Introduction: Tim's Miniature Drill Press
Some times when making small project, you need small tools make them.
This is my Miniature Drill Press I designed and made using my 3D Printer.
I use it for drilling tiny holes in projects I make.
This Instructable is just for the Miniature Pedestal Drill, I assume you will have an adequate DC power supply for it.
Supplies
A 3D Printer is required to make this project.
- The whole thing is 3D Printed apart from the bought-out Items.
Bought-Out Items
- One DC Motor: The one I have with 12 volts it spins 28000 RPM. the speed and voltage is not critical, but it's physical size matters as the 3D printed Parts are designed for a certain type.
- One Speed controller: The speed controller I got from eBay. There are many DC Motor Speed Controllers, the one I have can handle 3 Amps, and is like the one shown.
- One Collet Chuk: Make sure the Collet Chuck you get has the correct hole size to fit the motor you have. Be carful there are Metric and Imperial Sizes.
- Collets: You may not have to get these separately, sometimes you can get a good deal when buying the Chuck. Remember there is Imperial and Metric versions of these. Not just the Chuck they fit, but also the drill bits they hold.
- Twenty Seven Self Tapping Screws: M3 X 10 mm long.
- Some cable and a Connector for the Power Supply. Ideally the Connector needs to match the DC Power supply you have.
- Two 3mm diameter linear bars 93mm long.
Attached is the STL files for the printed parts:
Attachments
Step 1: The Motor and Collet Chuck
The motor needs to be the size shown.
- It is a common size, so it should not be hard to find one similar.
- I have marked crucial dimensions with red letters.
A: This dimension is the diameter of the spindle. It is critical that the arbour of the Collet chuck matches this diameter.
B and C: These are the diameters of the bearing mounts, 10mm is what my Drill Press is deigned for.
D: This is the overall length of the motor body. 37.8mm is what my Drill Press is deigned for.
E: This is the overall Diameter of the motor body. 27.7mm is what my Drill Press is deigned for.
F: This is the hole centres for the Motor mounting screws. 16mm is what my Drill Press is deigned for.
The electrical parameters do not need to be exact.
- Mine with 12 Volts runs at 28000 RPM. (Half this speed should be sufficient)
Note!
When getting a Collet set, a drill size that should be a must is 1/8 inch (3.175mm).
- There are many drill bit sets with a 1/8 inch shank.
- Its a standard size for PCB Drill bits and they cam be acquired quite cheep.
When you have your Motor and Collet Chuck assemble them if needed and attach a reasonable length of cable to the Motor Terminals.
Step 2: Assembly [Motor Bracket]
Using two M2.6x0.45 Screws Fit the Motor to the Motor Bracket as shown.
Step 3: Assembly [Slide]
Using four M3 Self Tapping Screws, attach the Slide to the Motor Bracket.
Step 4: Assembly [Rack]
Using two M3 Self Tapping Screws, attach the Rack to the Slide.
Step 5: Assembly [Support Frame]
Using four M3 Self Tapping Screws, attach the Support Frame to the Base.
Step 6: Assembly [Side Braces]
Using six M3 Self Tapping Screws (3 in each), attach the two Side Braces to the Base and the Support Frame.
- There is a Right and Left Side Brace.
- Be sure to put the them on the correct sides, as shown.
Step 7: Assembly [Pinion Shaft]
Slide the M8 Washer onto the Pinion Shaft.
- From the side shown, slide the Pinion Shaft into the holes shown.
- Using one M3 Self Tapping Screw, secure the Shaft Cap to the end of the Pinion Shaft.
Step 8: Assembly [Pinion and Wheel]
Slide the Pinion Wheel (gear) onto the Pinion Shaft.
Slide the Wheel (Three spoke lever) onto the Pinion Shaft.
- Note that the square shape of the Pinion Shaft and the square hole of the wheel have two corners removed for screws.
- The corners need to be aligned together to form two holes for the fixing screws.
Using two M3 Self Tapping Screws and M3 Washers, secure the wheel in place.
- The washers are needed to reduce the length of the screw going into the connection.
- If the screws go in too far the shaft will not turn.
Step 9: Assembly [Speed Controller Brackets]
Using four M3 Self Tapping Screws, secure the two Speed Controller Brackets in place.
- Both Speed Controller Brackets are the same.
- The Speed Controller Brackets will only fit one way.
Step 10: Assembly [Speed Controller]
Using four M3 Self Tapping Screws, secure the Speed Controller in place.
- I am using four M3 Washers to pack off the the PCB from the Speed Controller Brackets, as I have soldered my cables direct to the circuit board underneath.
- Packing off the PCB also gives room for any terminals that are pocking through the PCB.
Step 11: Assembly [Motor and Slide]
Using two 3mm diameter smooth rods, 93mm long. Attach the motor and slide to the Support Frame.
- I find it best to attach the side that does not have the Rack first.
- The Motor and Slide assembly will swing into place for the second rod.
Once the two rods are in place, keep them there by placing a Bar Cap on each.
- These just clip into place.
Step 12: Work Support
I have made some "V" blocks to aid drilling of round objects.
Also I have made a large block with various shaped sides to aid drilling.
Step 13: The Circuit
The circuit is straight forward.
The Speed Controller has:
- Power In. To this I connected a Connector to match my power supply.
- Power Out. The Motor connects to the Output.
The speed is controlled by the Potentiometer.
- Mine came with a knob, but I found better control without the knob on.
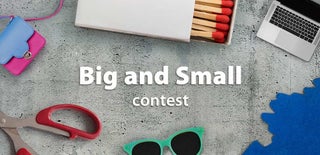
Second Prize in the
Big and Small Contest