Introduction: Midcentury Style Walnut Coffee Table
I have a terrible propensity, like many makers, to adopt an attitude of "I could make that for a quarter the price".
Months later, after spending much more than the original price on niche tools, if I'm lucky, I'll get a finished article.
This is one of those stories, the fruition of a long standing promise to make a coffee table for my wife, which was unfulfilled for many years!
As usual, this is a rough guide, which ideally will serve as inspiration for similar projects, and is written informally in the first person. I hope to describe it in simple steps. There were no heavy specialist tools, no jointers, no thickness planers - just things that one would find in an average workshop... I think!
Supplies
Hardwood Planks
I used Walnut that was 210mm wide. As far aw I was concerened, within, reason, the wider the plank, the less work I would have to do on the table top, and the more chance I had of reasonably matching grains to form one homogenous surface.
Hardwood Dowels
I used 25mm Walnut Dowel
Wood Glue
I use Titebond Original
Screws
6 screws from your screw tin!
Finish
I used A combination of Dansh Oil for the body & a spray lacquer for the top.
Tools
- Sash Clamps Ideally... As many as you can get. I made improvised sash clamps out of regular clamps - Read on!
- Bandsaw - This is really just for the legs... you could get away with a handsaw here
- Jigsaw - For the table Top
- Hand Plane - Get theat tabletop nice and flat
- Sander - I use a random Orbit - with discs from 80-240.. and then some hand sanding with 320
- Steel Wool - Following application of coat of laqcuer.
Step 1: Design, Research & Drawing
See attached PDF for the exact plan.
I could see this table in my head, and didn't really need to get into a 3D design process...However, with splayed legs, and geometric, almost plectrum shaped tabletop. I genuinely needed a drawing that would assist me in setting it out on the timber at 1:1.
In my midcentury for dummies brain..
- Rich Grain - Check - Go with Walnut
- Splayed Diminishing Profiles - Check - Splay the legs - Profile the table top Edge
- Sharp...but not sharp - Rounded Profiles - Not too much
- Minimalist, Simple Joints - Check - no hint of visible fixing, and floating dowel connections.
I draw in autocad. As an architect, this has become an extension of my hand, and further, an extension of my brain, in that, in many cases I can simply resolve a plan and elevation in my head somewhere! However I truly suggest software like sketchup and tinkercad to assist with designing things like this under normal circumstances.
Furthermore, many furniture makers make scale models.. why not make a model out of card.
Even further furthermore, Ive no doubt that a serious artist would make a prototype first, maybe out of MDF or plywood. See it in reallife...and refine and adjust for the final version.
Thankfully, I had a birthday deadline coming up, so went with the attitude of "first thought = best thought"
One thing that I recommend, that you will not from my drawing. It is a design drawing, but it also serves as a cutting and quantity check. Walnut is expensive, I did not want to order more than I needed. You can see that I laid out the boards, and drew the pieces that I needed to cut on top of the boards. I also added lots of dimensions and setout points. I wanted a single drawing, that would stop me having to refer back to a computer, once i got to the workshop (ok its a glorified garden shed, but I like to call it a workshop!)
Attachments
Step 2: Loving the Timber & Some Prep
The Prep - Now this is a step you can skip.
I inherited two sash clamps, which had been left outside for a number of years. They needed serious wire-brush love and a lick of paint. I felt like my restoration of those clamps was part of this project, so I simply have to post a photo or two.
The Real Step
So, after that aside: As mentioned, this project does not use a thickness planer or jointer. How?
You've got to source decent dimensional Hardwood from somewhere. I have a good, but expensive hardwood supplier, I took a chance and ordered online, without even seeing the timber, due to covid times! As quick as selecting Walnut & ordering.
I was greeted in a few days with a tightly wrapped delivery.
4no. Planks 210mm x 1200mm, and a single dowel. Somewhere within that black plastic wrap, is my wifes coffee table I thought!!
After unwrapping, I was pleasantly surprised with the walnut. Really you should be looking at timber before buying it, so this was just good luck , but if its a choice between a project or no project... just do it!
At this point, study the boards, and start to place side by side in different configurations. I was looking for a couple of things.
1) I wasn't brave enough to express the beautiful knots - so I wished to avoid these.
2) Wished to avoid wastage of that precious walnut
3) want the separate grains to read harmoniously when butted together. Dark to Dark, Light to Light etc. This is where an experienced joiner who could go to view the timber, would certainly investigate book matching grains.
Step 3: TableTop : the Big Clampup & the Big Cleanup
1) Cut the timber to logical lengths for the tabletop.
2a) Loose lay and ensure happiness with the grain layout.
2b) Check the edges for trueness. They should perfectly flat, hold 2 pieces up against a light, and no light comes trhough. I had to run a plane over all the glued edges. One or 2 passes of a no. 5 plane... or any plane!
3) Glue, I use titebond original, I'm never shy on applying glue... to both sides. The whole tabletop relies on this.
4) Biscuits / Dowels - I'm of a mind, that while no harm, these would not be required on such a small tabletop, and really would be there to assist with alignment on glue up. With my limited skills, and lack of biscuit jointer I was happy to go without!
5) Clamp the hell out of it! - Sash or bar clamps and lots of them.. Unfortunately I only had 2 clamps of appropriate size.
6) Make clamp extenders if required. I cobbled together some clamp extenders from MDF strips, with blocks screwed on either end. These extended the limited range of my many cheap clamps.
7) Watch for the cupping!!! When the clamps are applied, there will be a matural propensity for the board to cup upwards off the surface. I put eveything I had in the shed on top, to counteract this. See the photos, It looked ridiculous.. but worked.
8) Clean off as much excess glue as is possible to do.
9) Wait one day!!
10) Unclamp - this is great fun.
11) Clean off as much glue as possible before getting to planing.
12) Use a straight edge to check for trueness and cupping. Plane by eye, with a very sharp plane. Keep checking for flatness. This is extremely satisfying, and provides an excellent upper arm workout!
Step 4: Cutting & Shaping the Tabletop
Using my dimensioned drawing, I pinpointed the setout point for the radius of my plectrum shape.
I used thin MDF with a screw on one end and a pencil hole in the other end to make a primitive compass.
This tabletop requires 3 arcs, which are filleted together with radiused corners.
The radiused corners, are marked up using a paint pot with just the right radius. I'm pretty certain that this is how everyone does radiused corners!!
After marking out - its time to cut out I cut out very carefully as close to the outside of the pencil mark as possible. Slow and steady. I started doing this on a small bandsaw, but it was an extremely awkward shape to manage on a small bandsaw table top.
In future I would have no issues using a jigsaw. Because the edges get routed on both sides... the cut does not have to be perfect. It could even withstand some splintering and tear-out.
Once cut, I sanded the edge to remove blade marks, and ensure perfect consistent relationship with the edge of the pencil mark.
If I was making more than one of these tables, I would certainly investigate making an MDF perfect template and cutting out the timber with a "copy bit" and router.
To make the diminishing edge, I cut the underside using a 45 degree chamfer bit all round. I did this in multiple patient passes. After this I used a fillet bit to put a small radius on the top edge in a single pass.
Lastly, I Set aside the table top and breathed a sigh of relief! All of that expensive walnut ... and no cockups!
Step 5: Cutting & Shaping the Legs & Frame
Almost There!
Cutting the Legs
1. Using the original drawing I made a template by carefully marking a plywood offcut, and cutting it out, again, very carefully, with a jigsaw.
2. Due to my thriftiness / economy of material, I decided to laminate the somewhat fat legs, using the thinner stock board. So for 3 legs, I needed to cut out 6 legs!
3. I matched / mirrored the grains into pairings.
4. I glued and clamped the hell out of them to form three single legs.
5. I cleaned up the rough sawcuts and glue run off with a plane.
6. I marked on the 3 legs, individually, the pencil marks for the taper cuts.
7. I cut these tapers roughly on bandsaw. Handsaw, could have done this, and possibly would have been better than my small underpowered bandsaw.
8. Cleaned up the taper cuts with a plane.
9. Rounded the leg corners in a small fillet with router. Remembering to not fillet the top of the legs on the side where thye meet the triangular frame. This is genuinely spokeshave territory, if you do not have a router.
10. Sand Sand Sand! - 120-320 Grit...fine for me. I Gave the legs a "lick of the orbital sander".120-240-320 Grit...fine for me.
Cutting the Frame
See 5th photo. I ripped three pieces of walnut to the correct width using the same technique. Bandsaw, and cleaned up with a plane.
Step 6: Assembly
This stage of a project is great. When all the messy and dusty stuff is done.
I did this in a funny way, but so simple that it worked.
1) Drew a perfect triangle.. By the way its really difficult to draw an equilateral triangle!! - You'll have to google how to do it.
2) From this perfect triangle, I dry layed out the cross members, and basically, "eyeball marked" the bridsmouth joint which receives the leg. I cut this on all 3 cross rails, at both ends, identically, and cleaned up the joints with a file.
3) I cut three identical chamfered walnut blocks, and glued and screwed them in place to hold the perfect equilateral triangle rail together.
4) Finally the fun part. I drilled and countersunk 2no. holes per chamfered block. Glued up the tops of the legs, and screwed them on using fairly hefty stainless steel screws. (from the screw tin!!)
5) So now I had an assembled frame, and just needed to fix the tabletop. To create the midcentury floating vibe, I let the tabletop float above the table frame, using 3no. 25mm dowels. These were cut to size at approximately 75mm.
6) Drill 25mm hole with forstner bit in top of the three legs at perfect center. I drilled the holes to the perfect depth of the forstner bit - which is as good a depth gauge as there is!
7) Fit the Dowels dry. My shop bought dowel was a perfectly satisfying fit.
8) Place the frame upside down on the coffee table top, and transfer the dowel positions. I drew a pencil mark the full way around each dowel.
9) Now drill the table top for the dowel...and DO NOT DRILL THROUGH IT... Oh and Double check that you are drilling the bottom and not the top.
10. Clunk...perfect dry fit. Now for the finishing.
Step 7: Finishing
Danish Oil
To say that watching Danish oil soak into walnut is satisfying, is an understatement. This was just so much fun. I use old T-shirts or vests to apply Danish oil, generally applying heavy, and wiping it in in a circular rubbing motion.
I let the Danish oil dry overnight between coats, and then left it for a week before attacking it with lacquer.
Lacquer
Because I have children, who do not know the meaning of coasters, I dared not, leave an oil only finish. However, I also really like the natural finish of oil - After a lot of soul searching, I masked off the body of the table using old towels, and applied a clear spray lacquer finish.
3 coats over 3 nights, with light rubbing of steel wool in between.
Finishing is an art that I know little about...when it starts to look good I usually just leave it alone, and avoid wet sanding and fine tuning. I've no doubt that one could spend many years learning the nuances of various finish types. But again lets face it, seeing insipid timber, turn into beautifully warm and rich materials, seeing grain pop and contrast...it's great fun!!
Step 8: Epilogue: Happy Wife
So the table is finished.
The finish is yet to be dented or scratched. My wife and I have religiously used coasters just incase, and it really pulls the room together.
I presented it to my wife for her birthday, rushing the finishing in the process, but alas I had a happy wife and a coffee table which will follow us everywhere.
My one lesson here, is to not be afraid of expensive hardwoods like walnut, what's the worst that can happen!
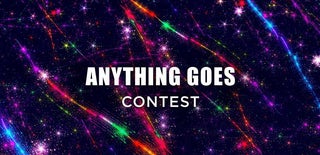
First Prize in the
Anything Goes Contest