Introduction: Easy Table Saw Sled
A table saw sled (or cross cut sled) makes cutting wood against the grain safer, and much easier. There are lots of technical ways to approach making a table saw sled, but sometimes you just need a simple and elegant solution to a problem. This is possibly the easiest cross cutting sled you can make, and it still achieves accurate cuts.
Cross cutting sleds (in case you didn't know) are used to cut against the grain of wood on a table saw, or cut very small pieces without fear of chopping your fingers off. Cross cutting (or mitre cuts) is a topic that is covered on the free Table Saw Class, which will bring you from zero to hero on being a table saw pro.
This cross cut sled can be made with scraps and only requires three cuts to be precise, the rest can be slapped together with reckless abandon and sill make perpendicular cuts. At the end of the Instructable we'll use the 5-cut method to check the accuracy of the sled once it's created.
Ready to get cross cutting? Let's make!
Step 1: Tools + Supplies
This table saw sled uses scrap wood, relying on a few precise cuts and a very straight piece of hardwood. Here's what you'll need to make your own:
- Calipers
- Tri Square
- Drill bits + countersink
- Wood glue
- Plywood (flat, and at least ¼" thick)
- Straight hardwood scrap (I used white oak)
The calipers are essential to get an accurate measurement of your table saw mitre track. You'll also need a solid tri-square to align the sled fence to the blade, which is what will determine if your cuts are square or not.
![]() | ![]() |
Before making any cuts make sure your table saw is calibrated, otherwise every cut you make will be off. Table saw calibration is covered extensively in theTable Saw Class.
Step 2: Measure Mitre Track
Almost all table saws have a standard mitre track dimension of 0.75" wide x 0.375" deep. Before making any cuts it's best to check to determine your mitre track dimensions.
![]() | ![]() |
Digital calipers have 4 measurement points: exterior dimensions (the large jaws that go outside an item to be measured), interior dimensions (the smaller jaws that go inside an item to be measured - located above the larger jaws), depth gauge (a probe that extends out the end), and an exterior depth gauge (the hammerhead front of the calipers and the inside jaw of the moveable side - example).
Use the interior measure to check the width of your mitre track, and then use the depth gauge to see how deep the track is.
Step 3: Cut Track
Set the table saw fence to the track width dimension and make a rip cut on your straight hardwood scrap. Next, set the fence to the mitre depth and run the cut hardwood through again.
![]() | ![]() |
We're using a hardwood like oak here as it's a very dense and durable wood that's not prone to warping. Using this as our track will allow the sled to glide smooth and not get stuck in the mitre track.
Step 4: Clean Up
Before checking your cut it's wise to clean up your table saw surface and mitre track of any sawdust or debris. If you neglect this step you're not going to get an accurate assessment if your cut fits snugly in the track.
Step 5: Test Fit Track
Place the cut hardwood into the mitre track to test the fit. Try pushing the hardwood along the track and see if it sticks anywhere, then try wiggling the hardwood laterally against the track to see how much slop or play there is.
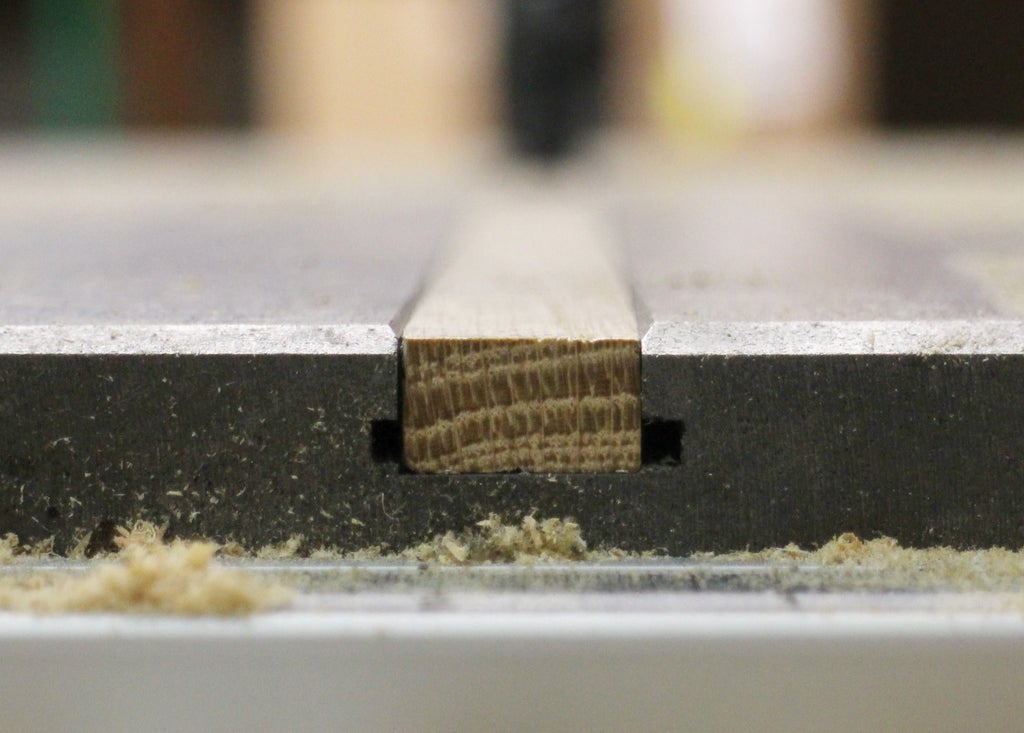
You're looking for a snug fit, with no play, and a smooth glide. If you're getting caught up anywhere check the track to make sure there's no debris, then try sanding sections of the hardwood to get the correct fit. If all else fails you can always remeasure and rip another piece of hardwood until you get the proper fit.
Step 6: Plywood Sled Base
With the track cut we can make the base of the sled. The greatest thing about this style of sled is that your sled base doesn't need to be perfectly square at all.
I used a scrap piece of ¼" plywood that had very uneven edges - perfect for this application!
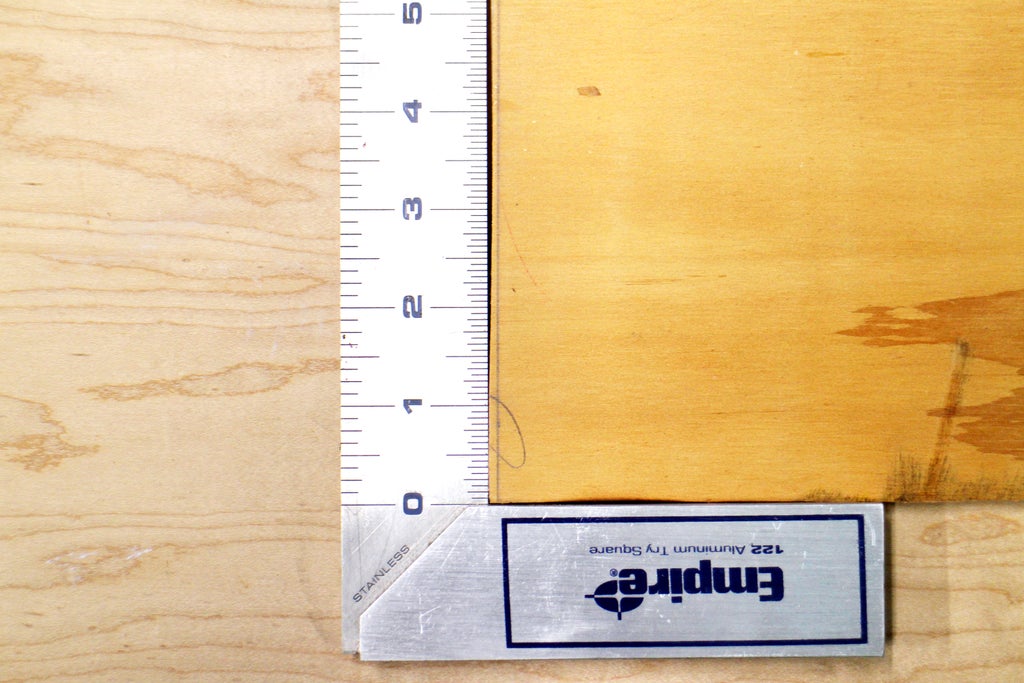
This plywood base will sit on top of the track and be the bottom of the sled. Since it's only serving as a platform and no measurements will be made from it, there's no need for it to be anything other than a flat surface we can cut through.
Step 7: Glue Base to Track
Insert the hardwood into the mitre track.
Apply a small bead of glue on the hardwood along the length making sure not to use too much or accidentally spill any glue onto the table saw. You only need a small amount of glue, since we'll be adding screws to attach the hardwood to the plywood later.
Once glue is applied place the plywood on top of the hardwood track, aligning the plywood so it's approximately square to the track and the center of the plywood is in line with the saw blade.
Add weight to the plywood over the glue and allow the glue to dry overnight before moving.
Step 8: Secure Track
once the glue has dried slide the glued assembly out of the miter track and flip the plywood over.
Drill pilot holes along the hardwood length and countersink each drilled opening. Hand screw fasteners in each opening to mechanically secure the hardwood to the plywood. The glue and screw combination will ensure the two parts are mated securely.
![]() | ![]() |
It's important to countersink the openings so the screw heads are inset from the hardwood track surface, thereby not hindering any movement when the sled is in the track.
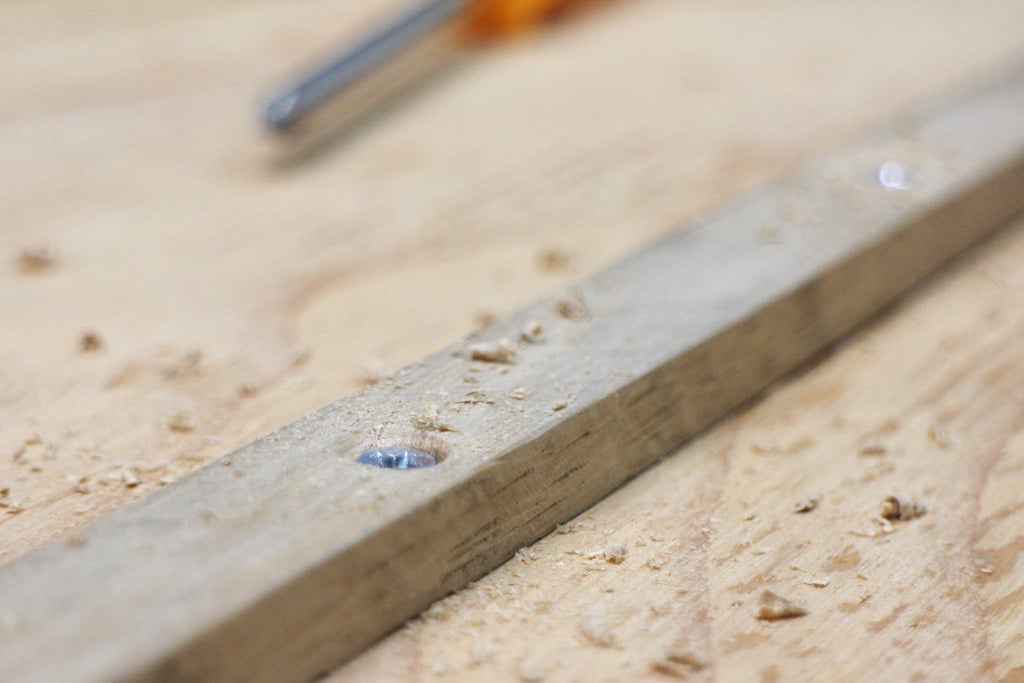
Hand sand any burrs or rough spots from drilling.
Step 9: Glue Sled Front Fence
The sled front fence (the part furthest away from you when operating the sled) does not need to be accurate, since it's only job is to keep the structure of the sled once we cut the kerf in the plywood.
I used scrap wood glued along the front edge of the plywood, only making sure that the scrap wood was reasonably square so that the surface would glue correctly to the plywood.
Step 10: Cut Partial Kerf
Before gluing on the sled back fence, which needs to be square to the blade, we'll need to make a reference cut. The back fence needs to be perpendicular to the saw blade and perfectly square to make accurate cuts.
With your saw de-energized remove the insert and remove the riving knife, then place the insert back over the blade and lower the blade completely into the table. We'll be bringing the blade up through the plywood base to create a reference cut which we'll align the back fence to.
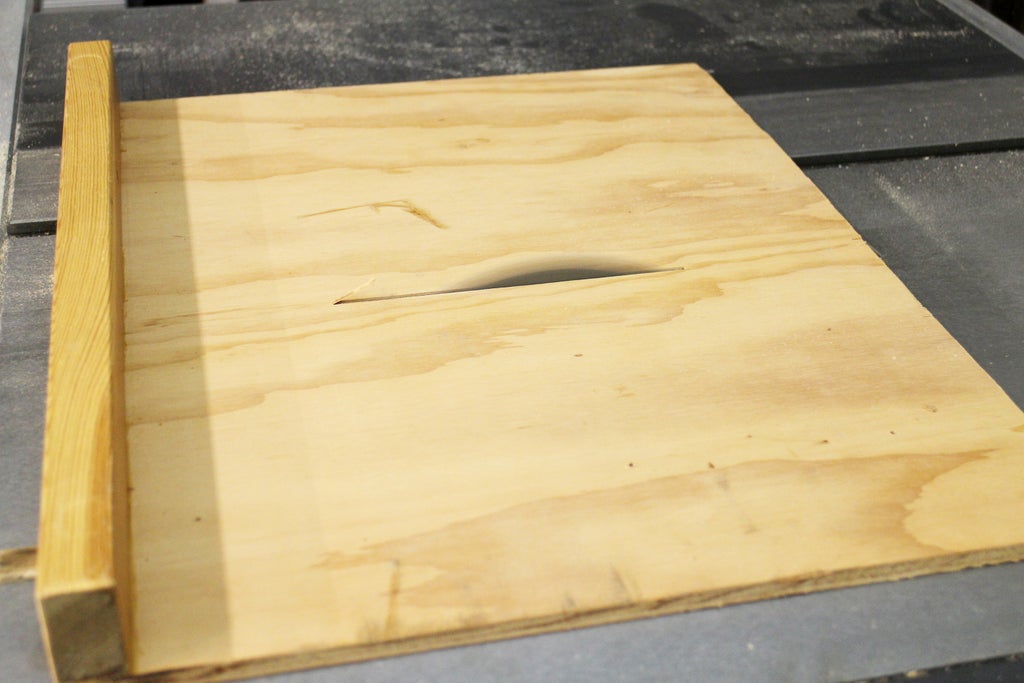
Place the sled into the mitre track and place the plywood directly over the lowered blade. Start the saw and slowly raise the blade until it's about 1" higher than the surface of your plywood base, steadying the plywood with your other hand (away from the blade) as needed to prevent the plywood from wandering during the cut.
Kerf is the material that is removed when cutting and it's equal to the thickness of the blade, this is described in more detail in the Table Saw Class.
Turn off saw and de-energize for the next steps.
Step 11: Select Wood for Sled Back
The sled back fence is the only other piece of wood that needs to be precise for this sled. This back fence will be where you align your wood to be cut in reference to the saw blade, so it needs to be square and perpendicular to the blade.
Use the tri-square to ensure your wood choice is completely square and straight. Like the front fence, the back fence wood should be as long as your sled is wide.
Step 12: Glue Sled Back
With the saw de-energized and the blade extended up through the plywood, place the tri-square against the face of the blade. Know that the saw teeth are slightly wider than the face of the saw, so make sure your tri-square misses the teeth and sits flush against the blade face.
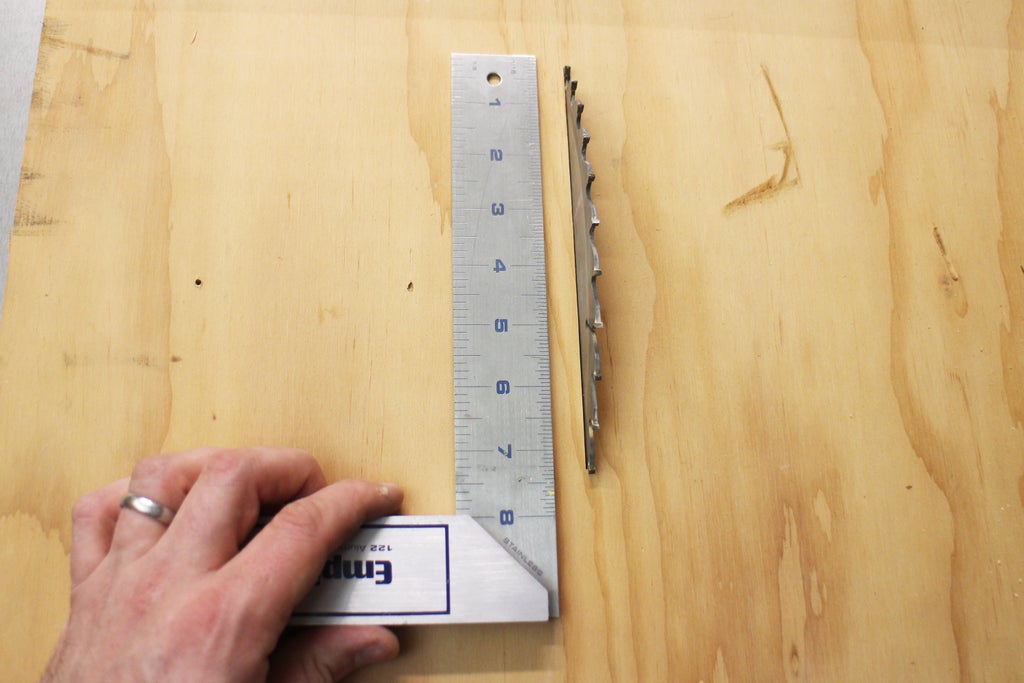
With the tri-square flush against the blade align your square back fence to the perpendicular arm of the tri-square to locate it 90° to the blade.
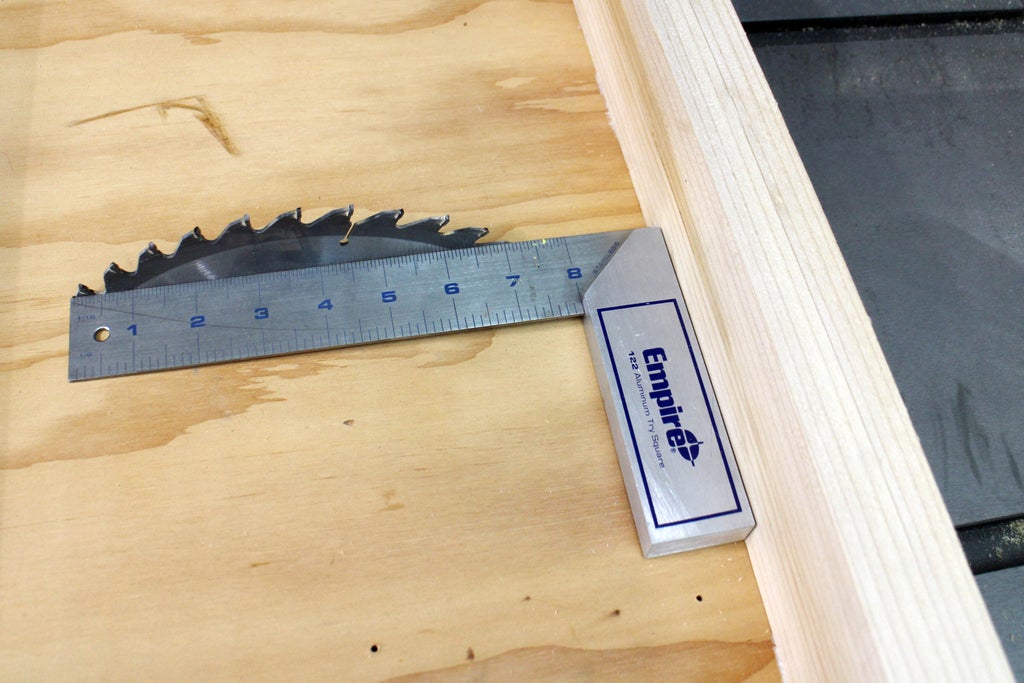
Apply a small bead of glue to the back fence and place on the plywood. This is the most critical part of the entire sled, as misalignment here will result in every cut made on the sled being at an angle. Take the time to ensure your back fence is totally perpendicular to the saw blade.
Step 13: Examine
Reposition the tri-square on either side of the blade to check the back fence for squareness.
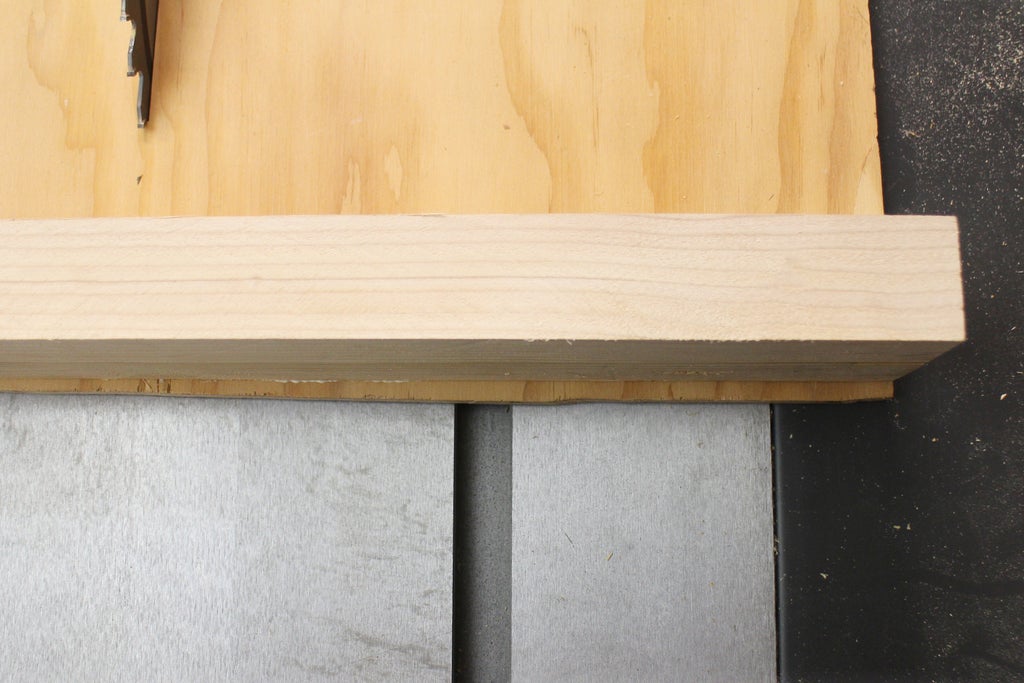
When satisfied the back fence is aligned perpendicular to the saw allow the glue to dry overnight before moving.
Like with the hardwood track, after the glue has dried you can flip over the sled and drill and countersink openings to attach the back fence with screws.
When the back fence is secured, raise the blade up about ½" higher than the surface of the plywood and run the sled through the blade completely. your sled is functionally complete!
Now, how do we know it's accurate?
Step 14: Check Accuracy (5-cut Method)
To check the accuracy of the sled we'll use the 5-cut method, cutting a piece of scrap 5 times, rotating after each cut, to see the deviation from perpendicular.
By making multiple subsequent cuts on the same piece of wood, the resulting 5th cut will have magnified the error and show us our deviation.
Start with a rectangular scrap piece of wood and label each side 1-4 counterclockwise. This scrap piece doesn't need to be square to begin with, the 5-cut method can handle any scrap piece of any shape.
![]() | ![]() |
Place side 4 against the back fence and line side marked 1 with the saw blade, move the sled forward through the blade to make a cut along side 1 removing a small amount of material. Move the sled back and rotate the scrap piece clockwise so that side 1 is now against the fence and side 2 is lined up to be cut. Repeat this process for all 4 sides until you are back to side 1 at the saw blade.
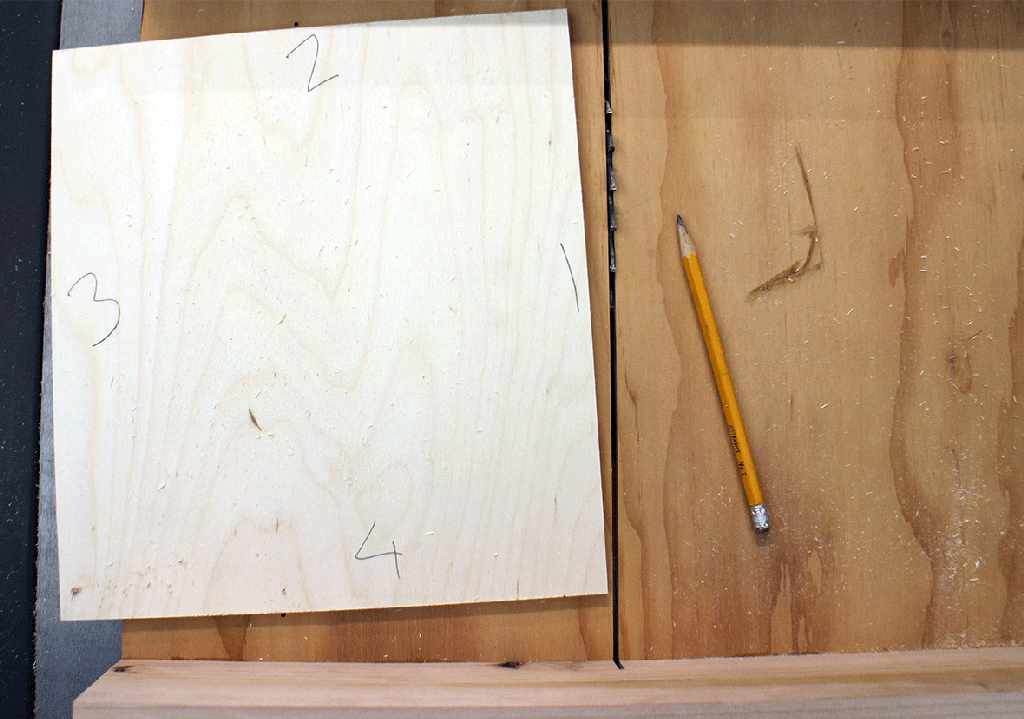
After cutting all 4 sides make one final cut along side 1 again, this time make the cut of a decent size. The off-cut here will be the piece we measure to see the sled accuracy.
Step 15: Measure 5-Cut
If your back fence of the sled is perfectly perpendicular to the blade there there will be no deviation of measurement between the top and bottom of the 5th cut.
Use calipers to measure either end of the off-cut and write down the readings.
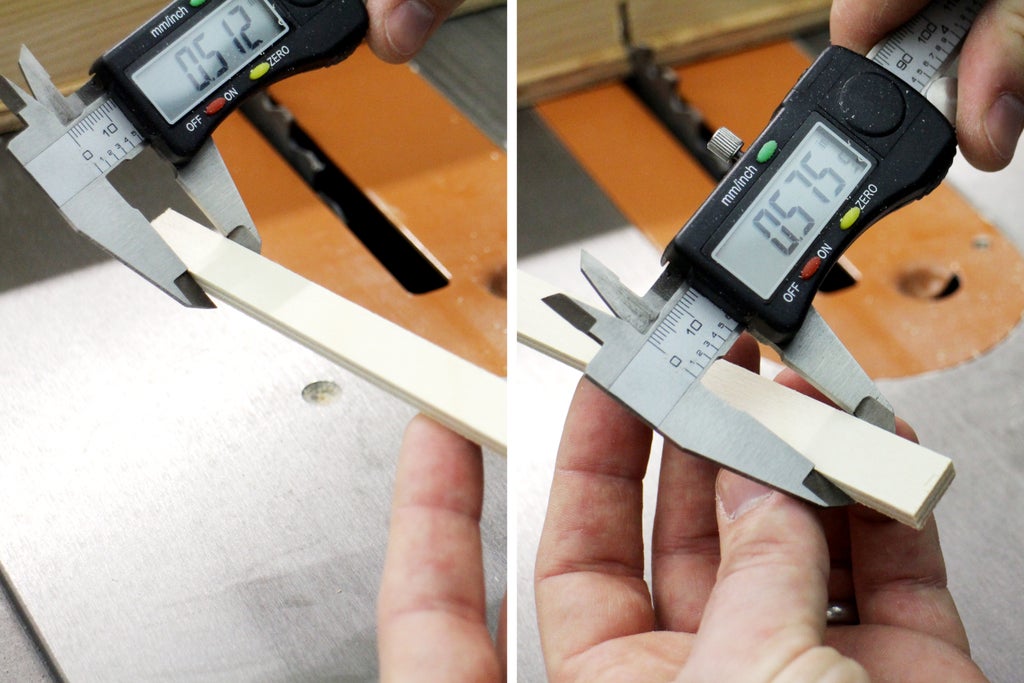
One end reads 0.512" and the other 0.575", a difference of 0.05" (50 thou) or 1.5mm. This is less than 1/16" compounded along 4 sides of my roughly 1'x1' scrap piece.
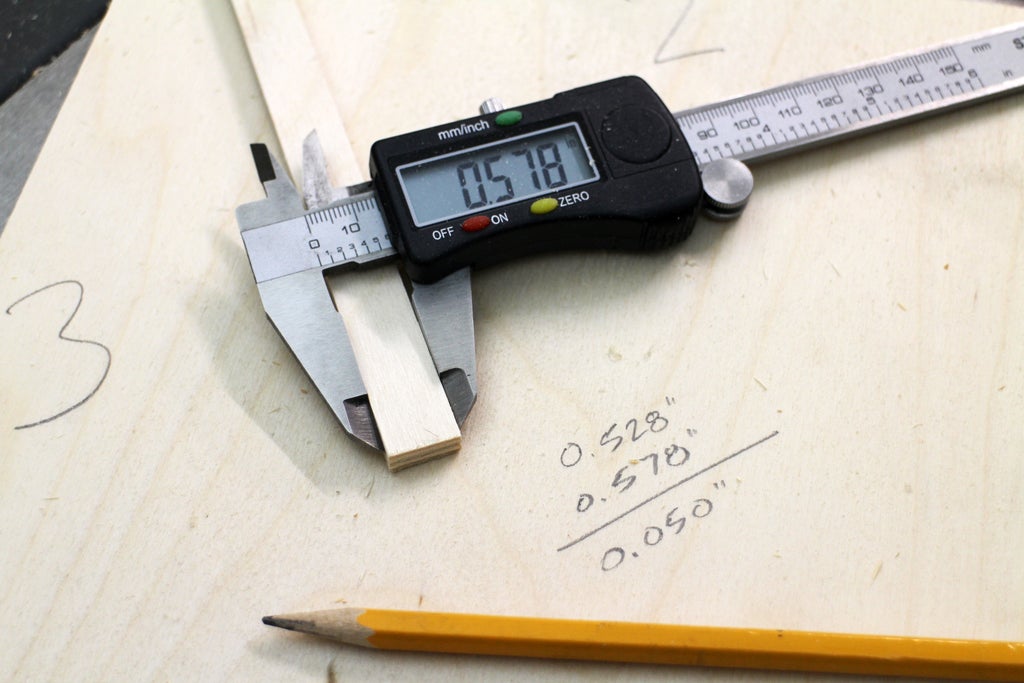
How accurate you want your sled to be is up to you. If you want more precision then you'll need to make minor adjustments to the back fence and redo the 5-cut method to check your adjustments.
Before going too far down the rabbit hole of accuracy I caution you to think about a few things.
Sled capacity
The 5-cut method is taking advantage of compounding the error with each successive cut, so the error you read on the 5th cut is not the same as a single pass.
Also, think about the capacity of your standard sled cut, it's probably not going to be a long cut, but a short cross grain cut. How much deviation is there going to be when your cut is 1" rather than my sample piece which is 4 cuts along a 1' length.
Being Realistic
Are you cutting wood that requires a level of precision reserved for a high tolerance space shuttle, or are you a hobbyist with a need to make fairly accurate cross cuts. This is a homemade sled to make cross cuts, further refinements can always be made later through trimming or sanding. Don't sweat the small stuff.
Step 16: Cross Cut
This table saw sled is simple to make, cuts accurately, and can easily be made in an afternoon.
What I'm showing is only a very basic start, table saw sleds can be customized with all kinds of clamps, tracks, and hold-downs to suit your needs. Once you make one sled there's no limit to the types of additions you can make, why not make a few and have sleds on hand for every specific cross cut you make!
Though this sled is simply made, it's wise to treat it like any precision tool and not just toss it around. You've spent the time to calibrate the fence and track to take care of your sled and you'll have it around for years to come.
Happy making!
Have you made your own simple cross cutting sled?I want to see it!
Happy making :)