Introduction: No Carpentry Experience Needed: Plywood Chicken Coop
Literally the day before everything started shutting down in March, my husband Nate and I went to look at chicks. We ended up purchasing 4 and when we went to bring them home a week later, we had 5. We didn't have a coop or anything for outdoor living, but we figured we had time. Chicks can't go outside until they're fully feathered and the temperature at night is like in the 70s. So we had until May-June to get the coop ready.
It took us from March until mid-April to decide we were building the coop and run ourselves and to order the wood. Once we had the wood, it took us another a couple weeks to get started. May 2020 was pretty warm and the chicks could have gone out then, had we been ready. We ended up finishing the coop and run towards the end of June and literally the same day we were done, we evicted the chicks who were good size pullets at that point. The next day we brought home ducklings, currently they live with the chicks :-D
Anyway, we decided to build our own coop after pricing a variety of pre-fab ones and ones made my locals. We realized that if we did it ourselves, we could build a coop and the run for less than $500. The only reason the cost went up a bit higher was because I wanted polycarbonate panels for the roof of the run and those were about $16/each. Most prefab coops are between $300-500 and claim to fit 4-6 chickens when they are really only suitable for 1-2. You want 3-4 square feet of coop per bird, and 10 square feet of run per bird. Our coop is 4x8, so we could comfortably house 10+ chickens (depending on size).
Right now we have 4 chickens taking up residence in the top half of the coop and our 4 ducks are on the bottom (cayuga ducks don't roost).
So this Instructable shows you how to put together a plywood coop with absolutely no carpentry skills whatsoever. Our coop looks fairly uneven, but it is sturdy and secure and nothing is knocking it over. I've decide the theme for it is Hansel & Gretel/Baba Yaga and am slowly revamping it to look more like a whimsical old house. I'm on the hunt for a candy machine with stand that I can put outside the front of it and fill with scratch. I also plan to add a little porch and mailbox at some point. I think landscaping around the coop is a project for next spring.
Supplies
Power Tools
Drill & bits
Circular Saw
Jigsaw
Dremel
Lumber
6- 4x8 plywood sheets (we used pressure treated)
10- 2x4x12
12- 2x4x16
Roofing
Shingles
Roofing nails
Tar paper
Drip edge
Other Supplies
U-tacks or staple gun
Exterior screws (1", 1.5", 2", 3", 4")
Box cutter, scissors
Cinder blocks
Windows
Caulk
1/4" or 1/2" GAW hardware cloth
1-1.25" fender washers
Door hardware (hinges, locks)
Exterior latex/gloss paint
Step 1: Cuts!
Plywood
All of the plywood remained uncut except for 1 piece, which was cut in half to make the front and back of the coop.
2x4s
We ordered mostly 12' and 16' with the plan to cut them ourselves using a circular saw, and that's what we did.
For the walls/floor we cut eight 8' pieces and sixteen 4' pieces.
The roof was one 9' and six 3' pieces cut at an angle with a t-square
Step 2: Framing the Floor and Sides
Our coop is 8ft long, the sides are 4ft high (not including the roof), and 4ft wide. We went with these dimensions because plywood comes in 4x8 sheets and it just seemed like the easiest thing to do.
We used two 8ft and four 46" 2x4s to frame the floor. Starting from the inside, we connected the 46" pieces to the 8ft 2x4s to build the frame and then put the plywood on top and drilled it in. We used mostly 2-3" exterior screws because I wanted to be sure everything would stay together.
The sides were framed the exact same way, the "beams" face the inside of the coop.
I didn't get enough pictures of this process because I was drilling the screws in and Nate was holding the pieces steady.
Once we realized that nails are NEVER the way to go when building something, it took maybe an hour to get all floor and sides framed out.
Step 3: Floor Construction
Next we hauled the floor and sides over to the area we had started construction on the run. Nate dug out some of the soil to make the ground more even and then we put a bunch of cinder blocks we got off CraigsList to be the base of the coop. Even though we used all pressure treated wood, we wanted to limit how much wood came into contact with the ground.
We put the framed floor on top of the cinder blocks and then used vinyl flooring from Home Depot to cover the plywood. HD has it on a roll and will cut to size, kind of, I wanted a little bit bigger than 4x8 so I ended up buying like 12x6 because the rolls are 12' long. This cost about $25.
So we rolled the flooring onto the plywood and hammered tacks to keep the flooring in place. This could also have been done with a staple gun, but we didn't have one at the time. After the flooring was secure, I trimmed the edges.
Step 4: Sides Construction
The sides were framed and built the same way was the floor, with the help of my husband (who held each side in place) I drilled pilot holes and then screws into various places along the 2x4s that would connect the floor with the walls. I probably put 3 screws every 2 feet and then repeated with the second side. We also added a couple 2x4s across the top to hold the sides together while we worked.
Step 5: Roof Construction Part 1
Because it's New England and we get a decent amount of snow, I really wanted the roof the coop and run to be pitched so that we wouldn't have to worry about snow piling up and causing a cave in.
We also wanted the roof pitched enough so that I could walk into the coop without having to crouch too much. I don't remember the exact measurements, I want to say the rafters are 3', but the roof is high enough that I can just about stand up straight in it (I'm 5' tall).
This part was also hard to get pictures of as it took both my husband and myself to hold pieces so we could drill and attach.
Because we've literally never built anything from wood before in our lives, our measurements and cuts were not 100% perfect and things were off. So about halfway through putting the rafters up we realized the sides were leaning more than we wanted, so we ended up putting the back piece of plywood onto the coop to keep things more stable.
After all the rafters were put up, we installed hardware cloth over the front and back triangles of the rafters. The hardware cloth (attached with screws and washers) is for predator protection and the open triangles are for ventilation.
Coop ventilation is extremely important when building a chicken coop. Ventilation remotes dampness, humidity, allows airflow and can prevent frostbite and illness. Appropriate ventilation is at the top of the coop, above where the chickens roost (airflow should not be directly on the chickens). It is also important to make sure the coop is free of drafts.
Step 6: Roof Construction Part 2
After the rafters were up, Nate and I worked to get the plywood that would be our roof up onto the coop. This was very difficult with just the two of us, with a third person it would have been much easier.
Basically what we ended up doing was, Nate held the plywood in place as much as he could and I climbed up a ladder to drill the plywood in place. In hindsight, self-drilling screws would have been perfect for this task.
Step 7: Roof Shingling
We ultimately decided to shingle our coop roof (with no prior experience whatsoever) after snagging about 20 packages of shingling from a person on FB marketplace that was getting rid of it all. We were also able to get a piece of drip edge and some tar paper from another person, all we had to buy was an extra piece of drip edge and roofing nails.
Nate watched a YouTube video on roofing and while I made a run to Harbor Freight for more caulk, he had half the roof shingled by the time I got back.
He started attaching the drip edge onto the sides of the plywood and then stapling the tar paper. The tar paper happened to have measurements on it, so Nate knew exactly where to place the shingles and worked from the bottom up.
For the very top of the roof he took shingles and folded them over the gap. The whole roof probably took Nate two hours to do and it came out amazing. No water leakage, no issues, and looks great.
I think 3-4 packages of shingling were used, so we paid it forward and gave the rest of the unused materials to other chicken coop builders.
Step 8: Windows!
While I was at work one day, Nate installed windows in the coop. He measured the old windows we had against the plywood and traced an outline. Then he used a drill to cut out holes in the plywood so that he could use the jigsaw to cut squares out for the windows. Then he drilled one window to the outside of the coop and a second window inside, so each window is actually made of 2 (4 windows were used in total).
I used silicone caulk to seal the edges of the windows both inside and out, to prevent water leakage and drafts. I also scraped the old paint and any chipped areas and re-glazed the windows (which took forever).
Step 9: Doors & Ramps!
Nate used the drill and jigsaw to cut a circular hole out of the back piece of plywood and added an exterior door (the third pic shows the door originally on the inside, we realized this was not useful and put it on the outside of the coop) that lifts up and hooks in so that the girls can come and go during the day. When it gets dark the girls put themselves away and we go out to the run to close it. Their run is fully enclosed, but this is just a little added security.
Plywood scraps were used to make a ramp inside the coop for the chickens to get up to their roosting bars (made out of 2x4 scraps) and for a ramp outside the coop for the chickens to get in and out.
Ramps inside the coop aren't really necessary, but we have one chicken (Angela, a Prairie Bluebell Egger) who was a little wobbly and had some balance issues as a chick and though she's absolutely fine now (Poultridrench is amazing!) we were initially worried she wouldn't be able to get up to the roosting bars (she can).
After we built all the ramps and roosting bars, we added our main door! Which to start was just a piece of plywood attached with door hinges. We also added a handle and a barrel lock.
Step 10: Paint!
The inside of the coop is currently light pink and lime green. The pink was oops paint from Home Depot and the lime was meant to be a trim color for our purple coop.
Both inside and out is exterior latex paint. Although I do not recommend a light paint color for coop interiors, chickens are messy and it shows on the walls.
I'm planning to use vinyl flooring on the entire interior of our duck house when the time comes.
Step 11: Just Add Chickens
After the paint dried we added shavings for the flooring and then quickly switched to washed construction sand. There's now a 4-6" layer of sand in our coop and run which makes cleaning so much easier.
When the chicks hit 20 weeks old we added a nesting box, another free Craigs List find. All we needed to do was assemble the boxes (2-in-1) and drill inside the coop to hang.
Step 12: Important Things to Remember
1. Ventilation is necessary. Make sure you have cross-ventilation. Put your ventilation at the top of the coop, well above where your chickens will roost. You do not want air blowing on them.
2. Block all drafts. This means checking the doors, windows, edges where wood meet etc. make sure there are no drafts that can get to your chickens. Drafts can cause illness and frostbite, it also makes it harder for chickens to stay insulated. (Coops do not need added insulation).
3. Make sure there are no holes etc. for pests or predators to get in.
4. Chicken wire keeps chickens in, it does not keep predators out. Do not waste your time or money with chicken wire.
5. You will likely still need to winterize your coop. I used 3mm plastic sheeting around the run and bottom half of the coop triangles.
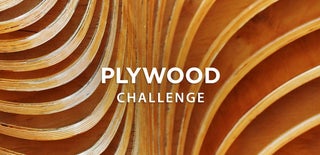
Participated in the
Plywood Challenge