Introduction: Bookmatched Natural Edge Dining Room Table Top
In this Instructable I will explain how to bookmatching a pair of 2" poplar slab's into a live edge or natural edge dining room table top. This is a craze that his sweeping the high end decorating market and is replacing the traditional dining room table. There are several pit falls when working with a rough milled kiln dried slab like these and I will explain the best procedures I have found to get the flattest table with the best most durable finish.
Step 1: Bookmatching the Wood
Here I have started with two 2" poplar slabs that have been kiln dried and are successive cuts from the same tree in the same spot. The grain, the "wind break" the outer "live edge" are identical on the two facing pieces of wood. The trick here is to determine what are the two facing pieces. and which direction they are oriented.
Dimensioning the material can also be a challenge. Measuring an irregular piece of wood can be difficult but take your time, examine the grain, and try to find common elements that will book-match attractively. I tried using my table saw first and quickly determined (even as large a table saw as I have) that it really wasn't the best way to cut a slab of this size and weight. The skill saw a good straight edge or chalk line worked great.
Step 2: Gluing and Matching the Wood
Once cut, I used a jointer and (two people) to clean up the edge of the skill saw cut. and give me a good gluing surface. Many clamps both above and below were left on overnight to dry. I used a standard waterproof wood glue found at any hardware store. You will notice in the image that the two pieces are not lining up perfectly and not seen is a slight twist in the finished glue up... the difficult part was figuring out how to get the table top level.
Step 3: How Do You Get the Dang Thing Level?
My planer is only 16" and certainly will not accommodate a 40" wide piece of material. So... how do I get the top level? Sand it? no... YouTube!
On my assembly table I attached two rails and leveled them with the top just above the surface of my glued slabs. I then leveled the twisted slabs as best as I could and secured it in place with some cleats. Then I made a gantry slide of types for my router to ride in. Then with a box planer blade I made successive 3/4" cuts across the table top to level the surface.
Prior to sanding I found it necessary to fill all of the open "wounds" in the wood with a standard west systems epoxy. I simply floated/poured the epoxy in the gaps and cracks and I covered the underside with blue painters tape to keep the epoxy from running through. I have researched several builders of this type of top and I have found that all of them use an epoxy system to fill in the large gaps and splits in the wood. This process worked out great and made for a beautiful top in the end.
Step 4: Sanding - Staining and Finishing
Sand - Sand - Sand! That's the name of the game here. Some heavy sanding with some 80 Grit on the belt sander will get us ready for finish sanding! The difficult thing is trying to not snipe, roll, or dimple the wood with the sander.
After sanding to 320 grit I stained the poplar with a popular brand of stain - Special Walnut. The colors in the "rainbow" poplar really popped and the special walnut toned down some of the "green" color that newly cut poplar tends to have.
From there 7 coats of clear fast drying polyurethane. Typically one or two coats a day with some light 320 grit sanding in between. After a three day cure time I wet sanded the top with some 2000 grit paper and buffed it with a buffer and some polishing compound. The finished result looks great.
Thanks for taking the time to read my Instructable and please vote!
Kirk Lewellen
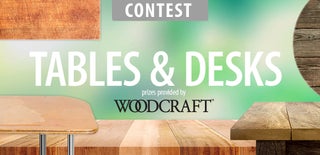
Participated in the
Tables and Desks Contest 2016