Introduction: Wooden Precision Screwdriver Set
I have a pocket precision screwdriver set. Why pray tell would I take a perfectly fine portable screwdriver set and make wooden handles for the bits? Doesn't that defeat the point of having a portable set? Well, my friend the problem is that I got enticed by the sleek metal body and faux leather casing. The design is positively awful for two reasons:
1) the sleek metal screwdriver while perfect for a shelf doesn't offer much in the way of torque for opening loctite'd screws
2) since the bits are held by friction and not magnetically, it is a pain to change bits.
Plus, you know that if you're working with more than two bits at the same time, you will lose one of them. Not to mention how annoying it is to keep changing bits as you encounter those two types of screws all over the device teardown you are doing.
One day I decided, enough was enough and it was time to get a proper precision screwdriver set. Since I love the look and feel of wood, I decided to make wooden handles for these bits and upcycle them.
P.S. : I know this is a very basic job and probably doesn't deserve a whole instructable, I'm new to woodworking so I thought I'd share a beginner's point of view. Also, I've been in something of a writers block so I thought better to document this than nothing at all.
Step 1: Materials
* A 3/4" (1.9cm) wooden dowel, 4' (~1.3m) long
* A precision screwdriver set
* Epoxy (I'd recommend something with a setting time of at least 20 minutes; it was a mistake to rush things with the five minute epoxy
Step 2: Tools
* Band saw (or hacksaw)
* Drill press (and/or hand drill)
* Drill bits - a small pilot hole bit and a bit around the size of the screwdriver bits
* Belt sander (and/or 220 grit sandpaper)
Step 3: Step 1: Make That Cut!
Cut the dowel into 4" (10cm) long pieces. I used a vertical band saw, but this should be easy with a handsaw as well. Don't worry about making the cuts perpendicular, the cut surface will soon be sanded. With the 4' dowel I got 12 pieces.
Step 4: Step 2: Center That Hole!
Choose a drill bit which is slightly smaller than your screwdriver bit in diameter and make a hole in the dowel as shown. The hole depth will determine how far in the screwdriver bit will go. Try to make the hole as centered as possible, this is where a drill press comes in really handy, but I tried it with a hand drill too and it's not very hard. If you're using a hand drill, clamp the dowel well and keep your eye level with the cutting point to make sure that the bit is vertical.
Step 5: Step 3: Sand Sand Sand and Sand Some More
I'll be truthful, this was the most tedious and potentially dangerous part of the project. The belt sander is a remorseless beast. While you could do this with some sandpaper as well, it would take far too much time(like eons) I've sanded the tip sharp and the back rounded. I also sanded the sides for an oh so good, sanded wood finish. I'm using a scrap piece of wood to hold and turn the piece because it seemed too dangerous to use my hand in that last case.
BTW: in the images you can notice that I'm not wearing safety gloves. I think opinion is divided on the topic, but many people have advised me not to wear gloves when working with grinders of any kind because they can get caught and result in severe degloving injuries(do NOT google image search that)
Step 6: Step 3.5: Step Back and Admire Your Work
I really liked how the tip came out, looks like an oversized pencil :)
Step 7: Step 4: Why Drill Another Hole?
Drill a small (as small as possible, a pcb drill bit is fine too) Later we're going to insert the bits in a the hole at the tip, and as we force the epoxy coated screwdriver bit in, the small hole we'll drill now will let the air and excess epoxy escape. The first time I tried doing this without this hole, the result is the cracked handle in the second image. Don't get me wrong, this is still plenty strong, but best practices and all :) We want the hole to be as far back as possible while still being connected to the central hole where the screwdriver bit will go.
Step 8: Step 5: Whip Up Some Epoxy!
Mix some two part epoxy and coat the back of the screwdriver bit in it. Pour a drop into the handle as well. I used 5 minute epoxy which is why I ended up wasting about half of it. Use something with atleast a 20 minute setting time, it'll not only give you more time to work, it'll also soak into the wood better and probably give you a stronger bond.
Step 9: Step 6: Put the Bit In
Push the bit into the handle. Don't be afraid to push down on the bit to make it go in. Some epoxy will pour out of the small hole in the handle and from around the bit. Wipe it off before it hardens and wham! we're done. Just wait for the epoxy to set. I liked the finish the epoxy gave to the area around the small hole, so I used the epoxy as a lacquer and coated the entire handle in a thin layer. It came out a lot better than I expected. Although, the next time, I'd rather finish the wood with tung seed oil because the wood feel is almost gone with the epoxy lacquer.
Step 10: Done!
Now that you have one, make more and more! Stack them in pyramidal and floral shapes!
Good, now stop playing with your screwdrivers and get back to work! Happy making :)
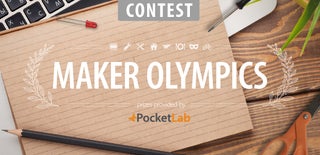
Participated in the
Maker Olympics Contest 2016