Introduction: Mini Bench Power Supply
Ever since my first bench power supply project, I have wanted to build another one which would be much smaller and cheaper. The issue with the first one was that the total cost was over 70$ and it was overpowered for most of my applications. I wanted to have multiple power supplies on my bench so that I can power more than one project at a time but the cost and size didn't allow it.
So I decided to build a mini bench power supply. My main goal with this power supply was low cost, small size and visually appealing aesthetic. I wanted it to cost no more that $25. I wanted to have variable current and voltage settings. And I wanted a decent output power of ~ 30 Watts.
So follow me along as I take my goals and turn them into a reality. If you like my work, please support me by voting for me and by sharing with you like minded friends.
Follow me on other platforms for more news and content on upcoming projects
Facebook: Badar's Workshop
Instagram: Badar's Workshop
Youtube: Badar's Workshop
Step 1: Design and Testing
I started my design for the power supply with the selection of the switch mode power supply. I found 19 Volt 1.6 Amp laptop chargers in an electronics recycling center. They were small in size and good quality so they were perfect for my mini power supply.
I chose to use a buck converter with constant current and constant voltage modes as my regulator module. This was easily available and very low cost.
For the display, I first purchased the buck converter with the integrated volt/amp meter but the seven segment display was very dim so I scrapped that plan and bought a panel volt/amp meter.
Once I had all the parts, I mocked up my design and used an electronic load to perform some testing to see if the power supply can provide the output power I wanted.
After several hours under full load, the thermals were within safe limits so I went ahead with the design.
Step 2: Parts Required
You will need the following parts:
- 19V 1.6Amp Laptop Charger eBay
- 5A DC - DC Step Down Module CC CV AliExpress
- Panel Volt/Amp Meter AliExpress
- Banana Jack Binding Posts AliExpress
- IEC 320 C8 Panel Socket with Switch AliExpress
- 10K Potentiometer AliExpress
- 6mm MOS Heat Sink AliExpress
- Potentiometer Knobs AliExpress
- Terminal Connectors
- Wires
You will also need the 3D Printed and Laser Cut housing which we will talk about in the next step.
Step 3: Housing Design
For the housing, I wanted to use laser cut plywood as I have never used it before for any of my electronics projects. I also wanted to experiment with living hinges. That being said, I will attach my SolidWorks model and my CorelDraw laser cutter files. If you have access to both a 3D Printer and a laser cutter, you can follow what I did. Otherwise you can 3D Print the entire housing.
I used 1/8" plywood for the top and sides of the housing. I used laser cut living hinges to add some of the curvature. I 3D Printed the base as it was the easiest way to secure all the modules to the bottom and to make the power supply serviceable.
Something to keep in mind is that the tolerances on the Main Body model are set for laser cutter and not 3D Printing so you would need to experiment with those.
I experimented with the tolerances on all my files at least 2 to 3 times to get them just right. Your machines may vary hence you would need to experiment a little as well. Having the clips in the base and the cutouts for the push fit panel meter just right is a bit tricky so I would recommend testing them out first separately if possible.
Step 4: Housing Construction
Like I mentioned before, I started off the housing build the right way by first testing all my dimensions. Although it may be worth mentioning that I still ended up redoing the housing 3 times but the testing probably helped avoid redoing it more than three times.
I laser cut the pieces, cleaned them and sanded them. Then I used superglue to glue them together. Then I 3D Printed the base and I was done. Well all of that times three because I had one dimension wrong and them my living hinge was too weak. For the 3D Printed base I designed clips to hold everything in place and when you design clips, dimensions are very important so I ended up reprinting many times.
But once I was done, I tested the fit and despite some minor gaps here and there, I was happy with how it looked.
Step 5: Main Assembly
The assembly for builds like these is never too complicated. It just wiring everything together and making it fit.
Since I designed the housing to be as small as possible, everything will fit in very snugly. I also used connectors and terminals so that I can disassemble everything fairly easily. Its the attention to detail what counts when it comes to good design and build quality. Even though it is much easier to solder every wire, a more professional approach is properly sized connectors with solid crimped wires.
First step is to remove the potentiometers on the buck converter and replace it with jst connectors. Then solder some wires to the panel mount pots and crimp on the jst connectors. Put a heatsink on the voltage regulator.
Next step is to prepare the psu. Cut open its plastic case and desolder the input and output wires. Solder some wires on the input and output. Take note of the thickness of the wires as these would be the main current carrying wires hence we want to be appropriately sized.
Next, snap the two module in the base and crimp on the terminals for the binding post and the mains input. Screw in the connections based on the schematic.
Finally tuck everything in and close the case. A good way to do this is to keep the panel meter and the IEC connector popped out. Once you close the base, tuck in the wires and then push in the two modules.
Lastly, stick some non slip feet on the base so that it doesnt slip on your bench.
Step 6: Testing
Once I was done with assembly, I wanted to test it out but unfortunately I wired my voltage regulator in backwards and fried it. So I had to use my backup. Once I did that, I was able to vary the voltage and control the current as expected.
Testing the supply did reveal some flaws. One of the major flaw is that the voltage and current adjustment doesnt span the full range of the pots and thats because I am not using the full range of the driver. That just makes the adjustment very finicky. But I have some smaller value pots in the mail and will be testing with them to modify the circuit for my current and voltage range. I also have some knobs for the pots in the mail. For now I just 3D Printed some but will be getting the actual ones soon which will make it more ergonomic.
Testing also revealed that drawing more power than the power supply can handle results in a shutdown followed by a self reset, which is a neat feature to have as the power supply is smart enough not to damage itself if it is shorted out.
Step 7: Conclusion
Overall I am very happy with how it looks and I will be using it in the future to test it out in practical situations. This is just the first version and I will be working on it to make improvements. I would love to hear from your guys what you think about it. Maybe suggest areas where I can improve. My eventual goal is to turn this into a marketable product and would love some feedback.
Anyways, thank for following along and once again, please support my work by voting for me. All the help is highly appreciated.
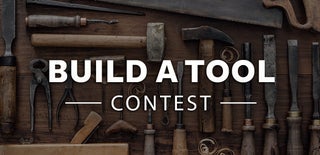
Participated in the
Build a Tool Contest