Introduction: Patio Table With Cinder Block Legs and Beeswax Finish (Benches Included)
Summer is coming soon, and it will be time to enjoy the outdoors again. I found a guy, locally, who cuts slabs of lumber from whole logs, and these make great table tops. It's super easy to make a pair of legs from stacked cinder blocks. The legs become secure with the addition of long bolts, mounted in concrete poured in the bottom blocks. The bolts (all thread rods) extend upward through two blank cinder blocks, and through the boards that bring the table to the correct height. The stack of cinder blocks and boards are bolted together securely, to provide a stable foundation for this slab table. The table top is screwed to the spanner boards from underneath for a solid connection. I've added some wooden angle-braces to make sure the table won't move.
Two other slabs of wood were cut up to make matching benches.
I shortened the twelve-foot (plus) table slab to make a ten-foot long table, and used the 32-inch square cut-off piece to make a separate "pedestal" table to put by the barbeque.
Supplies
For the legs
6 - Cinder blocks
4 - All Thread rods, 5/16-inch by 36-inch
4 - Nuts and washers to fit the rods
Propane torch for bending the rods
1 60-pound sack of concrete mix
2 - 1 1/2x8-inch boards 18-inches long
2 - 3x8-inch boards 24-inches long (I cut some of the bench material to these dimensions, so if you're using planed boards from the hardware store, work out the thickness you want. Three factory 2x10s would work out about right).
1 1/2-inch circle cutting bit (hammer and chisel) for recessing the nuts
For the table top
1 slab of wood, approximately 3-inches thick, and at least 32-inches wide, by 10 feet long (or whatever you like).
For the benches
2 rough-cut slabs of wood, same thickness as the table top. Cut into pieces, as follows:
Rip two 12-inch wide by 8-foot long pieces for the bench tops, and a third 14-inch wide by 8-foot long piece to be cut into legs (and angle braces). Note, the legs are recessed into slots that are milled into the underside of the benches with a router. Using this three inch thick material, the legs need to be cut 16-inches tall to have the top of the bench at 18-inches high.
Router and bit. If you don't have a router, you can just cut channels in the underside of the bench with a skill saw and set the legs in the channels.
For mounting the table top:
8 lag bolts 5/16-inch by 5-inches long (length will depend on thickness of lumber used)
Drill with bits
Skill Saw
Hammer and Chisel
Pocket hole jig, and screws
Sander and Sand Paper
2 Pounds of pure beeswax
16-feet clear vinyl corner protector tape (optional)
For the pedestal table:
Step 1: Make the Bases for the Legs
To make the legs, you need three cinder blocks for each leg (six total), a sack of concrete, and four 3-foot long all-thread rods (I was looking for 3/8-inch rods, but all the store had four of, were 5/16-inch diameter rods. You could probably get by with 2-foot rods, and use nuts and washers to anchor the ends of the rods in the concrete. The store I bought parts from didn't have four 2-foot rods of any size, so I used 3-foot rods and made bends so the rod would be anchored really well. Note, this 5/16-inch rod does not bend without breaking, so you need to heat it with a torch to make the bends.
One 60 pound sack of concrete mix will adequately fill the twin openings in two cinder blocks, with a bit left over. Be sure to wet down the cinder blocks first. For some reason, I set the blocks on cardboard before filling them with concrete. As soon as they were full of wet concrete, I realized that the concrete would wet the cardboard, and sag below the bottom of the cinder blocks. To fix this oversight, I slid the concrete-filled blocks off the cardboard and scraped off the bulged concrete on the bottom to make them sit flat. Forget the cardboard, and just put a piece of plastic under the cinder blocks, if you're worried about staining your patio.
Cinder block openings are tapered, so put the narrow end of the taper on the top side to make the foundation of the legs more secure.
Let the concrete cure for a few days before tightening the bolts.
Step 2: Stack the Legs and Mount the Spanner Boards
The legs each have a combination of boards on top to bring the table top to the correct height. The upper-most "spanner" boards will need to extend a couple of inches past the boards used for spacers to make room for the lag bolts that will secure the table to the legs. The exact combination of boards will depend on the thickness of your table top, and how high you want the table to be. This stack of three cinder blocks measures 23 1/4 inches high. I ripped a piece of the 3-inch material in half to make two 1 1/2 thick boards, which when added to the 3-inch thick spanner board, brings the table to about 30-inches high.
You need to drill holes through the spacer boards and the spanner boards so the rods can extend through. You will also need to chisel out or cut notches about a half-inch deep around the top of each drill hole in the spanner boards to recess the nuts that hold the legs secure. When the legs are bolted securely together, the rods will be slightly below the upper surface of the spanner boards (assuming you were careful about positioning the rods in the concrete).
You can also drill holes near the ends of the spanner boards for the lag bolts that will secure the table to the spanners. If you would rather, this can be done later.
Note: if you are able to find a board for the table that is at least 36-inches wide, there shouldn't be a problem with people hitting their knees and ankles on the sharp corners of the blocks. My tabletop was only 32-inches wide, which leaves less space between your knees and the cinder blocks. To prevent complaints, I used some vinyl corner protector strips that I had left over from another project. They are clear, so not very noticeable, and they are worth the effort.
Step 3: Position the Legs and Mount the Table Top
This table will be very difficult to move, so decide on where you want the table before mounting the table top to the legs. Once you have the legs in position, set the table top evenly on top of the spanner boards. You don't want the legs too close to the middle, or someone standing on the table (trust me, someone will do this) could tip the table over. I'm positioning the legs two feet from the ends.
Once the table top is in the position you want, screw the lag bolts into the table top from the underside.
Note: I have moved a similar table (a few inches) with the legs attached, by sliding both legs at the same time, using webbing straps. I don't recommend trying this. If you need to move the table, you should disassemble it and move the legs and table separately.
Step 4: Sand and Finish the Table Top
The table is essentially complete. If you didn't sand the surface ahead of time, you will want to do that now. I don't like sawdust, so I worked the arch in this table down with a carpenter's plane. Make sure you learn how to sharpen a plane correctly, or you'll just make more work for yourself in the final sanding.
Before the final sanding, I mixed up some two-part epoxy to fill in a few cracks and knotholes.
I debated about what kind of finish to apply to this table. I hate painting, but I don't want the wood to just weather outside. I've been using beeswax to treat canvas for some projects, and I thought I'd try using the same technique on this table. There are a lot of recipes for mixtures of beeswax and various oils and solvents, but I wanted to see if I could do this with pure beeswax. Before starting, you will want to wipe off as much of the sawdust as you can with a rag. Using a bit of mineral spirits on the rag helps, but is not absolutely necessary.
For the beeswax finish, the tools are simple, just a block of beeswax, a heat gun, a rag, and you'll want to wear a glove. Also, you'll want to put down some cardboard to catch the drips. The technique is the same as with treating canvas, heat the surface of the wood with the heat gun on high, then rub the block of beeswax over the surface, and hit it with the heat gun again. Keep applying wax until the wood won't soak up any more wax.
This is a two-step process. In the first step, you go fairly quickly, getting as much wax as you can on the wood, just cover everything well. In the second step, go back over all the surfaces with the heat gun, moving the nozzle in a circular motion, fairly close to the wood. The wax melts, and forms a puddle in front of the heat gun. Work in strips, pushing the puddle along, adding more wax if necessary, and wiping the hot wood with a rag to remove any excess wax. Try to heat everything as evenly as possible. The goal is to avoid having the table feel sticky or having wax come off on peoples' clothing on warm days. I was a little concerned about scorching the wood, but it wasn't really a problem.
Fun fact: Beeswax melts at around 140 degrees Fahrenheit, because of the higher melting point, it burns hotter than other wax, so beeswax candles burn brighter.
One thing about using the hot wax treatment is that it works best on horizontal surfaces. For the bench legs, I propped the benches up against the table so I could do the flat sides of the legs more easily. This was very precarious, with a step stool on top of the table, so be careful.
A note about beeswax. Don't try to use the beeswax that is sold for sealing toilets, that is not pure beeswax. I found a local beekeeper who was selling beeswax for $7 per pound, which is much less than any other sources I found. It took about three pounds of beeswax for this project, including the table top, benches, and the bench legs. Quite a bit of wax comes off when you're wiping away the excess, but not as much as you'd think. I'm using the wiping rags for fire starter, so the wax is not wasted.
Step 5: Add Diagonal Braces
It really doesn't need it, but I'm adding diagonal bracing pieces to the underside of the table, where the legs mount. These are just triangular pieces of the same 3-inch thick material. I'm mounting them with pocket holes to the underside of the table, fitting them snug against the concrete legs, and adding a couple of screws into the spacer boards at the top of the legs.
Step 6: Make Some Benches
You need benches to sit around this table, and these are made from the same material as the table top. I ripped the benches 12-inches wide, and cut slots in the bottom to mount the legs in position. For added stability, I made the legs 14-inches wide (two inches wider than the bench top) at the bottom, so the legs extend an extra inch on each side of the bench. The legs are tapered upward, to 10-inches wide at the top. This allows the legs to be mounted in recessed holes, cut an inch deep into the underside of the bench. In the past, I've mounted bench legs buy just cutting channels with a skill saw, if that works better for you. Lastly, I cut "V" notches in the bottoms of the legs to keep them from wobbling on the less than perfectly smooth patio. Since I can't seem to line up where the V comes together when I'm sawing, I just drilled 3/4-inch diameter holes at the intersection.
After cutting the notches, I used the pocket hole jig to make holes on each side of the slot. The legs are fitted into the slots, and pocket hole screws inserted after leveling the bench. To make the bench legs more secure, I added diagonal supports, similar to the ones on the underside of the table. I used the same pocket hole jig to mount each diagonal support to the bench and the leg. Once the diagonal supports are secured, the bench legs are extremely sturdy.
Note: as with the table top, you don't want the legs to be too far from the ends, so the bench won't tip if someone is sitting on the end. These legs are mounted about a foot from each end of the bench.
Also note, these benches are about 8-feet long, and the table is 10-feet long. I hope no one has a problem with that.
Sand and finish the benches to match the table.
Bonus points if you noticed the swing in the background, made from a scrap of the three-inch thick board I used for the benches. Between the long table (and barbeque table), the benches, and their legs, there really wasn't much material left over. I have a six-foot long piece, about nine-inches wide, but that's all that's left over from three huge planks. It's a bit surprising that it takes more lumber to make the benches than it did to make the table, just something to keep in mind.
Note on the lack of photos showing how the boards were cut: I don't have a saw that can cut this 3-inch thick wood in one pass, consequently, the cutting was quite a mess, with setups that should not see the light of day. So I didn't take photos of the cutting process.
That's it, the patio is ready for summer (I will be installing a shade over the table). I will update this instructable to document how the beeswax finish survived after a summer and winter.
Step 7: One Year of Weathering
When I posted this instructable I said that after a year I'd do a follow-up on the beeswax finish. The table and benches were outside all last summer and winter. Temperatures in the summer got up to 100 degrees, and we had a particularly wet winter with lots of snow. I did put a shade cloth up last summer, and it shaded all but the last two feet of the table, but otherwise the table was exposed to the elements.
The big knots dried out and cracked, and those will need some sanding, but otherwise, the finish held up pretty well. Water still beads up on the table, even in places where you can't see the finish. The cracks that I filled with epoxy did not do well, and I'm planning to clean them out a bit and use a better mix of epoxy to fill the cracks.
Overall, I am pretty satisfied with the beeswax finish. I would use it again for outdoor or even indoor projects.
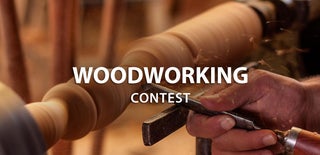
Participated in the
Woodworking Contest