Introduction: Tim's Hybrid Harmonic Drive
As usual every thing I make is on a budget.
I have the Idea for a new project, but it will need a few motors for it.
The type of motors I need are quite expensive.
- They need encoders to keep track of there position.
- They need a good range of speed.
- They need quite a bit of power (Strength).
- A gearbox that has accurate positioning.
The type needed is a Harmonic Drive, this dive is quite simple, but usually needs many bearings.
- The most common type, also needs a flexible part.
- There are many designs on the internet, but most still use many steel bearings.
The cost comes with the bearings and flexible component.
What I have designed is nothing new, if you search for harmonic drives on the internet, you will probably find something very similar, all metal of course and expensive.
I Found a nice little motor on eBay with an encoder very cheap. about 3 quid (£).
So using this I have designed a Hybrid Harmonic Dive.
- All printed with PLA on my 3D Printer (apart from the motor of course)
- Has only one Bearing, Printed PLA.
- The only bought out parts are: The Motor, A 3mm Diameter x 31mm polished bar and a few M1.7 x 6mm screws.
Supplies
- One fc130sa Mabuchi Motor with Encoder.
- Sixteen M1.7x6mm Self tapping screws.
- One 3mm diameter polished steel rod, length 31mm.
A 3D Printer is required to print the parts for the Gearbox.
As usual can not upload all my STL files here. (there is a 25Mb limit)
- Three of the files could not be uploaded here.
- I have done a Zip of All the files and put them on my Google Drive: Tims_Hybrid_Hamonic_Drive.zip
- The reason my STL files are large: Is because I fillet the sharp edges, I think it makes a better looking print.
Step 1: Why Is It Hybrid
There are lots of designs for Harmonic Drives in the internet
The basic principle of a Harmonic Drive is:
- You have two parts of the same length, each with a row of teeth along there length.
- The teeth run the full length of each part.
- One has less teeth than the other.
- The two parts are placed side by side.
- A toothed wheel that spans both parts runs along the teeth of the two parts.
- Because one part has less teeth than the other, it will have to move to keep it's teeth aligned with the other as the toothed wheel travels along its length.
Why mine is a Hybrid:
- The simplest version of a harmonic has the two parts in the form of rings, one inside the other. The inner ring is smaller and flexible, to the rigid outer drive. The teeth are meshed together by making the inner ring oval. As the oval shape is rotated, the inner ring rotates also because it has fewer teeth.
- I am making mine out of PLA, all plastic goes brittle over time, PLA goes brittle quite quickly. So a flexible ring is out of the question.
- Another way to do it is to have the two rings of teeth side by side and have an other set of floating teeth to keep the two rings of teeth aligned.
- To keep everything central lets have three.
- Placing a drive gear in the centre of these three floating gears enables us to drive the floating gears.
- This gives us a planetary gear setup. (second type of gear)
- Because the motor comes with a worm drive on it. The drive gear is driven by a worm gear. (third type of gear)
So from Input to Output, three types of gear are used. That's why I have called it a hybrid.
By using the planetary (floating) gears, there has been no need to use any bearings.
- The Floating Harmonic Teeth are held against the outer ring using a pressure ring in the centre.
The reason for different types of Gears is: To increase the ratio between the Motor revolutions and the Output Drive.
- The Motor is small and week, but has a high revolution speed.
- By reducing the speed of the revolutions we can get more power to drive something.
Step 2: Strength
I have attached an arm with a marker 300mm from the centre.
Holding the main body still and and attaching a Newton scale at the 300mm marker I get the following results:
- With 10 volts the motor stalls at 6N.
- With 13 volts the motor stalls at 8N.
- With 16 volts the motor stalls at 10N.
Just divide 300 by 1000 multiply that by a value should give you N/m.
My scale only goes up to 10N. I assume the strength will increase proportional to the voltage.
The motor will take about 24 volt.
Step 3: Pre-Assembly (Worm Gear)
Although the 3D printer will print complicated shapes, there are some things that is should be taken into account.
- One being, most printers have a 0.4mm nozzle.
- I am assuming it will be printed with a 0.4mm nozzle.
Although I have done my best to draw the teeth of the worm drive, when spliced and printed (FFF), some averages may get done.
So once the worm drive was printed, the hole needs reaming out to be a perfect fit on the polished 3mm diameter bar I will be using as a spindle.
Once the Worm Drive is a good fit on the round bar, I place a good length of the bar in a vice and place the Worm Drive on it.
I then take the Motor with Power attached, and bed the Worm Thread into the Worm Drive at high speed.
The friction between the Worm Thread and the Worm Drive will heat the plastic making it soft, the plastic should then mould it self to the perfect shape.
Good judgment is when to stop. There may be some spinach debris in between the teeth, pluck them out.
Step 4: Pre-Assembly (Bearing)
When something is converted to an STL File, It is divided up into triangles to create a mesh.
- The file for the bearings looks like I have shown.
- Then it goes through the slicer, making some averages.
- Then there is the printer tolerances.
- It hasn't got much chance at this size to be prefect.
So as we did with the Worm Drive, we need to bed them in.
- It is easier to bed them in without any other components fitted.
- This will mean a dismantle after doing the bedding in.
74 Roller Bearings are needed, more will fit but don't.
- I have done two sizes, It was designed for 4mm diameter bearings, "Roller_Bearing_R20.stl".
- As the shape of them printed, is not the best, I have reduced them to 3.8mm dimeter "Roller_Bearing_R19.stl".
- Use the "Roller_Bearing_R19.stl".
Assemble as shown:
- Fit the Output Drive inside the Outer Main.
- Fit the bearings between the two as shown, one one way, then the next the other way.
- When all bearings are in place, do a check to make sure of there orientation.
- Place the Bearing Retainer over the bearings.
- Fit the screws, don't make the tight, just screw them down so that the bearings will not fall out.
- Rotate the Output Drive several times to settle the bearings.
- Tighten the screws a little so that you can still rotate Output Drive.
The Output Drive will need spinning fairly quickly to get the bearings to warm up.
- I use a small piece of wood dowel in one of the holes to spin the Output Drive.
- Keep spinning and tightening the screws until the Bearing Retainer is all the way home.
- Spin in both directions until the Output Drive spins freely.
Disassemble.
- Keep your bearings safe, if you loose some you will have to bed-in new ones in again.
Step 5: Spindle
As small spindle is required for the Worm Drive.
- It needs to be a smooth polished spindle, to minimize friction.
- I have used an old 3mm bar I salvaged from an old CD drive.
- The spindle should be 31mm long +0 -1.
Step 6: Assembly [Spindle]
Fit the spindle into the Spindle Mount.
Step 7: Assembly [Worm Drive]
Fit Worm Drive onto Spindle
Step 8: Assembly [Spindle Mount]
Attach Spindle Mount to Outer Main with 3 screws.
Step 9: Assembly [Motor]
Fit Motor into the Motor Mount.
- Make sure the correct orientation.
Step 10: Assembly [Motor Mount]
Secure the Motor Mount with Motor using 4 screws to the Outer Main.
- You may want to check that the motor runs freely at this point.
- If it sounds a bit stiff, let it bed in a little more.
- You can put pressure on the spindle on the opposite side to help bed it in.
Step 11: Assembly [Planetary Gears]
At this stage we need to add some alignment marks to make sure the gears are aligned correctly.
- On the Gear side, the side you can see both sets of teeth.
- Place a mark on back side of the spoke that lines up with a tooth.
- Now on the side you have just made that mark, the side you can only see one set of teeth.
- Place a mark opposite.
- Do this for the other two Planetary Gears.
The Outer Main also needs some marks.
- It needs thee marks evenly spaced.
- Easiest way is mark in between the teeth that lie opposite three of the spokes.
Fit the three Planetary Gears inside the Outer Main so that all Marks line up through the middle.
- You may have to rotate the Worm Drive a little to line them up perfectly.
Once aligned, place the Pressure Ring in the centre between the three Planetary Gears.
- It's a fairly tight fit.
- It needs to be perfectly aligned to fit.
It is a good idea at this point to try some power to the Motor, to check all moves freely.
Step 12: Assembly [Output Drive]
We can now finish it of by fitting the Output Plate and Bearings.
- We fit everything the same way we did for beading in the bearings.
- Once the Bearing Retainer is in Place we should be all good to go.
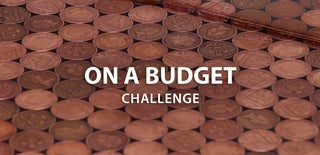
Participated in the
On a Budget Challenge