Introduction: DIY Crown Molding
Time to drag out the ancient Craftsman molding head set. Apparently a lot of people are afraid of these things. I can see why. If you use them with little thought and prep you'll probably get a little kick back. I'm not going to dwell on the cutter too long. If you want more info see my other Instructable about it.
This is about making your own, cheap crown molding. My cost for 32 feet of crown molding was about half of what you pay for premade. And it's unique so you have the added bonus of really making future owners of your house really mad because they can't match it!
If you're interested in getting a molding cutter you can find them on Ebay and there is a company that still makes them and loads of knives for them called Corob Cutters.
Step 1: Wood
Choose your material. I picked cheap pine, as straight as I could get with as few knots as I could manage. After working on this for a while I thought I could also have probably used a 4x8 sheet of 3/4" MDF ripped down to whatever width I wanted.
Step 2: Set Up Your Cutting Head
I picked a simple three bead cutter for the middle of my molding. I centered it on the board. It's fairly easy to do this because all of the cutting knives are 1" wide. Also the molding head is 3/8" wide and you can mark the middle of it easily enough.
Use those feather boards! They're helpful for keeping things tight against the fence and table.
Pick a piece of scrap to set your depth. If you're using a shape that requires a deep cut then do it in multiple passes. This is likely where the molding cutter novices err and scare the hell out of themselves. Go slow and do multiple passes as needed.
Step 3: As Always . . .
Don't forget these. Funny enough the molding heads have a lower pitched sound so they're not as bad without hearing protection. Until you start cutting and then they get a little noisy, but not as much as a regular blade.
Step 4: First Swipe
When making molding run everything through at the same time. If you're making two boards, run them both. Don't try to run one kind of cutting knife, then another, and then try to reset it up for your next board. It'll never line up. Also I like to mark which side of the board I run through against the fence and away from it.
Step 5: Pick Your Next Shape
Here we have the ancient, culturally inappropriate cutting knife packaging. I tried a few and settled on a flute cutting blade and used a piece of scrap to set the depth.
Step 6: Swipe Two and Three
I decided to make my design symmetric. So much easier to deal with. I centered the flute . . . cove . . . divot, whatever midway between my first shape and the edge, then ran one side through then the other. I ran all of the four boards through before changing the setup for the next phase.
Step 7: Cutting the Back Angle
Sticking with the symmetry idea I cut the back angle at 45 degrees with my regular blade set at 45. This will create the flat surface that will sit against the wall and ceiling. You can do other angles, but I'm not messing with that. Too much geometry for a lazy day off work.
Step 8: Cutting the Front Angle
By using 45 degrees for the back angle all I had to do was keep the blade at 45 degrees and send the board through on it's face this time. I tried a few small passes to make sure I didn't take off too much before deciding that I had everything set the way I wanted it. This will make the edge that is perpendicular from the wall and ceiling. Not strictly necessary I could have cut the back edge all of the way to the beginning of the flute on either side. Dealer's choice.
Step 9: Sanding
To sand the shaped side I used a combo of steel wool, mostly the finer variety. For the flat face edges I used a piece of nearly dead palm sander paper wrapped around a scrap block.
Step 10: Prime Time
After making a few passes sanding I decided it looked good enough for me and gave everything a coat of primer. I'll probably give it another primer coat before giving it a little of the business with steel wool and then putting a final top coat on. I know that in time it's possible that the knots will bleed through the paint. I'll wait to see if/when it happens before dealing with it. A coat of shellac then another layer of top coat will deal with it.
Step 11: Wrap Up
Yeah, it's not perfect. Slight warps in the wood will make it hard to get the corners to line up right because the molding head set up cut it unevenly. But it was inexpensive and I'm willing to deal with a little extra time on the finish work when I put it up. Fine work making adjustments with scrapers and chisels and what not then touching up the paint. Likely I'll be using a crown molding cutting guide and making 45 degree corners with a compound miter saw. But I do have a coping saw if I feel frisky. And as we all know painter's caulk can hide a lot of problems.
We could all do things better and there are always trade offs with price and expediency. Have fun and finish with the same number of fingers you started with.
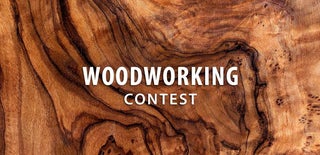
Participated in the
Woodworking Contest