Introduction: Glow Plates
As anyone who has taken at least a brief glance at my other Instructables can probably infer, I really like engraving things and playing with glow powder. So here's a little project involving both of those. (In my case I combined it with another one of my loves -- music -- but everybody else can use whatever images they want.)
Time: Moderate, depending on design complexity, toughness of glass and sharpness of burrs.
Skill: Some. Can you use a Dremel without injuring yourself or others (too badly)? Then you can do this.
Caution: We're playing with glass. If it breaks it can cut you, and glass dust is not something you want to breathe in. Also the normal precautions with the use of powered hand-tools.
Step 1: Tools & Materials
Required
- glass plate with a flat bottom that is a good few millimetres thick. Picked up mine at a thrift store for very cheap.
- rotary tool, e.g. a Dremel
- diamond engraving burrs of the round-tipped variety
- glow powder (I get mine from Techno Glow)
- clear porcelain varnish (I use the clear-gloss varnish from Marabu ← The Marabu gloss appears to have been discontinued, so instead try the Vitrea 160 Gloss Medium from Pēbēo)
- safety glasses/goggles
- ear protection
- DUST MASK because hooboy is this going to kick up a lot of glass dust, and you really don't want to breathe that
Recommended
- craft knife (X-acto or similar)
- paper
- permanent marker, preferably black or another dark colour
- clear packing tape
- large dental pick and/or wax scraper
- thick pad of fabric or anti-slip rubber mat or whatever else can provide cushioning and slip resistance
- table clamp stand or ceiling hook to hang up the Dremel (only if using a flex-shaft attachment)
- tape measure/ruler/calipers/measuring device of some kind
- glass polishing "burrs"
- anti-vibration gloves
- small container
- baking sheet
Step 2: Designing
If you're going to jump right in and freehand your design, skip on over to Step 5.
If you're like me and prefer a bit more planning, stick around.
Draw out your design, either traditionally or digitally. Traditional works can be drawn to the right size from the get-go, or scanned to computer for touch-up and resizing. Since the idea is to fill the engraved lines with glow powder, don't make a crazy-detailed design; keep it restricted to lines a good 2+ millimetres wide. 1mm at absolute minimum. I went with a simple treble clef and bass clef, so I found some Creative Commons images to use for my stencils.
Measure the area that will be engraved. Open up your image file in a program that will let you scale it to a set size. I imported mine into OpenOffice Writer, since the guides down the side and across the top make for quick and easy scaling. There might be better options, but this one consistently gives me accurate, trustworthy results. Note that for this method to be not-frustrating, crop the image to its bare minimum, with the drawing canvas edges right up against it.
Once everything is scaled to satisfaction, print it out. This will become the stencil.
Step 3: Stencilling
If you're going to tape your stencil to the reverse side of the glass and engrave from that, skip to Step5. Otherwise read on.
Time to make the stencil! I like mine to be a bit more durable than just a piece of paper, so I'll cover it back and front with a layer of packing tape to up the amount of handling it can take before falling apart. For a quick I-will-only-use-this-once-for-this-specific-project stencil, you can forgo the tape coating.
Once it's taped up (or not), grab a craft knife and carefully cut out the design.
Step 4: Outlining
Now that you've got your stencil, it's time to transfer it onto the glass. Tape the stencil into position to make sure it won't move partway through the process, then trace the design with a permanent marker. If it's a somewhat more complicated design I will sometimes use spray paint instead to transfer it, but this only really works for very flat surfaces (too much under/overspray getting all up in everything if the stencil isn't perfectly hugging a curved surface).
Remember that since things are being engraved from the reverse (we're engraving the underside of the plate because we don't want food coming into contact with the glow powder parts), the image needs to be flipped horizontally. Double- and even triple-check this. Often I have to get an outside opinion on my treble clefs, since I've engraved them from the reverse so often that I can't definitively recall which orientation is the normal one.
Step 5: Engraving
I've seen several glass-engraving how-to guides showing the engraving being done under some sort of water drip to keep the dust down, but the few times I've tried that method it was too difficult to see what I was doing through the diffraction of the water, so I just strap on a good filtration mask and then vacuum the dust out of my workspace when I'm done. Occasional wiping down of the work-in-progress with a damp cloth can help keep the dust down too. Just be careful not to wipe off your marker outlines.
Break out the rotary tool and engraving burrs. Start with the smaller burrs and work up to the bigger ones. This gets a smoother finish than going the other way. Begin with basic outlines and work up to larger "fill" areas. Several light passes are far preferable to one or two really heavy ones. Heavy, aggressive cuts are more prone to having the torque jerk the burr away from its intended path and scratching up areas that weren't supposed to be engraved, or even jumping away from the glass entirely in order to say hello to your skin, and then comes the challenge of figuring out how to incorporate the mistake so it doesn't look like a mistake, or just trying not to bleed all over your work. Starting with light cuts also helps get a feel for the glass, since the many varieties of glass will be harder or easier, rougher or smoother to engrave, and just generally behave differently under the burrs.
Cannot stress this enough: DO NOT INHALE THE GLASS DUST
Step 6: Deepening
Once the basic outlines are done, it's time to step up to larger burrs to deepen the engraving. The deeper the cuts go, the more glow powder can be filled into them, but don't go so deep that the integrity of the glass is compromised. Deeper, stronger passes should be balanced with quick, lighter ones to smooth out the finish and get an even depth all around.
Step 7: Polishing
This step is optional. Skip over it to the next one if you so desire.
These rubberized polishing burr things will buff up the engraved areas to remove some of the frosted effect that the diamond burrs left behind, and make it a bit easier for light to shine through unimpeded, which we want for the glow powder part. The effect isn't huge though, so this step can, as mentioned earlier, be skipped without too much trouble.
Step 8: Mixing
Break out the glow powder and varnish! A mix ratio of 1:1 gives a good consistency; thick enough to scoop up, but runny enough that it will self-level once it's smeared into the engraved areas. Mix up slightly more than you think you will need, because if you have to take time to mix up a second batch and the first application starts to dry while you;re at it, it will be very hard to smoothly blend it into what's already there. Any excess glow powder mixture can be dripped onto plastic or a sheet of waxed paper and turned into tiny glow cabochons.
Step 9: Filling
Put the plate down on a flat surface, with the engraved side facing up. Grab a scraper or popsicle stick or extremely tiny spoon and scoop a glob of the glow mixture into the engraved areas. Poke at it with the scraper to keep it flowing, and carefully slop it all over the engraved areas, working it carefully along the edges. Try to keep it confined to the cut-outs, but don't stress too much if some of it ends up colouring outside the lines, as it were. That can be cleaned up later. It will also shrink down as it dries, so as long as it isn't in an absolutely enormous mound, it will probably shrink down below the edge of the engraved zones. If it sinks down very far, that opens the possibility of doing a second layer. I just did the one coat on mine, though. Any outside-the-lines bits can be carefully scraped off once it's dry. I like tiny dental scrapers for this task.
Apologies for a slightly jumpy video. It's difficult to hold the camera still with one hand while doing crafting work with the other.
Step 10: Varnishing
Once the glow powder mix is dry, it will probably be a bit rough to the touch, kind of sandpapery. Near as I can tell, this seems to be due to the minute air bubbles that get stirred in during the initial mixing. I added a layer of just the varnish over top to act as a sealer and maybe smooth it out somewhat. Multiple coats might be required to do a proper job of it.
Apologies again for a slightly jumpy video. It's difficult to hold the camera still with one hand while doing crafting work with the other.
Step 11: Cleaning
Any outside-the-lines slop can be carefully and gently removed with a tiny, sharp implement, like a dental pick or fingernail, or even a small screwdriver if no other options present themselves.
Step 12: Baking
Treat the final pieces according to the instructions on the varnish. Some of the newer paint and varnish formulae may not even require baking to set them. In this case it was bake at 170°C for 30min. Put the pieces on a baking sheet and let them fully heat up and fully cool down in the oven. Thermal shock = not fun. It would be a shame for things to break after all the work that has been put into them.
Step 13: Enjoying
Now that the firing process is done, it's time to enjoy the new glassware. The varnish is supposed to be dishwasher-safe once it's fully cured, but I have yet to perform any extensive testing of this myself, and really have no idea how solid it is with glow powder mixed into it, so I definitely recommend gentle hand-washing when cleaning is needed.
Maximum enjoyment will, of course, come with using them in the dark or under a UV light.
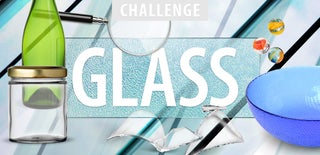
Runner Up in the
Glass Challenge 2017