Introduction: How to 3D Model for Fashion Design
In this Instructable you'll learn how to design a 3D form for a specific clothing pattern in the the perfect shape and size - without getting lost in three-dimensional space. If you're already familiar with pattern making and want to learn more about 3D modeling for fashion design, I'll show you a pretty easy technique.
For more information about the specific design in this Instructable, read more about the Symbiosis design concept here.
The dress was designed at The Studio by ElektroCouture. Photo by Andreas Waldschuetz, makeup by Patricia Hoos, model Laura Sieger.
Step 1: Design Pattern for 3D Print
In the first step you'll design the patterns for the fabric parts of your dress. In this case, it's the skirt as well as the right and left side of the bodice. After sewing the dress out of muslin fabric, attach some transparent paper onto the part which will be replaced by your 3D prints. With a sharpie, trace the lines onto the paper and cut off the extra paper.
If you know a little more about pattern making, you can also also skip this step and just design the pattern for your 3D piece without testing it on the mannequin.
Step 2: Create Digital Copy in Illustrator
Now scan the pattern and save it as an image file to your computer. Open it in Illustrator and use the line and arc segment tool to trace the lines. I mirrored the right line in order to have two individual looking curves. Delete the imported image underneath and use the ruler tool to measure if your digital pattern has the right size. After adjusting the size, save it as an SVG file.
Step 3: Import Pattern in 3D Modeling Software
After creating the digital copy of the pattern, we are now going to import the file into our 3D modeling software. For my design, I used Fusion 360. It's also possible in less complex software, like Tinkercad. However, I'm continuing with Fusion 360 for the rest of the Instructable.
In Fusion 360, from the menu bar select INSERT > INSERT SVG and a new window with the title 'OPEN SVG' will pop up. Select a plane in your 3D work enviroment to work with. Go back to the 'OPEN SVG' window and click on the little gray folder to open up a new Finder Window and select your file. Your digital pattern is now imported in the 3D modeling software. Use the arrows to move the pattern on the work plane and click 'stop sketch' whenever it's in the right position.
If you want to design 3D pieces for your design, it's helpful to add some depth to your pattern. Select the face of the pattern and open the 'EXTRUDE' function, which you can find in the menu bar or under the drop down menu 'CREATE'. A new input window will pop up right next to your face in which you specify the distance to extrude. In the next step you'll learn how to model around your 3D pattern.
Step 4: 3D Sketching Around Extruded Pattern
After extruding our face, it is quite simple to sketch around the pattern and design pieces with the right proportions. First, click on your account name in the top right corner and open preferences. Then, click on Design in the left column and check the box right next to Allow 3D sketching of lines and splines. Save the settings by clicking the OK button.
Now, open the SKETCH menu, click on Spline and select the body you want to draw on. Start designing curves on and around your extruded pattern. You are always able to modify the curves later on. Whenever you are done, click stop sketch. Now you have a 3D sketch around your pattern which we are going to turn into a solid form in the next step.
Step 5: Create Solid Form and Manipulate Shape
After creating the sketch, you can turn the lines into an object. Select your sketch and click on Create Form in the upper menu. Then, open the pull down menu CREATE and select pipe. You can change the appearance by changing settings in the PIPE window on the right side. For example, a round pipe instead of a box or different end types. Save the settings by clicking OK.
Now you can edit individual faces, edge or vertices or select multiple ones and manipulate them together. Click on the face, edge or vertex and hold shift to add more. When right clicking, a menu opens next to the form in which you can choose edit form. Use the arrows and tools to manipulate the form and create the shape you want. When done, click Finish Form.
Use the drop down menu CREATE > mirror to mirror your design or right click on the body in the browser menu on the left side and copy/paste the body to get a copy. To adjust the size of your designs, go to the MODIFY > scale menu.
Step 6: Render, Combine and Print It
After finishing your designs, you can click on MODEL in the left corner and select RENDER in the drop down menu. This gives you a nice preview of how your printed design will look. Change the appearance and physicalmaterial in SETUP in order to match the material of your future print.
Before printing, I sketched half a loop right where the print is going to touch the fabric and choose the settings CREATE > Extrude > Operation > Cut. Now the design has a hole for sewing it onto the fabric. In the end, select all bodies of one print and combine by selecting MODIFY > Combine. Then click on File > 3D print and save the file to import it into your slicing software.
If you don't have a 3D printer at home, look for the closest FabLab, TechShop or Maker Space in your area. To get higher resolution prints in various materials and colors I recommend Shapeways. Since my design was very complex and I wanted a high quality print, I ordered my pieces from Shapeways. Shapeways uses the SLS (Selective laser sintering) technique in which a powder is melted by a laser and creates a solid form. This method allows for complex shapes and high accuracy.
Step 7: Sew Pieces Onto Dress
After all your pieces are printed, you can sew them onto your design. In case you can't stitch through the hole with a needle, take the wire of a so-called needle threader and create your own flexible needle.
In case you have anymore questions don't hesitate to ask. Have fun designing your own 3D pattern!
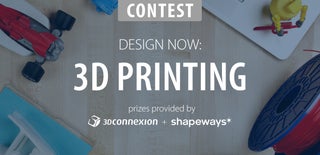
First Prize in the
Design Now: 3D Design Contest 2016