Introduction: Goldie Bronze Clay Ring With Name in Runes by 16-year-old Artist-in-Residence. You Can Make It Too!
YOU CAN MAKE ONE TOO!
Art genes run in our family blood! Me, my sister & my son, a grandson, and my great-nephew Derrick all have the gene. Invest your time, talents & resources in others with the same talent God gave you- pay it forward! Who helped you when you were "a work in progress"? My prayer is that God will gift Derrick & my grandson David with the same wisdom He gave these men for His glory:
" And... I have put wisdom in the hearts of all the gifted artisans, that they may make all that I have commanded you: 7the tabernacle of meeting, the ark of the Testimony and the mercy seat that is on it, and all the furniture of the tabernacle—8the table and its utensils, the pure gold lampstand with all its utensils, the altar of incense, 9the altar of burnt offering with all its utensils, and the laver and its base—"Exodus 31:6-9 NKJ
The Biblical description of the tabernacle and its articles including the gold breastplate with the 12 precious inlaid stones, is beyond magnificent, stunning. The ark, made of gold, silver, precious stones and wood, the skills these artists had to have in order to bring to life the blueprints in God's mind- HAD to be super-human! It genders excitement comparable to the opening night of SpeilbergsRaiders of the lost Ark! I've often thought about the special gift given to these men that carved spirals of angel wings and almond branches laden with their fruits. Pomegranates of blue, purple and scarlet. How did these sculptures, tapestries, and vessels set before mere men inspire them to worship such a Creator? And did the artists so gifted with this talent feel complete, fulfilled, to use their wisdom exactly as God intended when He created them for this very purpose, time, and place in the universe? And do you or I feel that same satisfaction when our work of art is finished? Does it inspire others? Does it bring honor and glory to our Creator? Ah, that's what I would pray for my David and Derrick!
Step 1: WHAT YOU NEED
- 100 grams soft Goldie Bronze clay (http://www.metalclays.com)
- wax paper cut into rectangles or teflon work surface (https://www.metalclaysupply.com/SearchResults.asp?search_button.x=0&search_button.y=0&Search=teflon+sheet)
- white sheet of paper to go under wax paper
- needle tool (http://www.metalclays.com)
- clay shaper size 0 taper point is what we used (http://www.cooltools.us)
- mug or candle warmer (goodwill or other thrift store, Hobby Lobby) make sure plate is level and doesn't make a shallow dip in the middle
- HattieS® QuikArt™ Ring Shank Templates - B or other guide for cutting a ring shank (http://www.metalclaysupply.com) and you can also make your own
- agate burnisher (http://www.metalclaysupply.com)
- scissors
- good lighting
- mirror for checking dryness of clay
- Badger balm or olive oil (use sparingly) (Cracker barrel for badger balm)j
- Metal tissue blade (http://www.metalclaysupply.com) or safety razor blade
- fondant roller with purple rings (Hobby Lobby or walmart Wilton cake section)
- distilled water in a non-metal bowl
- cosmetic sponge
- fine (usually pink) emery board (for filing fingernails)
- small spray bottle of distilled water
- stepped ring mandrel w base (http://www.cooltools.us)
- sheet of clear semi-flexible plastic like lightweight stencil sheet, acrylic sheet page protector, or the clear top of a box of cards
- ring sizers (plastic or metal, any of the metal clay sites)
- investment material (http://www.metalclays.com) or Hatties ring patties or Redy pellets (cooltools.us) ring sizer in your ring size
- half round set of sanding sticks (http://www.cooltools.us)
- sheet of fine sandpaper (walmart)
- steel hand brush (looks like a toothbrush-http://www.cooltools.usor Northern Tools, Harbor Freight)
- rubber block (http://www.cooltools.us)
- dremel tool w polishing wheel and stainless steel brush wheel (walmart, Lowe's, replacement wheel & brush- http://www.ebay.com)
- protection for fingertips (rubber fingertips/cots; office supply) or cut off fingers of a THICK rubber or latex glove
- clear protective goggles (lumber yard)
- small sanding sticks (http://www.firemountaingems.com) they look like q-tips
- programmable jewelry kiln (http://www.cooltools.us) mine is a Paragon front loader. It needs to go up to 2000 degrees F
- long metal cake decorating spatula that will fit between the posts to remove firing container (Hobby Lobby or walmart cake dept)
- stainless steel wire mesh cloth for carbon firing (you will need 2, one for base, one for making a tent to cover ringhttp://www.metalclaysupply.com instructions for making tent on same page as wire mesh)
- non-flaking foil to make container for firing with carbon (make it to fit your kiln-instruction video & foil kit @ http://www.cooltools.us)
- pre-fired or activated coconut carbon (http://www.cooltools.us)
- 4 kiln posts (to elevate firing container) (http://www.cooltools.us)
- tumbler (Harbor Freight, amazon orhttp://www.ebay.com)
- shot for tumbler (http://www.cooltools.us , amazon or ebay)
- Ivory liquid- 1 drop (must use this brand; other brands will dissolve the inside of the rubber canister of your tumbler)
- scotch tape
- flat smooth paintbrush, small head fine hair like sable
- small fan brush
- alcohol
- OPTIONAL:
- Vintaj patina for metal- onyx, aged bronze (Hobby Lobby)
- Vintaj glaze sealer for metal
- Vintaj Reliefing Block
- brush to apply glaze & patina
- Thermal gloves (http://www.metalclays.com/search?q=gloves)
- Green safety (eye protection)glasses (http://www.cooltools.us) for looking into glowing hot kiln
- Rubber stamp set 6-7pt for inside of ring (office supply)
Ok nephew, LET'S HAVE SOME FUN!
Step 2: Mix the Investment, Then the Clay
Use your ring sizer to figure the size you want your ring to be. You will need to make your ring 1 size larger to take into account Goldie Bronze's 6% shrinkage rate after firing.
PREPARE YOUR INVESTMENT PLUG. It's cheaper to make your own if you plan on making many rings, or setting stones (video on the page where you purchase investment:http://www.metalclays.com/p/815/shrinkage-plug-investment-100g) . You can use the Hattie's patties or Redy pellets as well. This will hold your ring's size in place during firing. It keeps the ring from shrinking too much. We used the ring sizer, and cut a strip from the clear plastic sheet, rolled it into a tube that fit inside the ring size desired, but a bit taller than the actual ring width. You might want to go up 1/2 a size to allow for the plastic tube. Overlap plastic slightly and secure it with a small strip of scotch tape the whole width of the plastic tube. Place it inside the ring sizer to hold the investment. It's a lot like plaster of paris. You can also order an investment ring mold from http://www.cooltools.us Follow the instructions on mixing that comes with it. If you make more than you meant to, just pour another for future rings. When dry, sand top lightly, mark size on bottom so you will be sure to set the level part (marked side down) inside the ring. It takes a couple of hours to dry, so do this ahead of time. We sped the process a bit by placing the plug on the warmer. After firing, dispose of the plug by dissolving in water and pouring outside. Don't pour it down your drain, it will turn into concrete in your pipes!
Step 3: Mix the Clay
Find the width and size you need on your ring template. Cut several sheets of the wax paper whatever size you would like to work with to roll out your clay. If the sheet gets messed up, get a new one :) The white paper underneath helps you see your work easier, unless your table top is already white! Goldie Bronze feels a bit like building castles of beach sand. Start by spraying distilled water directly into the container of powder. For more detailed instructions & great photos on mixing & firing, go to: http://drakonaria.blogspot.com/2012/08/test-of-goldie-bronze.html We won't be showing how to use a mold to impress the clay today, but soft Goldie Bronze really makes a beautiful image made from a mold impression- very crisp with fine details.
You want it to have the same consistency as the sand for your sand castle, it needs to hold its shape, but shouldn't crack when it is bent slightly. Derrick & I mixed with the end of a paintbrush.Lubricate very lightly your wax paper rectangle that is placed on top of the white sheet of paper with Badger Balm or olive oil. Lubricate your hands & your roller lightly . Take out the clay & start folding & rolling it out thinly several times to be sure it is well-mixed. Spray on water as needed, you will get the hang of it! If it starts sticking to the roller, your hands, etc. it's too wet. Let it sit 10 minutes rolled out, check it to see if it is less sticky, if not, repeat.
Put it back into the container & let it rest for 30 min. You can get all your other stuff ready while it rests, or you can listen to your headphones or watch a movie like Derrick did!
As we worked, we talked about God and lots of other topics. When you spend time with others, you learn their heart, and you exchange ideas. Derrick grew up all over the world- he's an army brat! So he has a good view of others from different cultures. What a blessing that he is not prejudiced, he understands that many differences between others are just cultural. Pretty neat for a 16-year-old! I was raised prejudiced against people of different color than I am, and it was not until college when I had a wonderful friend who had a different tint to his skin than I did that I came to understand prejudice is wrong, and God, the greatest Artist of all time, had a full palette when He made man, His crowning creation! Even my parents eventually changed, and realized their prejudice was wrong. Hooray for Paula Deen who admitted she was wrong for her former views. Anyone can learn no matter what their age!
Step 4: READY SET ROLL!!!
Prepare your ring mandrel by cutting a strip of wax paper the size of the step you will be using plus a little for overlapping. You can use a teflon work sheet as well. Tape together tightly to secure the paper to the mandrel. This will keep your mandrel nice, and makes it so easy to slip your ring off by pulling on the paper instead of the ring. If you are using a metal mandrel, you will HAVE to wrap it because the bronze will react to the metal.
Now for the fun- lubricate your hands, the roller & wax paper again lightly. Take out the clay, work it in your hand. If it needs more water, spritz sparingly! You should be able to smash it in your palm, it should leave your palm print, and when you start to fold it , it won't crack immediately, it will have a little bend to it. It's a fine balance when you get it perfectly hydrated. If it gets too wet, roll it out as best you can, and it will dry fairly rapidly. Let it sit about 10 minutes and fold & roll. Repeat until you can work with it without sticking to your hands, wax paper or roller. Derrick got the hang of it pretty quickly. If you've ever rolled out pie crust, or worked with any kind of clay, you will be a bit ahead of the person who hasn't .
Step 5: Cut Out Your Ring
Take your lubricated ring template and lay it on your rolled out clay. Use your needle tool to cut out your ring. With the goldie bronze, I have noticed that the needle tool will drag somewhat, and I've found that laying the needle tool down on the clay as much as possible & cutting downward works better than just dragging it through the clay. Kind of cut as you go. I don't want a lot of overlap on the ends, so cut off as much as you can, but leave enough so that you can overlap the ends (you can measure the length around the mandrel & measure your clay allowing for extra to overlap about 1/4").Use your cosmetic sponge to lightly wet your clay to prepare it for transfer to the ring mandrel. Let it soak in, surface shouldn't be wet looking. Get your hand underneath the paper and use the paper to flip the ring over onto a clean spot on the waxed paper, (now would be the time to impress a message with your font set from the office supply or write your signature in the middle). Lightly wet this side and all edges as well, then use the paper to transfer it onto the ring mandrel. Don't press it together though, just place one end over the top of the other.
I like using wax paper, but when it gets wet it will wrinkle & disintegrate, so you might want to invest in a teflon surface, and use a teflon sheet to wrap around the ring mandrel.
Step 6: Join the Seam
Take your metal tissue blade and cut through both ends of the clay ring at a 45-degree angle all at the same time. This ensures a better bond of the 2 ends. Remove cut ends, now join together as a seam with your wetted cosmetic sponge and/or paintbrush. You want to eliminate the seam on top & the sides. You will want to lightly wet the whole ring at intervals to keep it moist for your design work. Derrick used the shaper, and by simply turning the mandrel, made a line at the top & bottom of the ring to frame the lettering. He then used the clay shaper to carve rune characters spelling out his name in the ancient Viking alphabet (http://www.pbs.org/wgbh/nova/ancient/write-your-name-in-runes.html )
Step 7: Let It Dry Well
Don't be surprised if you have to start over a couple of times, I often have to make it into a ball, roll it out & recut. When you are happy with your design, let it dry on the mandrel overnight until you can gently pull on the paper and slip the whole ring & paper off. Carefully cut the paper fairly close to the edge of the ring. Then put it on the candle warmer to completely dry (30 min or so). Carefully fold the inside paper together all the way around until it is completely detached from the ring. Then you can fold it together & completely remove. Let dry on the warmer another 30 min. Do the mirror test, lay the ring on the mirror, when you remove it there should be no steam on the mirror. Any moisture in the clay will expand in the kiln & blow up your ring!
When I am working on art, I don't cook- I don't even think about eating- but teen men need to eat, so we ordered Hunt's pizza, thin crust, for around $11. That fed 3 of us, and even though Derrick said since he has eaten pizza in Italy-and it would be hard to impress him with pizza- he said it was 'pretty good!' He has seen Donatello & Michelangelo's work in Italy and we discussed the statue of David- very interesting conversation between a 16- and 60-yr-old! Derrick is a walking encyclopedia, much like my son- and knows something about most every subject. Derrick, God has great plans for you-Jer. 29:12- and I see a lot of leadership qualities in you.
Step 8: Finishing & Firing
After the ring is completely dry, now join the inside seam and the edges. Do this with a little water on your brush, if needed, make a thick paste of extra clay & water to fill any cracks. I just pat it in the cracks with the brush, after it dries, add more if needed. Put on the dryer another 15 minutes and then do the mirror test. When completely dry, use your half round sanding sticks for smoothing the inside of the ring. Use your small sticks, the emery board to smooth the top of the ring and knock off the sharp edges. Sand the top & bottom of the ring by moving your ring in a figure 8 on the fine sandpaper. Goldie bronze clay sands quickly, in comparison to fine silver clay so be careful not to sand away your ring. Brush off excess sanded bronze with a fan brush especially grooved areas. Areas that are to be shiny can also gently be burnished with your agate burnisher.
If your charcoal is labeled 'activated' that means it doesn't have to be pre-fired. If not, prefire according to the directions on the box or where you bought it. After each firing I sift it outside in a light wind to eliminate the ash, by pouring from one container to the other.
Step 9: Firing Phase 1 and 2
Prepare your no-flake-firing-foil firing container (instructions:http://www.cooltools.us/No-Flake-Firing-Foil-12-Wide-Roll-p/acc-600.htm). Prepare your wire mesh cloth tent as directed: (http://www.metalclaysupply.com/Stainless-Steel-Wire-Cloth-for-Carbon-Firing-6-p/54685.htm). It should be large enough to sit over your ring without touching it, but you don't want it any taller than it has to be. It should just cover the widest ring you think you will ever make. Cut the remaining square to fit the bottom of your firing container (mine shown below is not the full length of my container). It will make a wonderful support for all of your flat back pieces. Don't lay your raw pieces on top of the mesh however, the drag from shrinking in the kiln will pull the weakest point apart. A nice thing about Goldie Bronze clay however, is that it repairs beautifully, and will make a strong bond to the already fired clay.
Phase I
Place a thin layer (3-5mm) of activated carbon as level as possible on the bottom of your firing container. Then place your flat wire mesh cloth over that- it should be larger than your ring. Then sprinkle more carbon over the wire screen enough to cover it, about 3-5mm. Level the carbon as much as possible. Place the ring & investment on top of the carbon at the back part of the container that will go in the back part of the kiln.
Place your kiln posts in the kiln so it will support your container on all 4 corners. Place the container as close to the back of the kiln as possible if you have a front-loading kiln. The ideal temperature is at the back. You don't want to put it against the temperature sensor in the back of the kiln however or touching the wall. Now program at 660 degrees F and hold for 30 minutes. This is the pre-fire phase that burns out the clay from the bronze in the atmosphere. When it is finished, take out your container carefully with the spatula and set it down on a fire-proof surface. I use fire brick but anything that is heat-proof will work, like the top of your stove. Your pieces will be almost black and very fragile. DO NOT PICK THEM UP OR JIGGLE THEM AROUND. Place the wire mesh cloth tent CAREFULLY over the top of the ring. Since carbon acts as an insulator, the thicker the layers the longer it takes to heat to the desired temperature. So you will have to not only cover the height of the ring but you want about 3-5mm above the top of the tent. That's why you don't want the tent any higher than you need it to be. The tent keeps carbon from getting in between the investment plug & the ring, so when it shrinks, you won't have little carbon rocks embedded in your bronze ring that you will have to dig out. After firing, your container & mesh cloth will be black but can be used over & over.
Phase 2:
To sinter metal together properly, replace firing container back in the kiln on the posts, jewelry positioned in the back of the kiln. Use thermal gloves if needed (if kiln & carbon are glowing, you need the UV glasses & the thermal gloves). No need to cool your kiln; start right in, reprogram to 1508 degrees F and hold for 40-60 minutes. Since we had a lot of carbon, I chose 60 minutes. It's best to let it cool off in the kiln, but if you are in a hurry, put on furnace goggles, high temp gloves, and remove the container with the spatula. This can result in singed arm hair, and can damage your eyes if you don't take safety precautions! I like to let mine cool about 8 hours when possible. When your container & carbon are cool, you can take a fork & dig out your treasures from the carbon! Don't forget to sift the ashes out so it will be ready next time. Your jewelry will be different colors, black is oxidation, which is reduced when you fire anything in carbon. It may come out light bronze, light orange, brown, black.
As we worked, we decided to make a list, and when we get to heaven there is a lot we want to ask God. Derrick said he wondered how the tabernacle was built of so much gold when the Israelites had given all their gold to Aaron to make the golden calf. His great-great-grandmother Ella had a book called The Bible has the Answer and she often referred to it for such questions that I had as a teen. After Derrick left, I went back to the scriptures to see where the gold came from. I don't always remember the words verbatim, and the best thing to do is always go directly to God's word and find the answer. In Exodus 32:2-4 the Bible says the people gave their gold earrings to Aaron to build the golden calf. Back up to Ex 12:33-36 and the Egyptians had given the Israelites other articles of gold, not just earrings. So in Ex 35:4-29 the Lord stirred the Israelite people's hearts to give, and Ex 36:1-6 the Israelite people brought even more than was needed! Derrick do the wheels in your brain ever stop turning to rest?!
Step 10: Brushing & Polishing
Put on your clear goggles, the finger guards for your thumb and next 2 fingers, and get out the rubber block to work on. Load up your dremel tool with the steel brush and brush your piece on all surfaces to remove the oxidation colors. If you kick up much dust, I recommend that you use a face mask. You are grinding off bronze, which is mostly copper with a little tin, and the rubber from your block. Watch your speed- the brush starts flying and the little wires can come loose & stab you as they fly off the brush. You will sit on them, step on them, pick them out of your clothing, hair and skin for a couple of days!
After brushing all surfaces, change to the gray polishing wheel and polish everywhere you want the design to be shiny. If you want it shiny all over, you can tumble them for an hour or two to further close up the pores. Load your tumbler with the recommended amount of stainless steel shot (my rubber barrel is almost half full), cover just to the top of the shot with water, add 1 drop of Ivory Liquid, your bronze jewelry, close top, set onto already spinning motor and let 'er go for an hour or two for bronze. Detailed instructions:http://www.lortone.com/pdf/Jewelry_Tumbling_Instructions.pdfKeep your shot separate from other metals you tumble, as silver reacts to & pits bronze. Same goes for all your tools- wash them well after use, or have a separate set for bronze & silver.
Derrick loves antiquity, so it wasn't surprising that he wanted his ring to look like it had been excavated. He allowed some cracks to remain and hand-shaped his letters. He opted for the antiquing to further age his ring.
To antique:
Wash your jewelry with soap and rinse well. Wipe with alcohol to remove any oils. Dry, then:
Derrick used Vintaj metal patina in aged bronze first, then onyx, polishing with Vintaj reliefing block (follow directions on the box). More info:http://issuu.com/vintajbrass/docs/patina___glaze_on_arte_metal If you use the metal patinas, you should apply the glaze sealer over the top. Use thin layers. Allow each layer of patina and glaze to dry well in between. You can speed this process a bit by blow drying or setting on the hot plate until completely dry.
In between making jewelry, we decided to plan a rest day from working, so we took Derrick to our favorite steakhouse, Fogo de Chao, a Brazilian restaurant. Patrons have a disc by their plates that is green for go on one side when you want meat, and red on the other side for stop. This was a surprise for Derrick, so we didn't tell him anything about it. The waiter laughed when he was explaining the discs system to Derrick because he was wearing a green tee shirt !
Step 11: Some Examples of Derrick's Work
Pics
1 Sword in the stone which we made at the same time as the ring; he wanted it to look partially excavated
2 Antiqued with Vintaj patinas http://www.http://issuu.com/vintajbrass/docs/patina___glaze_on_arte_metal
3 Derrick learned how to stamp a butterfly; he did the wing pendant on the right from a mold and used a template to cut out a slim cross which he joined to the top of the wings with bronze paste; (made at same time as we made the ring)
4 Round dragon design by Derrick
5 I had his design made into a stamp ( http://therubberpress.etsy.com ) then I stamped the design into fine silver for a pendant with ruby cz for the eye
6 Dragon in night sky with colored pencil and ink
7 Shield design for future jewelry
8 Snowy Woods, acrylics
My etsy shop: http://www.picturesofsilver.etsy.com
Even more important than passing on your talent is passing on your faith in Christ (John 14:6). We spend our whole lives trying to do so many things, and then before we know it, we come to the end of our lives here on earth. Nothing wrong with all that, but we can neglect the most important thing; preparing for eternity- and passing that knowledge on to our children and others that God brings into our lives.
Derrick: Keep the main thing the main thing. Major on the majors and minor on the minors (most of it is minor). Choose your friends wisely, they will influence you for the better or worse. 7 times a righteous man falls and 7 times he gets up again. Prov 24:16. All things work together for good to them that love God and are the called according to His purposes. Rom 8:28. To make a decision, ask yourself: Does it matter in the light of eternity? Does it bring honor to God? That's pretty much what I've learned so far in 60 years.
But seek ye first the kingdom of God, and his righteousness; and all these things shall be added unto you.Matthew 6:33
Ok Derrick, give 'em heaven!

Participated in the
Craft Contest
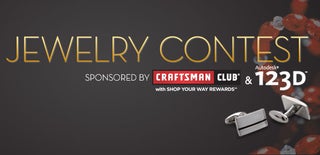
Participated in the
Jewelry Contest