insulation - To insulate the interior of the space, I primarily used pink fiberglass R-13 15 inch wide x 3.5 inch thick paper faced insulation. However, I also used several cans of spray foam insulation. If I were doing this project again, I'd probably use mostly fiberglass, and only a can or two of the spray foam.
- Framing lumber - I used four 1x6 rough boards for the corners, and framed out using 1x2 and 1x3 strapping lumber. I could have also done all this with 2x4 stock, but this was a pandemic project, and 2x4 prices are just dumb right now.
- Cladding lumber - For the visible exterior of the tub I used 3.5 inch by 1/4 inch tongue and groove cedar. For reasons that I don't really understand 14 sq/ft packs of this were $22, which seems crazy cheap. I used about 6 packs. You can use anything that is priced right for you, and is weather resistant.
- Filter-loop pump - I grabbed a Intex 1000 gal/hour pump filter unit. I was lucky enough to find one off Craigslist for relatively cheap. Depending on whether everyone in the world is building stock tank pools while quarantining at home they can usually be found relatively cheaply.
- Heater - This is where the major influence from Jon-a-tron's portable build came in. A propane tankless hot water heater kicks out significant BTUs relatively cheaply. I picked up the Camplux Pro 1.58 GPM unit because it was a nice balance between good reviews and price. There are cheaper ones, and bigger ones, your mileage may vary. All I know is there's a large disclaimer that using it in a circulating installation like this one voids your warranty, but there are plenty of reviews from people using it heat pools.
- Propane tank - Nothing special here, but you're going to need one
- Heater loop pump - The heater-loop pump doesn't need to have nearly the volume as the filter-loop pump. You just need enough to activate the propane heater, and to carry the hot water into the tub. I used a Grundfos circulation pump that I scavenged from our old home boiler heating system. During a boiler replacement these normally go in the trash, so you might be able to sweet-talk your local plumber into giving you one from a boiler replacement. Alternatively, any of the pumps that Amazon pairs with the Camplux heater would probably work. Just make sure you pair your planned power source with the pump you buy. If this is to be an off-grid solution, get a 12v pump. On-grid, plug-in, find a 120v pump.
- Heater pump controller - Originally I was going to roll my own heater controller, but a thermostatic controller was too cheap and turn-key to pass up. Search for "digital temperature controller", this is the one I found, but there are many like it. One thing to make sure of is that the power supply for the controler matches what the heater loop pump runs off of. If you're going portable and using a 12v pump, there are controllers that are powered off 12v. Otherwise, go for a 120v version. Basically, it's a temperature probe and a microcontroller connected to a set of relays. When the temperature gets below the setpoint, it closes the heater relay.
- Smart plugs - I plugged my filter loop and heating loop into two smart plugs. This allows me to both set a timer to run the filter a couple of times a day, and use my smartphone to activate the heating controller to bring the tub up to temperature. You could accomplish this by plugging and unplugging, but hey, we live in the future, why not enjoy it.
- GFCI outlets and/or cords - Anytime you're dealing with water and electricity you want to get a GCFI outlet involved. If you've bought a standalone pool filter like I linked above, it will likely have the GFCI breaker built into the end of the plug. It's the extra blocky plug that has the test and reset buttons. If you're wiring a plug onto your heater loop controller and pump you need a GFCI somewhere in the process. I managed to cut a cord off an old air conditioner that had a GFCI plug on it. Plus I'm plugging into an outdoor outlet that's a GFCI outlet. If you don't have either, then you can either buy a replacement air conditioner cord with GFCI built in or an inline GFCI pigtail cord. Either is cheaper than ending up dead.
- PVC piping - You'll need a bulkhead fitting for coming out of the IBC ball valve. At that point you can split out into the filter loop and the heater loop. My pool filter connected relatively easily to 1 inch PVC pipe. Grab enough pipe and fittings to transition from the bulkhead fitting through the filter and back into the pool. For the heater loop I ran 3/4 inch. Note that officially, PVC works for the cold side of the loop, but you should use CPVC for hot water applications. Now whether this really matters in this situation where pressure is extremely low, I'm not sure, but the hot water section is only a short loop and it's not that much more to grab the CPVC.
Step 1: Source Your IBC Tote
The first step is to find yourself an IBC tote. The IBC consists of two parts, the metal cage and the plastic bottle. The bottle is a semi-flexible plastic, like a giant milk jug, and relies on the cage for support. The cage provides support to the bottle, attaches to a standard metal pallet on the base, and provides significant strength to the full structure. The bottle is designed to be removed and replaced, and as you shop for totes you'll find some noted as "rebottled" meaning a used cage with a new plastic bottle installed. Other sellers have used IBCs. Make sure you check the former contents because you're likely to get a bonus gallon or two leftover in the bottom.
IBC totes come in two standard sizes, 275 gallon and 330 gallon. Both are the same footprint, but the 330 is taller. For this build you'll want straight walls on the tub, meaning you'll need to cut off the top several inches of the bottle and cage down to where the walls are straight. You could probably make it work with a 275 gallon tank, but a 330 gallon makes a nice deep tub. Using a 330 gallon tank, I ended up with a tub in which I can sit on a milk crate and have the water up to my shoulders.
Used IBC totes are relatively easy to find. I'd start on Craigslist or similar boards where there are usually people that make a side business out of collecting and reselling them. If you're lucky, you might also be able to snag one directly from the source if you find somewhere that's emptying them out. I've gotten empty 55 gallon drums out of car washes, possibly a larger industrial wash might get their soaps in IBCs.
Wherever you get your tote, you do want to make sure that they were formerly used for something relatively non-toxic because you'll have significant dregs and residue in the bottom. I've heard of them being used for something really evil like waste oil or corrosives and I'd avoid those for safety's sake. Mine held an oil-based food-grade lubricant called PAO8 and I ended up with about 2 gallons of it drained out in the end.
Most seem to also include the ball valve and screw cap on the bottom drain. These are helpful when you get to installing the plumbing, so try and make sure you get these with it. If not, Amazon seems to stock fittings designed for the IBC tote fittings.
Step 2: Disassemble Your IBC and Cut Down the Bottle
Mark a cut line on the IBC bottle
Before removing the IBC bottle from the cage, it's helpful to mark where you're going to initially cut the top off. At this point you want to just remove the top of the bottle, but leave plenty of excess bottle above the cut line of the metal cage. I've indicated rough positions in the photo. The green line is where the metal cage will be cut, the red line above it is where to cut the top off the bottle.
Mark all the way around the bottle 4 to 6 inches above the second horizontal metal bar. No need to be super accurate because in a later step you'll trim for accuracy.
Disassemble your IBC tote
Now that you've marked the cut line, you need to remove the bottle from the cage. The bottle and cage are designed to come apart easily so the bottle can be replaced. There are two metal cross bars across the top of the tote that are usually held in by heavy screws. In my case they were torx drive, so you may need a torx driver, or perhaps to just grab them with a pair of pliers. Once these bars are out the bottle should lift out from the cage.
Cut the top off the bottle and clean it
Now that you've got the bottle out of the cage, use a reciprocating saw to cut off and discard the top of the plastic bottle. No need to be super accurate. Your two goals here are to get the top off the bottle so you can clean it out, and to make sure you're cutting 4 to 6 inches higher than you'll ultimately need.
Now that the top is removed, you've got a good look inside the bottle and can remove any residual contents that were left behind. Take careful note of what was previously stored in the bottle and follow any safety and disposal recommendations. In my case, mine contained about 1 gallon of PAO8, an oil-based food-grade lubricant which is listed as non-toxic. After draining as much contents as possible, I scrubbed the inside out with water and dish soap.
Step 3: Insulate the Bottom of the IBC Cage
Flip your IBC cage upside down.
The underside of the IBC cage is designed to fit a pallet jack to move the full tote. This means that it's got lots of airflow and little to no insulation. To minimize heat loss fill this bottom void space with an insulating material.
I started by using spray foam insulation. and the first picture shows the results of one 16-ounce can of Great Stuff Big Gap Filler. With a second can, I was able to fill in the gaps between the rows of foam, giving about a 1-inch layer of foam. I was not entirely happy with this result. My goal was to fill the entire void space under the IBC, but that would take significantly more spray foam, and at about $6 per can, would be more than I wanted to spend on that portion of the project. Instead, to fill the remaining void space I used 3 1/2 inch think pink fiberglass batting insulation. In the second photo is a strip of the fiberglass insulation laid on top of the spray foam.
Initially I was planning on putting the batting in loose as pictured, but I was concerned about water from the ground saturating the batting and reducing it's effectiveness. To mitigate this, I ended up placing the batting inside a black plastic contractor trash bag which I sealed with duct tape before placing it like a pillow on top of the spray foam.
Finally, I closed the bottom of tote with a square of exterior grade plywood cut to just fit inside the metal frame of the bottom of the tote.
Now you can flip the IBC cage right-side up. Ensure you're happy with how the underside is insulated and sealed, because this is effectively the last time you'll have easy access to it.
Step 4: Frame Out the IBC Cage to 3 1/2 Inches
In order to keep your tub nice and toasty but cheap to run, you need some significant insulation space on the walls of the tub. The roll of pink fiberglass insulation I bought was intended for 2x4 walls, so you'll need to frame out from the cage to give yourself 3 1/2 inches of around the outside of the cage. The insulation roll is 15 inches wide, so I framed two horizontal spaces at 15 inches high, with the remainder as a small gap at the top.
Design
You have a bit of liberty in designing the framing shape. I chose to use 45-degree corners with cross members attached to them (top diagram in the blue sketch). In hindsight, it was difficult to get the 45-degree attachments as secure as I wanted, and I ended up using significantly more construction adhesive and pneumatic nails than I usually like to. If I did the process again, I think I'd probably go with something like the 90-degree structure I've illustrated in the bottom diagram.
For height, you'll want the top of the framing to line up with the top of the second to highest horizontal metal bar in the IBC cage (see the final picture of the constructed framing to illustrate this). In the next step you'll cut the cage down to height to match the framing.
Materials
I used 1x6 rough lumber for the corner boards, and 1x3 strapping lumber for the horizontals. I initially tried using math to figure out how wide the corner boards need to be in order to produce a 3 1/2 in interior space, but curved corners of the IBC cage meant math failed me. Instead, I just ended up dry-fitting the assembly in place and marking the width of board that would give me the proper space. then I ripped the corner boards to the proper width on the table saw.
Assembly
To attach the framing to the metal cage I drilled holes through the cage large enough to pass a 3" deck screw through, and drove the screw through from the inside of the cage into the vertical corner pieces. Then once the corners were in place I added the cross members after cutting a 45-degree ends using a miter saw.
In as I mentioned above, the 45-degree design ended up taking a ton of time and hassle to get together. If I'd gone with a more standard 90-degree framing design.
Step 5: Cut Down the IBC Cage and Top Off the Framing
Cut the cage
Now that you've got the basic framing in place, you can remove the excess cage. The top of the wood framing should line up with the top of the metal cross bar where you're going to cut. I cut the vertical bars about 1/2 inch above the top of the framing (illustrated in the second picture). This should hopefully provide a better connection between the metal cage and the wood cap I'm about to attach (details of this will become clear in just a moment). I used a reciprocating Sawzall with a metal blade to make the cuts. This will be loud. I recommend doing it early in the morning to assert dominance in the neighborhood.
Build the wood framing cap
Next construct the final cap structure for the framing. Whereas I used strapping-grade pine for the rest of the framing, this should use a harder wood that can hold a screw well. I used some maple that was part of a futon I pulled off the side of the road. You can feel free to use some other non-futon based wood as long as it's at least 3/4 of an inch thick and can hold a screw well.
The exterior dimensions of the square cap should line up with the outside of the framing. The interior should be about 1/4 inch inside of the interior edge of the metal cage. The third image shows my cap as it's assembled. Note that the 45-degree pieces are just bracing and will need to be removed once the cap is attached.
Attach the cap
Once the cap is constructed, align it temporarily on top of the cut off cage and framing. If you left 1/2 in of bar above the framing, the cap will rest on the cut stubs of the metal cage. Use a sharpie marker to draw a circle around each of the cut ends of the metal bars.
Now remove the cap and turn it upside down. Using a drill bit about 1/4 inch larger than the diameter of the cut off metal bars, drill holes at the sharpie marks where the tops of the cut off bars will fit into the wooden cap. The edges of these holes should be at, or slightly over the interior edge of the wooden cap. Once the holes are drilled, dry fit the cap back on the cage / framing structure. The cut ends of the metal cage should fit completely into the holes and the cap should sit flat on the top of the wooden framing.
Once you're satisfied that the cap fits, remove it again and turn it upside down. Apply a liberal amount of construction adhesive to the underside of the cap, taking specific care to fill the holes you drilled with a sizable dollop of adhesive. Now place the cap back on top of the cage / framing and clamp it down to hold it in place for a couple of hours as the construction adhesive dries. You can also drive some pneumatic nails through, or add some screws to hold the cap to the framing.
Suggested modifications
In hindsight, leaving extra height in the cut-off bars and drilling holes into the cap might have been overkill. I would have been better served by spending my time building a more flat, sturdy and stable cap and just attaching it to the wooden framing. Later you're going to attach the cedar facing to this cap, and it will easier to do if you've got a stable flat surface to attach to.
Step 6: Secure and Trim the IBC Bottle
Replace the bottle in the cage
Take the plastic bottle that you've rough cut the top off of and slide it back into cage that you've now framed out. The bottle should have a drain and valve in the bottom that fits in a cutout in the cage, ensure that these are both on the same side. The bottle will be a slightly tighter fit because the wood cap you added in the previous step has a slightly smaller interior dimension than the cage. However, the bottle is flexible enough that it should slide in relatively easily.
Once the bottle is in place, fill it with about 1 foot of water to add weight and settle it in place as you secure it in the next steps.
Secure the bottle
To hold the edges of the bottle in place, I decided to sandwich it between the interior edge of the wood framing cap and a strip of wood inside the bottle. This is why I suggested the cap use a wood that would hold screws well. The interior strips of wood should use a wood that is both moderately strong, but is somewhat water resistant because it will be exposed to the interior of the tub. I chose a 3/4 x 1-1/2-inch strip of fir lumber.
Because the corners of the bottle are rounded, the interior wood won't be able to extend completely to the edges. Measure and test and fit to get as close as you can. I ended up rounding the edges of my interior boards so they could extend further into the corners (see picture 3).
Before you begin assembly, run a bead of silicone caulk between the outside of the plastic bottle and the wood framing cap. Ideally you'd like to prevent splashed water from running down the outside of the bottle and wetting the insulation that you're going to place in the void space in the framing.
Now line each interior board up as closely as possible with the top edge of the exterior wood cap. This is going to be somewhat tricky because at this point the bottle still extends several inches above the edges of the wood. Sight through the white plastic bottle as best you can and try to line up the top edges of the boards. Possibly shine a flashlight through one side and line up to the shadow of the board on the far side.
When you have each board lined up, drill pilot holes through the interior board, through the plastic bottle and into the wood framing cap. Drive 2-inch exterior decking screws through the pilot holes to sandwich the plastic bottle in between.
Trim the bottle flush
Now that the bottle is secured, trim it flush to the top of the wood framing cap. I used a fine-tooth hacksaw to cut the bottle close to the top of the wood, then removed the final plastic using a small wood plane. Picture 3 shows the final product of the bottle secured in place and trimmed flush.
Step 7: Insulate the Sides
Box in the drain
The first picture shows the lower ball valve and drain fitting for the bottle. When you start plumbing you'll need access to this fitting, and it's useful to have a master drain to close. In order to allow access I added some plywood to the framing around the drain to allow access and keep the insulation away from the valve and plumbing.
Add fiberglass batting to the lower framing
When you're working with the fiberglass batting you should wear gloves, and possibly a dust mask if you're working inside or don't have a stiff cross breeze.
Cut the pink fiberglass batting to length to fit horizontally in the 15-inch spacing in the framing. I cut the batting by laying a scrap 2x4 on top of where I wanted to cut and using either a box cutter, or cheap kitchen knife to saw through. The fiberglass I bought had a paper backing. Place it in the spaces between the framing, fold out the edges of the paper backing and staple it in place. After adding the fiberglass batting, I covered the insulation with a layer of plastic sheeting, also stapled in place. I ended up cutting open contractor size trash bags to get large sheets of plastic, but you could use medium weight plastic drop cloth or regular plastic sheeting. 1/4-inch cedar is going over the insulation, and if water managed to penetrate the cedar I don't want it soaking the insulation.
Insulate inside the top row of framing
I had originally planned to just cut fiberglass batting down to size to fit in the approximately 8-inch space at the top of the framing. At the last minute however, I found a case of spray foam discarded on the side of the road and decided to try that instead. As you can see from the second picture, the spray foam effectively space fills, and expands outward into a gigeresque monstrosity. Once the foam has cured overnight, I came back with a long kitchen carving knife and trimmed the foam flush with the outside edge of the framing. I saved the bulbus orange cutoffs for use terrifying children and passing dogs.
In hindsight, I think the choice of spray foam was not a great decision. In later pictures you can see where the foam pressed against the outside of the translucent tub the orange of the foam clearly shows through to the inside of the tub, and in my opinion looks kind of ugly. If I did this again, I'd go entirely fiberglass for all the insulation.
Step 8: Add a Decorative Top and Cedar Cladding
Build and attach cedar top
At this point the top of the tub should be the wooden cap with the interior boards sandwiching and securing the plastic of the tub. In a previous step you should have trimmed the plastic tub to be flush with the top of the wood.
Next, add a decorative cedar top that looks good and is nice to sit on. I made mine using 2 layers of some leftover 3/4-inch cedar fence boards that I edge-glued up to 7 inches wide. The inside of the decorative top should be flush with the interior boards sandwiching the plastic tub, and the outside should overhang by about 1 to 1-1/2 inches.
Take some time in the construction of this top and make it sturdy because it's going to be exposed to significant splashed water and the elements. The wood on mine is starting to cup significantly and I think I may end up pulling it off and rebuilding. It's possible in the next iteration I may use some exterior grade plywood to add rigidity with the cedar glued to the plywood.
I attached the cedar top with construction adhesive. However, overall I've been disappointed with its performance. I may need to remove it and rebuild using waterproof wood glue and some exterior decking screws, though if I do use the screws I'll need to make some allowance to prevent the screws from pulling through the soft cedar wood.
Clad the sides
I used 1/4 inch tongue-and-groove cedar for the exterior siding. This was surprisingly cheap from The Home Depot (though now that I look again, the price has now gone up). Each pack was 14 sq/ft or 8 3-1/2in x 8ft boards. The cladding should extend from the underside of the overhanging cedar top that you built above, and should leave a 3 to 4 inch gap from the ground for airflow and to prevent the boards from rotting from ground contact. I was able to cut each 8ft board into 2 cladding strips with a minimal, approximately 6in waste piece.
To attach the cladding to the framing of the tub I used 1-1/2 narrow crown pneumatic staples. Nails might work also, but I was worried about the nails pulling through the thin soft cedar, and the cross-bar of the staple provides a much more secure attachment.
Trim the corners
At each corner the 1/4-inch cedar won't line up perfectly and either leaves an overhang or a slight gap. Using a box cutter I trimmed the excess cedar to flush. Then using the 3/4-inch cedar I constructed a 90-degree corner trim that I nailed in place. I also wood glued a horizontal trim board to the underside of the overhanging decorative top. This provides rigidity and cleaned up the look.
Add a finish to the cedar
If you leave the cedar raw and exposed to the elements it will slowly weather to the light gray that you see in the shingles of a Cape Cod beach house. Instead I wanted to retain the warm yellow color of the cedar, so I gave the wood a heavy coat of boiled linseed oil. This penetrates the wood and protects the color, while not sealing it and still allowing moisture to evaporate.
Step 9: Box and Weather Seal the Heater Pump
Now that the main structure of the tub is completed, we can begin work on the heating and circulation systems.
Because the heat loop circulator pump I chose was not rated for outdoor use, I needed to build a weatherproof box to house it in. I ended up laser cutting a box out of 4mm exterior grade plywood. My circulator pump is held in place by two wooden clamps that secure with deck screws and clamp the 3/4 inch pvc that is screwed into the pump fittings. Where the PVC pipe exits the top is sealed with silicone caulk.
I've also included a cutout in the front of the box to hold the heater pump controller, and have wired in my heater pump power cable through the controller and into the pump circuit. A wiring diagram is include here, but basically the controller runs off standard 120v and controls a relay. You bring the same 120v through the relay (make sure you switch the black line wire, not the neutral) and connect to the circulator pump. What's nice about the propane tankless water heater that I'm using for this project is that it switches off water pressure. Whenever the pump starts running, the water heater turns on.
!!! IMPORTANT !!!
Playing with 120 volts and water is a good way to die unpleasantly if you don't know what you're doing. If you're not comfortable and experienced wiring line voltage, there are plenty of circulator pump solutions available that run off 12 volts (this one for example). You can also buy the same heater controller relays in 12v versions, meaning you won't have to play with wiring 120v at all.
Also note, that not visible in this picture is the far end of my cord that has a bulky GFCI breaker on it. When playing with water and 120 volts a GFCI is a must. If your cord doesn't have one, invest in an additional in-line GFCI breaker (yellow device as pictured). From the picture of my wiring you can see that my bare copper ground line is connected to the metal body of the pump, and also snakes through the interior of the box. If I do get significant water infiltration, stray voltage should easily find a path to ground and pop my GFCI breaker before anybody gets too dead.
Alternative pump housings
Depending on the type of pump that you end up using, and whether you want to construct your own weathertight box you may want to go with another housing option. I'd start by looking at the weather-proof cases or an ammo box from harbor freight. Basically anything of sufficient size to house the circulator pump you choose and the heating controller.
Step 10: Connect the Pump to the Propane Heater
I pulled connecting the pump to the heater out into its own step because the equipment you're dealing with might be different than mine, and I have some general suggestions to make.
The heater I'm using is the Camplux 1.58 GPM water heater. They also make a slightly cheaper 1.32 GPM version, however, when I bought the price was similar enough that I wanted to extra BTUs of the 1.58 version. That said, the smaller version should be just fine also. The system has a gas valve that controls the size of the flame. Unless I'm trying to quickly heat the tub, I run it at 1/2 flame or lower, meaning I'm not cranking it up to its full rated BTUs anyway (I suspect it might be more efficient heating more slowly). The water heater takes two D-cell batteries and is triggered by flow. When the circulator pump starts up the water heater uses the batteries to ignite the flame and start heating.
There are other tankless propane water heaters available, some for significantly cheaper than the Camplux. I bought Camplux because the reviews looked good, and some of the reviews on the other units looked a bit not-good. On the other hand, some units are half the cost of the Camplux, so even if you have to throw one away you might still be ahead. In one of the reviews for a cheaper model I read that it didn't include the gas line and regulator, so as you're pricing out make sure that's included.
Big caveat here, the Camplux manual states that using this heater for a recirculating application like this one voids the warranty. This application seems to work just fine, and plenty of reviewers on the Amazon site are using it heat their pools and such. Just know if you have problems with the unit and call up Camplux for a warranty claim, they will laugh and laugh, and call you silly names.
You'll also need the rain cap for the heater that makes it suitable for outdoor installation. Otherwise, you'll need to mount the heater with a cover so it's protected from rain.
The other consideration for the heater is the fittings for the water connections. There are several thread types you're going to encounter when working on random plumbing fittings, especially when you order things from Amazon or Ebay that may be intended for the international market.
- NPT - National Pipe Thread, normally used in the United States. This can also be referred to as FPT, FIP, MPT or MIP. This is a tapered thread, meaning the more you screw two fittings together the tighter the become.
- BPT - British Pipe Thread, used in most non-US countries. Is also referred to as G- thread, i.e. G-1/2 for a 1/2 fitting. Usually a straight thread, with a rubber washer at the end that seals the connection.
- GHT - Garden Hose Thread. Standard US hose connection, straight thread, uses a washer for sealing.
These three threads types are incompatible, so if your heater uses BSP threads, make sure you have the proper adapters to convert to the NPT that you'll find in the US. You won't find these adapters at your local hardware store, so Amazon is probably the best bet. The Camplux heater I ordered uses G-1/2 fittings, but includes the adapters to convert to 3/4 NPT. Other brand heaters may not include these adapters, so make sure you have them.
If you look closely at the photos, you'll see I've used PVC pipe for the water input to the heater, and CPVC for the output. For actual plumbing use, PVC is only rated for cold water and can fail if exposed to higher temperatures, whereas CPVC is rated for hot water use. Now granted, those standards apply to high pressure water systems, buried in drywall, and water temperatures of 130 degrees F or higher. For the hot tub, we're only working with around 1 psi, and water that's around 100 F. CPVC might not be necessary. For my build it was easy enough to use, but you can make your own choices.
Not pictured here, but I also added a basket filter upstream of the water heater. In my plumbing, the heater loop is seperate from the filter loop and I didn't want crud from the bottom of the hot tub being pulled through the heater.
Step 11: Plumb the Filter and Heater Loops
The first step is come out of the ball valve at the bottom of the IBC and connect to PVC. You can buy fittings that are IBC thread to NPT. In my case, my IBC drain had a cap on it, and I chose to drill a hole in the cap and install a 1-inch bulkhead fitting. It's not super robust, but again, we're dealing with a low-pressure system. If I start having problems with leaking I'll upgrade to the fitting I linked above.
From there, transition to PVC and start piecing it together like a giant tinker-toy. Placement and pipe routing is up to you and your artistic sensibilities. I've included a schematic of the loops and the a photo of my plumbing job. I recommend dry fitting all the piping before gluing. Honestly, given the low pressure, you can almost get away with not gluing, though in my case I still had a bit of leakage and ended up PVC cementing everything in place. I also found that the threads going into the mesh strainer were a bit loose and required some pipe dope (or possibly several wraps of teflon tape) to be watertight.
For water return, I decided to route the pipes back up the side, over the top of the tub, and down below the water line. Theoretically I could have drilled through my cedar and insulation and passed the piping through another bulkhead fitting back into the tub. For this build however, I was nervous about punching another hole in the tub and in the the exterior cedar cladding, and so I decided to live with the two pipes coming over the top.
Related to the point above, you'll notice that I didn't join the filter loop and heater loop into a single return. This is because I noticed that bringing them together before the return to the tub would form another possible loop, passing from the filter pump, then backwards through the heater loop, and then back into the filter, bypassing the tub. Additionally, since the propane heater ignites based on an increase in water pressure and flow, I was concerned about introducing any additional water dynamics through that loop that could potentially trigger it when only the filter was running.
Step 12: Add a Power and Controller Box
You'll need a weathertight box to hold plugs and power distribution for the tub. I used a tactical ammo box from Harbor Freight. You know it's high quality because it's tactical.
I passed an extension cord inside with a 3-way splitter plug, and then brought in the chunky GFCI plugs from the filter pump and heater pump controller. I plugged both of these in through two smart plugs. Now I can say "Hey Google, turn on the hot tub" and suddenly I'm living in the future that 1981 was dreaming of.
I also have the filter smart plug on a schedule to run for 30 minutes twice a day.
The ammo box comes with a rubber gasket around the top. Cut a slot in the side so the plugs can enter and the cord can slide down, allowing the top to still latch.
Step 13: Add a Cover
The final step to the build is adding a cover to the tub. This serves both as an additional insulation for the top, and to prevent leaves, sticks, and squirrels from falling in. Currently I'm using a couple of sheets of reflective bubble insulation floating on top of the water, along with a sheet of 1/8th inch plywood on top of the tub.
In the future, I plan to construct a more custom cover that fits more tightly and contains a thicker layer of insulation, however, I'm still working out the design. Until that point, the silver insulation seems to work relatively well to hold in heat. If I heat the tub to 98 or so degrees in the evening, it's still at around 93 or 94 by the next day. However, as we get out of summer and the temperature starts dropping overnight I may have more of a need for a good insulating cover.
Step 14: Final Thoughts
Water displacement
One aspect of this design is that the ratio between the people in the tub to the overall size of the tub is relatively low. With one or two people in the tub, the water level rises significantly. To account for this, you have to keep the water level a good 5 to 6 inches below the top of the plastic tub so it doesn't overflow when people get in. If you wanted to squeeze a third or even fourth person in, well, that would probably be more human than water at that point, so maybe stick to two.
Along with this, one of my concerns with this build is that if the water level exceeds the top of the plastic tub, it might overflow back into the wood framing and soak the insulation. A possible upgrade might be to add an exterior overflow so if the level got too high water could escape outside of the tub instead of overtopping the interior plastic tub.
Seating
Right now I'm still solving the question of seating inside the tub. Currently I'm using milk crates as seating, and they raise you just high enough to keep your head above water, but your shoulders submerged. Ultimately I may build some classier seating using some of my scrap cedar. In order to weight it down, I may integrate internal boxes that I can fill with river stones, or alternatively use suction cups on the underside of the benches.
Winterization
One downside to this build is that this is only a 3-season tub. Much of the plumbing is exposed and uninsulated. If the system were exposed to temperatures below freezing for very long, the pipes in the propane heater and filter would freeze and probably split. As such, in late fall the tub and plumbing system should be drained in preparation for winter.
I could imagine a future design that boxed the plumbing and heater inside an insulated space that was exposed to the plastic IBC bottle, allowing the thermal mass of the water to keep the piping warm. However, this design would require a lot of forethought about how the plumbing was going to be run, and how the venting of the exhaust from the propane heater would work.
Portable build?
When full, this tub is too heavy to be moved, but empty it could feasibly be mounted on a medium duty trailer. Because you're heating with propane, the power requirements for the system are relatively minimal, only running a pump or two. If you were committed to filling and emptying relatively soon you could probably even omit the filter pump. At that point, your heater loop pump could probably run off a car inverter, a small generator, or even switch over to using a 12v pump.
With an additional $500 for a medium duty Harbor Freight trailer you could pretty easily have a build that could tow to a location, fill and heat over the course of 3 or 4 hours, and then enjoy for a weekend before emptying it and trailering it home.
Final thoughts
Overall I'm very happy with the way this project has turned out. For well under $1000 I have a nice looking hot tub that fits neatly into my backyard space. It heats relatively cheaply, and with the addition of a good lid should hold temperature well into the fall.
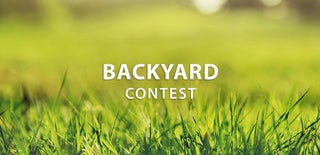
Judges Prize in the
Backyard Contest