Introduction: Wall Cabinet With Glue and Joinery
I have always wished to design and make furniture pieces that are uniquely meaningful and beautiful for our home. I was a power tool phobia who never even used a drill, until about 6 months ago, my wish became irresistible, so I took a 16 week woodworking class at our local college which happened to have one of the best programs in the country, and made this cabinet which I designed from scratch.
This wall cabinet is assembled entirely with glue and joinery. The only places screws are used is on the back panel to allow for wood expansion, and on the door hinges.
It's made of our local Torrey Pine: "the rarest pine species in the United States, an endangered species growing only in San Diego County and on one of the Channel Islands"-Wikipedia.
The design is inspired by early American jelly cupboards and cabinets. We wanted an open cabinet with shelves so we can see and appreciate those pretty bowls and potteries we love. We also love the charming country style of those primitive furniture pieces.
Step 1: Design and Materials
The college has an amazing urban forestry program, which works closely with the communities of San Diego County to obtain trees for milling. Felled trees would most probably end up in landfills. Instead, they are delivered or picked up and brought to the campus and turned into quality lumber for woodworking classes!
Materials:
- 15 board feet of Wood: Torrey Pine has a special spot in our heart because we love hiking at the Torrey Pines State Reserve. So I chose Torrey Pine (and you can't buy it anywhere!) and some gorgeous purple poplar.
- Wood glue: Please see Step 3 for some tips on gluing, Elmers or Titebond, both work great
- Clamps: very important in every step of gluing!
- Door hinges, knobs, small magnet, and small screws
- Wood finishing such as Tung Oil Finish
- Glass: I decided to leave out the glass, but designed it so that 5x7 photo frame glass can fit into each of the 4 openings if we do want glass in the future.
When I googled early American wall cupboard, I got a lot of inspiring images, which I used to come up with the design. It also fits the space we have.
Please don't feel you need all the fancy tools to built it! If you start with finished lumber and some trim, you can make this with just a table saw and a jig saw for the curved part. But this tutorial will cover steps starting with rough sawn lumber.
Step 2: From Urban Wood to Finished Lumber
The wood I got from our urban forestry program is rough sawn lumber, which needs to be turned into finished lumber for clean joinery and glue to work nicely. Feel free to skip this step if you are using finished lumber.
Here's my gorgeous Torrey Pine and Poplar, which adds to about 15 board feet. After some planning and fitting all the elements of the cabinet onto these boards, they were cut with a jig saw into smaller pieces.
First they went on the jointer a few times to create a flat face, then through the surfacer with the flat face down. The surfacer (planer) takes off 1/32" thickness per pass, until the desired thickness is achieved.
Then they go back to the jointer for edge jointing - creating a straight and square edge, ready for our table saw next!
Step 3: Cut , Dry Fit & Tips on Gluing
Since almost the whole piece is assembled with glue, here are a few tips on wood gluing-
- make sure the two surfaces are really clean and smooth for a better bond
- use clamps!
- once you tighten the clamps, make sure to clean off the excess glue using a scraper.
- let the glue dry for at least an hour before removing clamps
- when gluing end grain to another surface, use dowels or biscuits with glue for a stronger joint
The Top and bottom pieces were cut to size on the table saw first. Then the rabbet and blind dado joints were cut with a router. Since the router cuts in a circular motion, the end of the blind dado joints were cut square using a 1/2" chisel.
The molding around the sides and front were also cut on the router table. Since I can't cut and take photos at the same time, some of the photos are of my lovely classmates working on the same machine =)
The 2 side pieces were cut on the table saw first, then on a band saw to cut the curved part. The rabbet were cut on the router table as well.
If you don't have a router, there are table saw blades that will cut dado and rabbet. You can get pre-made moldings to glue around the edges also.
After the shelves are cut, all the pieces are dry fitted (without glue yet), and the back piece is measured.It's a good practice to use the plan as a guide but use actual measurements as you start building to make sure all pieces fit tightly.
To make the back piece, a 1" thick piece of torrey pine is re-saw on the band saw into two 0.5"+- pieces, and smoothed in the surfacer.
Then they are edge glued together.
Step 4: Door and Face Frame
Cut the rails and stiles for the face frame and door frame on the table saw.
As mentioned in the gluing tips (step 3) , when gluing end grain to edge grain here, dowels are used to give a stronger joint.
After the glue dries, round the inside edges on the front, and create the rabbet on the back on a router table. Optional: create a mitered look with a chisel on the inside corners.
The face frame is made slightly larger than needed. Put it on top of the dry fit cabinet, trace with a sharp pencil the sides, and sand the face frame on a belt sander to match the pencil line.
The grid pieces for the door glass was cut on the router table, then mitered and glued where they cross one another. They were also cut a little larger than needed, so they can be trimmed to fit tightly into the door frame, with some glue on all the flat ends.
Step 5: Hardwares, Assemble and Finish
At the top of the back panel is the piece with key hole(cut with a drill and router) for hanging.
Glue all pieces, clamp where needed.
The back panel is the only place where small screws are used to allow wood movement - 1/8" every 8" across the face grain.
Mark the hinges on the flush inset door and face frame, and cut out the thickness of the plates with a chisel. Attach hinges to door and face frame with screws.
I decided to paint the hinges and door knob blue for a bit of color. Attach the door knob, drill a hole on the shelf wher the screw of the knob is and glue a magnet inside to hold the door closed.
The entire piece was sanded with the slurry method : sand with 220 -400 grit sand paper and create a oil + fine saw
dust slurry mixture, which fill in the pores of the wood and create a marble like finish after doing it daily for 7 days. Honestly I did 3 coats and was happy with it already!
And now we can put some pretty things in it!
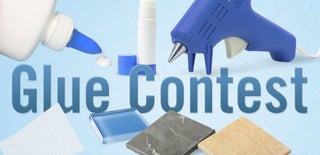
Participated in the
Glue Contest