Introduction: World Map End Table | Made With a Cricut!
If you’ve ever peeked into the world of vinyl crafting, you already know that those beautiful round wood welcome signs are a big hit among makers and homeowners. There are entire businesses dedicated to just round wood signs, with one of our favorites being those by Wood Love Signs like this one.
Having recently procured a Cricut Maker, I was, of course eager to make one as well—and did. But then the idea hit me: what if we used this same initial technique and remixed it into a cool piece of graphic furniture?
I’ve been slowly incorporating travel-themed decor into the master bedroom (in a tasteful way, of course), and so I quickly knew that the graphic end table I wanted to create had to feature a world map.
Using similar techniques to the wood signs and adding in our expertise in resin pouring, we created this amazing World Map End Table, which now proudly sits in the master bedroom next to my reading chair.
Supplies
(Amazon Links = Affiliate Links)
Cricut (or other vinyl cutting machine): https://amzn.to/33NngKm
Wood round (we get the 17.75" ones at Home Depot)
Power sander - https://amzn.to/37eG5I2
220 grit sand paper - https://amzn.to/2SWEs9w
Plastic drop cloth - https://amzn.to/2tqbk1c
Wood stain (we used Early American)- https://amzn.to/3dwEm1L
Water-based polycrylic - https://amzn.to/37evvRo
Painter’s tape - https://amzn.to/3injICg
Level - https://amzn.to/36Zzj60
Resin - https://amzn.to/35ZnHi6
Mixing cups - https://amzn.to/2RiDRxq
Mixing sticks - https://amzn.to/2tgKatK
Gloves - https://amzn.to/2TuHzH1
Trowel/Spreader - https://amzn.to/3j686na
Heat gun - https://amzn.to/2R3IbC6
Butane torch - https://amzn.to/2Rrk2Ei + https://amzn.to/3kx7Sri
Removable vinyl, white - https://amzn.to/37eF2rA
Standard grip transfer tape - https://amzn.to/3lMpgbg
Double sided tape - https://amzn.to/341y0o0
Moving blanket - https://amzn.to/3o7QQ4W
Drill - https://amzn.to/375oC1y
Screwdriver - https://amzn.to/2QYURdk
Spray paint - https://amzn.to/37euHMm
Box Cutter/Utility Knife - https://amzn.to/2DSSxAi
Table legs of choice
Computer
Paint stripper (optional)
Affiliate Notification
We are a participant in the Amazon Services LLC Associates Program, an affiliate advertising program designed to provide a means for us to earn fees by linking to Amazon.com and affiliated sites. You don't pay anything extra for the items you buy - we just get credit for referring you!
Step 1: Prep the Wood Round
This is by far the most important step in the success of your project. Without the proper prep work on the wood round, your resin may react negatively, or your vinyl may not stick well. Don’t skimp on the prep!
Gather the following materials: wood round, power sander, sand paper, cloth, stain, and water-based polycrylic.
Follow these steps:
1. Buy or cut out a round piece of wood. We bought this 17.75” wood round from Home Depot.
2. Sand the front, back and sides of the wood round until smooth.
3. Remove dust from sanding using a cloth.
4. Stain the wood round (front, sides and back) using the stain of your choice.
5. Let the stain dry and cure for a full 24 hours.
6. Apply a thin coat of water-based polycrylic to the front and sides of your wood round.
Tip: Watch for drips on the underside.
7. Follow the directions on your sealer for recoating times. We did three layers, with 2 hours between each layer, sanding with 220 grit sand paper before the final (third) layer.
8. Let the Polycrylic cure for a full 24 hours before proceeding to the resin seal coat.
Step 2: Pour Resin Seal Coat
Once your polycrylic is fully cured, it’s time to move on to the seal coat for the resin!
For a little background on why we’re doing this: When you pour resin on wood, tiny bubbles tend to appear in the resin. To prevent these from trying to come up underneath the vinyl, we’re going to do a seal coat with resin first. A seal coat is a thin layer of resin used to—you guessed it—seal off the wood.
Gather the following materials: painter’s tape, level, resin, mixing cup, plastic drop cloth, mixing stick, trowel, heat gun, and butane torch.
Follow these steps:
1. Use painter’s tape to seal off the edges on the underside of your wood round. This is to catch drips and make it easier to have a clean underside on your project.
Tip: Be very precise and ensure that the tape is not sticking out from the underneath of your wood round; that will cause an unsightly ridge when you pour your resin.
2. Find a good spot where you can pour. Keep in mind the temperature sensitivity of your resin, as well as putting down a plastic drop cloth to protect the surface of your area.
3. Elevate and level your project on the surface where you will pour. Check for level from numerous directions.
4. Mix your resin according to the instructions on your particular brand.
5. Pour a thin layer of resin and heat it with the heat gun to give it extra viscosity.
6. Spread the resin out with the trowel. Be sure that you cover all edges and have no bare spots.
7. Use the torch to pop bubbles as they appear.
8. Babysit your project for the first 30-45 minutes to watch for bubbles.
9. Cover and let resin fully cure. For the ProMarine resin that we used, we gave it three full days.
Step 3: Create Vinyl Graphic
While you’re resin is curing, it’s time to work on your vinyl graphic! We used a Cricut to cut our vinyl, but the steps below will apply to most cutting machines.
Before we dive in, a note on why we chose removable vinyl (versus permanent or iron-on/HTV): We tried iron-in vinyl initially, but the size of the graphic an slight unevenness of the wood, even with sanding, didn’t enable the graphic to adhere fully to the bare wood (which is when you’d need to apply the iron-on graphic). If you use permanent vinyl, you’ll have no room for error/repositioning once the graphic hits the cured resin. Removable vinyl is great, as you’ll be sealing over it with resin anyway, so there’s no need to worry about the graphic peeling over time.
Gather the following materials: computer, vinyl cutting machine and needed accessories (mat, etc.), and removable adhesive vinyl.
Follow these steps:
1. Find a world map graphic that you like. We chose and purchased THIS ONE from Alamy.com.
2. Unless your cutting machine can handle a graphic of the size of your wood round, you’ll need to slice it into sections. We used Photoshop to slice our world map graphic into three pieces.
3. Save the images as a PNG so you have a transparent background.
4. Upload the graphic into the program you use to control your cutting machine. For Cricut users, that will be Design Space.
5. Resize your graphics, if needed, to fit within the dimensions of your wood round.
6. Have the machine cut the graphics out of removable vinyl.
7. Weed the excess vinyl.
Step 4: Apply Vinyl Graphic to Wood Round
If you have a graphic that has connecting lines across it (like ours with the flight path), this step will be the most complicated of all. Take your time and go slowly.
Gather the following materials: weeded vinyl cutouts, wood round, transfer tape, and double sided tape.
Follow these steps:
1. If your graphic has connecting lines like the flight paths in ours, it’s best to connect the graphics before you try to apply them.
Tip: We lifted small parts of the vinyl from the backing and connected them, using a spare wood round as a guide for size and placement.
2. Tape the graphics in place using double-sided tape on the back of the backing paper to ensure that the pieces didn’t move as we were applying the transfer tape.
3. Apply transfer tape to the top of the vinyl graphic, ensuring that it lays flat and doesn’t have any bubbles or wrinkles.
Tip: To see how we applied the transfer tape, see the video at 9:14.
4. Once the transfer tape is securely covering the entire graphic, place the graphic on your sealed wood round.
5. Play with the placement until you’re confident that all edges line up.
6. Keeping the entire graphic in place, pull up one corner of the project, peel back the vinyl backing, and secure the adhesive graphic and transfer tape on the board.
7. Pull the rest of the graphic up from the board and carefully press the graphic into place, using your scraper on the front of the transfer tape while slowly peeling back the backing.
8. Once the graphic is fully adhered, slowly peel back the transfer tape, keeping it parallel to the project (see picture).
9. If you have any bubbles, you can pop them with a pin and apply pressure.
10. Let the vinyl set for 24 hours before moving on to the resin flood coat.
Step 5: Pour Resin Flood Coat
Whew! Now that you got the graphic down and let it set for 24 hours, it’s time for the flood coat. The steps here are similar to the seal coat, with a few exceptions, so read closely.
Gather the following materials: 220 grit sand paper, level, resin, mixing cup, plastic drop cloth, mixing stick, trowel, heat gun, and butane torch.
Follow these steps:
1. Sand any spots on your project where there is bare resin. This will help two two layers of resin adhere together more securely.
2. Elevate and level your project on the surface where you will pour.
3. Check level in numerous directions.
4. Mix your resin according to the instructions on your particular brand.
5. Pour a thick layer of resin and heat it with the heat gun to give it extra viscosity.
6. Spread the resin out with the trowel. Be gentle so as to not pull up any edges of your vinyl graphic.
7. Ensure that you cover all edges and have no bare spots.
8. Use the torch to pop bubbles as they appear.
9. Cover and let resin fully cure. For the ProMarine resin that we used, we gave it three full days.
10. Remove tape from bottom carefully after resin has cured. If needed, carefully use a box cutter to break any stubborn seals between the resin and the tape.
Step 6: Add Table Legs
There are so many options for how to add legs to your table. Your local hardware store likely carries some, as well as places like Amazon. We actually stole the base for this table off of another table that no longer matched the decor. The steps below will briefly outline what we did.
Gather the following materials: legs of choice, blanket, drill, screw driver, paint, stain, power sander, and paint stripper.
Follow these steps:
1. Use a combination of paint stripper and sanding to remove any old paint from any wood pieces of the old table.
2. Stain the wood pieces, using the same stain you used on the wood round in the first step.
3. Paint any non-wood pieces. We used white spray paint to match the white vinyl.
4. Place the wood round face down on a blanked to protect the surface from any damage as you attach the legs.
5. Screw the legs/base into the bottom of the wood round.
Tip: If you have a 2-layer table like we do, it's helpful to put two legs on, attach the bottom round piece, and then add the other two legs.
6. Add decorative caps for the screws, if desired.
Step 7: Enjoy!
Whew! To be honest, there is a lot of curing time in this project between steps that makes it take a little longer than your typical weekend furniture project. However, we can say that it is absolutely worth it to have a beautiful, unique, professional quality table that showcases our love of travel. Let us know if you give it a try in the comments below.
In the meantime, if you liked this project, please head over to JustMightDIY.com for more tips, tutorials, back stories and more. And if you’re interested in checking out more of our tutorials, check out our Instructables profile or head over to our YouTube channel.
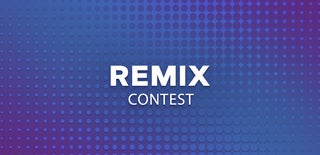
Participated in the
Remix Contest